HSE&T Corner
GHS compliance: What does it mean to you?
By Christine M. Lederer, Parker Drilling
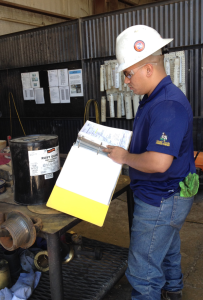
The use of chemicals is fundamental to all economies, including the oil and gas drilling industry. Hazardous chemicals have the potential to cause injury to employees who work with and around them and, in a worst-case scenario, exposure to hazardous chemicals can be fatal. For example, in 2007, an employee died from an apparent chemical overexposure while working on a drilling rig. When the employee began showing signs of dizziness, the employee was sent to the doghouse while the crew continued to run more than 25 stands of pipe in the hole. The employee was later found stumbling and fell to the ground, and he was eventually taken to a medical center where he died. As the example illustrates, it is essential for chemicals to be managed safely.
It is important for employees to be aware of all chemicals onsite, the hazards they present to people and the environment, and the means to control those hazards. Arming employees with knowledge about the hazards of certain chemicals used in the drilling industry could mean the difference between life and death.
Background
When the Occupational Safety and Health Administration’s (OSHA) Hazard Communication Standard (HCS) was first promulgated in 1983, it covered only the manufacturing sector. It was later expanded to cover all industries where workers may be exposed to hazardous chemicals. Its purpose was to ensure employees were aware of the hazards of chemicals.
Chemical information was generally disseminated to employees via information included on labels placed on the chemical containers and within the material safety data sheet maintained by the employer. Employees also learned about the chemical information through training. However, depending on where chemicals were manufactured or who shipped them, the information was not always consistent. Also, descriptions and symbols for the hazards of a chemical were not aligned.
To add even more complexity, language barriers or even illiteracy sometimes prevented industry employees from fully understanding the hazards associated with the chemicals to which they were exposed. These challenges increased the likelihood of the hazards not being properly communicated to employees.
Recognizing the need for a more uniform and consistent way to communicate hazards of chemicals, the United Nations adopted the Globally Harmonized System of Classification and Labeling of Chemicals (GHS) in 2002 to address classification of chemicals by types of hazard and proposed harmonized hazard communication elements, including labels and safety data sheets. To date, there have been six revisions to the GHS (the latest revision, not yet published, was made earlier this year), and it has been implemented by 67 countries.
OSHA revised the HCS in 2012 to align with the United Nations’ GHS. The revised standard – referred to as HazCom 2012 – has changed “from a performance-based standard to one that has more structured requirements for the labeling of chemicals,” according to OSHA. The main reason for the change was to ensure standardization of hazard classification, labels on hazardous chemicals and format of safety data sheet (SDS), formerly the material safety data sheet (MSDS).
GHS requirements
The major changes associated with adoption of GHS impose more requirements on chemical manufacturers and importers, who are required to (i) determine hazards of chemicals they produce or import; (ii) use a label that includes a signal word, pictogram, hazard statement and precautionary statement for each hazard class and category; and (iii) provide safety data sheets in a new format with 16 specific sections. They must be compliant with these requirements by 1 June 2015. Distributors may ship products labeled by manufacturers under the old system until 1 December 2015.
Since the bulk of the requirements fall on manufacturers, employers have fewer GHS requirements. The deadline for employers to provide training to employees on the new label elements and SDS format was 1 December 2013. By 1 June 2016, employers must ensure all alternative workplace labeling and their hazard communication program are updated. Additionally, employers must provide training for newly identified physical or health hazards by this date.
Compliance recommendations
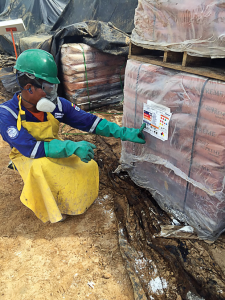
The first thing to remember about compliance is that HazCom 2012 governs only hazardous chemicals. Information about each hazardous chemical should be easily discernable from the product label or SDS. Drilling rig sites typically have quite a few hazardous chemicals, and the better practice may be to uniformly apply the same requirements for each chemical onsite in order to avoid the risk of certain chemicals (possibly hazardous) inadvertently being excluded. The following are compliance recommendations for each of the required elements:
1. Written hazard communication program. A hazard communication program for workers potentially exposed to hazardous chemicals must be prepared and implemented. The program must describe how the employer will address the requirements related to labels, SDS’s and employee information and training.
Drilling industry considerations:
a. The corporate program needs to address how third-party chemicals will be treated, such as how access to SDS’s will be provided to third-party employees, methods for transmitting precautionary measures and any special onsite labeling system, if one is utilized.
b. While a corporate program will suffice, each rig or facility will need to have a copy of the program and must have additional site-specific information, such as:
i. The person responsible for various aspects of the program.
ii. The location of where written materials will be made available to workers.
iii. A hazardous chemical inventory for the facility. The inventory may be kept by common name or chemical name. The important aspect is to make sure that the identifying name on the inventory can be found on the SDS and the label of the chemical. Remember to include chemicals in all forms – solids, liquids, gases, vapors, fumes and mists. For example, welding rods may be considered hazardous and should not be overlooked.
2. Labels. Manufacturers and importers must include the following information on labels: product identifier, signal word, hazard statement(s), pictogram(s), precautionary statement(s), and name, address, and phone number of responsible party.
Drilling industry considerations:
a. Hazardous chemicals at the facility must be labeled.
b. While maintaining the original label on a container is the best and easiest option, custom labels may be used as long as personnel have access to specific information about physical and health hazards of the chemical. This information should also be included in the hazard communication program.
c. Chemicals in portable containers that an employee intends to use during his shift are not required to be labeled; however, it is good practice to have a label that minimally includes the product name and any associated hazards with the chemical it contains.
3. Safety data sheets. Manufacturers and importers are required to develop or obtain an SDS for each hazardous chemical they produce or import. Manufacturers, importers and distributors are responsible for providing a copy of the SDS at the time of the first shipment and when the SDS is updated with new and significant information. If one is not received (or it is not appropriately completed), it is important to request an SDS (and one that has the required information).
Drilling industry considerations:
a. SDS’s may be maintained in hard copy or electronically. However, due to the limited access to computers on a drilling rig, it is recommended that a hard copy of SDS’s be maintained in a binder that is accessible to personnel on site.
4. Information and training. With regard to information, employees must be informed of HazCom 2012, where chemicals are located on site, and the workplace hazard communication program, including where and how they can access it. Training must include identification of the hazards of chemicals in the work area, how to detect the presence or release of a hazardous chemical and measures to be taken to protect themselves against these hazards. Training should also include details of the workplace hazard communication program. If the required GHS training on the new label elements and SDS format has not been provided to employees, this should be done as soon as possible. The next required training deadline is 1 June 2016 for training on any newly identified physical or health hazards.
Drilling industry considerations:
a. Because of the difficulty in finding time for training during drilling operations, it may be beneficial to include initial HazCom 2012 training, as well as GHS training, in a RigPass course before the employee reports to work. Another option may be to provide online training that employees can access before reporting to work or when they are off-tour.
Conclusion
Safe use and handling of chemicals is critical to the oil and gas drilling industry. OSHA’s adoption of GHS is a step in the right direction. Uniform and consistent labeling and safety data sheets, in addition to training, will provide employees with knowledge about the hazards of chemicals with which they work and reduce both short-term and long-term risks to health, safety and the environment.