From intervention to innovation
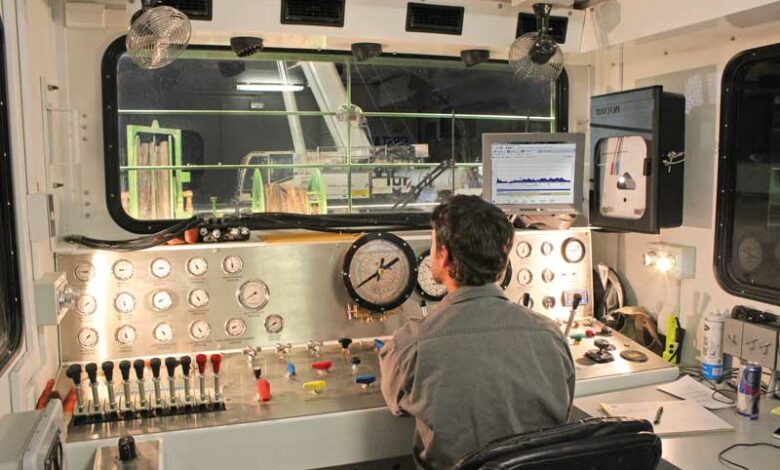
Coiled tubing provides greater reliability as it shifts to higher-profile role in completions
by Katie Mazerov, Contributing Editor
More than 30 years after it emerged onto the oilfield, coiled tubing (CT) is moving beyond its niche, especially in the North American sector. Once primarily limited to well servicing and workover operations, CT is increasingly a planned and integral part of the completion strategy. Companies are now seeing it as an enabler that facilitates everything from drilling out composite frac plugs in plug-and-perf operations to running sophisticated logging tools downhole.
Responding to industry demands, CT has become longer, stronger and thicker, performing under live well conditions that are deeper, hotter and more highly pressurized. Alongside those advances, computer models that determine fatigue life of the tubing and the welds that connect sections of tubing are boosting reliability in the field.
Outside of North America, including sectors that don’t rely on hydraulic fracturing, CT is still predominantly an intervention tool used widely for cleanouts, sand removal and nitrogen kick-offs to get a well flowing using the smaller, standard 1 ½- to 1 ¾-in. tubing. In North America, it’s a different story altogether. Driven by the unconventionals, innovation appears to be happening at a faster pace.

(Image courtesy of Schlumberger)
“In 1993, we could sum up the CT market as 25% acidizing and stimulation operations; 25% wellbore cleanouts; 25% nitrogen kick-offs to blow out the drilling mud or water so wells could begin producing, and 25% for everything else – fishing, running logging tools, drilling, etc,” said Ken Newman, founder of Coiled Tubing Engineering Services (CTES), now a division of National Oilwell Varco (NOV). “That was the world until hydraulic fracturing,” Mr Newman said. CTES provides consulting services and well intervention/drilling modeling tools to the industry. “Today in North America, some 85% of the CT business is drilling out frac plugs and cleaning out frac sand.”
Jason Skufca, Staff Engineer, Well Intervention for ConocoPhillips and Senior Chair of the Intervention & Coiled Tubing Association (ICoTA), said the North American unconventional market has been the “biggest driver for increasing CT size and reliability and for increasing the extended-reach capabilities of tools that aid in facilitating CT to reach total depths. That increased need for reliability spans across all diameters used globally and applies to the offshore sector, including deepwater.”
Some hydraulic fracturing technologies, including interventionless solutions involving sleeves activated by disintegrating balls, or large flow-through inside-diameter plugs with dissolvable balls, are looking to eliminate usage of CT. Other technologies, such as CT-activated frac sleeves, aim to further extend the applications for the oilfield workhorse, he said. “Also, as the industry has moved into deeper, hotter and higher-pressured fields, CT has evolved as a method for conveying the downhole tools needed for those environments.”

As operators expand the applications for CT, often pushing the pipe to the limit or beyond its original intended purpose, reliability remains a key challenge, Mr Skufca said. “The combination of constantly working the tubing in highly deviated wellbores, high-pressure and extreme environments, such as H2S (sour gas) reservoirs, can damage the coil, resulting in premature failures. That is driving manufacturers to develop pipe that is less prone to that type of damage, as well as predictive software to help us determine if we can achieve our objectives of reaching total depth.”
Extending the reach
Operations that 10 years ago were typically done with 1 ½-in. diameter CT now require 2-in. diameter tubing that is more than 20,000 ft in length. “Shales, deepwater and highly deviated, extended-reach wells require larger-diameter tubing to reach farther,” said Dale Klink, VP of Strategic Business Initiatives for NOV Intervention and Stimulation Equipment/Quality Tubing, part of NOV Completion & Production Solutions.
