Nabors: Workflows must transform to maximize value of automation
Drillers should be given tools to automate repetitive tasks as rig environment becomes increasingly complicated
By Drew Curran and Blakley Farrow, Nabors
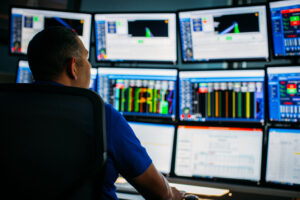
For decades, advances in the drilling industry have focused primarily on equipment that made manual labor more efficient and safer. But these days, all eyes are focused on automation. There is broad consensus that automation is the linchpin of the oil and gas evolution and that, when you seamlessly connect workflows, you take automation to a new level.
Industrywide, companies have significantly improved the way they gather data that originate from workflows, but the reality is most companies have more data than they know what to do with. Consider the rig instrumentation and controls system that impact multiple components of well delivery, including drilling performance and directional automation. The sheer amount of information that comes in every millisecond can be overwhelming and needs thoughtful analysis and context.
Such drilling data has proven to be invaluable when it comes to operational visualizations and automated sequences, as well as leveraging tools to consolidate driller and operator workflows. Here’s how drillers can harmonize their workflows and leverage them to achieve efficiency and cost savings.
The process begins with a robust lessons-learned process in the field by investigating root causes, understanding various scenarios and creating solutions/functionality to aid the driller’s job execution. The changes are included into new code releases to immediately improve a workflow or the driller’s experience. Part of the challenge is creating user-friendly, configurable products that make the drilling details digestible. Driving functionality improvements from the field operations up will ultimately improve drilling performance to deliver faster and safer wells.
Directional Independence
In the heart of the Permian Basin, Nabors introduced a new approach to directional services in collaboration with an operator. In the past, at least two directional drillers per rig were tasked with interpreting downhole data and drilling conditions in real time to make all the directional decisions required to drill horizontal wells. By employing automation and digital tools, the two directional drillers were able to effectively guide the placement of wells on three or more rigs from a remote operations center (ROC).
This scenario stems from pairing an automated directional guidance software with a steering control algorithm that will execute the given slide instructions. By automating the decision making and execution of this process, the uncertainty arising from multiple human factors – such as variances in experience levels, turnover of personnel and career progression – is mitigated.
When the driller has effective tools to automate the execution of the rotary and slide drilling process, as well as monitored support from the ROC, operator best practices can be consistently executed and learnings can be effectively disseminated throughout the drilling fleet.
By integrating the full complement of the company’s Smart Suite products and the ROC, the system facilitates digital and automated workflows for well planning, logistics, drilling and monitoring to deliver wells with 100% remote directional crews.
This gives rise to a unique concept dubbed “directional independence.” Adoption of this strategy enables wellbore construction and placement of the well agnostic of the provider of the downhole wellbore placement tools, giving operators the freedom to run their preferred tools while having their top-performing directional drillers steer them.
In the case of this specific operator, the fully remote model allowed the client to complete wells ahead of schedule and below its authorization for expenditure. In some cases, both were reduced by more than 20%.
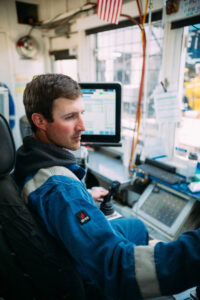
Transformation of the driller
The evolution of drilling workflows is also evident in the role of the driller. Traditionally, a driller was considered an equipment operator whose primary responsibilities were of the mechanical nature – oil, lubrication and engine maintenance. Often, drillers relied on intuition and experience to make decisions because the only information available came from the surface.
Today, the driller’s role has drastically evolved. The deployment of advanced automated and digital tools on the rig have fostered the requirement for new competencies. Drillers are expected to serve as operators of the rig controls and automation, interpret massive amounts of data to monitor downhole conditions, manage crew members working on the rig floor, and work with remote operations to support maintenance, all while ensuring safe operations that exceed customer expectations.
This is no easy feat. In fact, it would be unmanageable without providing the right tools to ease their workflows. By automating repetitive tasks, such as transitioning on/off bottom, effectively engaging the bit and ramping to full drilling rate and transitioning to/from slide drilling, the driller can better manage safe operations and drill more efficiently. Additionally, access to the ROC gives the driller another layer of confidence in operating the tools by providing a highly trained team of specialized experts monitoring the rig around the clock.
Remaining challenges
Moving forward, the industry must design user-friendly, automated solutions that do even more to incorporate immediate and future needs around drilling operations. Product development must be driven from three core perspectives, then prioritized appropriately – expanding core functionality, improving and integrating user workflows, and building supporting systems to monitor and analyze the system.
When deploying new technology, there is always some level of reluctance to change, but when a product is intuitive, configurable, and the value is clear at all levels of the organization, that hesitancy to adopt and adapt can be mitigated and overcome.
Automation and digitalization mitigate the challenge of executing disparate workflows, even within the same operation. By digitalizing the operator well plan and driller workflows, step-by-step guidance is now available to the rig. All instructions needed to drill the well to-plan, with advanced automation, are delivered directly to the driller’s human-machine interface for simple and informed execution spud to spud.
When it comes to transforming workflows, the benefits are many. For directional automation, they include:
- Scaling and standardizing best practices into workflows;
- Eliminating knowledge silos;
- Removing people from hazardous locations; and
- Mitigating turnover.
- Benefits for drilling performance include:
- Mitigating damage to downhole tools through consistent execution of best practices;
- Scaling performance and best practices;
- Ensuring procedural adherence;
- Maintaining performance regardless of driller experience; and
- Continuous improvement enabled through strategic analysis.
Additionally, by employing remote operating models and automating repetitive drilling tasks, the driller is freed to focus on other tasks. In essence, that person is empowered to function as a safety champion and/or project manager on the rig.
As workflows evolve over time, there is an increased safety component by virtue of removing people from the location, along with improving risk mitigation and management. This gives the driller better tools to complete their job safely and efficiently. This integrated approach delivers multiple efficiencies and continues to transform workflows.
The future
The twin challenges of the pandemic and the Russia-Saudi Arabia friction certainly affected global demand. However, the pandemic also revealed the need for technological advances, whether it be automating processes or scaling timely data across an entire fleet.
Downturns have always spurred innovation, and the companies that leverage their expertise will be the ones leading the way. However, the industry must innovate thoughtfully. With so many moving pieces, if there is not alignment or automation, separate areas may deliver efficiency but not maximize the potential that could be reached.
Performance that was unheard of just a decade ago will soon give way to a new reality. It’s incumbent on the industry to optimize workflows to continue adjusting for the industry’s – and society’s – demands. DC