Better and better, bit by bit
New drill bits utilize unique cutting structures, cutter element shapes, advanced modeling software to increase ROP, control, durability
By Linda Hsieh, Managing Editor, and Alex Endress, Editorial Coordinator
-
Manufacturers rethink cutter placement on PDC, hybrid bits to direct more force to formation without compromising control.
-
Improved modeling capabilities provide better understanding of how a specific bit will react in a specific formation, allowing for pre-deployment customization and fit-for-purpose bits.
-
Unique cutter protection measures are being developed to help prolong bit life in multiple formation types.
Manufacturers rethink cutter placement on PDC, hybrid bits to direct more force to formation without compromising control. Improved modeling capabilities provide better understanding of how a specific bit will react in a specific formation, allowing for pre-deployment customization and fit-for-purpose bits. Unique cutter protection measures are being developed to help prolong bit life in multiple formation types. The drill bits market is an ultra-competitive one. Operators are constantly on the lookout for newer, more robust bits that can drill faster or farther through increasingly aggressive curves and longer laterals. At the same time, they demand durability and control through a wide range of formations. To help increase ROP, bit manufacturers are pushing ahead on more advanced algorithms for better modeling – knowing exactly how a bit will react in a certain formation and how to customize a bit for a specific application. Bit companies also continue to reexamine everything from cutter placement to cutter element shapes to protective cutter caps. Each company demonstrates a different approach on the path to improvement, but it’s clear that their ultimate goal is the same.

“At the end of the day, our goal is to develop innovative products that allow us to drill holes in the ground more efficiently and to save our customers money so that they will drill more holes in the ground,” Tim Beaton, Vice President of Engineering and Manufacturing for Shear Bits, said. In this article, DC gets updates on drill bit technologies from Tercel Oilfield Products, Baker Hughes, Shear Bits, Halliburton, Schlumberger and Varel International.
From core generation to ROP optimization
When Tercel launched the first generation of the MicroCORE PDC drill bit several years ago, the company was looking to provide a bit that could produce small core samples while drilling. At the time, the development of this bit was largely driven by the requirement for these “microcores” to be sufficiently sized to facilitate geological evaluation. Over time, however, the company realized that the bit’s unique cutting structure – initially optimized for core generation – could be enhanced to improve ROP instead. Late last year, after some redesign work around the bit profile, PDC cutters and hydraulics, as well as optimization of the diameter and depth of the core chamber and the “microcore” shearing process, the company launched an updated version of the bit.
It applies PDC cutters to the outer diameter of the bit face and eliminates cutters in the center of the bit – instead implementing a cylindrical chamber through the middle of the bit for core generation. An additional shearing cutter in the back of the coring chamber cuts off the core of formation collected, which is then released from the bit and circulated to the surface up the annulus for evaluation, if desired.
“On a traditional bit, a large portion of the drilling energy is consumed in the center of the bit where the cutters are not moving very far around the radius, versus the outside of the bit, where those cutters are moving very quickly,” Mark Freeman, Tercel VP of Drill Bits and Drilling Enhancement, said. “By removing those cutters in the center of the bit, we are redistributing that energy to the part of the cutting structure that is doing the most work.”
In summer 2014, this new bit was used in three horizontal wells in the Eagle Ford in South Texas, next to five similar wells using non-core cutting PDC bits. The operator was specifically looking for ROP gains in the 8 ¾-in. production interval. “They were having issues with ROP while drilling their curve and their lateral,” Mr Freeman said. He added that the operator was kicking off the build sections at around 8,500-ft at 10-14˚/100 ft, then continuing to drill 7,000-ft laterals without tripping for a BHA or bit change. TDs for all these wells were approximately 16,500 ft.

The MicroCORE achieved 92 ft/hr average ROP, while the other PDC bits in offset wells – also drilling the curve and lateral sections – achieved 72 ft/hr. “In most cases, the operator will make the run with one bit in the Eagle Ford. It’s just a question of how quickly they can do it,” Mr Freeman said. Besides the Eagle Ford, the new version of this bit has also been run extensively in the Bakken in North Dakota, the Tunu field in Indonesia and the Southern North Sea in the UK.
Adding speed to control
Last year, Baker Hughes commercially launched its second-generation hybrid bit, Kymera FSR, which combines features of a PDC and roller cone bit. While the first-generation model, launched Q4 2011, worked well in hard and interbedded formations, the company saw room for improvement in softer formations and in carbonates, Baker Hughes Product Manager Alan Holliday said.
To reach these markets and improve the overall efficiency of the bit, the company began seeking ways to make the bit more aggressive while still maintaining its low torque response. To address this, Baker Hughes developed an optimized roller cone and PDC cutting structure. This new structure allows the bit to drill with lower weight on bit (WOB) requirements while achieving higher overall ROPs compared with the first-generation model. “We found that we were able to improve the efficiency, yet maintain the smooth drilling that directional drillers came to appreciate from the first generation,” Mr Holliday said. He added that the optimized design improved performance in carbonates by 50% to 100%.

