Uptake of automation, remote operations enhances need for systematic alarm management
Panel: False alarms can sow human distrust in automation, while lack of interoperability is still leading to pain points for end users
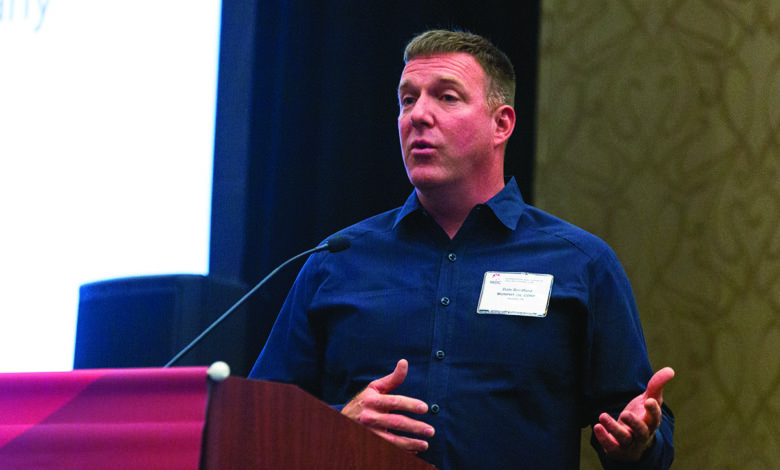
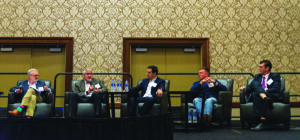
By Jessica Whiteside, Contributor
Disciplined alarm rationalization helped Murphy Oil cut alarm notifications from its Eagle Ford Shale production sites from 10,000-plus a week to just approximately 100. The key to this dramatic result? “Brute force methodology,” said Dale Bradford, Murphy’s Vice President, Global HSE.
Speaking on a panel about automation and safety systems at the 2022 IADC Advanced Rig Technology Conference in Austin on 31 August, Mr Bradford said the company used the International Society of Automation Alarm Management Standard 18.2 to guide the process of rationalizing each alarm in a given facility.
Alarms that indicated an abnormal situation requiring an immediate response from the operator, that had a defined action for the operator to take within a given time, and that would lead to a defined consequence if the operator ignored the alarm, were maintained. Alarms that did not meet this criteria were eliminated. This rationalization process was not complicated but was “very brutal,” Mr Bradford said.
“You’re sitting in rooms with a group of folks that manage this every day and banging away at every alarm and rationalizing and changing and recoding systems to eliminate the issue,” he added.
So far, the company has conducted more than 17 facility reviews in the Eagle Ford Shale. Only a small fraction of the thousands of alerts and alarms assessed during the rationalization process were real exceedances that required action. Many turned out to be information that was useful or needed for various purposes but that was not truly an actionable, problematic issue to deal with, Mr Bradford said. “We’ve just gotten started, and we’ve already seen some pretty incredible results.”
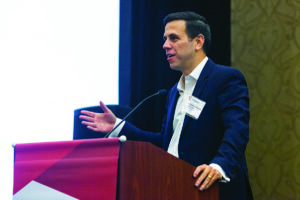
Managing alarms for remote operations
Murphy has been pursuing sensors and automation primarily to monitor processes and provide data for predictive maintenance at its upstream production facilities (e.g., monitoring conditions such as pressure, vibration, temperature, fluid rates, fire and gas) to ensure that they are operating within the guardrails for safety, Mr Bradford said.
Managing alarms was not a significant problem when field-located management was the norm, with crews dedicated to each field and facility. However, as Murphy Oil began concentrating its onshore production in the Eagle Ford and Canadian shale fields with sites scattered many miles apart, the company moved to an “operated by exception” model that uses a remote operations center and dynamic, data-driven crew routing to manage a large number of sites across vast distances.
“We simply must rely more on instrumentation and automation to keep track of everything,” Mr Bradford said. Under the remote operations concept, information, alarms and data from multiple facilities, pads and wells are routed to one center – concentrating the alarms and information on a small group of people who were dealing with “a ridiculous number of alarms,” Mr Bradford said. The volume of alarms made it challenging for people to focus on their work, and the situation was not sustainable.
“In the past, frankly, we could get away with less-than-wonderful alarm management because we had people there to look at it and to understand it,” he said. “That’s not the case anymore.”
There’s a school of thought that when an alarm occurs, it’s already too late for safety: Something has already gone wrong, and it’s a very reactive mode to be in, Mr Bradford said. While talking about alarm management can, therefore, feel “old school,” getting a handle on alarm management is a precursor to “a world where we can be more proactive and actually be ahead of the situation,” he said. “We must sort out this reactive alarm management situation so that we can have reasonable data and have people be able to pay attention to the right things – and then we may be able to develop the trust in the system.”
“Nobody trusts 10,000 alarms a week. If we can move beyond that and develop that trust, then we can start considering actual automation.”
Building trust in automation
Distrust of automation is one of the key challenges the drilling sector must overcome if it is to use automation to deliver higher standards of process safety, said Rafael Guedes de Carvalho, Project Manager, Schlumberger, another panelist from the same session at the conference.
Mr Carvalho noted that a 2021 International Association of Oil and Gas Producers report found that three-quarters of incidents leading to a well control event were related to human factors, and at least half of those were people not following procedures. Automation could help the humans in the equation make better decisions and, where possible, enable systems to make those decisions instead of humans, he said.
In this case, validation of data quality is critical. If the data that automated systems are collecting is not good, “we sometimes have the risk of overwhelming the operators with alarms that are not actually accurate,” he commented. “Every time we have a false alarm, we have the consequence of lack of trust in the system.”
To help build trust, there also needs to be a balance between generating sophisticated analytics and presenting those through an interface in an easy way for the user to understand. Finding better ways to communicate what the machine is actually doing could help get buy-in from the driller, Mr Carvalho said. “Trust only comes from understanding.”
Addressing multi-vendor challenges
Contributing to potential distrust of automation is that, even on a single rig, there may be a variety of different systems that were not designed to communicate with each other, Mr Carvalho said. Fellow panelist Don Bartusiak, President of Collaborative Systems Integration and Co-Chair of the Open Process Automation Forum, asserted that the closed, proprietary nature of control and information-using systems is a root cause of many of the asset owner’s pain points in multiple industry sectors.
“I know from first-hand conversations with drillers you guys have a particularly acute problem in terms of the number of different companies that are performing work or providing services on those rigs. So if every company that wants to use a control system or any information-using system brings a closed proprietary solution, you’re going to have a problem,” he said.
One initiative that could aid integration of automated systems in a multi-vendor environment is the Open Process Automation Standard, facilitated by The Open Group, which is working to transition the process control industry away from proprietary solutions toward a standards-based, open, secure, interoperable process control architecture.
“Just because we use the phrase ‘open’ does not mean we’re asking anyone to give valuable intellectual property away,” Mr Bartusiak said. “The whole point of it is about standardizing the interfaces between the components that make up the system.”
“This should influence what this community is thinking about in terms of what the future of automation looks like in your world.”
Mr Bartusiak pointed to the Institute of Electrical and Electronics Engineers networking standards as one example of industries achieving a common goal for interoperability.
“Take Wi-Fi for example. How much economic value has been created by that industry standard that has allowed solutions providers to bring products to the marketplace and how big that pie has grown,” he said, calling it a “compelling case for openness.” DC