MWD/LWD advances push telemetry rates higher, expand capabilities in horizontal, HPHT, deepwater environments
By Katie Mazerov, contributing editor

Drilling wells in today’s complex oilfields bears little resemblance to the drilling operations of just a few decades ago. Fast-evolving technology has turned drilling into a sophisticated and scientific undertaking driven by the need for real-time data. From unconventional plays, characterized by long, deviated laterals to complex deepwater and ultra-deepwater fields, data rules. Data can help boost recovery and gain higher rates of penetration (ROP), achieve greater drilling efficiencies, lower costs and reduce damage to downhole tools. To that end, an ongoing array of measuring-while-drilling (MWD) and logging-while-drilling (LWD) tools are helping the industry to measure and transmit critical information from downhole to surface – continuously and in real time.
Since their arrival on the scene in the 1970s, MWD technologies have gone far beyond their original applications of determining the direction and inclination of a well. These days, MWD tools, in concert with LWD systems, are often installed as part of the bottomhole assembly (BHA) to continuously measure borehole pressure, temperature and gamma radiation to characterize rock or sediment. The tools measure drilling mechanics, such as vibration and shock, torque and weight on bit, and evaluate formation density, porosity, pressure and resistivity to optimize well placement, keeping the bit in the sweet spot. Such measurements can be used to adjust critical drilling parameters that can lead to improvements in the drilling operation.
Pivotal in the development of this new-generation of MWD/LWD technology has been the shift from vertical to horizontal drilling in unconventional shale plays, where data is typically delivered either by mud-pulse telemetry that sends signals through the drilling fluid, or electromagnetic (EM) telemetry that sends radio wave signals through rock.
At the same time, improvements in deepwater MWD capabilities are being achieved with advances in mud-pulse telemetry, as well as the use of acoustic signals that travel through the drill string. The latter open doors to acquiring downhole data in water depths and fluid systems that can compromise traditional telemetry methods.
An acoustic solution

“Our acoustic telemetry technology and tool network design reduces risk and improves efficiency, particularly in deepwater applications where risk is elevated by complex well geometry,” explained Douglas Smith, director of business development for XACT Downhole Telemetry, majority-owned by Shell Technology Ventures Fund 1 and BP Ventures. The company’s telemetry technology is currently available in two forms. BoreSentry provides along-string, real-time MWD for pressure, temperature, compression, tension, torque and bending. SandSentry monitors downhole conditions during open-hole gravel pack/frac pack completions with a focus on pressure, temperature and weight on the service tool in the gravel pack packer, which allows operators to more effectively manage service tool position.
Acoustic telemetry provides a solution in deepwater operations that can be problematic for more conventional technologies. For example,water depths in those drilling environments challenge the effectiveness of EMT. And mud-pulse telemetry does not function where there is no fluid or where the fluid flow is insufficient to support pressure wave propagation, Mr Smith explained.
XACT’s acoustic telemetry network uses modulated compression waves generated by the tool; the signal travels through the steel of the drill string. It operates independent of fluid flow and is not restricted by high-resistivity formations, the company said. “It doesn’t matter what kind of rock we’re in, the type of mud, or even if there is mud,” Mr Smith said. “For example, if an operator is in an air, air mist, foam or nitrogen application, an acoustic system is really the best option for transmitting the data.
“The data rate for the network is similar to the higher-end mud-pulse systems,” he continued. “But with recent technology advances, we expect to double our transmission rates very soon. Early tests indicate that it can be improved far beyond that level.”
Acoustic telemetry traditionally has been limited to shallow depths due to signal reflections at drill pipe connections and the dampening effect from drill pipe contact with the wall of the borehole. The refinement of a reliable “repeater” system has allowed XACT to deploy the technology in deeper and higher-angle wells.
Inserted in the drill string at predetermined intervals based on the well profile, the repeater nodes boost the signal and transmit the data to the next repeater. This “daisy chain” approach continues until the signal reaches the surface, where an electronic acoustic receiver attached to the quill of the top drive transmits the signal wirelessly to a computer on location. Each repeater is also capable of making all the same measurements as the primary tool at the bottom of the hole and streaming that information simultaneously.
“With the repeater system, there is theoretically no limit to the depth we can take these acoustic telemetry tools,” Mr Smith said.
Expanding the frontier