In an Eagle Ford project in Q4 2014, an operator chose the second-generation hybrid bit to drill curves in three separate wells in the Austin Chalk and Anacacho formations. The PDC bits that were being used were creating high torque fluctuations, sending the BHA off its planned trajectory and requiring at least two bits to get through the curve. In addition, the high torque fluctuation forced the operator to reduce WOB, limiting ROP.
The new bit was selected to drill three curves that averaged 789 ft each, and average total depth for the three wells was 12,600 ft. The first well was drilled in 22 hrs at an average ROP of 36 ft/hr. The second bit finished the section in 17 hrs, averaging 46 ft/hr ROP. The third run averaged 41 ft/hr.
Two offset wells each required multiple bits to drill the curve, with one requiring three bits over 35 hrs, for an average ROP of 23.7 ft/hr. The other well required two PDC bits over 27.5 hrs for an average ROP of 32.2 ft/hr.
Each Kymera bit was pulled out in “green” condition, according to Baker Hughes. The operator reduced cost-per-foot in each curve by at least 36% and saved a total of $503,122 on all three runs combined, Baker Hughes stated.
Two-step cutting structure
Halliburton’s line of GeoTech fixed cutter PDC bits, launched in February, is geared toward difficult-to-drill applications, such as hard or abrasive formations or formations that transition back and forth between hard and soft rock. It features a two-step cutter layout position that, compared with a traditional cutting structure, takes some of the cutting structure off the profile of the bit face so that some cutters are cutting more than others, according to Halliburton. “You may have a very soft section where you don’t need as much cutting structure… and then you may get into a harder or more abrasive formation later where you need that extra diamond,” Halliburton Product Manager Brad Dunbar said. “We’re trying to optimize having a very light structure in one part and a much heavier-set cutting structure in another.” Operating parameters can be adjusted to help the bit engage the second cutting structure where necessary, he added.

