Full-scale BOP electrification test rig shows benefits of electrified BOP, enables design optimization
JIP, set to launch this year, seeks to complete design and manufacturing of marinized versions of all BOP functions for an 18-15K stack
By Brian Piccolo, Amine Abou-Assaad, Vijay Chatufale, Jeff Fisher, Viral Shah and Bob Judge, HMH; Magne Rød and John Dale, ESD
Through internal engineering, testing and the acquisition of Electric Subsea Drilling, HMH has developed a fully electrified subsea BOP (SSBOP) system known as the E-BOP. In doing so, all hydraulic systems have been replaced with electric actuators to create a step change in the reliability, operational efficiency and performance of today’s BOP systems.
The E-BOP leverages HMH’s history of field-proven wellbore wetted components while integrating motor/drive technology into the latest version of the OEM’s surface and subsea control systems. HMH is designing electric subsea and surface BOP stacks to serve both floating and fixed offshore rigs, as well as land rigs. The result is that the industry is able to provide energy in a safer, more environmentally friendly and more economical manner than possible today and have greater operational certainty in the process.
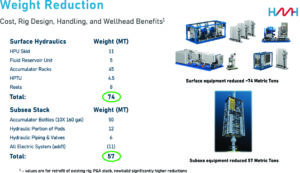
Benefits on offshore rigs
- 22+ days saved per year due to reduced API Std 53 critical path test time, driven by a robust condition-based monitoring program, substantially less wear, and a simplified control system
HMH calculates that a drillship operating on five wells a year can see an operational time savings of a minimum of 22 days per year, driven by capabilities described below.
With regards to pre-deployment testing, hydraulic soak tests, which typically take two to three days, can be replaced with electrical continuity/system functionality checks that can be completed in an almost instantaneous fashion.
Electrical continuity checks and signature tests for key parameters, such as torque, temperature, position, time, etc. result in a robust real-time condition monitoring program for the BOP throughout the well construction process.
Precise motor control enables features such as micro-testing and soft stops on ram closures. Micro-testing refers to a feature of the E-BOP that enables drillers to execute weekly function testing in parallel to drilling ahead. During micro-testing, a set of rams or an annular can be extended a short distance and retracted without protruding into the wellbore. In doing so, micro-testing confirms that the BOP is functioning properly without requiring a pause in drilling operations to execute the test. The motor and drive system are also capable of executing a ram closure with a soft stop, resulting in minimized shock loads on the BOP. Collectively, both soft stops and partial closures reduce wear on elastomers through gentler operation and reduced usage volume respectively, resulting in improved BOP reliability.
Finally, the E-BOP justifies extending pressure test intervals beyond 21 days through an increase in reliability from features that markedly reduce wear on BOP systems and decrease the number of control system components and connections, while also providing a comprehensive real-time condition-based monitoring program.
- Significantly reduced weight enables P&A on older wellheads and from lighter vessels
In addition to performance and reliability enhancements, the elimination of hydraulic components creates significant weight savings, which can result in the reduction of wellhead fatigue and the ability for smaller vessels to execute P&A operations. As a starting point, the weight of today’s SSBOP stack can be reduced by at least 57 metric tons due to the elimination of accumulator bottles and MUX pod hydraulics. On surface, the HPU skid, fluid reservoir unit, accumulator racks, high-pressure test units and hydraulic reels are eliminated, resulting in an additional 74 metric tons removed and a decrease in the footprint needed for this equipment.
- Faster shearing results in an estimated 50% EDS time reduction
A fully electric BOP closes faster than a conventional BOP, resulting in a faster emergency disconnect sequence (EDS). A key enabler of this EDS time reduction is the capability to close shear rams in under 14 seconds. This closing speed is achieved by the capability of the electric motors and gearboxes to generate torque in relatively compact space.
- Depth-independent shearing
Currently, MUX BOP systems rely on accumulator bottles for stored energy to complete a shear. A disadvantage to this solution is that the number of bottles required increases astronomically when higher shear forces are required along with deeper depths. Conversely, the E-BOP system relies on batteries and an electric motor, which are able to provide the system’s rated peak performance irrespective of depth.
- Enables drilling in environmentally sensitive areas (no hydraulic fluid vented)
From an environmental standpoint, the E-BOP does not vent hydraulic fluid to sea, which can create opportunities to drill in environmentally sensitive areas where regulatory bodies have prohibited such projects.
- Broadly accepted well control technology combined with proven components from rugged industries
The objective of the E-BOP program is to keep wellbore wetted components and key aspects of the surface and subsea control systems the same. As such, the E-BOP is designed to incorporate the same ram blocks, BOP body, connector system and elastomer sealing technology currently utilized in the industry. The surface and subsea control systems remain the same as in operation today, with the exception that these systems will be adapted to communicate with the BOP’s motor, drive, gearbox and battery systems.
