Fuel consumption, overload capacity among critical criteria in selection of generator sets
By Steve Besore, MTU Detroit Diesel
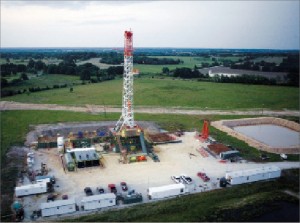
Modern horizontal drilling techniques used in oil and gas exploration require rugged, reliable and fuel-efficient on-site generator sets to supply electric power for the drawworks, drilling, mud pumping and camp loads. Today’s rigs have to drill deeper and faster than ever before. In addition, they have to use unconventional techniques, such as horizontal drilling and fracturing, to improve extraction from less permeable geologic structures such as shales.
Today’s drilling realities require more power than conventional wells did and have given rise to the development of the AC/DC SCR drilling rig powered by multiple generator sets.
While AC/DC electric rigs with SCR controls dominate petroleum exploration today, operators are constantly looking to increase total power availability, reliability and fuel efficiency. Generator sets must deliver high specific power, low fuel consumption and less maintenance.
AC/DC RIGS WITH SCR
Drilling rigs tend to be classified by the type of power used to operate the equipment on the rig:
• Mechanical rigs use dedicated diesel engines to provide motive force for the mud pumps, drawworks, rotary drill table and other loads through a system of clutches and transmissions.
• Hydraulic rigs have dedicated diesel engines running hydraulic pumps, which provide power to the necessary equipment.
• DC/DC electric rigs use dedicated diesel-electric direct-current generators to power DC motors that run the equipment.
With mechanical, hydraulic and DC/DC systems, individual engines are dedicated to single functions such as driving the mud pump or operating the drawworks. A failure on any one engine can halt drilling altogether.
The majority of new rigs today are AC/DC electric rigs with SCR controls, which use multiple diesel-electric generator sets running in parallel to produce the two to four megawatts of power needed at the drill site, including the power needed for camp loads such as lighting, heating and air-conditioning for crew quarters. Power is generated as alternating current (AC), then converted to direct current (DC) by an SCR unit, so called for the banks of silicon-controlled rectifier semiconductors that it contains. The SCR unit allows precise control of the flow of power to any of the rig’s DC motor loads while the generators run at a constant speed.
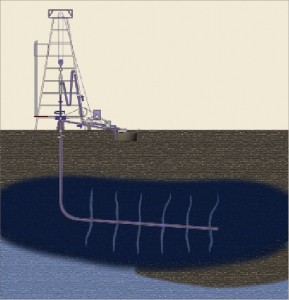
The number of generators needed by a rig varies with the depth of the drilling operation. Generator sets can easily be added to the AC/DC SCR-powered rig to match power requirements, making this a flexible design. The number of generator sets running at any one time can be varied depending on total load in order to save fuel.
This configuration also improves reliability because a failure of one of the generator sets does not necessarily cause a shutdown of drilling operations, even though it may reduce the total amount of power available. An additional advantage is that individual units can be taken offline for maintenance without greatly affecting the drilling operation.
GENERATOR SELECTION CRITERIA
When selecting generator sets to power a modern drill rig, these attributes are key:
1. Base frame stiffness, durability: A prerequisite for any electric drill generator set is rugged construction. The stiffness of the generator set base is critical to its longevity because any distortion could affect the alignment of the coupling between the engine and alternator, resulting in severe vibration and damage.
Ordinary structural steel does not have the necessary stiffness to prevent base frame distortion under severe handling or if placed on uneven ground. A base frame that uses high-strength, low-alloy steel, such as A572 steel, can withstand rigorous operating conditions.
A three-point mounting system with rubber vibration isolators provides more stability of the engine generator.
2. Ratings and performance characteristics: Rig generator sets are designed for continuous operation and therefore are conservatively rated in terms of their kW output. A typical rig generator set has a nameplate rating of about 1,100 kW, although larger and smaller units are available.
Since these units are likely to be subjected to severe service, generator sets with a 10% overload capability beyond their nameplate rating will meet most requirements. While engines on typical commercial 60 Hz generator sets operate at 1,800 rpm, well servicing companies have found that engines that operate at 1,200 rpm have a better record of longevity in the field.
3. Overload capacity: Due to the severity of operating conditions in the field, generator sets are often called on to deliver maximum output — and then some. Generator sets should have at least a 10% overload capability beyond their nameplate rating. For further assurance, compare the ratio of cylinder displacement to rated horsepower of the generator drive engine. Generally, engines with a larger displacement-to-horsepower ratio combined with a longer piston stroke will have more built-in reserve horsepower and torque than smaller, shorter-stroke engines of the same horsepower rating. They will also exhibit greater fuel economy and durability.

