Technical innovations bridge gaps as pace of shale drilling intensifies
Manufacturers working to address challenges around supply chain, equipment service life, casing running and corrosion inhibition
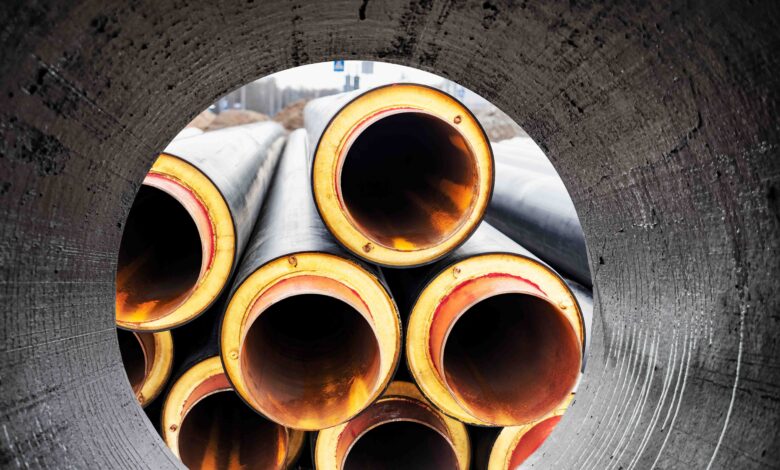
By Stephen Whitfield, Associate Editor
In the North American shale plays, competition is high, and companies are always on the search for new tools and technologies that can help them push new technical limits. As lateral lengths continue to increase, the components needed to drill shale wells are being placed under greater stresses and higher pressures.
Other gaps are also being created as the intensity of shale drilling grows, for example, around the ability to get casing to bottom, equipment corrosion and even with the OCTG supply chain – all are factors that can impact the delivery of a well safely, on time and within budget.
“Efficiency is the name of the game,” said Afif Najjar, VP of Rig Direct Services at Tenaris. “This is one of biggest areas where we can add value to our customers at this moment, building on our strong foundation of safety and product quality. The operators in the US shales are just going faster and faster.”
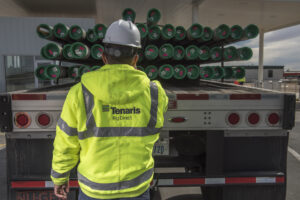
Optimizing supply chain management
As the oil and gas industry continues to deal with supply chain constraints, Tenaris is focused on bolstering its Rig Direct model to better mitigate challenges in the value chain and support operational needs. Rig Direct includes services for material selection and well design. Tenaris then uses the inputs provided as part of these services, as well as customer rig forecasts, to produce the product and quantities needed.
Under Rig Direct, Tenaris manages pipe inventory, delivering product when and as needed, as well as rig equipment returns. The company manages deliveries through a combination of its own fleet of trucks and third-party companies that work with its regional service centers. Operators can also access the Rig Direct Portal, an online platform to request or modify material orders. These capabilities all help to increase efficiencies in the supply chain, Mr Najjar said.
“Operators were asking us for more streamlined processing and more ‘just-in-time’ delivery where they didn’t have to hold huge inventory commitments,” he said. “With Rig Direct, we went into this model where we work with the operators to provide goods and services directly, which, historically, was not how the OCTG industry operated. It was really one of the only industries in the oil and gas sector that was largely controlled through distribution channels. Rig Direct allows us to go from the raw material production, delivery to the service center, management of inventory in the service center, then delivery to the wellsite.”
Tenaris has regularly updated Rig Direct with new solutions since its initial launch in 2016. One of the biggest updates came in 2020, when the company introduced the Rig Direct Portal, a centralized communication system. As opposed to managing pipe deliveries for a given well, the portal allows operators to view all the wells planned for a given rig and manage material requests for those future wells.
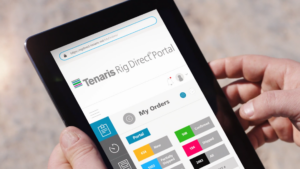
The portal also streamlined administrative processes in a single digital platform. This makes it easier for operators to place orders, track shipments, issue an electronic proof of delivery, access invoices and other order-related backup documents.
“The Rig Direct Portal is the piece that connects our forecasting to the call-out and the delivery,” Mr Najjar said. “You can see the products that were forecasted for a given rig for, say, the next 12 months, and it allows them to communicate all of their needs to us. If you suddenly need casing and you call it in, we can give them updates on the delivery time, show them when the truck was scheduled and give them updates. Everyone involved can see it in one platform.”
Other new developments are helping to push the Rig Direct system beyond supply chain management and into full well lifecycle management. The iRun Casing cloud platform, launched this year, monitors casing installation operations, providing notes on the progress of critical variables during a given operation and guidelines to enhance safety and efficiency. The tool detects challenges during casing installation based on wellbore conditions.
“One of the things we’ve been looking at with Rig Direct is how do we reduce risks for the operators,” Mr Najjar said. “We’re producing and delivering to the wellsite, and we have field service representatives supporting the rig during casing operations. When you look at the value chain, Tenaris has ownership over the whole process. With iRun, we’re further connecting ourselves to the whole value chain and allowing ourselves to address specific well construction and integrity pain points for the operators.”
