Alan Spackman retires after career dedicated to offshore safety, regulations
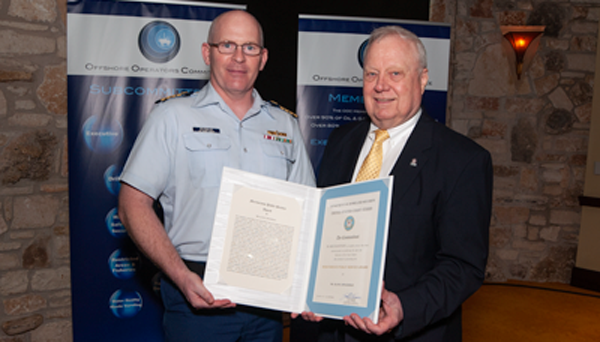
Development of IADC HSE Case Guidelines for MODUs, update of IMO MODU code among numerous accomplishments over 27 years at IADC
By Kelli Ainsworth Robinson, Associate Editor
After 27 years with IADC and 25 years in the US Coast Guard, Alan Spackman is retiring in July. Mr Spackman previously served as Vice President of Policy, Government and Regulatory Affairs for IADC before moving into an advisory role at the beginning of this year.
Throughout his life, Mr Spackman has lived in dozens of locations, not only due to his own military service but also his father’s. Growing up with a father in the US Air Force, Mr Spackman lived in 21 cities, primarily in the US Southwest, including Riverside, Calif., and Tucson, Ariz, through his childhood. However, the most interesting place he lived was actually Guam, a tiny island that measures just 23 miles long and five miles wide. Apart from being incredibly safe, “it was sunshine, beaches and bare feet,” he recalled.
When it came time for him to choose a college, Mr Spackman looked to the military academies and ultimately decided on the Coast Guard Academy, where he obtained a Bachelor’s of Science in engineering in 1970. “At the time that I was considering it, the Coast Guard had an oceanography program, and I was interested in oceanography,” Mr Spackman said. The Academy eliminated the oceanography program after he enrolled, however. Because he excelled in his engineering courses, particularly civil engineering, he decided to pursue that path instead.
After graduating from the academy, Mr Spackman began Coast Guard shipboard service as an engineer, first on a ship stationed in Honolulu, Hawaii, and then in Norfolk, Va. In 1973, he was one of several officers selected by the Coast Guard to pursue a master’s degree. He took the opportunity and opted to study naval architecture at the University of Michigan.
“At that point, I became interested in the timely topic of optimizing tanker design to minimize outflow in the case of accidents, so that became the subject of my master’s thesis, and that got the attention of the Coast Guard’s emerging Marine Safety Environmental Protection Program,” he said. “So instead of going back to engineering afloat in the Coast Guard, I went into the regulatory side after graduating from the University of Michigan with a master’s in naval architecture and marine engineering.” He’s found that his engineering background and the discipline it instilled “fits well toward working regulations.”
His first job after obtaining his master’s in 1975 was as a Plan Review Officer for the Merchant Marine Technical office in New York, reviewing plans for a wide variety of commercial vessels. One of his assignments was to review plans for semisubmersibles that were being constructed in a Canadian shipyard for Sedco, which merged with Transocean in 1999. This particular job brought Mr Spackman in contact with the drilling industry for the first time.
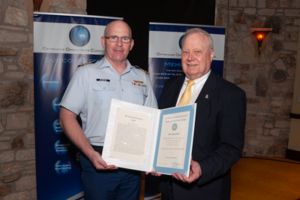
“It was at this time that offshore drilling activities were first beginning to get serious regulatory attention, both in the US and elsewhere,” he said. In addition to reviewing plans for these MODUs, he was also tasked with plan review for container ships, tankers, LNG carriers and numerous small-passenger vessels.
This was followed by a tour in Coast Guard headquarters, where he was part of a team developing high-profile regulations, including those implementing the Port and Tanker Safety Act of 1978.
In 1984, he was transferred to the Marine Inspection Office in New Orleans and then was named as the Executive Officer in 1987 at the newly established Marine Safety Office in the same city. During this tour, he became more aware of the causes and consequences of safety incidents that occur on offshore drilling rigs and production platforms. “It demonstrated to me that the lack of central oversight of safety-critical activities was a persistent problem in the offshore industry,” Mr Spackman said. “While industry has made great strides in this regard, we haven’t entirely fixed that problem yet. It’s somewhat antithetical to some people’s view of independent contractors and independent contractors’ activities.”