The electric motor and drivetrain of the E-BOP are comprised of proven technology from other industries that can solve the combination of high force, high shock load and minimized space challenges experienced in the oil and gas industry. The electric motors and drives have been selected from the transportation industry, where power density is maximized.
The gearbox and linear actuator are comprised of technologies prevalent in the mining industry, which is known for high force applications and shock loads that surpass what is experienced during shearing.
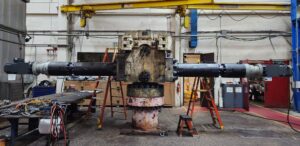
HMH BOP electrification lab
With proof-of-concept testing previously completed on the shear rams, HMH has constructed a BOP electrification lab in Houston designed for rapid design optimization. This lab has enabled the validation of soft close and micro-testing algorithms, as well as assessments on the behavior of selected components traditionally used in high force/continuous duty applications as opposed to the high force/low volume associated with a BOP.
The test rig shown in Figure 2 is currently configured for electric shear ram testing using commercial off-the-shelf components. The system is controlled via an HMI/PLC workstation and can be powered by either the on-site battery energy storage system or 120 VAC power.
The electrification lab demonstrated that proven drive and motor systems used in other applications can also be programmed to perform shears at high speeds while allowing the shear rams to be brought to a slow and controlled stop. Micro-testing has also been successfully performed.
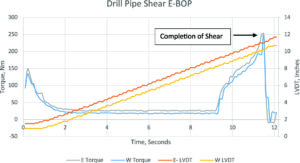
Figure 3 demonstrates a drill pipe shear that occurred in 12 seconds with an 850-kip shear ram actuator system. The overlapping blue and grey lines denote the position of each ram block over time. It should be noted that throughout the entire stroke, the slope of these lines does not change, indicating the capability of the drive system to manipulate torque as needed to ensure that the rams complete their stroke in a specified period of time. The overlapping blue and grey lines denote the torque applied to each actuator. The changes in torque throughout the stroke demonstrate how the system can manipulate current to maintain the speed of the rams. As expected, the peak torque output for the East and West actuators is at the end of the shear. Minimal, positive torque was applied while the rams crossed the open wellbore. In cases where braking was needed, a negative torque was applied.
The drive capabilities described above were also expanded to cover micro-testing. During such testing, the drive system manipulated torque to move the blades a specified stroke length and then applied a reduced or reverse torque to enable the blades to stop at a set location without extending into the wellbore. Next, the blades were fully retracted. This feature enables the E-BOP to perform weekly function testing without requiring a pause in ongoing drilling operations.
Full-scale, SSBOP shear ram testing
As a result of the lessons learned from the electrification test rig, a full-scale, shear ram actuator is scheduled for testing this year. This actuator is rated to shear at 1.9 MM lbf, which is equivalent to the force delivered by HMH’s 22-in. 5k shear ram actuator operating at 5,000 psi on an 18-15K ram BOP. This version of the actuator is sized for retrofits to existing SSBOP stacks and remains compact enough to enable the BOP bonnet doors to swing open so that maintenance on the rams can be performed just as it is today. This compact version continues to shear drill pipe in under 14 seconds, with solutions in development to reduce that time further. This technology can also be scaled down as necessary for smaller 18-10K BOP and 13 5/8-in. land or jackup BOP applications.
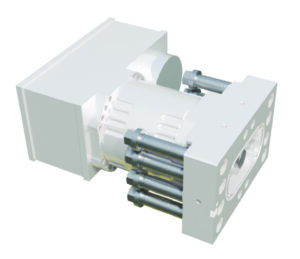
Commencing a JIP
HMH and multiple major operators intend to kick off a joint industry project (JIP) prior to the end of 2024 to complete the electrification of all E-BOP actuators, including the annular BOP, lower marine riser package and wellhead connectors, and choke & kill valve actuators. HMH has patented solutions for these that will be used as the basis of design.
The specific goal of the JIP will be to complete the design and manufacturing of full-scale, marinized versions of all BOP functions for an 18-15K BOP stack. Once completed, these systems will be available for the next phase of the JIP, in which an offshore field trial is scheduled. Such testing may take place on an offshore surface stack BOP initially before progressing toward a subsea field trial.
The support gained from a committee of industry partners – operators, rig contractors and OEMs – enables the oil and gas industry to benefit from a fully electrified SSBOP in substantially less time compared with having one party execute this development effort.
Transitioning from MUX BOPs to fully electric BOPs
Once the first fully electrified BOP system goes into operation, it is difficult to believe that the industry will regress back toward the limitations of the current MUX BOP technology. The combination of improved operational efficiency, reliability and operational performance, coupled with the creation of new opportunities to drill in certain locations and execute P&A operations from lighter vessels create a compelling case for operators and rig contractors to quickly adopt an E-BOP. DC
This article is based on a presentation at the 2024 IADC Advanced Rig Technology Conference, 27-28 August, in Austin, Texas.