Companies take initiatives on the road to ensure safe driving
In-vehicle monitoring, awareness programs, journey management target one of industry’s biggest fatality sources
By Joanne Liou, Associate Editor

The North American shale boom has transformed the landscape of the industry far beyond the worksite. Its effect on communities, from employment to infrastructure and safety, has not gone unnoticed. Road traffic has also increased across multiple states, and companies are taking a proactive stance to address driving safety. Transportation incidents are one of the major causes of fatalities across the oil and gas industry.
From 2003-2012, transportation incidents accounted for approximately 40% of fatalities in the oil and gas industry, based on data from the US Bureau of Labor Statistics’ Census of Fatal Occupational Injuries. Of the 1,073 fatalities recorded in that period, transportation incidents accounted for 433. Kyla Retzer from the National Institute for Occupational Safety and Health’s Oil & Gas Safety/Health Program presented the data at an IADC Rig Moving Committee Meeting in April 2014. From 2003-2009, out of 202 vehicle fatalities, nearly 52% involved a pickup truck, according to Ms Retzer’s presentation. She cited the main causes of fatalities as lack of seat belt use, lack of resources and experience, the sense of urgency, and speeding.
Like many other safety and competency assurance programs, driving safety initiatives are not a one-time occurrence and are evolving with new technologies. Companies now routinely provide ongoing training for drivers, and new-generation vehicle tracking systems are providing constant monitoring of drivers. One of the major shifts in driving safety has been the industry’s implementation of in-vehicle monitoring systems, which track behaviors such as speeding. “
A tracking system affects behaviors and, more importantly, accountability,” Michael Stephens, Director HSE at Nomac Drilling, said. “It doesn’t matter if you’re a 5- or 10-year employee.” Monitoring systems can record data, such as time, speed, acceleration, deceleration and seat belt use. They also can measure a driver’s performance against specific parameters.
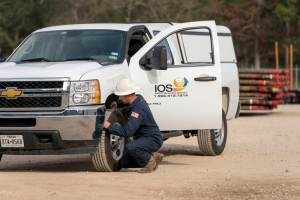
Approximately four years ago, Nomac Drilling began installing the Telogis GPS tracking systems equipped with speed alarms and alerts on company vehicles. A majority of the company’s 250-300 vehicles have been equipped, though some older vehicles do not have the system since they will rotate out of the fleet. For Nomac, the in-vehicle system is set up to permit a maximum speed slightly above most interstate limits. If the driver exceeds that limit, an alarm will sound. “The alarms remind them to slow down,” Mr Stephens said.
Alarms in the vehicle don’t serve to warn only the driver. If a driver exceeds the maximum speed limit, the system also sends email notifications to Mr Stephens and even to Nomac President Jay Minmier. “I make phone calls to drivers, letting them know of the alarm and to ask if they have a reason for driving fast; the answer is usually ‘no.’ I remind them of company expectations for safe driving and to slow down. I also notify their supervisor, who will take appropriate action, so there’s an accountability part. In the first couple of years, I had to make several calls a month. Now it is just a few a year,” Mr Stephens explained. “We also receive a monthly report showing how many infractions a driver has had. From our standpoint, if they do not meet our expectations – if they can’t slow down and they can’t handle their vehicles correctly – we eliminate their vehicle use.”
In addition to being proactive with the latest monitoring and tracking systems, being aware is also key to improving driving safety. For example, “we receive information from Burlington Northern or Union Pacific or the Operation Lifesaver program, which provides information related to railroad grade crossing safety. Unfortunately, some of the notices are about grade crossing accidents and fatalities; however, they also provide awareness training material that we can forward to our employees to assist them in making better judgement at grade crossings to help prevent collisions on and around railroad tracks. Since most of our employees drive their own personal vehicles, we can’t directly affect how they drive, but we share the information that’s given to us from the railroads and from the highway patrol to help raise their awareness,” Mr Stephens said.
