Dual cutting structure on hybrid roller cone bit increases efficiency of bridge, frac plug drill-outs
4 ½-in. bit drilled frac plugs at average of 8.1 min/plug in 57-well study in Eagle Ford
By Matt Stroever, Varel Oil & Gas Drill Bits
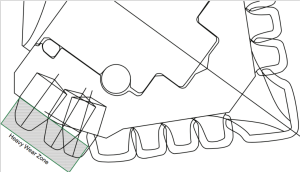
Drilling out bridge and frac plugs is a regular and inefficient task in multi-zone completions. The job is commonly done using a variety of standard drill bits. However, removing between 15 and 40 plugs comprised of hard outer slips surrounded by ductile composites and elastomer materials presents several challenges to bit performance. Like drilling operations, the completion objective is to efficiently drill as much as possible before having to pull out of hole to replace the bit.
The plug’s hard outer slips can quickly wear steel tooth cutting structures so that the bit is increasingly less effective with each plug it drills. It is also difficult to achieve small cuttings across the various plug materials in use, which can limit hole-cleaning efficiency. In addition, the fluid pressure behind isolated completion zones can result in pressure spikes that reduce bearing life.
Varel Oil & Gas Drill Bits has developed the SlipStream RC Pro hybrid roller cone bit, which features a dual-cutting-action cutting structure comprised of steel tooth and tungsten carbide insert (TCI) cutting structures on each cone. In an extensive study in South Texas, the roller cone bit improved performance with greater efficiency and less cutting structure wear.
Eagle Ford Completion Study
In a 57-well study conducted in the Eagle Ford shale play in South Texas, 4 ½-in. Slipstream SRP624 bits drilled frac plugs at an average of 8.1 min/plug – 13.6% faster than standard tooth roller cone bits. The bits also averaged 3.3 more plugs per use than the competitive steel tooth or TCI bit.
Further, the bits produced considerably smaller cuttings to significantly decrease wash down time between plugs. The bits drilled consistently over the full set of plugs compared with the conventional bits, where cutting structure wear resulted in slower drilling after multiple plugs had been drilled. Beyond the 15th plug, where drilling with conventional bits commonly slows, the SRP624 bits resulted in higher drill rates.
In an Atascosa County well, a single bit drilled one composite bridge plug and 25 composite frac plugs in 234 minutes total drilling time. The average drilling time was 9 min/plug. Run parameters include 2.75 bbl/min pump rate, 3.9 bbl/min return rate with a circulating pressure of 3,800 psi and wellhead pressure of 2,300 psi.
A Gonzales County completion drilled one composite bridge plug and 21 composite frac plugs in 175 min for an average drill time of 8 min/plug. The pump rate was 2.75 bbl/min with a return rate of 3.9 bbl/min, circulation pressure of 3,800 psi and wellhead pressure of 2,300 psi.
The bits used in both well completion drill-outs experienced minimal wear and had dull grades of 1-2-WT-G-E-I-ER-TD.
Recent Performance

A 4 5/8-in. SRP624 drilled 36 plugs in Texas’ Martin County, averaging 4.97 min/plug to complete the drill-out. Operating parameters were a flow rate of 4 bbl/min, an RPM of 400 and a weight on bit (WOB) between 1,000 to 4,000 lb. There were no motor stalls or short trips required in drilling the plugs. Total time required to complete the job, from tagging of the first plug to completing the 36th plug, took 20 hrs.
In Wyoming, a 3 ¾-in. SRP624 drilled 45 plugs. The operator chose to control drilling at a speed of 25 min/plug as they do with all bits in this application. When drilling normally, the SRP624 averaged 8 min/plug. In this application, an extra 15 plugs were drilled.
Karnes County, Texas, saw a 4 ½-in. SRP624 drill 34 frac plugs in 218 minutes on a coiled-tubing rig. The dull grade of the bits was 2-1-CT-M-E-1-ER-TD. As a result of the dull condition, the operator has extended the number of plugs to drill before pulling out of hole to replace the bit.
Operating parameters varied with each application. WOB is difficult to accurately predict, but typical applications range from 3,000 to 5,000 lb. The RPM can range from 80 to 400 depending on a rotary or motor application. Typical motor speeds are between 230 and 350 RPM, dependent upon flow and motor configuration.