“The tubing must support its own weight or, in the case of shales, deliver more fluid at higher pressure for stimulation. That capability results in a smaller footprint, quicker rig time and the ability to do multiple frac stages in one run without having to kill the well to remove the isolation plugs.”
Today, 60% of CT manufactured is 2-in. diameter or greater, with 130,000 psi or greater yield strength, up from 70,000 psi yield strength introduced 35 years ago. This capability was originally developed for the offshore sector, where axial loads, or the ability of the tubing to carry its own weight when conveying perforation guns, is critical, Mr Klink said. “Lower-strength CT required operators to drill 1,500 ft of extra wellbore and release guns after firing because there wasn’t enough strength to pull out of the well. Stronger tubing, combined with the larger diameters, has facilitated extended-reach, tubing-conveyed perforations and the ability to retrieve and reuse the equipment while drilling less wellbore.”
In 2014, in what NOV believes to be the longest CT operation to date, 35,770 ft of 2-in. CT was run in a Gulf of Mexico extended-reach operation, Mr Klink said. The operator is now asking for 40,000 ft. “Now, the equation becomes more difficult because we start running out of available strength for the tubing to support its own strength. If we go to a smaller diameter, the pressure required to overcome friction to pump the fluid becomes excessive. It’s always a balancing act between the weight of the CT and providing enough ID to do the work downhole.”
As NOV is already working on next-generation tubing with yield strength of more than 150,000 psi, injectors, pressure control equipment and power packs that rotate the spools also must be upgraded, while the wall thickness of the tubing is increasing to hold the pressure, Mr Klink said.
The company is developing joining techniques that would allow CT strings to be shipped in two pieces and joined at the wellsite. This capability would overcome a significant limitation – how much CT at these diameters can be transported. Many places have weight limitations for moving equipment along roads and highways. “This is especially true in the shale plays outside North America, where the infrastructure is less developed,” Mr Klink said. “The infrastructure in developing countries will be a very limiting factor in how fast this technology comes to those markets.” The technique also would facilitate the removal and repair of worn-out sections of tubing, extending the life of the entire string.
Enabler for fracturing

In the US unconventional sector, Cudd Energy Services is seeing more CT units scheduled in conjunction with the hydraulic fracturing process. They’re being used to handle the increased number of frac plugs that need to be milled immediately after stimulation, especially as laterals have become longer. “Before the unconventional boom, CT was primarily a production tool used to clean out sand and do some in-situ stimulation,” Senior VP Dan Bohannon said. “Now it is used right behind and in front of the hydraulic fracturing process.”
Cudd has 53 units working in the continental US. Customers’ need for more information from the reservoir is driving increased implementation of fracturing with CT, a technique utilizing CT to isolate zones, perforate and execute down the CT annulus so operators can target zones quickly. The tool facilitates the use of a CT-deployed resettable downhole packer, a technology licensed from ExxonMobil Upstream Research Company, which moves from zone to zone, eliminating the need for perforating guns.
The packer is incorporated into the bottomhole assembly. “The zone isolation process allows us to fracture multiple zones in a single trip,” Mr Bohannon said. “We set the packer, perforate and hydraulically fracture the zone. The packer is then equalized, released and moved up the hole to the next zone of interest, and we repeat the process downhole. This allows decisions to be made in real time. Operators are seeing the benefits of greater flexibility downhole and time savings, which equates to reduced costs.” The packer is being used in the Permian Basin, western Oklahoma and the Rocky Mountain region.
Cudd recently acquired a technology designed to work in conjunction with the company’s e-coil tool, a specialized CT pipe, or e-line, which provides real-time images, logs and data of all downhole operations. “Anything that requires surface realization of downhole positioning will be revamped by these types of tools,” he said. “This is proving to be the case in multilateral wells. It used to be a peck-and-hunt operation for CT to determine depths. Now, with directional tools deployed on the CT, operators can better pinpoint where they are downhole and can target a specific leg of a multilateral well. This gives us a lot of flexibility in approaching problems in the wellbore.”
As CT has become more efficient, with larger, heavier pipe and increased annular velocities, it also has become more dependable. “As the pipe has become bigger, the injectors have gone from 35,000-lb hookload capability to 140,000-lb hookload capability,” he said. “The CT units are more technology-driven, equipped with computers and satellites that stream data remotely.”
Fiber optic telemetry

In response to the challenges of increasingly long and deviated wellbores, Schlumberger is launching two additions to its ACTive family of live downhole CT services in March. “When we look at the way wells are being drilled and completed today, more than 70% are highly deviated or horizontal,” said Teoman Altinkopru, VP Well Intervention Marketing and Technology, Schumberger. “In many extended-reach wells, the total length of the well is more than three times the true vertical depth, and that trend is increasing. The growth of horizontal displacement has far exceeded the capabilities of tractors, especially when we factor in the gravity limitations of using slickline and wireline.”
