Automated well control: Industry gets ready for 20,000 psi and beyond
Well control system incorporates real-time data to precisely manipulate pressures, manage risk in extreme HPHT wells
By Paul Sonnemann and Helio Santos, SafeKick

The drilling industry continues to push the limits of its technologies in order to access deeper, hotter, higher-pressure reservoirs. As the industry moves toward drilling wells where surface pressures may top 20,000 psi – or “extreme HPHT wells” – it must ensure its capability to manage unexpected well control events.
Such high-pressure wells typically involve a multitude of factors during the well construction process, and there can often be a high degree of uncertainty when interpreting commonly available data. Therefore, even after following time-consuming procedures to properly understand a situation, doubts may remain about whether a certain condition requires non-standard control action. This can lead to decisions that add significant costs or unnecessarily threaten to stop the well short of its target.
Well control challenges associated with extreme HPHT operations may include:
• Narrow safe operating “windows”;
• High wellbore temperatures;
• Fluid compressibility issues;
• Mud rheology challenges;
• Relatively high equivalent circulating density (ECD) effects in long, small-diameter hole sections;
• Large wellbore fluid volumes requiring long displacement time; and
• Surface equipment complications/limitations.
SafeKick’s SafeVision Well Control Package was developed to provide benefits during conventional well control operations, but its features may also help to manage extreme HPHT wells. These include:
• Conversion of real-time data into useful well control information;
• Use of process controls to manage (automate) routine tasks;
• Display logic that facilitates effective collaboration; and
• Tools that assist and improve event-driven decision-making.
The package contains these components:
• An integrated, automated, fully transient wellbore hydraulics model that includes:
o Fluid hydraulics, taking into account temperature and pressure effects;
o Integrated solids transport and thermal models;
o Fluid compressibility; and
o Complete well geometry.
• An intuitive display showing the wellbore sketch, pressures and temperature along the wellbore and time charts with flexible variable display;
• On-rig data-processing capabilities, including:
o Selected data logging and data quality monitoring;
o Localized and remote display;
o Quick access to historical data;
o Real-time, instant forward simulation from current status; and
o Automated calculation of key parameters.
• High-resolution measurements of return flow and mud density through choke manifold using a Coriolis meter (i.e., during kill circulation);
• Surface pressure management provided by process-controlled, automated, electrically driven choke with:
o Ability to provide highly accurate control of standpipe, choke, kill line or BOP pressures;
o User friendly, flexible automated control logic.
Challenges in ultra-high-pressure wells

Below are specific well control challenges that are likely to be associated with ultra-high-pressure wells and how they can be addressed.
Narrow safe operating windows
Drilling contractor personnel must remain adequately informed and aware of downhole conditions to ensure early kick detection and response. SafeVision displays relevant downhole conditions throughout a well control event being managed using conventional well control resources (i.e., BOP), even when most advanced tools that may be in use for monitoring drilling operations may be out of service due to reduced pumping rates and location of sensors on flow paths.
High wellbore temperatures
Very high-pressure formations are also typically very hot formations. Reductions in downhole tool reliability – or possibly even usage – will increase dependence on real-time modeling when evaluating and monitoring downhole conditions. SafeVision models that fully and automatically integrates thermal effects with mechanical, geometric, rheological and hydraulic effects. This moves beyond using surface readings and measurements to manage increasingly complex downhole relationships.
Having the ability to quickly estimate thermal consequences of whatever well control method is used may provide an opportunity to help prevent downhole tool failure caused by extreme temperatures during an unnecessarily slow or prolonged well control event.
Fluid compressibility issues
Fluid compressibility, like temperature, may be largely ignored while drilling moderately deep and moderately warm formations. However, the combined effects of compressibility and temperature changes possible in extreme HPHT wells can create significant confusion and potential problems. The ability to automatically and simultaneously model both fluid compression and temperature effects makes it much easier to reliably manage critical downhole relationships (e.g., staying within drilling margins) by manipulation of surface pressure, mud density and displacement rates.
Continuous, real-time display of surface measurements – fluid density, choke pressure and surface temperatures – as well as corresponding but different downhole measurements – downhole mud density, pressure and temperature along the wellbore – helps users become much more aware of important downhole relationships. This opens the possibility of using well control procedures intended to keep wellbore pressures throughout the open-hole section within specified margins. Well control operations would not be limited through practices that ignore factors such as compression, temperature and hydraulic friction.
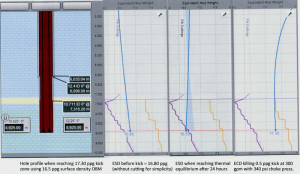
Mud rheology challenges
Extreme temperature and pressure conditions will likely challenge the industry’s ability to accurately predict and reliably control mud properties. Real-time modeling of affected pressures can provide an indication of unexpected fluid performance that could force wellbore pressure outside of necessary control limits.
The SafeVision hydraulics modeling software allows crews to observe well trends indicative of fluid system changes that need to be addressed – hopefully before such changes result in unacceptable downhole pressure excursions. Further, by using a hydraulics model during drilling operations that immediately precede a well control event, relative accuracy of the model can be assured just prior to its use during a subsequent, unexpected well control event.
Relatively high ECD effects in long, small-diameter hole sections
Very high formation pressures are generally encountered only in deep wells, which likely also include zones of significantly lower pressures. To ensure proper annular flow barriers, hole stability and kick tolerance, these wells often require many casing and/or liner strings. This can result in a relatively small-diameter but perhaps fairly long open hole in the extreme HPHT sections.
Along with high rheological values typical of very dense muds, this creates conditions for very high annulus friction, or ECD values, as well as significant possible gel effects. Through SafeVision, the effect of such ECD can be automatically monitored, including consequences of cuttings loads, thermal changes and wellbore pressure limits, particularly when transitioning between dynamic and static conditions.
Large wellbore fluid volumes, requiring long displacement times
The large fluid volumes contained in very deep wells have a substantial impact on crucial displacement measurements, such as deep cement plug displacement volume. Volume changes caused by temperature changes, which can impact kick detection practices, also increase in proportion to well volume.
Perhaps more important in practice is the fact that, in these wells, information obtained by circulating “bottoms up” comes at a much higher time and operational cost. This makes it nearly cost-prohibitive to depend heavily on surface evaluation of cuttings, fluids present, gas readings, etc, to understand downhole conditions. The ability of advanced modeling techniques together with downhole tools to reduce dependence on surface measurements is key to their ability to improve overall drilling efficiencies.