In 1989, he was transferred back to Coast Guard headquarters to serve as Assistant Division Chief for the Coast Guard Marine Protection Division – just in time to participate in the development of what became the Oil Pollution Act of 1990. In April 1991, he retired from the Coast Guard with the rank of Commander. That same month, he joined IADC as Vice President-Offshore Technical and Regulatory Affairs.
When he first joined the association, it was only a few months after the UK government published the Cullen Inquiry into the Piper Alpha incident. “I basically spent my first two years working with IADC’s officers in the North Sea Chapter to develop IADC’s response to the Cullen Inquiry,” Mr Spackman said. “The key part of that response was trying to come up with an approach by which contractors could develop a safety case that was required by the post-Piper Alpha legislation in the UK.”
Initially, the association developed a “template” that contractors could use to present information required by the UK’s safety case legislation. However, UK regulators rejected this approach, as they wanted the information presented to be organic to the contractor. “The approach to minimizing risk had to come from the contractor itself, not the trade association,” he said. From there, IADC began to work on what eventually became the IADC HSE Case Guidelines for MODUs, which were published in the early 1990s. The guidelines have been updated several times, in 2006, 2014 and 2015.
In the mid-2000s, he coordinated IADC’s years-long efforts to update the International Maritime Organization’s (IMO) MODU code, drawing on expertise developed during his time with the Coast Guard and support from IADC members. While the IMO had intended for the code to be an evergreen document, it hadn’t been revisited in more than a decade before IADC took the lead on this revision. “IADC got with several of the interested flag administrations and decided to develop a new edition of the code that would take into consideration the additional lessons learned from casualties, as well as the changes that had been made generally within the IMO’s safety conventions that could be applicable to MODUs,” Mr Spackman said.
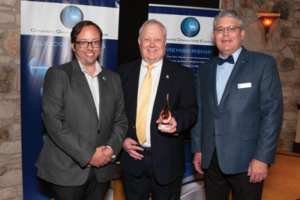
An IADC-led workgroup spent three years developing a list of changes proposed for the MODU code, and then took a fully developed proposal to the IMO for consideration. It took an additional two and a half years before IMO approved the changes and adopted them into the code in 2009. “It established an updated standard for the design and construction of MODUs and aligned with the standards that were being applied in the rest of the commercial shipbuilding industry,” he said.
When working on industry guidance, incidents like Piper Alpha and Macondo, where lives were lost offshore, have always been at the front of Mr Spackman’s mind, he said. “One of the things I keep on my desk, so that I can see it every day, is a list of rig accidents that have occurred and the loss of life that occurred with it because somebody decided to take a shortcut or not take a serious look at the risks involved, or deliberately ignored those risks.”
In 2014, Mr Spackman became Vice President of IADC’s Offshore Division and assumed the role of Vice President of Policy, Government and Regulatory Affairs. One of the highlights of his career has been the opportunity to tap into the expertise of his colleagues, both in the Coast Guard and in the oil and gas industry. “I’ve always sought and found persons who could serve as mentors,” he said. “I’ve had to rely on the knowledge of others throughout my career, both in the Coast Guard and in IADC. I’ve been blessed in having access to people who would make their time and knowledge available to me.”
Jim Rocco, a fellow Coast Guard alum who has been with IADC since 2015 and currently serves as Senior Director, Government and Industry Affairs-Offshore, will succeed Mr Spackman at the association. Mr Rocco will liaise with regulatory authorities and trade association representatives, respond to regulatory and standards development proposals, advise IADC’s regional representatives and staff in addressing matters of regulations and standards development, and serve as IADC’s representative at IMO meetings.
“For over 27 years, Alan has engaged in an extraordinarily wide variety of offshore safety and regulatory issues to the great benefit of the industry,” Mr Rocco said. “The experience and knowledge accumulated throughout this period has been invaluable to IADC membership. Alan’s acumen on particularly intricate and technical matters has always provided an effective and pragmatic approach to progressing some of the most intractable issues. His unique and adept insights will certainly be missed.” DC