Completing the shale puzzle

Fracturing, stimulation advances fuel production boom, reduce environmental impact; next-gen innovations focus on increasing overall, IP rates
By Katie Mazerov, contributing editor
It’s no secret that unconventional shale production is booming in North America, and the news keeps getting better as industry continues expanding into new oil and liquids-rich plays. So bullish is the outlook for shale oil, the International Energy Agency (IEA) has projected that the US will overtake Saudi Arabia as the world’s largest oil producer by 2020.
“When it comes to unconventional shale fracturing and completions, the US is the center of the universe,” said Rob Fulks, director of shale resource projects for Weatherford. “Not every country is blessed with these great expanses of shale that hold tremendous potential to meet global demand for increased oil and gas.”
Still, challenges remain. Recovery rates remain in the single digits, considerably lower than in conventional reservoirs. Wells also see steep decline rates after initial production (IP). This is driving operators and service companies to continue developing technologies to boost recovery and improve economics and efficiency while at the same time reduce the environmental footprint and comply with increasing regulations.
Whereas the drilling side of the business cracked the horizontal drilling code that made unconventional production possible, the completion side of the equation still has work to do beyond multistage fracturing. Over the past 10 to 12 years, industry has learned that the geologic variability of shale reservoirs means production is inconsistent and uneven. To that end, the focus is now on finding solutions to improve monitoring, better understand and connect to the reservoir, identify and target the sweet spots, enhance fracturing and stimulation and proppant distribution and even re-fracture to boost rates in older, nonproductive wells.

“Ultimately, improved recovery, both overall and IP rates, is what we’re looking for,” said John Paneitz, senior operations engineer for Whiting Petroleum, one of the largest operators in the Williston Basin’s Bakken and Three Forks plays, which is characterized by complicated geology and extended-reach laterals with measured well depths as long as 20,000 ft. “Overall recovery is low in shales because the reservoirs are generally poorer quality than conventional reservoirs, which have higher-quality rock that allows the hydrocarbons to flow much better. We’ve picked the low-hanging fruit; today there are more reservoirs that are poor quality, and we’ve gotten better at accessing them.”

Looking to capitalize on multistage completion technology, operators have increased the number of stages and fractures to access more rock. “We are now running 40 stages, shrinking the distance between each of those stages down to less than 300 ft,” Mr Paneitz said. But even that strategy has limits. “We saw significant results when we went from 10 to 20 stages and some improvement when we went from 20 to 30 stages,” he said. “But we’re starting to see diminishing returns on 40 stages because when we add more stages, we also increase the cost.”
Whiting has drilled nearly 500 wells in the Williston Basin, all with an open-hole design that uses swell packers for annular isolation. “We like open-hole technology because we can take advantage of the natural fractures,” Mr Paneitz said. In the vast majority of those wells, frac sleeve technology, as opposed to the conventional plug-and-perf method, is used for fracturing.
The sleeves, containing specially designed ball seats, are shifted open with frac balls to expose ports for fracturing. Advances in sleeve design have made the technology possible in wells with 30 or more stages. Using the open-hole packer and sleeve completion design, Whiting has seen both improved economics and a reduction in days on location, which translates to HSE benefits and lowered risk, he noted.