The SafeVision package does not stop working when a well is shut-in on a kick; data is continuously provided while the secondary well control system is being used to control wells containing surface pressures up to the full pressure rating of the rig’s well control equipment (e.g., the BOP, choke manifold, MGS, etc). This makes it possible to differentiate a real sustainable kick from a false kick (under controlled conditions with the BOP closed). It also allows for the use of dynamic processes to circulate suspected or real influx volumes to surface through the advanced, automated choke.
The system also makes it possible to quantify and take advantage of high circulation rate friction pressures, thereby widening the pressure window available during kill operations. It may even permit circulation rates sufficient to allow utilization of downhole tools, such as PWD or LWD instruments, to assist in assuring successful management of bottomhole pressures.
The ability of the system to facilitate instant, on-site forward simulations based on existing well conditions – including temperature, density, geometry and cuttings load transients – makes possible evaluation of non-standard well control practices before implementing them. This could improve safety and efficiency of well control operations.
When used properly in conjunction with teams of local and/or remote well control, operations and risk management resource personnel – all of whom have the same situation-critical information displayed the same way by the system at the same time – new well control approaches become possible.
Because even small increases in the circulation rate have large proportional effects on the time required for well control-related circulations, there is a surprisingly large benefit to using kill rates that would never be permissible without adequate real-time modeling, flow-out measurements and high-performance/reliability choke control. Current dependence on slow kill rates may be causing excessive NPT. Avoiding this dependence may help the industry to control the costs of drilling extreme HPHT wells. In other words, while efficiency must not take priority over operational safety, there is little point in pursuing targets with processes too inefficient to permit commercial success.
Fortunately, from a drilling well control perspective, managing a well with truly extreme pressures acting on surface equipment will almost surely depend mostly on containment during shut-in and subsequent high-pressure bullheading operations. It remains very unlikely that there will ever be a need for regular crews to use a rig’s standard well control equipment, such as its rig chokes, to dynamically control wells with truly extreme surface pressures. The focus of secondary well control procedures will and should remain on the planning, training and execution of procedures necessary to avoid preventable escalation of technically controllable situations.
Conclusion
While new, currently undreamed of tools and technologies could be developed, it is more likely that the ultra-high-pressure wells of the future will be drilled using many of today’s existing technologies. Commercially successful and safe development of extreme HPHT wells will require much better and more reliable use of current drilling technologies, including those devoted to proper management of unplanned well control events.
SafeVision is a trademark of Safekick.
This article is based on a presentation at the 2014 IADC International Deepwater Drilling Conference, 18-19 March, Rio de Janeiro.
Drilling Fluid Compressibility had always been an issue at HI Pressure HI Temperature drilling operations. Moreover dependencies on drilling parameters, soil geometry and fracture gradient being monitored on surface may not give crucial time slot in event of kick from unstable well, so there you go left with minimum options and hence this above 20K pressure gives that quick response option needed for well control.