Drilling & Completion Tech Digest
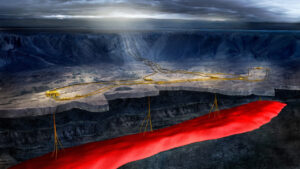
Norske Shell, Kongsberg collaborate on integrated reservoir with digital twin technology
Norske Shell and Kongsberg Digital have developed a digital twin of the Ormen Lange deepwater gas field using the Kongnitwin Energy solution. The new digital twin will feed into the existing onshore digital twin developed at the Nyhamna gas-processing facility to create a fully integrated reservoir-to-market digital twin.
The first version of the Ormen Lange digital twin comprises primarily data integrations and visualization of subsea 3D models, including production pipelines, well surface locations and wellbore paths, seabed bathymetry data detailed around the production templates, built documentation and drawings, and real-time data from distributed control systems and plant interfaces.
For disciplines and teams across the initial Ormen Lange user base – like subsea maintenance, wells, flow assurance, production technology, reservoir engineering, process engineering and operations – the twin provides unified data for everyone to access across the same work surface. The companies will continue to develop new ways of working with specific use cases. The first version of the Ormen Lange digital twin was released to users in Norske Shell in May.
Norske Shell began working with Kongsberg Digital in October 2019 to develop the Nyhamna Dynamic Digital Twin. It has been operational since January 2020 and is evolving continuously through monthly product releases, focusing on safe, effective and integrated work processes and optimization of production and energy use.
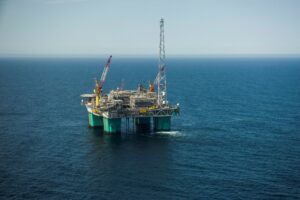
3D gaming technology helps to digitalize subsea wells
Neptune Energy recently digitalized its subsea wells in Norway, using a data visualization platform based on 3D gaming technology to enhance drilling and production efficiency, as well as reduce time and costs.
The new digital twins of Neptune’s wells were developed in collaboration with InformatiQ. The company’s GeologiQ cloud-based software combined raw E&P data in 3D and 2D environments and used 3D gaming technology, which allowed Neptune to visualize both historical and live data to improve well design and incorporate learnings in future operations.
The adoption of the software for Neptune’s assets follows the creation of digital twins of several of the operator’s platforms in the Norwegian, UK and Dutch sectors of the North Sea, enabling offshore site inspections and maintenance planning to be carried out from onshore.
Neptune has also implemented virtual reality technology, originally developed to train astronauts traveling to the International Space Station, on the Neptune-operated Gjøa platform.
“By digitalizing all subsea wells within our Norwegian portfolio, we have greatly improved our ability to plan interventions,” said Thor Andre Løvoll, Neptune Energy’s Director of Drilling & Wells for Norway.
Click here to view a video demonstrating the digitalization of Neptune’s wells.
Nabors, Halliburton integrate digital well planning, onsite execution
Nabors and Halliburton recently announced that they have integrated Nabors’ SmartROS platform with Halliburton’s Digital Well Program. Using Halliburton’s Well Construction 4.0 platform, digital well planning will be connected with onsite execution through Nabors’ SmartRig system.
Traditional methods still utilize static documents for the well plan. This legacy process results in limited validation of the plan and inconsistent communication between the parties, fails to capture changes that may be required based on operational conditions, and impacts the ability to capture and leverage lessons learned.
“In addition to providing our customers with a seamless digital experience for interactive rig activity planning, scheduling and coordination, this integrated offering also enables optimization of the drilling recipes and workflows for automated drilling and wellbore placement,” said Subodh Saxena, SVP for Nabors Drilling Solutions.
The technology uses an open architecture so it can be integrated seamlessly into existing workflows.
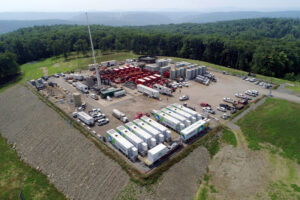
E-frac system reduces emissions for Chesapeake by 32%
Halliburton and VoltaGrid announced the successful deployment of an electric fracturing solution. The project is the first pad in a multi-year contract with Chesapeake Energy, with more than 140 stages in the Marcellus.
The solution combines Halliburton’s all-electric fracturing spread, featuring the Zeus 5,000-hp electric pumping unit, with VoltaGrid’s advanced power generation system. The solution reduced emissions for Chesapeake by 32% and applied over 25 MW of lower-carbon power generation by leveraging Chesapeake’s local field gas network.
Chesapeake credited the technologies for reducing emissions and driving additional fuel savings.
Unlike other pumping units that may average around 3,000 hp, a single Zeus pumping unit delivers 5,000 hp at over 22 bbl/min. Halliburton’s all-electric spread features a large-bore, dual-manifold trailer, which allows the Zeus pumps to achieve higher rate capacities with fewer failure points. With its electric-based powertrain, the pumping unit delivers 40% higher performance than conventional pumps. This spread also provides electric blending, wireline and ancillary equipment.
Using VoltaGrid’s emissions portal, Chesapeake can track and analyze real-time emissions and carbon intensity throughout the completions operation, allowing the operator to maximize fuel efficiency and minimize emissions.
Filter carts installed to help to improve uptime of wireline tensioners
Logan Industries, a hydraulic repair, manufacturing and rental company, recently completed the manufacture, assembly and installation of 64 filter carts as part of a continual monitoring program for a drilling contractor’s subsea tensioner equipment, ensuring greater uptime in the field.
The two companies developed the program to enable full uptime for the contractor’s wireline tensioner units (WLTs) on four of its drillships offshore Africa. Each vessel has 16 WLTs onboard, which are critical for holding a subsea riser up in the water column and enabling drilling, completion and intervention work.
A key focus of this program involved preventive maintenance in the form of actively filtering the fluids running through the WLT. Logan developed a unique filter cart in order to keep WLT fluid cleaner for longer, enabling longer service life between maintenance overhauls of the units.
Logan’s filter cart continuously filtered and polished the WLT fluid while it was still in service, monitoring the health of the fluid. This type of filtering was especially difficult because each side of the fluid path for the pump moving the fluid is pressurized. This introduced unique design challenges and required lengthy testing and tuning to ensure adequate performance ahead of field deployment.
The program began in Q2 2019, followed by six months of testing and tuning the prototype. The delivery of the first set of 16 assembled and completed units took place in March this year.
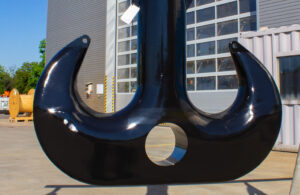
Huisman scales up additive manufacturing of crane hooks
Huisman recently successfully tested four 3D-printed 350-mt crane hooks under the supervision of Lloyd’s Register. The hooks are approximately 170×130 cm in size, almost nine times larger than the company’s first 3D-printed crane hook. They each weigh 1,700 kg and have a 350-mt loading capacity.
Huisman has been employing a 3D printing technique called wire & arc additive manufacturing to produce mid-size to large components with high-grade tensile steel. An important benefit of using this technique for crane hooks is the significant reduction in delivery time, at a cost that competes with forgings and castings, as well as a more consistent quality. The technique also offers higher control over process and material quality than conventional manufacturing techniques.
Huisman plans to expand the robotic workplace of its production facility in Sviadnov, Czech Republic, which currently holds three welding robots. By upgrading its capacity, Huisman will be able to produce crane hooks with a weight up to 5,000 kg. DC