Operational safety, integrity challenges, expectations evolve as global rig fleet ages
R&D targets new tools and methodologies for rig moves, maintenance, ice effects, jackup site assessments and more
By Dave Forsyth, Pao-Lin Tan and Jim Brekke, ABS
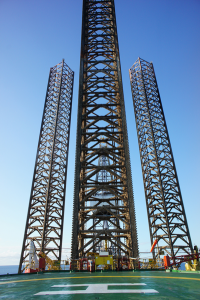
The global jackup fleet operating today comprises more than 650 units, many of which are aging or nearing the end of their intended service life. According to research data from ABS, which monitors the global MODU fleet, 50% of the MODUs working offshore are more than 30 years old. That percentage is dominated by jackups.
As new rigs are being delivered, they are typically built to a higher specification capable of operating in harsher environments. But as operational expectations change, there has to be a clear understanding of how new challenges are exacting a toll on older assets so it is possible for lower-specification units to continue to perform safely.
Identifying client needs is an important first step in addressing jackup safety challenges. The next critical step is to identify areas for research that can lead to solutions. Ongoing R&D efforts through the technology program at ABS span a broad spectrum that includes safety issues related to jacking systems and equipment, units moving on and off location, spudcan fixity, soils and floating stability.
Knowledge and experience derived from the classification process through engineering reviews and ongoing surveys are supplemented by R&D work to develop operational tools, methodologies and safety standards that can be used to mitigate incidents.
Moving on and off location
Jackup units face unique challenges that affect their ability to move and operate safely. These challenges are separated into two broad categories: issues while afloat – particularly while moving on and off location – and issues while elevated on location.
In general, incidents during rig moves are more frequent than incidents while the jackup is elevated at a site. Rig move incidents are costly to rig owners and operators, not only because of repair costs but because of the associated nonproductive time. This is not to diminish the importance of elevated site assessments. Although more rare, incidents while in the elevated condition have high consequences, such as total loss of the unit. Higher consequences that result in fatalities and environmental releases also are extremely rare, and industry site assessment standards have played a role in maintaining this level of safety.
While the methodology for site assessment continues to be studied and refined, it has become clear that the issue of jackup rig moves warrants the attention it is presently getting in the industry.
Jackup drilling units have a challenging set of overall design requirements. Designed to withstand hurricane-force winds when properly jacked up above the highest waves, these units should survive all but the most severe storms. When jacked down and moving from one site to another, a thorough rig move planning process helps steer them clear of storm threats. Finally, the decisions to move on and off site are made using knowledge of the vessel motions and sea conditions and the limitations of the vessel as it moves on a specific site.
By examining the challenges and defining research projects that target the issue of moving on and off location, investment in R&D will result in better tools to assist rig owners with monitoring key parameters during rig move operations and developing methodologies to produce better guidance. Examples include methodologies that allow limits to be established on weather and rig motions during rig moves and the use of monitoring systems that can provide real-time measurements of weather and rig motions during drilling operations
Aging jackups

As a jackup gets older, hull inspection becomes more important. Periodic surveys are part of the classification process. These surveys address requirements for inspecting coating condition, corrosion, pitting and grooving, structural deformations, fractures and housekeeping. Owner-driven inspections can help preserve the hull and reduce the work that needs to be done following regular third-party surveys.
Jackup equipment is inspected according to a process called condition-based maintenance (CBM). Simply stated, the condition of the rig and associated equipment dictates the inspection program instead of following a prescribed calendar-based inspection program. Continuous monitoring allows for more relevant inspections based on activity and equipment usage.
Of course, consideration should be given to inspecting equipment immediately following an incident, when a jackup or equipment has been overstressed either while elevated or after a rig move. Toward that aim, maintenance procedures and asset integrity management programs carried out by an independent third party can help operators maximize operational efficiency and uptime because these programs are designed to address the entire asset from construction and modification to life extension and decommissioning.