Another tool for driving safety is journey management. Though journey management might vary from one company to another, the goal is consistent: to arrive safely at the destination. Journey management programs minimize unnecessary trips, distances driven and associated risks. “Because we have a lot of technical people – our tech support people, mechanics, electricians, top drive personnel, etc – journey management is huge with Nomac,” he said. “Before these guys go out to a site, they notify their supervisor, and they have to keep their supervisor informed of their travels. This allows for good communication between the supervisor and the employee, which is an important part of journey management. We want to make sure that our techs are rested before they leave a work site.”
In some of Nomac’s Southern and Eastern operations, most field employees live within driving distance to the rigs. “We may not have housing available on the rig sites, but by emphasizing journey management, the employee understands that they need to arrive at their destination safely. It’s not just a matter of that drive to and from the site, but it’s also how one’s work day is affected based on the drive,” Mr Stephens said. He noted that drivers ages 25-30 have the highest rate of fatality in South Texas. “Those (in that age group) have more jobs in South Texas now,” he added. “It’s not that they’re any more dangerous or less dangerous; there’s just a greater number of them concentrated in one area.”
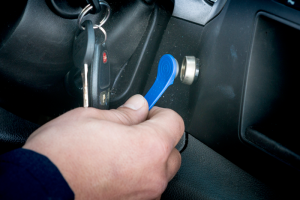
Nonetheless, one of the biggest factors in vehicle incidents is lack of experience, Edward Limas, HSE Director at Inspection Oilfield Services (IOS), said. The company provides inspection and tubular management services. “You may have somebody from Texas who gets hired to do a job in North Dakota. They’ve never driven in snow before, and now they’re driving a big vehicle in snow or sleet in unknown surroundings.” Companies must evaluate drivers’ experience and not assume that a new employee who can drive his personal truck will be able to drive a company truck loaded with equipment, he added.
IOS has approximately 200 vehicles in its fleet, with nearly 70% of them servicing drilling rigs across the US, from North Dakota to Texas and Colorado to West Virginia. Personnel in sales, corporate and safety drive the remaining vehicles.
Mr Limas cited texting while driving as a major cause of incidents. “If you look at the incidents, you find out that nine times out of 10, they were on the phone when the accident happened.” Many companies, including both Nomac and IOS, have implemented hands-free Bluetooth technology to curb texting and talking while driving.
Like Nomac, IOS utilizes GPS monitoring systems to track the locations and driving behaviors of employees. Since the systems were installed in mid-2014, the company has already seen results – only nine driving incidents recorded in 2014 compared with 14 in 2013, according to Mr Limas.
Going back to the basics, Mr Limas believes the industry as a whole needs to conduct more hands-on training for employees operating large vehicles or vehicles with extra loads, especially with the shale boom leading companies to hire more vehicle drivers than before. IOS also requires a motor vehicle record (MVR) check for any employee who could potentially drive a vehicle or forklift.
Once a potential driver passes the MVR check, IOS identifies the “kind of vehicle they could be operating. We then have a driver training course and teach what to look for during vehicle inspection before operating.” Behind-the-wheel training and assessments help qualify and determine the readiness of new employees. “For example, we find that some employees drive small cars. So when you put them in a big truck, they’re completely clueless on how to park the vehicle, which is a red flag.”
IOS has also adapted its mentoring program from work sites to its driving safety program, allowing an employee to drive and work with an assigned mentor for 90 days. During that period, the mentor will monitor the other employee’s driving behaviors and proficiencies.
Despite the myriad technologies and training that companies can use to proactively improve employees’ driving behaviors, some factors remain out of the industry’s control, such as weather and road conditions, timing and distance. “We have employees that are going in all sorts of directions,” Mr Stephens said. “Some employees may drive 45 minutes or less to start their hitch, and someone might be driving 20 hours. That’s not something we can control. We can only make sure we communicate to them to be as safe as they can and provide any information we can. We also encourage them to share the information with their friends and loved ones.”