Rig Direct services are currently being used in several onshore basins in North America, as well as in 20 other countries.
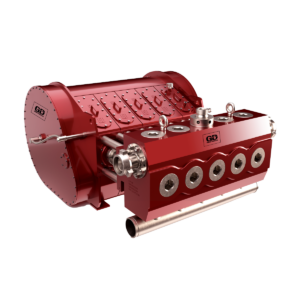
elements from the company’s 5,000-hp pump. The resulting changes to the pump’s frames are leading to significant improvements in its service life compared with the company’s legacy 2,500-hp pump.
Stronger frames on smaller pumps
GD Energy Products (GDEP) launched its first 5,000-hp pump, the Thunder 5000 Quintuplex frac pump, in 2019. It can cut the size of a frac spread by 50% compared with a 2,500-hp pump, according to the company. Moreover, with fewer pumps, transmissions and engines to maintain, the system can reduce the potential points of failure at the frac site.
However, not all companies are ready to invest in upgrading an entire frac fleet, which is why there is still demand for lower-capacity equipment like GDEP’s GD 2500Q Heavy Duty Frame (HDF) quintuplex pump, which can run off of diesel, dual fuel and electric driven motors. “The majority of frac fleets are built around 2,500-hp pumps, so redesigns of existing trailers are not necessary. You can utilize the same units that you already have, saving significant capital investment,” said Turner Hall, Engineering Supervisor at GDEP.
Still, longer laterals and more intense frac operations mean that innovation was needed to extend the life of these 2,500-hp pumps. So, in 2021 GDEP incorporated design elements of the Thunder 5000 into the HDF pump. “Our old 2,500-hp pumps were designed back in the day when the duty cycle was much lower. An operator might only run the pumps 8-12 hours per day,” Mr Hall said. “Now, most companies are looking to have 20 hours of uptime or more on their frac jobs each day, so these pumps are being run a lot harder and for longer durations of time.”
Among the design upgrades incorporated were a thicker top and bottom skin plate, as well as a thicker main bearing plate. The main bearing plate was also redesigned to protrude between the skin plates, which Mr Hall said reduces stress on the frame and the welds. The nose plate weld size was also increased to reduce stress in the nose plate joint, and the thickness in the support structure around the nose plate was increased.
“Adding thicker material in certain places allows for bigger welds, which makes it easier to handle the fatigue damage that’s prominent in those areas. The steel we used didn’t change. The change was more in the geometry. The thicker welds help to better distribute the load found on a pump throughout the frame,” Mr Hall said.
The challenge in designing an HDF frame for the 2,500-hp pump was to ensure that the added thickness of the various redesigned plates did not add to the physical size of the pump itself. While the 5,000-hp pump was designed from scratch and requires the installation of a larger frac trailer, GDEP wanted to offer its customers cost savings benefits by retrofitting the 2,500 HDF onto existing trailers and eliminating the need to purchase new trailers.
“That was one of our key design inputs when we set off to redesign the frame – we wanted it to be a drop-in replacement on the current 2,500-hp pump,” Mr Hall said. “If you looked at the two pumps – the old 2,500-hp and the HDF frame – from a distance, you wouldn’t be able to recognize the difference between the two.”
So far, the new design elements appear to be making a difference. GDEP says that, based on data it received from its customers, the 2,500-hp HDF pumps have seen an average 5,000 hours of service life, and one frame lasted more than 7,000 hours. By comparison, the legacy frames on GDEP’s previous 2,500-hp models commonly showed frame-related issues in less than 3,000 hours.
“We’ve worked incredibly hard over the last few years on the 2,500-hp pumps with the frame redesign,” Mr Hall said. “We’ve got a lot of them out in the field right now, and we have not had any frames come back from service. That’s a really big win for us in the industry. Even though we’ve got the 5,000-hp pumps, we definitely have not forgotten about our 2,500Q HDF product line. It’s something that we know the industry’s needs.”
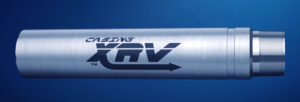
Improving casing operations in extended-reach wells
As operators drill wells with increasing lateral lengths, running casing to total depth has become more challenging. The completion string can also be exposed to a high stress rate, which could increase fatigue on the string and cause issues during the life of the well. These challenges have led Thru Tubing Solutions to renew focus on an old product originally launched in 2014 that, until recently, had a limited footprint. Its Casing XRV tool is designed to reduce the friction between the wellbore and the casing, helping to get the completion to total depth without excessive force.
The tool is positioned in the casing string near the shoe, inducing axial vibration to reduce friction forces and improve casing running ability. As fluid flows through the casing, the tool pulsates fluid at its exit point. This creates a continuous flow, mitigating the risk of water hammer, or the shock waves caused by a reduction or sudden stoppage in fluid flow. One of the other benefits of the induced vibration is that it reduces the air voids often found in cementing, improving the integrity of the cement jobs.
