Drilling & Completions Tech Digest
BP enhances EOR with launch of first robotic core-flooding system
BP has begun operating the world’s first robotic core-flooding system. The Core Flood Robot is the most recent addition to the operator’s program of enhanced oil recovery (EOR) research facilities.
“The EOR technologies being developed by BP are vitally important to help increase global oil supplies,” Ahmed Hashmi, BP’s Head of Upstream Technology, said. Core flooding measures the effectiveness of water or gas injected into an oil-bearing rock sample to displace oil. This can be used to assess the potential for water flooding in an oil field. The Core Flood Robot is operated by the same team that developed LoSal EOR, BP’s reduced salinity water-flooding technology. More than 45 core-flood tests were performed in validating the LoSal EOR effect before field trials in Alaska. BP and its partners are now deploying the technology at scale on the Clair Ridge project in the North Sea.
Mozambique seismic survey completed, ready for licensing
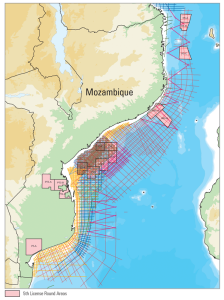
Schlumberger and the National Petroleum Institute of Mozambique are offering a multiclient seismic survey conducted offshore Mozambique. The survey includes reprocessed 2D lines and newly acquired seismic data that provides detailed imaging of the subsurface.
“The recent discoveries and regional appraisals in the area indicate significant frontier exploration potential,” Maurice Nessim, President, PetroTechnical Services, Schlumberger, said. “By combining multidisciplinary expertise for advanced attribute analysis and high-quality acquisition technology, the data can provide valuable insights in this geologically complex area.”
More than 110,000 km of exclusive 2D seismic data are available for licensing. The multiclient data are available in all offshore blocks offered in the Mozambique 5th Licensing Round issued by INP.
Completion records set with 94, 104 stages
NCS Multistage recently announced two completion records with its Multistage Unlimited coiled-tubing completion technology. The wells were completed for an independent operator in McKenzie County, North Dakota. The first well, in the Middle Bakken formation, was completed with 94 stages. Soon after, an offset well in the Upper Three Forks formation was completed with 104 stages. This was a hybrid completion comprising 97 NCS GripShift cemented casing sleeves, with seven NCS BallShift cemented ball-drop sleeves in the lower section of the well. In both wells, all stages were successfully fractured.
Nigeria’s first rigless ESP conveyance system installed
AccessESP has installed the first rigless ESP conveyance system in Nigeria in the Ukpokiti No. 4 offshore well for Shebah Exploration and Production Co.
The installation was performed using AccessESP’s 375 series, 190 HP Permanent Magnet Motor and wet connector system. The ESP system was deployed through 4.5-in. tubing on conventional 0.125-in. slickline after installation of the tubing string. The Ukpokiti No. 4 system was deployed via slickline to a depth of 5,900 ft and took less than 15 hrs to install.
For a Permian Basin well, AccessESP also announced that its rigless conveyance system had passed one year of continuous service since being pulled and reinstalled.
ORLEN applies Tenaris connections in Polish shale

ORLEN Upstream applied the TenarisHydril Wedge 563 connection in the Stoczek-OU1K horizontal shale well last year, resulting in a smooth connection and reaching of the target depth.
The well is one of few horizontal shale wells that have been drilled in Poland so far. It is part of ORLEN’s exploration of the complex Lublin Basin assets that extend under Poland and Ukraine. Stoczek-OU1K was drilled to explore the gas accumulation and producing capability in the Lower Silurian and Ordovician shale deposits.
The Wedge 563 connections used in this operation came with the Recess Free Bore option to facilitate undisturbed flow in the well during the fracturing process. The connections presented zero re-makeups and rejects. Final survey data of the well was taken at 4,307-m MD and 2,953-m TVD, with a final inclination 91.5° and maximum recorded dogleg severity of 8.56°/100 ft. During the five-day operation, a mud-logging unit recorded torque peak of almost 25,000 ft/lb and a maximum rotational speed of 90 rpm.
Subsea compressor to increase Gullfaks recovery
The world’s first subsea wet gas compressor station will soon come to the Gullfaks field in the Norwegian North Sea, Statoil announced. Subsea compression, combined with conventional low-pressure production in a later phase, is expected to push the recovery factor for gas from Gullfaks South Brent from 63% to 73%.
The compressor was developed in cooperation with One Subsea, and large parts of the compressor station were built by suppliers and sub-suppliers in western Norway and in the Bergen region.
The delivery from One Subsea consists of a 420-ton protective structure, a compressor station with two compressors totaling 650 tons, and all necessary topsides equipment for power supply and control of the plant.
The compressor station has been undergoing final system integration tests at Horsøy outside Bergen before being prepared for installation and hook-up to Gullfaks C in 2015. The possibility of tying in several of the subsea templates connected to Gullfaks C to the compressor station will also be considered. This would further increase the profitability of the project.
ExxonMobil awards license for Alternate Path
ExxonMobil Upstream Research Co has awarded Delta Screens & Filtration a limited international license for ExxonMobil’s Alternate Path technology patent portfolio for gravel packing cased and open-hole completion wells.
Alternate Path helps to improve the reliability of wells completed in sand-prone reservoirs.
The technology provides alternate flow paths called shunt tubes in the downhole tool used for packing gravel in the producing sections of a well. The shunt tubes enable the Alternate Path packing operation to continue when sand prematurely blocks the well annulus, which would stop a conventional packing operation. The shunt tubes divert the gravel slurry around sand blockages and through distributed portholes to fill voids in the annulus until a complete pack is in place.
Click here for more articles about industry technology milestones and downhole or subsea innovations are available on DC’s Innovating While Drilling microsite.