Drill bit adapts depth-of-cut control to mitigate stick-slip, enhance ROP
After proving performance in simulations and full-scale lab testing, self-adjusting bit recently proved potential in Delaware Basin, drilling 3,355 ft in one run
By Jayesh R. Jain, Gregory Ricks, L. W. Ledgerwood III and Anthony Phillips, Baker Hughes
Mitigating vibrations during drilling remains a challenge for many fixed polycrystalline-diamond-compact (PDC) bits, particularly as drillers attempt to drill longer sections in a single bit run. Vibration arising from torsional stick-slip and impact loading in interbedded formation and transition can cause premature damage to a drill bit and other components in the bottomhole assembly (BHA) – ultimately hindering drilling performance.
The drilling industry has made great strides toward improving bit/BHA designs, optimizing operating procedures and using surface controls to minimize vibrations. However, drillers often have to strike a balance between vibration mitigation and drilling performance because different formations and operating conditions often have conflicting bit design requirements. This challenge becomes more severe in long single bit runs through diverse formations.
To address such challenges, Baker Hughes recently developed a self-adjusting PDC bit technology that dynamically adapts its depth-of-cut (DOC) control characteristics to rapidly changing drilling environments. Through the use of replaceable, self-adjusting units installed inside the bit blades, the bit quickly mitigates vibrations while improving rate of penetration (ROP).
This article describes the self-adjusting bit technology and reviews its performance under various drilling conditions in both computer simulations and full-scale laboratory testing. A field run from the Delaware Basin in West Texas is also reviewed, in which the bit improved drilling dynamics through a formation containing interbedded shale, limestone and salt.
Adaptive DOC Control

The self-adjusting bit mitigates vibrations by resisting rapid changes in DOC that occur during unfavorable dynamic events. This auto-adjustment is accomplished through a passive hydro-mechanical feedback mechanism encapsulated in self-contained units that are installed inside the bit blades (Figure 1). Each unit houses a piston-cylinder arrangement with its own hydraulic fluid. A DOC control element, typically a diamond “ovoid,” is attached to the unit.
The control element gauges the contact force between the bit and the formation to sense whether and how to adapt. Rapid changes in contact force indicate unintended variations in DOC, which are typically encountered during the onset of stick-slip, weight transfer or stacking issues, and entering erratic/interbedded formations. The control element responds by absorbing a portion of the load and then instigating a gradual retraction stroke (over a minute or longer) to draw the ovoid inward and mitigate the dysfunctions. When there is no external load on the ovoid, the mechanism activates the extension stroke, which is carried out within a fraction of a second. This extension and retraction of the diamond ovoids affords a wide range of DOC control.
Time-Domain Modeling
As part of the development process, time-domain modeling was performed to study the influence of the self-adjusting mechanism on drilling system response. A non-linear dynamic model was built by integrating a simplified dynamics model with 3D bit dynamics code. This model was developed to simulate time-domain drilling with self-adjusting bits under confining pressures.
The model’s accuracy was validated by comparison with full-scale drilling tests in the laboratory (Ledgerwood and Kelly, 1991) in limestone under a confining pressure of 3,000 psi (21 MPa). Each drilling test consisted of steady drilling at constant weight on bit (WOB) of 30,000 lb (13,608 kg), a momentary reduction in WOB to 5,000 lb (2,268 kg) representing a dynamic event, followed by another steady drilling phase (Jain et al, 2016).
During testing, with the diamond ovoids initially extended, the bit starts out with reduced aggressiveness similar to fixed DOC control, and gradually exhibits increasing aggressiveness as drilling progresses and the diamond ovoids retract. When the perturbation in WOB causes fluctuation in DOC, the diamond ovoids extend to reduce the bit aggressiveness.
The integrated time-domain model simulated the drilling test by using parameters from bench test results. The simulation results agreed with the test results.
Improper Start-Up
Time-domain simulations were also performed to study a startup scenario where bit weight overshoots before stabilizing at the set point – a common occurrence that damages PDC cutters and shortens bit life. Two simulated 8 ¾-in. bits, a standard PDC bit and the self-adjusting bit, were subjected to a loading path comprising an approach to the bottom, a 67% overshoot in WOB and return to the set point.
The simulations showed that the cutters in the cone region of the standard PDC bit experienced high loads, while the self-adjusting bit reduced the load on the primary cutters by partly absorbing it on the extended diamond ovoids. As the WOB returned to the set point in the simulation, the self-adjusting ovoids continued to support a significant portion of the load and gradually retract. These results suggest that the self-adjusting feature can minimize the cutter overload and let the bit set in gradually, thus expanding the range of startup practices that can be utilized without instigating vibrations.
Bit Stick-Slip on Motor BHA
While the use of mud motors in the BHA helps reduce the likelihood of stick-slip, it still occurs in applications where drillers push their operating parameters to maximize performance. Therefore, two 3,150-ft (960-m) deep, 8 ¾- in. vertical wells were drilled at a research facility to compare the tendency of standard and self-adjusting PDC bits to instigate bit stick-slip on motor BHAs.
In each test, the same motor, BHA, and 3 ½-in. drill pipes were used. The adjustable kick-off angle was set to 1.8° and was run in slick configuration. The BHA was equipped with a commercially available MWD service, which recorded diagnostic data and stored raw high-frequency measurements on demand.