The DigiScope service is designed for complex extended-reach drilling, deepwater and horizontal wells where slim-hole sizes require drilling efficiency and where transmission of downhole data can be problematic.
The need for increasing amounts of downhole data along with growing power needs of the BHA were the main drivers behind Schlumberger’s new DigiScope slim-hole MWD service. It expands the range of frequencies and physical bits per second (bps) available to transmit high-quality data for 5 ¾-in. to 6 ¾-in. hole sizes. It was also designed for complex extended-reach drilling (ERD), deepwater and horizontal wells where slim hole sizes require drilling efficiency and where transmission of downhole data can be problematic, according to Jimmy Varughese, MWD product champion.
“The frontier of drilling is continually being expanded, and with more ERD, deepwater and multilateral wells, we’re also seeing the complexity of LWD tools increasing,” he continued. “With existing MWD technology, there is often a gap in the amount of data that can actually be transmitted to the surface.” He notes that the new service can power more tools, allowing multiple LWD tools to be run in the same drill string.
The service also has a wider telemetry range, capable of delivering data at rates between 0.25 to 36 bps. When used with the Schlumberger Orion II data compression platform, the new MWD service has achieved 140 bps in real time, he said.

Mexican operator PEMEX incorporated the DigiScope service, along with a rotary steerable system, a hydraulically expandable reamer and the Schlumberger PeriScope bed boundary mapper, into the BHA to drill the 6 ½-in. section of a well in the Canterell Field. The section was drilled to total depth and then underreamed to open for expandable casing.
While drilling the 5 7/8-in. section using the same BHA, the well encountered heavy mud losses, a situation that often diminishes both the signal noise ratio and signal quality in delivering real-time data. As the new MWD service was already incorporated in the BHA, it was able to maintain the signal throughout the run without signal quality issues. The signal achieved a frequency of 12 hertz with a 1.5 bps physical bit rate, allowing the operator to reach well depth at 3,886 meters (12,750 ft).
In a horizontal well being developed by CACT Operators Group, a joint venture of Chevron, China National Offshore Oil Corp (CNOOC) and Agip Eni China, the DigiScope service was incorporated into a 6-in. lateral sidetrack to help geosteer the well through a thin layer (0.9 to 5 ft, or .3 to 1.5 meters) of sand. The service maintained 9 bps physical bit rate while drilling the 984-ft (300-meter) lateral with a signal strength of 21 psi at a pump pressure of 1,467 psi, enabling the delivery of resistivity measurements and images to place and steer the well.
The system set a record for high-speed data transmission in a 6-in. hole, with 18 bps physical bit rate reaming up the section. “By using this service, operators are now able to maintain higher ROP and increase drilling efficiency,” Mr Varughese said. “At the same time, it is now possible to obtain increased volume of quality real-time data to successfully drill to target depths faster and while geosteering the well.”
HPHT operation in China
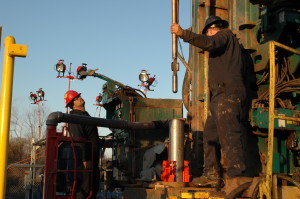
Another driver in the evolution of MWD/LWD technologies has been the industry’s move into harsher drilling environments characterized by high pressures, temperatures and vibration. Last year, APS Technology’s SureShot, an MWD system with rotary pulser, was used on a high-pressure, high-temperature (HPHT) well in China. The system enabled Sinopec Research Institute of Petroleum Engineering (SRIPE) to drill sections of a well in China’s Sichuan Basin with true vertical depth of 21,883 ft (6,670 meters), total depth of 24,869 ft (7,580 meters) and a 1,968-ft (600-meter) horizontal section. The MWD system performed in temperatures as high as 297°F (147°C) static and 280°F (138°C) circulating and pressures at more than 20,000 psi.
“The rotary design of the pulser makes it very tolerant of high levels of lost circulation material and therefore more reliable,” said Brian Stroehlein, marketing director for APS. “For HPHT applications, we have repackaged the system using materials for our pressure barrels and centralizers that are more corrosion-resistant in hydrogen sulfide (sour gas) and high-chloride (salt) environments.” The system is designed to work in temperatures up to 350°F and pressures up to 25,000 psi.
To develop SureShot, APS took a basic MWD system, including directional package, natural gamma detector, a pulser and a flow switch, and
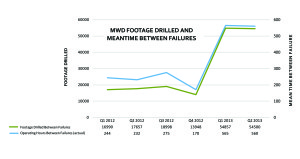
added pressure-while-drilling, propagation resistivity and weight, torque and bending on bit (WTB) sensor options. Optional vibration memory module software records and transmits vibration data either with a standalone MWD system or fed to the SureDrill system, a closed-loop drilling optimization service that provides real-time operating set points to maximize ROP and bit life under changing drilling conditions. So far, the system has been field-tested in six US land operations.
Vibration measurements include axial (up and down), lateral (sideways) and torsional or rotational, which identifies stick-slip. “Stick-slip indicates the interface between the bit and rock isn’t optimized,” he said. “We’ve found that by managing a couple of drilling parameters, primarily RPM and weight on bit, which can be controlled from the surface, drillers can simultaneously increase ROP and mitigate accumulated damage to the BHA.”
To geosteer horizontal wells, measuring resistivity downhole can be useful. APS’ wave propagation resistivity (WPR) tool uses radio waves to make such measurements. “Resistivity tells you whether you’re in dry rock, salt water or somewhere in between, which would be oil and gas,” Mr Stroehlein said. “If the resistivity measurement goes up, it may mean you are going out of the top of the reservoir, and you can correct it back down to stay in the sweet spot. Likewise, if the resistivity measurement lowers, it may mean the bit is moving toward the salt water, and you can adjust it back up.”
[flv flashvars=”file=https://drillingcontractor.org/wp-content/uploads/2013/07/video-aps.flv&&image=https://drillingcontractor.org/wp-content/uploads/2013/07/poster-aps.jpg”]https://drillingcontractor.org/wp-content/uploads/2013/07/video-aps.flv[/flv]Leveling the playing field

