High-density survey data allows for capture of live inclination, azimuth, delivers clearer downhole picture
By enabling rapid assessment of wellbore trajectory, directional drillers can construct smoother well path, optimize sliding time
By Chris Hartley, Gyrodata
The evolution of drilling technology continues to play an important role in improving drilling efficiencies and well placement. Directional drilling providers use specialized sensors that can operate in harsh downhole environments, where temperatures reach 300°F or higher.
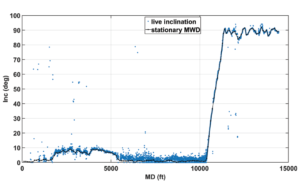
These sensors are used to compute the orientation relative to vertical and north directions. The orientation is then used to calculate the wellbore position from the surface location to a known point along a well path, which is defined by a series of survey stations.
Operators need accurate and precise measurements from drilling surveys so they can drill into the target reservoir without colliding with neighboring wells.
Accurate surveys lead to the accurate placement of wells, which is essential for maximizing production.
Over the years, measurement-while-drilling (MWD) has become the standard surveying tool. MWD tools use accelerometers and magnetometers – measuring the Earth’s gravity field and magnetic field – to estimate:
- The survey inclination: deviation from the vertical plane;
- Azimuth: deviation from magnetic north; and
- Toolface: usually refers to the orientation of a drilling motor.
Gyro while drilling (GWD) tools use accelerometers and gyroscopes – measuring the Earth’s gravity field and rotational rate – to estimate:
- The survey inclination, similar to an MWD tool;
- True azimuth: deviation from true north; and
- Toolface angle.
It can be difficult to fully understand the nuances of the different drilling tools and determine which one best fits the drilling objectives.
Operators provide drilling targets and objectives to the oilfield service providers. The service providers create well and drilling plans, which are reviewed, and the tools required to drill the well are selected. MWD and GWD are examples of tools that they determine.
Drilling Surveys
Surveys are typically taken at every connection during the drilling process in stationary conditions and transmitted in real time to the surface using different types of telemetry. Once the inclination and azimuth are computed, the borehole position is calculated and compared with the well plan. The directional driller then determines the actions – to rotate or to steer as required – and drilling continues.
During drilling operations, high-density surveys can be acquired with MWD tools, given that the electronics sample the survey sensors very quickly. This information can be transmitted to the surface and aid in steering the well, or it can be stored in memory for post-drilling analysis.
After drilling is complete, high-density survey data can also be obtained while tripping out of the hole, allowing wellbore tortuosity analysis and the ability to update torque and drag models. This can aid in drillstring design and running casing.
While magnetic MWD tools are considered the standard surveying tool, they can be subject to azimuth errors caused by magnetic material in the Earth, magnetic solar storms, magnetic drillstring interference or nearby steel casing.
Another obstacle to overcome is that the magnetic pole is continuously moving and, therefore, magnetic north needs to be referenced to true north, which is stable. The reference term is called declination and is calculated based on surface location and time the well is planned to be drilled. These issues can produce several degrees of azimuth error and change the true location of the wellbore by hundreds of feet.
GWD tools use gyros to measure the Earth’s rotational rate, producing an azimuth based on true north (geometric north). True north is stable, as the geometric north does not change over time. Drillers traditionally use GWD surveying instruments when the azimuth of a magnetic MWD survey system may be corrupt by magnetic interference or hard lines on the well plan cannot be crossed and higher accuracy is required.
High-Density Data
Continuous MWD surveys while drilling are able to produce high-density survey data, which can give operators tremendous value over the life of a well. Continuous surveys provide inclination and azimuth values while drilling ahead in either sliding or rotating mode.
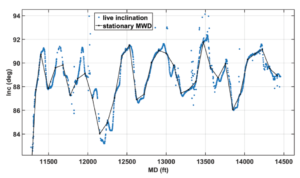
Continuous MWD surveys enable the directional driller to drill a well closer to the well plan than if they drilled only based on stationary surveys. Stationary surveys are used to determine the well path computed based on each surveying station.
Values of inclination and azimuth are taken after each connection (30 ft or 90 ft) or at intervals that do not exceed the minimum regulatory requirements. Continuous surveys also allow directional drillers to see the actual hole trajectory so they can avoid large doglegs. This results in a smoother wellbore, enabling longer laterals. Additionally, experts are starting to utilize high-density real-time continuous MWD survey data to analyze wellbore tortuosity.