Plug Drill-Out
A wide variety of bit types are commonly used to drill out frac and bridge plugs, including flat-faced TCI mills, PDC bits, steel tooth bits and tungsten carbide bits. The bits are run on rotary and motor applications and are often used with coiled tubing. Bit sizes are driven by the casing size used in the completion process and range from 3 7/8 in. to 4 7/8 in. for most applications.
Each standard bit poses a problem when used for plug drill-out operations. These difficulties range from being overly aggressive and requiring excessive torque, to being too passive or not sufficiently aggressive. Torque problems can include motor stalls, producing large pieces of plug material that are difficult to circulate out of the hole, resulting in prematurely worn or severely damaged cutting structures.
Bit wear problems are a key issue in drilling out plugs. Common bridge and frac plugs consist of various combinations of body materials – composites, brass, thermoplastics, cast iron metal and ceramic inserts. These materials utilized in different frac and bridge plug designs present several drilling challenges that the bit cutting structure must address.
The hole wall, casing, slips and insert areas require the bit cutting structure be able to destroy ceramic or cast iron and dislodge titanium alloy inserts from the hole or casing wall. The bit must also be sufficiently durable to withstand continuous contact with the casing wall and lodged inserts of the frac plug.
Drilling the plug body and filler materials require that the cutting structure be able to destroy the aluminum, brass or composite filler materials to a cutting size for easy circulation out of the well, as well as withstand the occasional insert or slip impact.
The mandrel and filler materials require that the cutting structure be able to destroy the aluminum, brass or composite material and that the cutting structure be strong enough to withstand the materials and torque associated with cutting them.
In addition, the bit must withstand fluid pressure from drilling into the completion’s isolated zones. During hydraulic fracturing operations, the plugs isolate high-pressure fluid. When the plug is drilled, the pressurized fluid is released and subjects the drill bit to pressure spikes. Maintaining bearing life requires a pressure compensation system capable of handling these rapid variations in downhole pressure.
Plug Drilling Technology
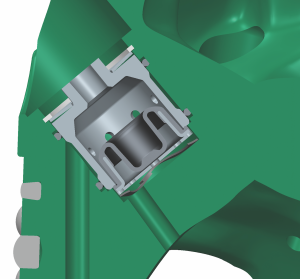
Varel’s SlipStream bit design has both steel tooth and TCI cutting structures on each cone of the bit. The unique design places the TCI cutting structure on the outside of the cone, where heavy wear occurs from drilling hard frac plug components, and a steel tooth cutting structure on the inside to drill the composite and softer material parts of the plug.
The fit-for-purpose tungsten carbide inserts are subjected to a patented high energy tumble process to increase durability. Short and closely spaced steel tooth inner rows are fully covered by DC30 premium welded hard metal to provide tooth durability resulting in small cuttings for easy transport.
Bit life is further enhanced with a patented bearing seal design that increases reliability with greater resistance to pressure spikes and mud packing. Seals are manufactured from a highly saturated nitrile (HSN) material with more thermal stability, broader chemical resistance and greater tensile strength. Pressure fluctuations experienced when drilling out each completion interval is addressed with a conical seal gland that is positioned to better handle and maintain a preferred sealing location and interface. Thermal insulation of the seal is also provided netting a lower operating temperature for the seal.
A common result of pressure spikes is cone pumping, in which grease can be lost through a compensator relief. A patented pressure attenuator added to the lubrication system mitigates the pressure spikes at the seal area, providing the newly designed canister compensator time to react without releasing grease. The new compensator design used in SlipStream bits results in an increase in grease volume of 200% for the 4 ½-in. and 4 ¾-in. SlipStream product. With the increased volume of grease, the bearings last longer and run cooler increasing bit efficiency and life.
The SlipStream bit was achieved through cutter research and bit design focused on cutter performance when drilling out metal and composite materials commonly encountered with bridge and frac plugs. The dual cutting structure of the SlipStream design improves the efficiency and reduces the cost of producing unconventional assets.
A recent West Virginia SlipStream application resulted in 68 plugs being drilled by one bit, attesting to the longevity of the cutting structure and efficiency of the design. The SlipStream bit addresses the new challenges presented by the metal, composite and elastomer components encountered while drilling bridge and frac plugs in multi zone completion wells. DC
SlipStream is registered trademark of Varel.