Pilot test for automated mud management leverages real-time monitoring, hydraulic modeling
Control system that adjusts mud properties in real time was also built to test a new concept for placing drilling mud into an automatic closed loop
By Jan Ole Skogestad, Manuel Aghito, SINTEF Industry; Jelmer Braaksma and Jan Atle Andresen, Huisman; Jan Ove Brevik, Equinor; George Gibbs Smith, Intelligent Mud Solution
The drilling industry is undergoing rapid changes, with increased focus on digitalization and automation. The increased availability of sensors – and growing opportunities for extracting valuable information from the data they provide – are also driving the industry toward efficient solutions that reduce manual operations.
The handling of equipment and fluids is seeing higher degrees of automation, with the goal of reducing nonproductive time (NPT) and the risk of unwanted events. However, when it comes to mud management, there is still a large gap to be filled as the operation is still largely manual today. A step-change will be needed to enable consistent high-performance operations with accurate pressure control.
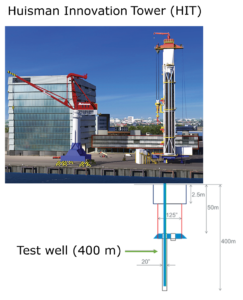
Comparing mud properties control to choke control in managed pressure drilling (MPD) sheds light on why a change is needed. When drilling with MPD, downhole pressure can be measured every second, so that the driller and the control system always have current values and trends available. Based on these measurements, the required choke pressure to either maintain the downhole pressure at the current level or adjust it to a new value is calculated, and the choke opening is adjusted automatically.
Managing mud properties, such as density and viscosity, is a different story, although these properties are crucial for drilling performance. Requirements for the mud are based on several factors, including wellbore pressure gradient, formation properties and hole-cleaning requirements. The mud mix “recipe” is then determined based on these requirements, and the mud is mixed in batches.
Measurements of mud properties are done using manual instruments designed decades ago, such as a mud balance weight for density and a Fann viscometer for rheology. They’re also typically done only a few times a day using small mud samples. Based on these measurements, the mud may be adjusted by adding ingredients, but only infrequently. This process is error-prone and not suitable for optimizing and automating mud management.
With existing and new technologies, it is possible to make a step-change by putting the mud into an automatic control loop. Key elements are:
• Real-time automatic sensors for density and viscosity, allowing continuous monitoring of the mud;
• Mathematical models for simulating flow in the wellbore, forming a basis for calculating the required mud properties; and
• Automatic mud mixing and treatment systems.
By combining these elements, it is possible to develop a system for automatic mud management that adjusts the mud as needed. In addition to putting mud into the control loop, this also provides data about the mud that can be input into data-driven methods for controlling and monitoring the operation, e.g. allowing for more advanced automation and remotely controlled operations.
Test Site Setup
In a pilot test performed in Schiedam, The Netherlands, in August 2018, an automatic mud management concept incorporating the elements described above was demonstrated successfully. The primary objective of the pilot test was to verify, at realistic rig conditions and based on real-time rheology measurements, the impact of automatic mud treatment on the successful and robust performance of typical drilling operations. The objective was achieved by combining different pieces of technology as described below.
The test site was at the Huisman Innovation Tower (HIT) test facility. The HIT is a 90-m tall full-scale drill tower capable of handling 55-m (180-ft) stands and simulating dynamic vessel movements. A 400-m deep vertical test well of 20-in. diameter (118 in. for the upper 50 m) has been drilled and cased at the same location.
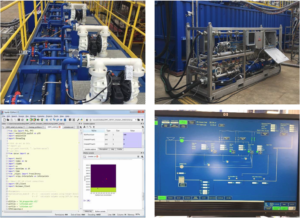
An automatic mud mixer with a control system for managing the mixing process was built for this pilot test. Two premixed fluids with known properties were used as starting points; one was highly viscous but not very dense, and the other had high density and low viscosity. This allowed for fluid mixes with a wide range of fluid properties by varying the mixing ratios.
For the purpose of this test, one high-density CaCl2 brine and one high-viscosity solution based on xanthan gum and water were used. Combined with fresh water, this provided the possibility to mix muds with a sufficient range of different properties for the experiments to be performed.
The mixer had designated tanks for each fluid; 5.8-cu-m tanks for each premix, a 4.8-cu-m water tank, and an 18-cu-m active tank where the fluids were mixed. The mixed fluid was pumped from the active tank to the well. Fluid from the well was then returned to the active tank, so keeping track of the active fluid properties was a key task.
An automatic sensor for real-time monitoring of density and rheology, RheoSense, was installed so that it could be connected both to the upstream and downstream side of the well, as well as to the individual tanks in the mixer.
By diverting some of the flow into this sensor, it provided the density and a rheology profile by combining differential pressure measurements in horizontal and vertical pipe sections at different flow rates (controlled internally in the sensor).
To keep track of the flow through the well and provide inputs to the mixer based on downhole conditions, a downhole hydraulic flow model was used. By running several steady-state instances of the flow model using different mud properties, it was possible to determine the mixing ratios needed and provide that as an input to the mixer. The sensor could then be used to verify that the mud produced had the prescribed properties. The downhole sensors were used for calibration ahead of the tests, as well as for verifying the downhole response to mud changes.