Continued reliance on CT and the growing need for live downhole measurements for conveying tools and perforating in extended-reach wellbores led to the development of ACTive OptiFIRE CT real-time selective perforating and activation system, which provides the ability to perforate up to 10 zones at different depths and in one run. This helps to achieve proper depth correlation between each detonation using fiber-optic telemetry-enabled CT. The system, which fires one gun at a time, saves time and cost over conventional methods, where guns are deployed in one run per zone, Mr Altinkopru explained.
Because signals are conveyed with fiber-optic telemetry, there is no need to pump fluids downhole to initiate detonation. “This enables operators to create an underbalanced environment to minimize formation damage while perforating,” he added. “The fluid required by conventional perforation systems prevents the opportunity for underbalanced perforating.”
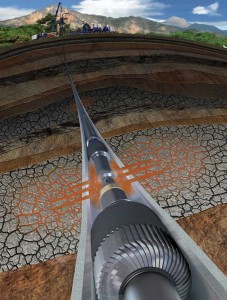
Using the same telemetry service, ACTive Straddle CT real-time multi-set inflatable packer is a thru-tubing system that can be positioned with wireline depth accuracy using real-time downhole pressure readings. The small, 2 1/8-in. packer assembly is deployed on the CT and inflated to specified pressures. “The inflation pressures need to be very accurate,” Mr Altinkopru said. “Without real-time measurements, we do not have that assurance because the packer inflation fluids must go through the entire length of the CT. This imposes backpressure and, therefore, renders the pressure readings from the surface inaccurate.”
To ensure CT pipe maintains integrity, Schlumberger has developed defect recognition software that complements the CoilScan real-time pipe inspection service. The service works on a magnetic flux leakage system that provides 360° coverage of the pipe, including outer diameter, inner diameter and wall thickness, to detect corrosion, pitting or other defects. “CT pipe is the most used piece of equipment in the oilfield, constantly bending and straightening,” Mr Altinkopru said. “Maintaining the integrity of the pipe during operations is critical. The software enables data interpretation in real time in order to predict problems and make operational changes during the job.”
CT is designed to wear out and be replaced, and the carbon steel of the tubing has few limitations, in large part because of the relatively short exposure time in the well. However, H2S (sour gas) environments, and more recently, microbial corrosion, can impact the steel and requires the cooperation of service companies, as well as operators, to ensure water is treated properly. NOV’s 100,000-psi yield strength CT is approved for sour-service use, with the caveat that the water has been treated.
Improved fatigue prediction
CT fatigue is inevitable during the course of routine field operations. Historically, fatigue-prediction software has utilized a non-linear approach to calculate this damage. “Fatigue life is cumulative and highly dependent on the circulating pressures being pumped through the CT as the CT is being bent and straightened during deployment in and out of the well,” explained Edward Smalley, General Manager, NOV Intervention and Stimulation Equipment/CTES, part of NOV Completions & Production Solutions. “Early in the life of a CT string, the bending events associated with a particular field operation may use 3% of the CT fatigue life, but performing that exact same operation near the end of the string’s life may yield fatigue damage double that.”
NOV has introduced a linear fatigue calculation model so that a particular field operation will impart the same amount of predicted fatigue damage on the CT regardless of whether the string is new or nearly ready for retirement. “The linear fatigue calculation software makes it easier for field crews to determine how many more trips they can make with the string,” Mr Smalley said. The software includes an added feature that similarly models the fatigue damage of the bias welds that connect long sections of tubing to create a 15,000- to 20,000-ft string of CT.
“Historically, the fatigue life of these welds was de-rated 20% versus the parent CT material, a formula that worked fairly well in 5,000-psi or less conditions,” Mr Smalley said. “However, when the CT is run in the higher-pressure regimes, such as 8,000 psi or higher that we’re seeing in long horizontal wells, that correction factor doesn’t seem to be as reliable. To address this, we’ve cycled sample bias welds to failure under various pressures at the mill in order to develop bias weld fatigue models instead of using a single de-rating factor.” The new model is suitable for any environment but is expected to be of greatest benefit in deepwater or high-pressure shale environments.
As part of the same software package, NOV has developed torque-and-drag modeling for use when pulsation/vibration devices are utilized on the end of the CT. These tools reduce the amount of sliding friction and slip-stick, allowing the coil to be pushed farther in extended-reach wells. “Until recently, operators couldn’t predict how much farther they could reach in the well when using these tools,” Mr Smalley said. “By modeling the vibration devices in the software, operators can determine if they can get an additional 1,600 or 1,800 ft out into the horizontal section, which may enable them to reach the last composite frac plug that needs to be milled out. In today’s oil and gas environment, going farther is the name of the game.”
ACTive, Straddle, ACTive OptiFIRE and CoilScan are marks of Schlumberger.
Click here to read a web-only article and view a video on how one company is expanding the intelligence of coiled-tubing services.