“This tool is all about saving time,” said Daniel Steelman, Middle East/North Africa Manager at Thru Tubing Solutions. “When you’re pumping cement, you’re creating fluidic oscillations of the cement when it leaves the shoe, but this tool stops you from having to over-rotate your pipe or slam pipe into the hole. When you’re doing that, you’re putting added stress on your connections, potentially creating degradation of your pipe or deformations in your pipe, which restrict the ID through the wellbore and potentially creates issues where you can’t pass plugs.”
The tool is an offshoot of the company’s Drilling XRV, an extended-reach downhole vibratory tool that minimizes friction between the drill pipe and the wellbore. Mr Steelman explained that the Casing XRV was initially developed for specific operators dealing with casing and cementing issues in Oklahoma. Other operators in various regions such as South Texas and the Midland Basin also found it useful, but the company did not see significant demand beyond that because operators weren’t frequently having issues running casing to bottom in their wells.
About two years ago, interest in the tool began to grow, both from operators and directional companies, as the complexity and length of shale wells started to escalate, and there was suddenly a need for a tool that could drive efficiency in this part of the well construction.
Moreover, the traditional approach of getting casing to bottom “no matter what” – whether it was through the use of oscillators or reciprocating pumps that could drive the casing downhole – just didn’t work, Mr Steelman said. Those tools placed stress on the drill pipe connections, creating degradation of the pipe that could restrict the wellbore inner diameter and increasing the likelihood of cumulative drag and friction forces, which impede the process of pushing casing to bottom. The Casing XRV became a valuable resource in helping to address these issues. Aside from Oklahoma, the tool is now also used in the Niobrara and the Marcellus. Outside the US, the tool has been deployed in the Montney in Canada, as well as in Saudi Arabia.
“We looked at how companies were solving their completion jobs, and we saw that people were really driving for efficiency,” Mr Steelman said. “We partnered up with them, looked at how they were running their tools, how they were running their cement, and applied this tool to their string. They started seeing jobs that were coming out far better than they expected.”
Thru Tubing cited one project in the Niobrara where an operator was seeking to drill and complete a 12,333-ft well. In a nearby offset well, it had taken approximately 17 hours just to run the final 3,000 ft of casing to bottom. Using the Casing XRV in the new well, the operator was able to run the entire 12,333 ft of casing to bottom in 12 hours.
Inhibiting corrosion under high temperatures
Corrosion under insulation (CUI) can lead to major problems for onshore oil and gas facilities, including the equipment on an onshore rig. Water penetration can result from many causes, including rain, wash downs and sprinkler systems, as well as exposure to steam or frequent condensation and evaporation of atmospheric moisture. Complete removal of insulation to thoroughly inspect the materials can be time consuming and expensive. Much of maintenance costs are spent on external piping inspection, insulation removal and replacement, painting and pipe repairs. If undetected and untreated, CUI can lead to equipment failure.
To mitigate the potential for CUI, Cortec released its CorroLogic high-temperature vapor-phase corrosion inhibitor last year. When injected directly into insulating material, the corrosion-inhibiting vapor migrates from the injection point along the pipe to form a water-resistant protective layer on the metal surface of the pipe. It is a “100% vapor phase” inhibitor, meaning that it is undiluted – the inhibitor is a 100% active material that gives off corrosion-inhibiting vapors.
“In this industry, you usually see a lot of coatings that companies put on the pipes underneath the insulation,” said Julie Holmquist, Marketing Content Writer at Cortec. “The difficulty with that is, usually, this can only be done to new piping before laying the insulation on, or you have to remove the insulation, put the coating on and put on new insulation. With the vapor-phase product, you can inject it into the insulation. You don’t have to remove anything.”
Temperature is another challenge that the new inhibitor addresses. Cortec said one client has sometimes seen temperatures surpass 338°F, the limit of its highest-rated vapor-phase inhibitor for CUI. This meant the inhibitor was subject to a loss in chemical stability and, therefore, its effectiveness. “We needed something that was stable at those higher temperatures, where it can still protect the piping even if it cycles back and forth between the extremely high temperatures and lower temperatures,” Ms Holmquist said.
Cortec initially screened several vapor-phase inhibitor chemistries and their viability for CUI inhibition under high temperatures, ultimately settling on a chemistry that was stable at up to 600°F, with a flash point of above 300°F. Testing of the formula took place at Cortec’s in-house laboratory in spring 2022, with the company exposing metal plates to the protective vapors for different lengths of time. After each period, the company would measure results from one plate treated with the inhibitor and another that was untreated. It would drop a chloride solution on each plate, noting its hydrophobicity and corrosion protection.
The metal plates were also exposed to the corrosion-inhibiting vapors at various distances – effective corrosion protection at a long application distance would mean fewer points of injection are needed along a pipe. The inhibitor showed effective vapor diffusion and corrosion protection even when placed multiple feet away from the metal test panel. Based on test results, Cortec ultimately recommended spacing injection points 10-20 ft apart to allow proper diffusion and application of the inhibitor. DC