Researching ice effects
In contrast to working in open water, jackups operating in ice are affected by many more critical factors, including ice loads on legs while elevated, ice loads on the hull during transit and the effects of cold air temperatures.
For hull and leg structures, the prevailing design consideration is the ice loads resulting from different forms of sea ice. Ice management (IM) will play a key role in establishing the maximum design loads. The aim of ice management is to detect and characterize the ice that may interact with the unit and then to influence control over the ice environment in the vicinity of the offshore installation utilizing icebreakers to create floes of a specified maximum size.
The ice loads from the managed floes are highly localized impact loads or concentrated loads along the ice/structure contact area. This contrasts with open-water operations where jackups are optimized for severe hydrodynamic loads that typically are in the form of distributed loads. Localized ice loads manifest as pressure and line loads on leg components when elevated. In the event that the ice management system is overwhelmed, the unit may be required to jack-down. The hull structure needs to be able to resist the ice loads for a defined unmanaged or partially managed ice environment as the unit is moved off location, under tow or by its own thrusters. In addition, the hull must resist ice loads during a transit to or from the field if the operator is intending to maximize drilling time during the open water window.
In addition, jackups that work in cold air temperature environments must be designed to contend with the effect of sea spray, which can freeze instantly and accumulate on the exposed portions of the rig structure. Beyond the immense added weight that may compromise the structural integrity of the rig without consideration of winterization, systems – both operational and safety related – may also be compromised.
While IM operations and winterization considerations may be part of a newbuild jackup rig’s design specifications, their effectiveness should be considered in the holistic sense for operational safety since it is a determining factor for the safe operational limits of any jackup in ice and cold environs.
Jackup site assessments
ABS has worked with the industry for the past nearly 30 years on the issue of jackup site assessments, contributing to improvements in industry standards produced by the Society of Naval Architects and Marine Engineers (SNAME) and the International Standards Organization (ISO). One of the areas that still requires additional effort is leg foundation fixity. Work from academic institutions (e.g., Oxford, Cambridge, University of Western Australia, and National University of Singapore) has been brought to bear on the problem, and ABS has worked closely with these universities to interpret and apply their findings to solutions.
For decades, the US standards for offshore unit structures were based on the working stress design method (WSD). Recently, ISO 19900 introduced the use of Load and Resistance Factor Design (LRFD), applied to both fixed and floating structures. To align with current standards, ABS is upgrading its classification rules to reflect relevant LRFD-based classification criteria. The new guidelines will cover jackups and semisubmersibles, liftboats and floating production installations such as spars.
It is important for classification societies to take a proactive role in working with industry to better understand the impact of new ISO requirements for earthquake assessments for jackups working in seismically active regions of the world. As some operators are beginning to adopt the ISO document, ABS has commissioned a study to better understand how to apply the document and assess the impact on drilling contractors. The objective is to make a smooth transition as this document is delivered to industry.
Watertight integrity, wind tunnel testing
Experience in the offshore industry demonstrates that while vessels such as MODUs are designed to provide watertight integrity (WTI), incidents remain a concern. Flooding that has progressed beyond the original breach to additional hull compartments poses a threat to stability of the jackup. Owner-driven audits can promote safety in this area.
Another area that has the potential to impact jackup operational safety is wind tunnel testing. Jackup legs experience significant wind loading that needs to be evaluated in determining unit stability following exposure to high winds. SNAME issued guidelines on wind-tunnel testing of jackups in 1988 for both elevated and transit conditions, but more work is needed. ABS is facilitating an update of the SNAME document for both jackups and production units that includes the application of computational fluid dynamics.
Maintaining vigilance
Reliable technology, a strong safety culture and effective operational procedures are critical to creating a safe work environment on offshore assets. Operating environments and operational expectations are changing as new technologies are being introduced to enhance safety and improve efficiency. As performance requirements evolve, industry must continue to find better ways to maintain aging rigs and implement methodologies, tools, and monitoring techniques that drive incident mitigation and reduced nonproductive time.