To operate a system like this smoothly, communication and data handling were critical. A central server was used for storing the data, connected to all the components using the OPC/UA protocol.
Pilot Test Results
After testing the individual components of the setup and the communications, the pilot test was executed. A set of different scenarios that may be encountered in real drilling operations where the mud properties need to be adjusted were simulated, including:
1. Need to increase yield point of mud;
2. Need to increase static pressure; and
3. Need to reduce dynamic pressure range.
Case 1: Increase yield point
Keeping the yield point above a certain level reduces unwanted settling of cuttings in static periods.
Since the RheoSense continuously provides rheology data, it was easy to assess the current state of the mud at any given time. By using the real-time data to estimate the current yield point of the fluid, the necessary increase to achieve the new value could be readily found. The optimization algorithm for finding the mixing parameters using the downhole model can then be configured with a higher lower bound for the yield point, along with other parameters, such as a window for the bottomhole pressure (BHP).
In this case, the desired minimum value for the yield point was set to 7 lb/100 sq ft, while keeping the BHP within a relatively wide window of 43.5 to 52 bar. The initial yield point value was determined from sensor readings to be 5.8 lb/100 sq ft.
After determining the new mud recipe, which consisted of adding approximately 1.4 cu m of viscous premix and circulating through the well until a new stable state was reached, the yield point stabilized at approximately 8.7 lb/100 sq ft, somewhat higher than expected. After investigating the data streams, it became clear that the initial yield point value was underestimated, as the rheology values seemed to be fluctuating in the period before reading the yield point value, and the value used was in the low end of the range.
The fluctuations seen in the measurements may have been due to actual inhomogeneities, as a consequence of the mixing principle, where the premixes were entered into the active mix over a short time span. Thus, a few circulations were needed to homogenize the fluid. In this case, the fluctuations from a mixing process prior to the test were still present. By averaging over a longer period, a higher initial value would have been used, and the mixing recommendation would have been to add a smaller amount of viscous premix, resulting in a lower final yield point.
Case 2: Increase static pressure
The next case to be simulated was a situation where the BHP needs to be increased from its current value, e.g. in order to prevent gas influx. At the same time, the yield point should be kept at its current level in order to maintain flow and hole-cleaning properties. The initial value of the BHP was 44.2 bars, and the goal was to first increase it to 45 and then to 45.5 bars, while keeping the yield point at approximately 8.8 lb/100 sq ft. The mixing recommendation in the first step now consists of adding both dense and viscous premixes, since only adding dense premix would dilute the fluid of xanthan gum and, therefore, make it less viscous.
After performing the mixing and circulating through the well, the BHP was measured by the downhole pressure sensor at 44.99 bars. After the second step, the measured BHP was 45.50 bars. The yield point and other rheological properties remained at the same levels as before.
Case 3: Reduce dynamic pressure range
The goal was to reduce the downhole pressure at high flow rates, while maintaining the current static BHP. The system should automatically dilute the fluid with the correct volumes of water to reduce viscosity and add dense brine to maintain static pressure.
The initial yield point was 12.2 lb/100 sq ft, corresponding to a high dynamic pressure range, i.e. the pressure losses in the well are highly dependent on the flow rate. In this case, this gave a BHP of 53.5 bars at a flow rate of 1,500 l/min, the maximum flow rate used in these tests. The target BHP window was then set to 44.8-51.6 bar, along with a minimum requirement on the yield point of 9 lb/100 sq ft.
The optimization algorithm recommended adding approximately 4.2 cu m of water and 1.8 cu m of brine, which would give a yield point of 10.0 lb/100 sq ft. This turned out to be an accurate prediction of the resulting yield point, within a 0.5% deviation of the resulting observed value. However, the pressure was a bit off, with a maximum measured BHP at 52.9 bars.
After investigating the measurements before and after, it became clear that the optimization algorithm had not been properly calibrated to the measurements. New estimates with the correct calibration factors indicate that the BHP would have been much closer to the target value if the model had been calibrated correctly.
Discussion
The pilot test was determined to be successful after evaluation. The different components worked well together, and the measured results were largely as expected. There were some erroneous predictions, but they could be reasonably explained.
Challenges that were observed include fluctuations in measurements due to mud heterogeneities, which sometimes made it challenging to determine representative values of different fluid properties. It was evident that it took time to homogenize the mud after starting the mixing process, for example. This was due to a simplified mixing concept and can easily be overcome with available mixing technology. A lesson learned was that it is quite different to work with continuous trends of fluid properties rather than with discrete measurements taken a few times a day, and this needs to be incorporated in the related work processes.
Having real-time access to fluid properties opens new possibilities in mud management, especially when it comes to automation, but also in creating better understanding of how the fluid works and how it changes throughout the drilling operation. Potentially having the full history of the fluid available digitally enables the use of data-driven methods for optimizing mud handling and ultimately improving the drilling operations. This also allows for more transparency around mud mixing and paves the way for new business models.
Summary
A successful pilot test of a concept comprising the use of advanced real-time mud monitoring, automatic mixing and downhole predictive models has been performed, demonstrating that a step-change toward automation and digitalization in mud management is possible. By refining the concept further and incorporating new technology in the work processes on the rig, this could significantly improve drilling efficiency. DC
This article is based on an presentation at the 2019 IADC Advanced Rig Technology Conference & Exhibition, 22-23 October, Amsterdam.