Advanced materials have been incorporated into the bit, including new matrix/binder materials and more abrasion- and impact-resistant diamond cutters with increased thermal mechanical integrity. However, Mr Dunbar emphasized that while these materials make the bit more robust, they will not produce results if they’re put to the field without fully understanding how they’re going to be used. That’s why advanced simulation plays a key role in the performance of these new bits.
Late last year, Halliburton introduced a new version of its IBitS 3D design software, featuring updated algorithms and models. Working in conjunction with Halliburton’s rock interaction model, these tools can help to more realistically simulate formations and how the bit will interact with the formation. “Being able to simulate better helps you to change the cutting structure of the bit or change the material in the bit to accomplish what you need in order to hit the ROP or footage that the customer is looking for,” Mr Dunbar said. If an operator wants to drill faster, for example, the software can tell you where to place the right amount of cutting structure in the right place on the bit in order to achieve that.
Early this year in the North Sea, the GeoTech bit was used to drill the 12 ¼-in. section of an offshore well through seven distinct formations. The GeoTech GTD65D bit was tripped in to drill the entire 8,254-ft interval. The bit achieved an average ROP of 93 ft/hr, compared with an average ROP of 74 ft/hr for three offset wells, saving at least 11 hours of drilling time. When pulled, the bit had a dull grade of 1-1-BT – much less damage than the offset bits, according to Halliburton.
Concentrating on efficiency
Compared with conventional cylindrical PDC cutters, the Stinger diamond element used on the StingBlade Conical Diamond Element Bit is a conical-shaped cutting element. This shape allows the cutter to apply a higher concentrated point load on the formation to fracture high compressive strength formations more efficiently with a combination of plowing and shearing mechanism. Coupled with the unique geometry of the Stinger elements is a thicker diamond layer, which provides improvements in impact strength, enabling these bits to drill further and faster.
Allen White, Product Champion at Smith Bits, a Schlumberger company, explained that after analyzing more than 1,000 runs accrued so far by the StingBlade bits, the company has seen a 55% improvement in footage drilled compared with the baselines, as well as a 30% increase in ROP. “With previous technologies, there has always been trade-off in durability and bit speed… so the ability to create longer footage runs and higher overall ROPs is quite ground-breaking,” Mr White said.
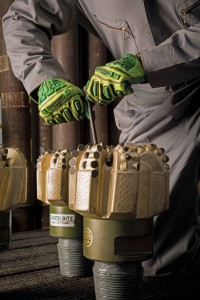
He also cited better toolface angle control from having a more concentrated point load, which applies WOB more efficiently and allows energy to transfer more effectively from the cutters into the formation. “When a hard stringer or interbedded formation is encountered while steering with a conventional PDC bit, the result is typically high fluctuations in torque and toolface angle, which can result in lower build rates and more time to achieve directional objectives. Due to the conical shape of Stinger elements on StingBlade bits, the magnitude of the torque and toolface angle fluctuations are reduced, allowing directional drillers to stay on target and finish curve sections faster,” Mr White said.
“We’ve also found the ability to reduce bit and BHA shock and vibrations for overall improved drilling efficiency and for prolonging BHA tool life,” he continued.
He explained that the conical shape of the element has a force profile when drilling that is much more symmetric about its centerline than a cylindrical PDC cutter. Therefore, the resultant lateral forces of each Stinger element are lower than a PDC cutter.
“If you take all of the cutting elements across a bit cutting structure, the more Stinger elements on the bit, the easier the bit has shown to be balanced in our IDEAS software, and we’ve seem similar results in the field.” The IDEAS design platform is used at Schlumberger to help engineers model the entire drilling system, from surface to the drill bit, including bit-rock interaction. This allows engineers to evaluate bit performance in a virtual environment and optimize placement of the diamond elements across the cutting structure.
In a field test done in Q2 2014 at Schlumberger’s testing facility in Cameron, Texas, a StingBlade bit and a conventional PDC bit were run in adjacent boreholes less than 50 ft apart, drilling 800 ft using the same rig, BHA and operating parameters. The formation consisted of interbedded limestone, sandstone and shale with compressive strengths exceeding 15,000 psi in some portions, Mr White said.
A drilling dynamics logging device placed at the bits showed that the StingBlade produced 53% fewer lateral vibrations and 37% fewer axial vibrations compared with the conventional PDC bit.
StingBlade bits have seen success in 27 countries so far, according to Schlumberger. In one project offshore Australia from Q3 2014, an operator chose the bit to drill a 12 ¼-in. vertical section in the Browse basin through the challenging Dampier, Heywood, Baudin Marl and Wollaston formations. Made up of high compressive strength interbedded hard limestones and chert, these formations in the Browse Basin are known to produce heavy damage to conventional PDC bits.
To address bit durability and ROP, two 12 ¼-in. StingBlade bits were used. The first drilled 1,516 m at 11 m/hr, equaling to 97% more footage than the best run in the same section of the offset well, according to Schlumberger. The second bit drilled the remaining section to TD at an average ROP of 16 m/hr, adding up to a total of five days of drilling time saved in the section, the company stated.
Drilling through multiple layers

Choosing a drill bit can be difficult when dealing with an interval that has a top layer of boulders and gravel and a bottom layer of softer sands and shales. The top layer can wreak havoc on traditional PDC bits, and using a roller cone bit in the bottom layer would be inefficient. “A lot of PDC bits can’t drill that kind of rock – the gravel and boulders – so a conventional PDC bit won’t survive the surface interval. It will get damaged very quickly trying to drill these very hard
rocks,” Mr Beaton said.
To address this challenge, Shear Bits launched the Pexus hybrid bit last year. The bit’s primary cutting structure is made up of rotating carbide elements, which are located on the outside of the bit face to protect the secondary cutting structure of PDC cutters. The carbide elements, similar to those found in roller cone bits, precede and protect the PDC cutters through top-level gravel and boulder sections. After the initial interval, PDC cutters on the inside will be activated to drill through the softer intervals. “Now you can drill the whole interval in one run, with one bit,” Mr Beaton said.

