BP upgrades digital rocks program with multiphase flow simulation technology
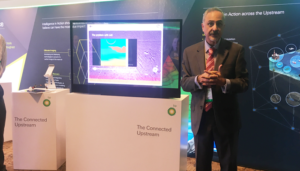
BP is adding multiphase flow simulation technology to its digital rocks program. The operator announced on 2 May a multi-year commercial agreement with Exa Corp that aims to enhance BP’s ability to predict the flow of oil and water in digital images of reservoir rock. Innovations like this have played a crucial role in the company’s ability to significantly reduce its breakevens over the past two years, Ahmed Hashmi, BP’s Head of Upstream Technology, said during a media briefing at the 2017 OTC. “Approximately 75% of the cost savings that we have brought into our portfolio are sustainable in nature. Technology is playing a big part in this,” he said.
BP originally established the digital rocks program 10 years ago. The technology takes rock core samples acquired during the drilling of exploration, development and appraisal wells and images the samples with ultra-high resolution CT scans to create a 3D digital model of the rock. The model is then put through proprietary algorithms that simulate the physics necessary to characterize the rock properties.
The ability to digitally analyze the rock properties eliminates the need to perform physical tests on the rock in the lab, Dr Joanne Fredrich, BP Upstream Technology Senior Advisor, said. “We can generate a suite of rock properties in a matter of a few days to a couple of weeks, as compared to in the laboratory where it might take us over a year to make all of these physical measurements on the rock core,” she said. Additionally, the digital rocks technology can perform its analysis using a small, thumbnail-sized piece of rock that can be acquired at a lower cost than a larger core sample. Taking a core sample from a well in the Gulf of Mexico can cost between $15 million to $20 million, according Fredrich.
To date, BP’s technology has only analyzed the rock’s static properties, not its dynamic properties. To address this gap, the operator worked with Exa to develop a relative permeability software solution for the digital rocks platform. The solution was adapted from Exa’s existing multiphase fluid flow simulation technology, which was originally developed for the automotive and aeronautics industries.
The new multi-year license agreement between BP and Exa allows BP to utilize the relative permeability software within the digital rocks platform, enabling the operator to better predict the flow of oil and water in digital images of reservoir rock. “With this technology, we can fully characterize the range of rocks in the reservoir and build better subsurface models and predict and understand the reservoir performance. It’s a game-changer for us,” Dr Fredrich said.
In addition to quickly obtaining a more complete understanding of the reservoir, BP has also been focused on reducing nonproductive time through predictive analytics. In November, BP and GE Oil & Gas launched the Plant Operations Advisor, which is being run in pilot mode on the Atlantis platform in the Gulf of Mexico. The collaboration leveraged BP’s knowledge and understanding of integrated production platforms and GE’s software and equipment expertise, said David Feineman, Digital Technology Senior Advisor.
The Plant Operations Advisor monitors the equipment on producing platforms in real time, allowing engineers to see trends in equipment performance and spot potential failures or performance issues before they occur. “A typical Gulf of Mexico platform may have 150,000 readings coming in at us every two seconds. No human being can make sense out of that data volume,” Mr Feineman said. “How do you get on top of all of those measurements and actually find a needle in the haystack, something which is indicative of a problem before it actually happens? That’s the place where this system was designed to go.”
Each sensor on the platform is programmed with limits that define the normal operating range for the piece of equipment the sensor is monitoring. The advisor system is able to track each time a component or piece of equipment goes beyond its normal operating limit and requires attention or intervention. “We can learn from it, and we save that information so that if it ever happens again, we’re able to tell people in operations that we’ve seen this in the past and this is what was done to correct it,” Mr Feineman said.
BP’s goal is to eliminate unplanned downtime and production losses, Mr Feineman said. The company will build this system into more producing assets in its upstream portfolio over the next two years, he added.
The Plant Operations Advisor and the newest advancement to the digital rocks software both resulted from BP’s collaboration with other companies. Collaboration will continue to be key to the operator’s new technology development, Mr Hashmi said. “We don’t try and develop everything ourselves. We work very closely with the supply chain, our partners and even our competitors.”