Schlumberger introduces Neuro autonomous solutions
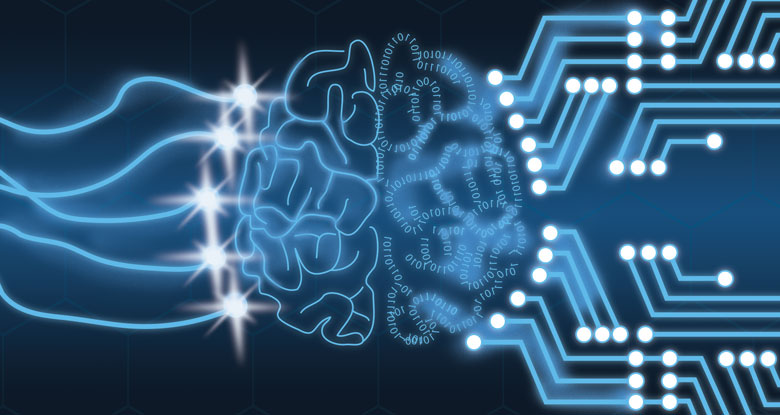
Schlumberger has introduced its Neuro autonomous solutions, which use advanced cloud-based software and connected intelligent systems to create a continuous feedback loop between surface and downhole. This significantly increases the efficiency and consistency of E&P operations while reducing human intervention and footprint.
“Neuro autonomous solutions transform hydrocarbon exploration and development workflows for the well construction process today and lay the groundwork for our customers to achieve fully autonomous operations tomorrow,” said Abdellah Merad, EVP, Core Services & Equipment, Schlumberger. “Over the next several years, we will scale autonomous solutions across the energy value chain to revolutionize our industry’s operating model and achieve higher-value outcomes for our customers.”
The first Neuro solution delivers steering autonomy for directional drilling. It uses artificial intelligence with surface and downhole automation workflows to self-determine steering sequences and deliver the well trajectory on plan. As the well is drilled, a real-time continuous feedback loop between an intelligent downhole system and a surface advisory system automates downlinks, reducing control loop time. The instantaneous correlation between downhole and surface actions in accordance with the well plan significantly reduces risk, refines precision and increases efficienc y— reducing associated drilling emissions.
Neuro autonomous solutions for directional drilling have been deployed across North America, South America, Middle East and East Asia. The solution has been deployed on more than 50 rigs across 10 countries and executed on 131 customer wells, drilling 612,000 ft.
In the Middle East, an operator recently used the solution to autonomously drill a well from 22° to 90° inclination with a curve section measuring 2,500 ft and a 5,400-ft lateral section. Both sections were performed using an autonomous-capable rotary steerable system that contributed to the balance between surface and downhole autonomy enabling the operator to reduce downlinks by 33%, compared with offset wells drilled in manual mode, while achieving a 13% increase in rate of penetration (ROP).