In March 2015, the Pexus bit was used to drill a very shallow 450-m intermediate build section of a well in the Wilrich-Bluesky oil sands in Fort McMurray, Canada. After drilling the 17 ½-in. section for 200 m with a roller cone bit, the operator tripped in the Pexus hybrid bit for the 12 ¼-in. build section, which involved drilling through gravel. The bit achieved an average ROP of 164 ft/hr (50 m/hr).
According to Shear Bits, that’s more than 30% higher than roller cone bits in offset wells and 66% higher than PDC bits in offset wells. Upon pulling the bits out after drilling, dull condition of the Pexus bit was 1:1:CT, while the conditions of the roller cone bits were 2:2:WT and 3:6:BT for PDC bits.
Shearing caps protecting PDC cutters
Severe formation swelling or caving can make it difficult for operators to reach the planned casing-setting depth during casing operations. This is a situation where casing while drilling is commonly utilized. To do this, operators use a specialized PDC casing bit with tungsten carbide backing that drills ahead while attached to the end of the casing, which is used in lieu of drill pipe during casing operations. Cement is then released through a flow valve to set the casing in
place. However, in order to reach the next interval, the casing drill bit and float equipment must then be drilled out.
To complete the drill-out with a PDC bit, operators typically have two options. They can either use a specialty roller cone bit for the drill-out and to switch to a PDC for the next interval, or they can use a single new PDC bit and BHA to drill out the cemented casing and continue toward the next interval. Neither of these choices is optimal, as the first method tacks on significantly more time in order to complete additional trips for the two bits, and the second option may harm the valuable PDC cutters.
“Now you have to drill through the face of a specialized PDC bit,” Varel International’s Bill King said.

Bottom: Varel’s shearing caps attach to the PDC cutters to protect them while drilling out the casing drill bit and float equipment. The caps wear away to reveal fresh cutters for cutting formation.
“You can suffer impact damage on PDC cutters of the drill-out bit from the PDC cutters of the casing bit. The PDC drill bit that follows a casing point and shoe track has to drill through a wiper plug, a column of cement, a float valve and out of the face of this metal casing shoe before it ever gets into the rock,” he continued. “These bits are designed to cut rock – they’re not designed to cut this other stuff, so when you have these metal components, the bit can get damaged.”
To protect the PDC cutters from damage during these drill-out applications, Varel developed the CuttPro shearing caps – or fitted tungsten carbide cutting elements – that bond to the outer profile of the PDC cutters for protection. They were commercially launched in March at the 2015 SPE/IADC Drilling Conference in London. “These shearing caps can mount on any standard PDC bit design, so we can choose the bit that’s best for the rock,” Mr King said. “Because we mount them only on the outer tip of the PDC cutters of the drill-out bit, they can do their job of protecting those PDC cutters, provide the cutting structure to do the drill-out of the casing bit, and they rapidly wear away once they get into
the rock, and the bit now is a standard PDC bit to drill ahead.”
In an August 2014 field trial, the CuttPro shearing caps were deployed in conjunction with a 12 ¼-in. Raider PDC bit for a well on Gabon’s DIGA field, next to five offset wells. In the offset wells, similar sections were drilled but with four PDC bits and one tricone bit from two different manufacturers. For the bit equipped with shearing caps, drill-out took a total of 3 hrs, versus 5.4 hrs in offsets, according to Varel. Average ROP for the bit fitted with shearing caps was 40 ft/hr (14.1 m/hr) with connections, while average ROP for the other bits was approximately 31 ft/hr (9.5 m/hr).
Looking to the future, Mr King said his company might expand the application of the shearing caps to protect PDC cutters during shoe track drill-outs. “Customers are asking to access this technology also as a simple insurance policy,” Mr King said. “Drilling with casing is not a thing that every oil well does. It’s only a small percentage of wells that actually get made with drilling with casing, but shoe track drill-out occurs in every well. It’s really exciting for us that this technology is likely to have application wherever PDC bits are used for drill out.”
-
The Tercel MicroCORE achieved 92 ft/hr average ROP in 3 Eagle Ford wells drilling curve and lateral sections. Other PDC bits in offset wells achieved 72 ft/hr.
-
An operator in the Eagle Ford reduced cost-per-foot by 36% in each of three curve sections drilled using the second-gen Kymera bit.
-
The Halliburton GeoTech achieved an average ROP of 132.4 ft/hr, compared with 107.6 ft/hr for 7 offset wells, in North Dakota’s Williston Basin.
-
In Western Canada, Shear Bits’ Pexus hybrid bit achieved 30% higher ROP than roller cone bits and 66% higher ROP than PDC bits.
-
In a 2014 field test, Smith Bits’ StingBlade bit produced 53% fewer lateral vibrations and 37% fewer axial vibrations compared with a conventional PDC bit.