Industry moves toward alignment with WellSharp’s enhanced well control training standards
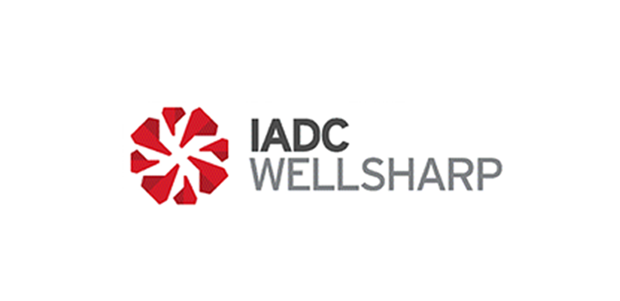
Industry-built accreditation program sees increasing adoption as it pushes past initial rollout phase
By Malcolm Wells, Contributing Editor
In rolling out a revolutionary well control accreditation program, it is clear the drilling industry is taking on a wider challenge.
“The world’s most advanced well control training regime devised to date” is how the media has described IADC’s WellSharp. Praise indeed, but WellSharp is also described by its developers as “a complete root and branch overhaul of well control training.” That means large-scale change and pushing the drilling industry out of its comfort zone at a time of challenging market conditions. The success of WellSharp is not simply about the delivery of well control training, critical though that is. It is also a wider test of the industry’s ability to improve operational excellence without external intervention or regulatory threat.
As Stephen Colville, President and CEO of IADC, puts it, “It’s very easy to pull everyone together in a room and get agreement in principle about changing for the better. The test comes when the change is real, when it has to work on the ground and when there is a dollar figure attached. The payback for the industry is building credibility and trust with regulators, politicians and the wider public.”
WellSharp is designed to raise the bar of well control training, explained Mark Denkowski, IADC Executive VP-Operational Integrity. He is responsible for WellSharp development. Two key areas that mark WellSharp as a radical departure from previous well control training are the structure of the component training programs and the extensive use of electronic testing, he said.
In accordance with the recommendations of OGP 476, produced by the International Association of Oil & Gas Producers in 2012 in response to Macondo, WellSharp has five course levels: awareness, introductory, driller, supervisor and engineer. In addition, WellSharp stipulates that each course must be taught separately. Previously, driller and supervisor courses were often combined.
“One of the key principles of WellSharp is that people are taught what they need to know for the level at which they’re working,” Mr Denkowski said. “We don’t waste training time or risk confusing people with information that’s not directly relevant to their role and responsibility.”
In practical terms, however, that means extra resources, because dedicated classes require more teachers and teaching space. It raises a cost issue, but Hector Moreno, formerly Lead Technical Instructor at Halliburton, believes this is the cost of doing business. “If you look at a medical school, they do not want anybody who is not absolutely qualified to get into the surgical theater with a scalpel,” he reasoned. “An operator is training people because an accident can cost a fortune or even lead to bankruptcy.”
While the program structure raises issues of teaching resources, the electronic testing process at the heart of WellSharp asks tough philosophical and cultural questions. In particular, the objectivity of the WellSharp system removes opportunities for trainees or trainers to “game” the system, cut corners or introduce any element of “benefit of the doubt” into the testing process.
Nonetheless, concerns exist that this more rigorous system could increase the overall failure rate and impact operations. Mr Denkowski explained, “Some are concerned about computerized and standardized testing. Another worry is that, because the training provider won’t have control over the test content, the trainees might be uncertain whether they can answer all the questions.”
However, those familiar with WellSharp praise its fairness. John Breidenthal, formerly Supervisor of Well Control Instructors for Chevron, feels WellSharp has achieved the right balance. “As long as a student has the ability to learn, has a fundamental background of basic math and science, and the appropriate amount of rig experience, they shouldn’t be afraid of WellSharp,” he said. “It’s not rocket science, but it does require focused attention and work to be successful. For any company out there, the fact that their employees are WellSharp-certified should make them more confident about their safety as it relates to well control.”
Positive industry response to date supports this view. Only three months since the WellSharp launch, institutions responsible for more than 80% of global well control training have moved to WellSharp, IADC data show.
Mark Venettozzi, Lead Well Control Instructor, BP, takes a pragmatic view. “I like the fact that WellSharp testing is now consistent. By having everyone take a test generated from a common question database, everyone is held to the same standard. This allows the industry to gauge the competency level across the board, and it quickly identifies gaps in training.”
Despite the positive response to date, Mr Denkowski recognizes the need to maintain the perception of fairness and balance.
“One of the great advantages of WellSharp is that it’s been created by the industry,” he said. “The downside of wholesale collaboration is that it takes time to get aligned and make progress. The upside is that what eventually gets produced is the considered and informed view of the whole industry. It’s the industry coming together through IADC and agreeing what the standard should be rather than a small group of self-appointed individuals laying down the law. That gives it an authority it couldn’t achieve any other way.”
Going forward, WellSharp will also feature “must know” questions with an immediate fail outcome if answered incorrectly. Concerns exist that these might be too prescriptive.
Mr Denkowski disagrees. “The ‘must know’ questions will be an important part of the test because, by definition, they will be safety-critical and role-specific,” he stressed. “People shouldn’t be unduly concerned by them because they will be used sparingly and with consideration and restraint. Further, if anyone gets these questions wrong, we can target remedial support immediately, so they will be hugely beneficial to the candidate in the long run.”
WellSharp is supported by an electronic question database that produces a random question set for each candidate. Trainers have no prior knowledge of the specific questions. Therefore, the temptation to “train to the test” is removed. Candidates can challenge a question if it is unclear or ambiguous, but WellSharp’s requirement for 100% proctored/invigilated testing for both the driller and supervisor courses prevents “clarification” from segueing into “coaching.”
The electronic testing system allows candidates to get feedback on what they got wrong and allows the WellSharp team to monitor individual trainers, identifying strengths and weaknesses in training styles and techniques.
The value of this feature has been recognized by the industry. John Bottrell, BOP Manager for Nomac Drilling, is enthusiastic. “We look forward to the increased integrity of WellSharp testing to more accurately identify those who might benefit from additional instruction,” he said.
As Mr Denkowski adds, “It’s always useful to know what you don’t know. It allows us to provide feedback to the candidate’s company to address an individual’s weaknesses on a targeted basis. WellSharp uses technology to underpin a more effective training and testing environment, and the overall integrity of the qualification is enhanced as a result. This makes WellSharp a real game-changer.”
WellSharp will be subject to further curricula development, with the initial emphasis on activating the engineer qualification, developing the human factors component and establishing WellSharp in a continuous learning context, he said.
Mr Colville acknowledges the challenges ahead but is happy with the direction of travel so far. “WellSharp has been generally welcomed by the industry because the industry wanted it, argued about it, designed it and built it,” he said. “There’s no doubt that the standards set will prove more challenging for some than for others, but there is broad consensus that this is the right way for our industry to go. Macondo asked a big question of our industry, and WellSharp is an important part of the answer.
“In the well control training space, we have an asset in WellSharp, which will make a real contribution to improving overall operational excellence and taking us closer to the ideal of getting it right the first time, every time, all the time.”
The drilling industry can point to WellSharp as an example of successful collaboration and delivery. However, its long-term success will depend on maintaining both the integrity of the program and industry consensus as the launch progresses. For individuals and organizations alike, the testing has only just begun.
Click here to register for and view the WellSharp virtual panel discussion.