The boom in unconventional drilling has made shale plays a laboratory of sorts for testing and launching new MWD/LWD technologies. “In terms of MWD/LWD, unconventionals have leveled the playing field,” said Steve Krase, vice president, marketing and technology for Ryan Directional Services, a wholly owned subsidiary of Nabors Industries. “There is currently no measurement or group of measurements that can consistently tell an operator exactly where to fracture. All we can do is try to place the wellbore in the reservoir accurately, safely and efficiently.”
That mission, along with the trend toward drilling automation, has been significant in the development of AccuSteer, an MWD tool that does not require dedicated MWD personnel at the wellsite, with a surface system designed to enable remote monitoring and remote directional drilling.
“Most surface systems require excessive hardware and personnel to operate,” Mr Krase said. “AccuSteer, which can be run with both mud-pulse and EM telemetry, is delivered to the wellsite fully assembled and allows downhole mechanical measurements to tie into surface measurements, such as weight, torque and RPM. With this system, everything we’ve done is designed to be unmanned. The surface system allows anyone at the wellsite or the corporate office to have access to the data in real time.”
The system, which began field tests in June in South Texas and is expected to be fully commercialized in early 2014, was designed for long horizontal land wells where operators are increasingly trying to drill wells with one bit run, Mr Krase explained. “Our focus is on developing a tool that will enable operators to drill wells efficiently and put them in the right place using survey, geosteering and mechanical sensors for weight on bit and torque on bit.”

The design also features shorter assemblies as a way of reducing cost. Compared with conventional MWD assemblies, which can be as long as 120 ft, the entire AccuSteer length is 30 ft. He believes that most MWD assemblies used today were developed either for conventional onshore wells or for the offshore cost structure and that they may be too long and expensive for the unconventional market. “Length is money in terms of the high-grade, non-magnetic materials that are required for these systems, as well as the need for additional connections, which add cost and complexity and result in higher potential lost-in-hole costs.”
Most unconventional wells today are drilled using only gamma or resistivity measurement, he continued, and the addition of azimuthally sensitive measurements, such as azimuthal gamma, will enhance operators stay in the sweet spot.
Further, the company also is working on additional drilling measurements that can be beneficial for regions such as the Bakken, where shock and vibration can be problematic in the long lateral sections. “Having the additional mechanical measurements of torque, weight and other drilling dynamics measurements can help the driller ensure he is not in a high shock-and-vibration mode downhole,” he explained. “With this additional information, the driller has the opportunity to make changes from the surface to avoid potentially damaging the downhole
equipment.”
Challenges in the BAKKEN
The Bakken formation also was a testing ground for Scientific Drilling International’s (SDI) mud-pulse system. The high-speed FALCON MWD provides a telemetry mechanism to accommodate the company’s LWD tools, including gamma, propagation sensitivity tools and gamma with inclination to provide near-bit readings. The system, which can be deployed in formations where EM tools cannot function, supports a data rate of up to 5 bps, said Mark Norris, MWD technical product champion for SDI. “We chose the Bakken because it presents difficult challenges and serves as one of the harshest drilling environments in the US. The temperatures are elevated, we see a lot of axial and lateral vibration, and it has a stick-slip component that, in the long laterals, is very damaging to tools.”
In addition to producing higher bit rates, the tool can go deeper and longer. “If we’re running more logging tools, we can sustain higher ROPs for the driller while still getting the same data to the surface that we did at slower rates,” Mr Norris said. “This makes more economical sense for our customers.”

