Delivering technology alone is not enough; performance matters
Critical issues in drilling & completions with Mike Williams, vice president of sales, Schlumberger Drilling & Measurements
By Diane Langley, editorial coordinator

What are some of the key drilling and completions challenges facing the industry today, and how is Schlumberger responding to them?
With respect to drilling every year, the technology requirements are increasing. In 2010, we have seen increased requirements for technology to be able to drill ultra-extended reach wells, operate in higher temperatures and pressures than ever before, and deliver a quality product, which is the hole we help drill in the most efficient way possible. If the industry at large is to be able to exploit the remaining resources cost effectively, then it is not simply technology capability but, more importantly, technology efficiency that is critical.
To deliver this, we have to look at how we measure our own performance and how we are remunerated for our services. New technology, while critical to the industry to move forward, is not enough. Today, Schlumberger Drilling & Measurements measures both reliability and performance in our clients’ terms. For example, how many feet were drilled before failure and how efficient were we in optimizing the drilling process to take the least possible time, while still ensuring system integrity and delivering a quality product?
By analyzing technology using these key performance indicators, we can drive our technology offering in a more effective way.
What technologies have been proven in meeting industry challenges?
A number of technologies have been commercialized or updated in 2010 to respond to these challenges, including higher output motors (ERTs), the PowerDrive X6 rotary steerable system (RSS), improved measurement-while-drilling systems with higher telemetry rates, and new or improved logging-while-drilling (LWD) systems such as the quadruple sonic or the latest versions of EcoScope multifunction logging-while-drilling service, which provides unique LWD measurements – sigma, spectroscopy and sourceless density.
I would like to focus on PowerDrive X6. Since its introduction in mid-2010, we have seen our RSS reliability increase by more than 30% and our drilling efficiency by over 10%. This improvement comes from building on previous tried-and-tested RSS systems but also from measuring and reviewing these systems’ performance and focusing on what matters. To repeat, it is critical to look at how far we drill before failure and how efficiently we do this.
How will the Macondo incident change the way your company conducts its operations, particularly in deepwater?

With recent events in the GOM, system integrity and technology functioning as it is designed to do first time, every time, is the absolute key priority for all in the industry at large today. The complete system functioning as it should is an absolute must. System reliability has never been as critical as it is today, particularly as we search for and exploit resources in harsher and harsher operating environments. With the Excellence in Execution program, Drilling & Measurements and Schlumberger at large strive to ensure the integrity of our piece of the overall operation every day. Never has been “get it right first time” been more prevalent or important. Any technology must work as advertised, work the first time, and do it in an efficient manner.
What steps has the industry taken to increase recovery rates over the past year or two?
While recovery rates are the ultimate concern of our clients, there is no doubt that any drilling services provider has a huge influence on whether a well produces to its full potential. This is covered by the “delivering a quality product” comment I made earlier. Simply drilling a hole is not enough. So, in the drilling services world, what does this mean?
First, position the well in the reservoir for maximum production potential. This means using the full benefits of LWD to ensure we are in the production sweet spot as much as possible. Today’s geosteering technology, such as PeriScope bed boundary mapper, allows the operator to see the formation boundaries around them not simply in close proximity to the wellbore but tens of feet away, in what direction and exactly how far away they are. Armed with this information, the well can be positioned much more appropriately to maximize production potential.
When coupled with the ability to take formation pressures in real time using the StethoScope formation pressure-while-drilling technology and to assess the mineralogy of the formations, we are drilling using EcoScope, as well as providing traditional resistivity, density neutron, the well can be positioned for maximum production.
All this information is worthless unless it is transmitted to the surface in an efficient and timely manner and acted upon by our clients and our own experts. Real-time steering decisions to access the sweet spot need real-time data. Whether we employ our latest Schlumberger incarnation of the TeleScope MWD with its high and effective mud pulse transmission rates or use the IntelliServe wired drill pipe, it is critical that we have the right data at the right time. These systems enable this.
The ability to steer the well reliably has always been of key importance, but with the geosteering techniques mentioned earlier, it becomes much more critical. Knowing where the reservoir sweet spot is but not having the ability to get there is worthless. Today, rotary steerable usage has become almost standard for these applications.
The Schlumberger PowerDrive systems have long been providing this ability, but as the applications become tougher, reliability and capability become more and more important. The Schlumberger PowerDrive X6 and PowerDrive Xceed RSS as described earlier provide the means to steer efficiently and reliably to the sweet spot identified with the latest LWD technologies.