The tests aimed to identify WOB-RPM combinations at which the system starts experiencing stick-slip. Each test began at a constant surface RPM and flow rate, and a WOB value that was sufficiently low to prevent stick-slip. After one minute at constant WOB-RPM settings, the WOB was incrementally increased until sustained stick-slip appeared or maximum WOB was reached. Observations of surface torque variations and pulsed stick-slip severity levels from the MWD service were used to indicate stick-slip. The process was repeated at several surface RPM-flow rate combinations.
In one representative test, the surface RPM was 60 and the motor turned at 100 RPM. When the standard PDC bit was used, the run sustained BHA stick-slip, which developed into bit stick-slip at higher WOB. In the test with the self-adjusting bit, the run sustained BHA stick-slip but did not develop into bit stick-slip at higher WOB.
Similar results in tests run at different RPM-flow rate values all demonstrated that the standard PDC bit exhibited stick-slip, while the self-adjusting bit did not. This suggests that the self-adjusting bit can effectively operate at higher WOB.
WOB Fluctuations
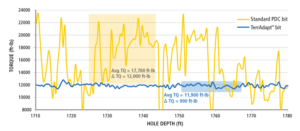
Unintended fluctuations in WOB are common in drilling operations. Field tests were conducted in research wells to induce such variations in WOB and monitor the response of a standard PDC bit and the self-adjusting bit. The driller varied surface WOB manually, with auto driller configured to slack off or pull to adjust the downhole WOB to the set point. The test was carried out on a conventional rotary system, as well as on a motor BHA.
When drilling with the rotary system, the WOB fluctuations caused the PDC bit to exhibit fully developed stick-slip in two out of three loading cycles. The self-adjusting bit exhibited less severe torsional oscillations with no instances of stick-slip.
A similar test using the motor BHA produced WOB oscillation cycles that were consistent and of similar amplitude between the PDC and self-adjusting bit tests. But once again, the standard PDC bit exhibited torsional oscillations during the first cycle, which led to bit stick-slip in subsequent cycles. The self-adjusting bit did not exhibit significant torsional oscillations in response to the oscillating WOB.
Wear
A 230-ft (70-m) interval was drilled with standard and self-adjusting PDC bits in two separate vertical wells at the field test facility, after which the cutters were examined for wear. The standard PDC bits experienced smooth wear, with visual evidence of scars and flats extending past the chamfer. The wear flats on the self-adjusting bit, by contrast, were appreciably smaller and mostly confined to within the chamfer. This test suggests promise in extending bit life with the self-adjusting DOC control by reducing smooth wear.
Proving Its Potential
Soon after the completion of these qualifications tests in testing facilities, Baker Hughes discussed the technology with operators who were willing to evaluate the bit’s ability to mitigate their torsional vibration issues.
One such operator, drilling in the Delaware Basin in West Texas, was experiencing erratic drilling performance in 12 ¼-in. intermediate sections running through interbedded shale, limestone and salt. Drilling efficiency was hindered by high torque fluctuations and stick-slip, and downhole tool failures were driving up nonproductive time and costs.
Looking to minimize downtime and maintain stable drilling through interbedded sections, the operator implemented the self-adjusting drill bit. It completed a 3,355-ft (1,023-m) long section in one run and achieved an average ROP of 168 ft/hr (51 m/hr). This was 27% higher than the ROP achieved in offset wells drilled with standard PDC bits.
By proactively mitigating stick-slip and impact loading, the adaptive bit completed the section with no damage to the BHA and minimal impact damage to the cutters. The bit also reduced average torque by 35% and torque variations by 90%. This translated to more efficient drilling, with up to a 45% improvement in mechanical specific energy recorded.
Summary
In laboratory tests and field trials, the self-adjusting PDC bit technology demonstrated an ability to mitigate stick-slip, and the torsional vibration that results, in a variety of drilling scenarios. Results of 3D non-linear dynamic modeling in time-domain showed the technology significantly reduces cutter overload from overshoots in bit weight compared with fixed PDC bits. Additionally, field tests in research wells showed that the bits exhibit reduced stick-slip and torsional oscillations compared with conventional PDC bits. The technology also showed promise in reducing cutter wear by reducing fluctuations in loads.
Ultimately, the self-adjusting mechanism can adapt DOC control characteristics to changing drilling environments and mitigate vibrations while delivering improved ROP. Baker Hughes envisions expanding the bit for other well scenarios, as a part of its strategy to improve drilling efficiency through the use of smart automation technology. DC
Click here to view a video interview from the bit’s launch at the 2017 SPE/IADC Drilling Conference.
Acknowledgements: This article was adapted from SPE/IADC 184736, presented at the 2017 SPE/IADC Drilling Conference, 14-16 March, The Hague, The Netherlands. The authors thank Baker Hughes for permission to publish this article and the Woodlands Testing Services and the Baker Hughes Experimental Test Area crew for the testing support.
References
Jain, J.R., Ricks, G., Baxter, B., Vempati, C., Peters, V., Bilen, J.-M., Spencer, R., and Stibbe, H. 2016a. Step change in drill bit technology with self-adjusting Polycrystalline-Diamond-Compact bits. SPE Drilling and Completion. doi:10.2118/178815-PA
Jain, J.R., Ricks, G., Baxter, B., Vempati, C., Peters, V., Bilen, J.-M., Spencer, R., and Stibbe, H. 2016b. Self-adjusting PDC Bits Could Enable Autonomous Drilling Systems. Hart’s E&P Magazine. June 1.
Ledgerwood, L.W. and Kelly, J.L. 1991. High Pressure Facility Re-Creates Downhole Conditions in Testing of Full Size Drill Bits. Presented at the ASME Energy-Sources Technology Conference and Exhibition, New Orleans, 20-24 January.