In the Bakken, operators using the new system have reduced drilling time from 20 days to an average of 8 to 10 days. The system also was tested in a pilot drilling program in Long Beach, Calif., in a sandy heavy oilfield where ROPs are high.
The MWD system was commercially launched in April; more than 250 units are in the field, and SDI plans to more than double that number by Q3 2013. “In the Niobrara Formation’s Denver-Julesburg Basin, the FALCON MWD system allowed an operator to receive gamma-ray data without limiting planned ROP. The system supplied an average of 1.2 data points per foot in the vertical hole section and more than two data points per foot in the build section, averaging between 55 to 400 ft/hr in the vertical section and up to 300 ft/hr in the build section.”
The system also uses an environment-based tool maintenance process called True Utilization Factor (TUF), which combines environmental measurements, such as temperature and vibration while drilling, to resolve fatigue-related issues. “This signifies a huge next step in our ability to provide preventative solutions to our customers,” Mr Norris said. “The technology records environmental operating conditions that it sees downhole. The objective is to ensure downhole certainty on our tools and mitigate any long-term fatigue related to normal drilling.”
To date, no failures have been reported with the system since deployment in Q1 2013, the company pointed out. Mr Norris also added that although the system is targeted for unconventional plays, it can also run offshore by adding or taking away LWD tools as needed.
Reducing shock effect
Shock and vibration have always presented challenges downhole, but the vibration levels encountered in today’s drilling operations can impact the reliability of MWD/LWD tools themselves. “The continual push to drill more quickly and drill deeper and longer laterals increases the occurrence of shock and vibration,” said Gregg Cune, business development manager for LORD Corp, a manufacturer of electronic vibration and motion control or dampening devices for downhole tools.
“For example, the Bakken, which features hard rock formations, is particularly brutal on downhole equipment, and MWD/LWD service providers want to protect their equipment from the harsh vibratory environment that comes with the use of agitators, EM telemetry and air drilling,” he said.
In response to the need for greater reliability and lifespan of MWD/LWD electronics in the unconventional market, LORD has enhanced its isolator technology to enhance protection against shock and vibration. “Our isolator reduces the amount of load transmitted to the sensitive portions of the MWD tools, specifically the electronics and battery packages, in turn allowing the tools to last longer or be used in harsher environments,” explained John Smid, oil and gas engineering manager for LORD.
He noted that the company is developing several devices to improve reliability and ultimately “expand the horizons of what is being used downhole.” These include micromount isolators for electronics packages, including wireline tractors, that have been tested and are being reconfigured to meet customer interfaces so as to fit as best as possible within existing designs. Users have reported seeing reliability rates on MWD tools increase from 80% to more than 90% using micromount isolators, Mr Smid said. The company also is developing an erosion-resistant isolator for lateral vibration and a torsional isolator designed to reduce stick-slip or “chatter.”
Another effort is focusing on reducing vibration transmission; the tool would be used with MWD tools in conjunction with a mud motor and would convert torque from the motor and apply it to the bit, Mr Cune said. “By applying more torque to the bit, we can gain a higher-efficiency transmission and reduce vibration and motion.”
BoreSentry and SandSentry are trademarked terms of XACT Downhole Telemetry.
DigiScope, Orion II, and PeriScope are marks of Schlumberger.
SureShot, SureDrill and WPR are trademarked terms of APS Technology.
TUF is a trademarked term of SDI.