4. Fuel consumption: Since rig generator sets operate continuously, fuel consumption accounts for the largest operational cost. Just a few percentage points of better fuel economy can add significantly to the bottom line. Diesel engines tend to be most fuel-efficient in proportion to their output when operated at 100% of their rated load.
Engines are typically rated in terms of their brake specific fuel consumption (BSFC), which varies with the percentage of rated load. The BSFC rating allows specifiers to compare the fuel economy of generator sets before the units are in the field. For 1,200-rpm generators sets with a rating of about 1,100 kW, BSFC should be less than 200 grams of fuel per kW-h generated.
For maximum fuel economy, always operate the generator sets as near their nameplate rating as possible.
Figure 3 illustrates that different engine manufacturers have different ratios of cylinder displacement to brake horsepower (BHP). This ratio is an important factor in a generator set’s ability to respond quickly to changes in load and maintain voltage and frequency. Generator drive engines with the highest displacement-to-BHP ratio have more reserve horsepower, low fuel consumption and more durability.
Figure 4 shows the fuel efficiency advantage that a large displacement-to-BHP ratio confers for Brand X. Since diesel engines are most fuel-efficient at full power, it is important not to oversize the generator sets for the job.
5. Oversized alternator: While the SCR unit on AC/DC rigs allows for efficient and precise control of power to the various DC motors loads, it causes the current in the system to lag the voltage, resulting in a low 0.7 power factor (PF) load on the generator sets. Ordinary generator sets are designed to operate optimally at about a 0.8 PF. The 0.7 PF load on the generator sets causes field heating in the alternator, and unless the alternator is properly oversized, damage can result.
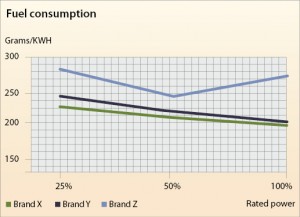
For a 1,200-rpm generator set with about 1,100 kW of capacity, look for its alternator to be oversized to at least 1,750 kVA to meet the low PF requirements. Also look for a 50°C ambient rating and minimum 80°C temperature-rise capability.
6. Control and monitoring: Precise control of the generator engine’s speed and operating parameters yields optimal regulation of the power output and quick response to changes in the load. Generator sets with engines that feature an integrated electronic engine governor and electronic engine management system provide accurate control, protection and monitoring.
These systems will also monitor alarm conditions and protect the engine from damage. They are also capable of communicating with external control systems for remote monitoring and control of the generator sets. This can be convenient when paralleled generator sets need to be started or stopped to match the load conditions. Mechanical gauges on the generator set skid should display variables such as lube oil pressure, oil temperature, engine coolant temperature, engine speed and operating hours.
7. Maintenance requirements: All diesel engines require periodic maintenance to ensure good performance and reliability. Besides regular inspections, the most important maintenance procedure involves changing the engine oil approximately every 10 days or 250 hours of operation. Generator sets that feature an engine-mounted lube oil centrifuge as standard equipment reduce the downtime required for oil changes. This device can significantly extend the lube oil change intervals, save money on oil and filters and increase generator set availability.
8. Single-source supplier: Generator sets from a single-source supplier that manufactures and tests the complete drill modules in a factory setting can mean a higher-quality product and faster repairs.
CONCLUSION
Today’s deeper wells and horizontal drilling techniques require more power than conventional vertical wells and have given rise to the development of the AC/DC SCR rig powered by multiple generator sets. While these rigs represent the current state of the art, operators are constantly looking for ways to increase total power availability, reliability and fuel efficiency as a way to minimize costs and maximize returns.
Generator sets that are designed for oil and gas rigs have the rugged design features and performance that ensure reliable operation and low maintenance. By comparing specifications such as manufacturing quality, reserve power, control/monitoring functions and fuel consumption, drillers will be assured of selecting generator sets with the lowest operating cost and the best reliability.
The very best choice in designing or upgrading drilling rigs is to power the rig with VFD drives. The use of these drives using AC motors are by far a better choice due to the power factor these systems operate. This makes the complete system for superior to a SCR or DC/DC system, no damage due to stalls and less maintenance (no brushes) in AC motors.
Hi Sir.
It`s nice to meet you.
We are ACE Plantech in south Korea.
First, thank you for your analysis of Drilling rig and its related articles above
We, ACE Plantech Co., Ltd., are a leading company which is exporting and importing various machinery equipment, chemical and its related parts.
so, we are now searching the supplier or manufacturers of spare parts of [AC SCR drilling rig (Mitsubishi electric corporation made)]. would you mind informing me the supplier of factory, company ?
sorry for inconvenien caused you and waiting answer
Thank you