With recent acquisitions, what new industry challenges has your company become aware of? What is being done to meet those challenges?

The recent mergers and acquisitions provide the industry a vast opportunity to improve by exploiting the synergies these mergers bring. A systems approach will provide the industry with a much more effective “fit-for-purpose” solution than trying to build one from a myriad of different providers’ components.
A case in point for Schlumberger is our ability to provide clients with a complete bottomhole assembly offering due to the recent merger with Smith. By integrating downhole directional drilling, MWD and LWD technology from Drilling & Measurements with bit, reamer and jar technology, we can provide a complete BHA package.
It should be noted the key word here is integrated. Simply putting a collection of pieces together is not integration. We are looking at how all these components fit and operate together to provide the best optimized drilling package. For example, are the bit and reamer cutting structure optimized with the RSS to provide the highest levels of drilling efficiency? Through this sort of optimization work, the service sector mergers will improve drilling efficiency and benefit the industry as a whole.
What areas of downhole breakthroughs is Schlumberger is working toward in the next 1-2 years?
Other than those already mentioned, we have a number of developments close to commercialization. Most notable is a revolutionary RSS that can generate doglegs (DLS) of up to 15° per 100 ft reliably and consistently. We are in advanced stages of field testing. Its importance cannot be underestimated. It effectively doubles the dogleg capability available from the RSS offerings of today, providing cost-effective solutions to wells requiring high DLS, removing the need to slide with conventional motors systems. It also provides consistent and repeatable DLS to ensure the target is reached in the most cost-effective manner while providing superior wellbore quality. Once in the target, it provides the most efficient method to steer to the reservoir sweet spot as identified by the LWD systems.
Other services that will become available are increased formation imaging capability, increased look-around look-ahead ability, and the ability to take formation samples while drilling.
How are operators and service companies working to improve the process of developing and implementing frontier technologies?
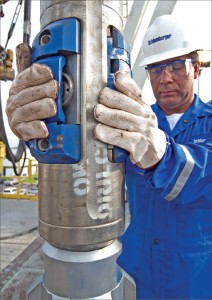
Communication is the critical component. A clear definition of what any potential technology will be used for, what conditions it will be required to operate in, both now and in the future, and the size and how many applications there will be are all critical pieces of information that ultimately decide whether a technology gets built or not. As the cost of technology development continues to rise, it is essential that the service sector spends its R&D dollars in the right place as there are obviously financial constraints on this budget.
Operators who clearly communicate exactly what their need is, how many opportunities for the potential technology exist, when it’s needed and what functionality is required are most likely to get a technology that fits their requirements. This information will immeasurably increase the chances of any potential technology being developed.
Further input as we go through the R&D cycle is key, particularly if requirements change. Most important of all is the opportunity to field test any technology and patience while the development teams go through the inevitable cycle of modifying the initial test tools to provide a commercial and fit-for-purpose product.
The service sector wants to invest its R&D money wisely but needs the operators’ help to do this. In the last few years this communication has improved drastically but can always be improved. It is this communication and the ability to test any technology developed in true applications multiple times that lead to the development of effective new technology.
As sharpening performance and cutting costs are usually operating imperatives, what issues stand in the way of achieving these goals?
There are two ways to reduce the cost of drilling and completing a well. One, reduce the unit cost of all the components critical to the process, and/or two, increase the efficiency of the operation to reduce the time it takes, particularly the nonproductive time that often occurs.
With the recent industry downturn, competition between service companies has led to reduced cost in return for volume of work. Moving forward these unit costs may change with the introduction of new technology, but honestly the effect of this movement is relatively minor. The industry must focus on increasing its efficiency as this is where the most benefit will be derived.
The operators and service sector must work together to improve these efficiencies, and key to this is having aligned goals. Today, very few contracts between the two are based on performance or have a performance component. Many are simply based on operating time. This needs to be changed if the industry is to progress.
Operators must be willing to reward those providers who increase the efficiency of their drilling operation with performance bonuses, etc. Conversely, service providers who do not deliver must expect their remuneration to reflect their poor performance.
In a nutshell, any contract must align the operator and service company so that if the goals are reached, then the operator shares the savings with the high-performing service providers. If they are not reached, the service company can expect return to diminish.
