Precision Drilling CTO: Digital mindset can help drilling contractors reach ‘Drilling 4.0’
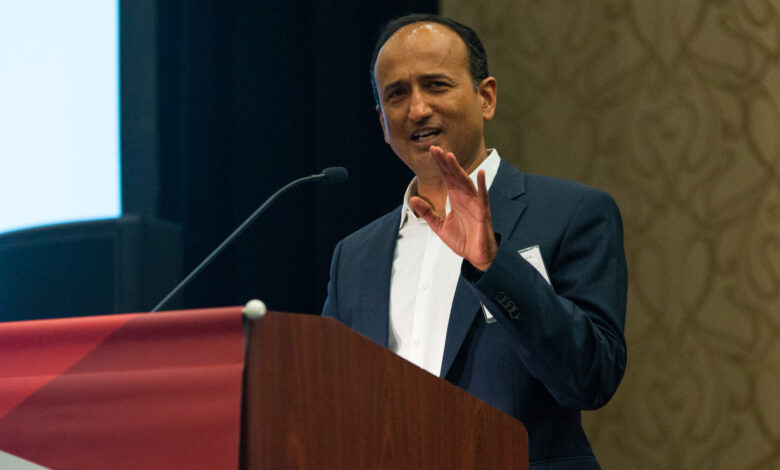
By Stephen Whitfield, Associate Editor
While the drilling industry has seen significant increases in footage drilled per rig over the years, it may have to look to other industries for inspiration that will bring about the next step change in performance. The manufacturing sector, for example, has done a great job of implementing “Industry 4.0,” or the digital convergence between industry, businesses and processes through cyber-physical systems such as AI. This has helped manufacturers realize new efficiencies and performance improvements in their operations, according to Shuja Goraya, CTO of Precision Drilling, and he believes the implementation of a “Drilling 4.0” can help drilling contractors see similar improvements.
However, Mr Goraya, who gave the keynote address at the 2022 IADC Advanced Rig Technology (ART) Conference in Austin, Texas, on 30 August, said the drilling industry is not yet in its own Industry 4.0 phase. In order to get there, the industry must be willing to adapt a more flexible digital mindset, prioritizing the incorporation of data and technology in their operations and encouraging collaboration between stakeholders in analyzing data and making decisions based off of those analyses. This means allowing machines to become an integral part of the decision-making process.
“With Industry 4.0, we can get all of that data to the right people in the right format at the right time, so that we can start making optimized decisions,” Mr Goraya said. “It’s all about optimizing decisions. These machines can do complex computations with AI, so why not have them participate in the decision-making process, as well?”
This doesn’t mean that drilling contractors are not already utilizing advanced systems on their rigs. In fact, Precision Drilling is running more than 60 automation systems across its rig fleet, transmitting around 5,000 channels of high-definition data per rig, and the fleet has registered around 45,000 automation days over the past four years.
However, embracing a digital mindset remains a major challenge for the industry, in part because of the fragmented nature of drilling operations. Mr Goraya estimated that a wellsite can have as many as 30 different service providers working over the course of a drilling campaign, and oftentimes each company is “incentivized with their own objectives.” Breaking out of these silos will require each of these companies to be aligned on performance objectives.
Collaboration between stakeholders and integration of services will also be critical to realizing step changes in performance. Mr Goraya said that full automation of the well construction process, as well as the use of open digital well plans stored on a rig operating system that service providers can access at any time, can help generate greater performance efficiencies.
Efficient rig performance will also be a key component in helping drillers lower emissions from their operations. Automation systems can also help drilling contractors here, since they allow them to realize the most effective use of power on their rigs. Mr Goraya noted it will also be important for drilling contractors to make the most of the drilling efficiency data gathered from their automation systems, in order to better understand where they can make the most impact on reducing power consumption.
“When it comes to sustainability, everything matters. Every single watt of power that we can save counts. Every single time we can push the maintenance cycle back by an hour. Every time we don’t suck the life out of our drill string counts. That’s what we need to figure out,” Mr Goraya said.