Benefits of Survey Data
As the saying goes, “an ounce of prevention is worth a pound of cure.” Data, especially high-density data, serves a cure in this case because it helps engineers to make rapid assessments of wellbore trajectory. When engineers are able to catch a change in direction many feet before the stationary survey, they can respond quickly. Having the ability to catch problems early can mean the difference between controlling or losing a well.
High-density survey data from MWD tools allows the construction of smoother well paths. Because high-density survey data is able to capture continuous inclination and azimuth, engineers are able to see everything they are doing in a live environment. The use of continuous data for wellbore positioning also reduces true vertical depth errors.
Additionally, using continuous azimuth for wellbore positioning instead of only using the stationary data reduces lateral errors, particularly those that arise when drilling a long horizontal section. A key aspect of the lateral positioning involves wellbore spacing in unconventional wells.
High-density survey data enables an improved understanding of the shape and tortuosity of the wellbore. It is important to analyze tortuosity on a small scale since 90-ft data does not provide enough granularity. When high-density survey data is part of the drilling process and is used to its full extent, operators are able to improve drilling efficiencies, lower costs and extend the life of drilling equipment.
Case Studies
Continuous inclination provides immediate knowledge of build rates or drop rates in the wellbore without having to wait for the stationary survey. This additional inclination information allows the directional driller to optimize the slide time when using a mud motor. Drilling with a mud motor and changing between sliding and rotating creates a stair-step effect. This is not typically identified by standard surveying intervals that are at 93 ft.
When high-density survey data is used to its full extent, operators are able to improve drilling efficiencies, lower costs and extend the life of drilling equipment.
With continuous inclination, however, information can be utilized to provide an improved explanation of the increased open-hole torque and drag that drillers experience while they are drilling a curve.
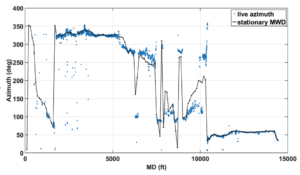
Figure 1 shows continuous (live) inclination versus static inclination measured at every stand. From 0° to 10° of inclination, the continuous data appears noisy because the Z-accelerometer is aligned with the vertical component of the gravity field; these are small variations in inclination that do not generate large changes in the Z-accelerometer reading. The noise gradually reduces over 10°. At that point, the continuous inclination becomes very accurate as it can be seen near horizontal.
Figure 2 shows a zoomed-in view of a lateral section. The continuous inclination correlates well with the stationary data. However, it has irregular outliers. High drilling vibration levels are the primary source of the outliers. Additionally, the continuous inclination shows a higher degree of tortuosity in the wellbore compared with the static surveys taken at every stand. This accounts for the higher torque while drilling versus the modeled torque determined during the planning phase.
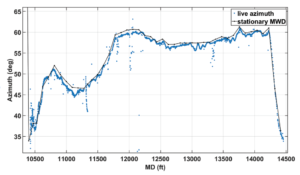
The additional continuous azimuth data allows the directional driller to optimize the sliding time required to turn the well when a mud motor is used. While changes in downhole formation can push the wellbore away from the desired plan, the availability of continuous azimuth data allows the directional driller to identify this issue early and react much faster than just relying on traditional static surveys taken at every stand.
Figure 3 shows continuous azimuth versus static azimuth measured at every stand. The quality of the continuous azimuth data is superior when the tool is not aligned with magnetic north or magnetic south. Continuous azimuth data has more outliers when vertical. As inclination gets higher, the amount of outliers reduces incrementally.
Figure 4 shows a zoomed-in graph of the horizontal section of a well. A systematic error exists between continuous azimuth and static azimuth. This error may have occurred because the stationary data was corrected for axial magnetic drillstring interference while the continuous azimuth was not corrected.
Even with the presence of magnetic interference, the continuous azimuth provides useful data regarding the detailed shape of the wellbore trajectory. For this particular example, the last stand drilled shows the formation caused a change in the trajectory, which caused an azimuth shift of 15° over one stand length.
Conclusion
As operators attempt to work within strict budget requirements while trying to improve production rates, they continue to depend on high-quality, accurate data to keep in line with well plans. High-density survey data, in particular, helps to deliver a clearer understanding of what is occurring downhole. Both maintenance and well intervention are critical – especially in this complex drilling environment, where there are longer laterals and less space to drill due to an abundance of offset wells.
There are a number of approaches to utilizing data and models to gain valuable insights into upstream operations that contribute to improved reliability, productivity and operating integrity. Overall, high-definition survey data provides valuable knowledge and critical insights that operators can use for the entire life of a well. DC