In reality, this process is a little more complicated than setting up a simple time-based contract, but with a little thought, the objective setting and measurement of suitable key performance indicators, etc, is not impossible. In our experience, those operations where the operator and service provider are aligned deliver by far the most cost-effective results. Cost effectiveness, not cost reduction, should be the aim. If cost effectiveness is increased, then by default, cost reduction is achieved.
How does a technology like seismic-while-drilling benefit the industry as a whole? What are drivers/issues behind this technology?
Schlumberger has provided seismicVISION seismic-while-drilling (SWD) for many years. The ability to place the bit/BHA on the seismic section and look ahead to reduce positional uncertainty is especially important in exploration or appraisal wells where there are drilling hazards. The SWD measurements enable accurate time-to-depth conversion of surface seismic data and provide direct measurement of distances and indications of the structures ahead of the drill bit.
This enables drilling and well construction decisions, such as landing, salt-proximity steering, casing and coring point selection. Real-time velocity measurements can also be used to update pore-pressure predictions from the surface seismic, helping to avoid drilling hazards. Operators have eliminated the cost of sidetracks in offshore wells by using the seismicVISION service to land wells – in many cases modifying the original trajectories by more than 100 feet. The service has also enabled operators to acquire seismic data in boreholes where stability issues made wireline runs risky or even impossible.
Initial adoption of the technology was slow as the seismic-while-drilling service appeared to be complex due to the logistics and coordination issues surrounding the seismic source, rig-crane and/or boat deployment. In addition, each well has unique challenges that must be addressed individually to configure the appropriate acquisition program and associated logistics. As the technology has evolved over the past few years, and with the experience gained over numerous wells, these challenges have been overcome. seismicVISION activity has increased steadily as operators are recognizing the benefits of the seismic-while-drilling service to reduce drilling uncertainties.
How does a technology like rotary steerables benefit the industry? What are the drivers/issues behind this technology?
The premise of rotary steerable is simple: drill more efficiently with a conventional positive displacement motor (PDM). When drilling with a PDM, drilling efficiency is compromised every time it is necessary to slide to adjust the well’s trajectory. While sliding penetrations typically fall to less than half of those while rotating, and as wells get longer and longer, the efficiency effect becomes more marked until it becomes impossible to slide and directional control is lost. Rotary steerables are not more efficient drillingwise unless trajectory control is required. If not, then PDMs are still more efficient as they add downhole power to that supplied from surface and usually drill faster.
The future of rotary steerables is to become part of an integrated system with the PDM included.
So what benefit does RSS bring? First, increased drilling efficiency by negating the need to slide. Second, better wellbore quality – the slide/rotate sequences need for trajectory control with a PDM often produce inferior wellbore quality. Third, the ability to drill well profiles today that were impossible yesterday. Nowhere is this more apparent than when drilling extended-reach wells, where wells over 10-km long took over six months and had no directional control at extreme depth. With RSS, these wells can be drilled in a little over a month with full directional control all the way to TD.
In the early days, RSS was a high-risk proposition. Today RSS is a key component of most BHAs. Operators ask themselves why they are not using RSS rather than why. In 2010, Drilling & Measurements drilled over 15 million feet with RSS, and over half of its total jobs are now with RSS. We fully expect 70%-plus of all wells to use RSS technology in the next couple of years – RSS is simply a no brainer. But, as mentioned earlier, not instead of PDMs but in conjunction with PDMs.
What are the hard truths about drilling and about completions that companies are facing today? And what choices are being made to maintain a strong exploration future?
It all comes to one hard truth – how do we as an industry continue to exploit the remaining resources safely, efficiently and cost effectively to ensure a healthy future for all in the industry and ensure the future hydrocarbon provision for the world at large? This requires the continued and improved implementation of proper process and procedure to ensure the population and environment are protected, the development of cost-effective, fit-for-purpose technology and its application, the development of competent personnel to make the best use of key technologies and the alignment of the goals of the operator and service sector to drill and produce to the benefit of all, sharing in any successes delivered.
– PowerDrive X6, PowerDrive Xceed, EcoScope, PeriScope, StethoScope and seismicVISION are marks of Schlumberger.
How does Schlumberger address the issues with mud motors:
1) Reliability where trips are required every 150 – 200 hrs for service ?
2) Torque capacity ?
3) Cost ?
Thanks,
Mike Dib
Houston, TX