Looking ahead, Mr Paneitz believes fluids and fluid surfactants that improve recovery of oil from rock will be the next big breakthrough. Farther down the road is the idea of refracturing, which he says cannot be done with the same multistage design. “At this point, we would have to do a ‘Hail Mary’ operation and hope the fracture goes where we think it should.”
Four years ago, Whiting installed reclosable frac sleeves as a long-term experiment with the idea of refracturing the well or wellbore sections to reestablish production at a later date. The operation has not been carried out, primarily because the company is focused on new production. “When there is a well on every corner, which we’re quickly hitting, then we can go back and revisit older wells to refracture,” he said.
Eliminating bad wells
Among the ongoing challenges the industry is beginning to tackle is the inconsistent production resulting from the intense variability of unconventional plays. “The industry has done a fantastic job of improving the cost of these wells, which we can drill and complete very quickly,” said Kyel Hodenfield, vice president, unconventional resources for Schlumberger. For example, to reduce costs and improve efficiency in cemented plug-and-perf operations, the KickStart pressure-activated rupture disc valve is being installed as part of the casing string in the first stage, or toe, of many wells to allow for stimulation without the need for coiled tubing or other intervention.
While driving down costs is important, however, operators really want to improve the cost per unit of production. “That means eliminating bad wells by locating the sweet spots and then optimizing the completion,” Mr Hodenfield said, citing IHS data indicating that as many as 60% of the wells in a given play are uneconomic, due to the heterogeneity and variability of the reservoir.
“Operators are often surprised that what they thought was going to be a productive well actually is not.”
Schlumberger is integrating seismic technology with core and wireline logging data from vertical pilot wells to study the properties of the reservoir to identify the sweet spots, which is a combination of reservoir quality and completion quality parameters. “With this integrated reservoir-centric workflow approach, we’re measuring effective porosity, pore pressure, natural fractures, hydrocarbon saturation and whether the formation will be receptive to a fracture filled with proppant,” Mr Hodenfield explained. “Many reservoir sections do not have the proper composition, stress or texture that produces a viable fracturing system.”
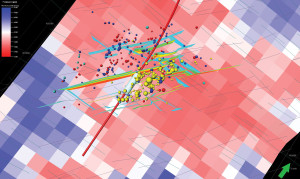
Due to the variability, the completion effectiveness also varies along the wellbore. “We have run production logs in hundreds of horizontal multistage wells and have identified inconsistent production, with more than 40% of the perforation clusters and 20% of the stages not contributing to production,” he continued.
To achieve more consistent results, the Mangrove reservoir-centric stimulation design software uses the integrated workflow approach to devise a seismic-to-simulation model that designs a complex fracture ahead of time by taking into account the reservoir geology and geomechanics and properties of the rock.
“We can’t assume these reservoirs are homogeneous,” he said. “Rather than place perforation clusters every 100 ft, which is the way many wells have been addressed, we have proven it is more productive to engineer the completion and vary the stage lengths based on the composition and fabric of the rock and then locate the perforation clusters where stresses are similar to achieve a simultaneous breakdown.”

Schlumberger’s HiWAY flow-channel hydraulic fracturing service increases production while significantly reducing water and proppant. Combining chemistry, fibers and a pumping schedule, proppant treatment is pulsed while the fibers are pumped continuously. The fiber keeps the proppant together in pillars, creates channels and then dissolves into fluid after the operation is completed.
The technology is being used in most plays on nearly a third of the company’s hydraulic fracturing jobs. In the Eagle Ford, wells using the technology showed a 32% production increase over wells completed with crosslinked gels after 90 days and a 37% increase after 250 days. Compared with slick water, production rates using this technology showed 67% and 87% increases after 90 days and 250 days, respectively.
“With HiWAY we reduce the amount of proppant by about 40% and eliminate up to 60% of the water. Over the past 18 months, the reduction of water and proppant has already eliminated over 40,000 transports to and from the well site,” Mr Hodenfield said. “We want to do more with less – less proppant and water, fewer people and trucks.”

Sustainable stimulation
While recovery, efficiency and economics are priorities for operators, reducing the environmental impact while improving sustainability of the stimulation process remains critical. Halliburton’s CleanSuite portfolio of production enhancement technologies for hydraulic fracturing and water treatment is a three-tiered approach to addressing that challenge, said Nicholas Gardiner, strategic business manager, production enhancement. The CleanStim fracturing fluid, 100% sourced from the food industry, reduces chemical exposure risk at and below the well site; the CleanStream service uses ultra-violet light instead of chemical biocides to control bacteria; the CleanWave system recycles water through electro-coagulation, minimizing waste and the use of chemicals.
While the shift from gas production to oil has not had a major impact on completion methods, it has resulted in a swing away from water-fracturing techniques to gel and crosslinked gel techniques. “The move to oil increases the requirement for a highly conductive fracture, and we’re seeing an emphasis on surfactant technologies and gels with less residue,” Mr Gardiner said.
Last year, Halliburton introduced PermStim, a robust fluid system to improve fracture connectivity using a derived natural polymer rather than guar.
Among other basins, the system was deployed in the Eagle Ford play, in a fracturing treatment in a 6,050-ft horizontal well section at 10,897-ft vertical depth with a bottomhole temperature of 280°F, where the operator saw a 20% increase in average initial production. It has since been used successfully in more than 100 wells, primarily in the Williston, Denver-Julesburg and Green River basins at temperatures up to 300°F bottom static temperature.
Another challenge in the low-permeability shale basins is proppant distribution. Halliburton’s AccessFrac suite of stimulation services improves proppant distribution in multizone completions and includes features designed for refracturing treatments, infinite conductivity and enhanced development of complex fracture networks. “This ensures operators that multiple perforated intervals can be fracture-stimulated at the same time, without inserting isolation plugs between intervals,” Mr Gardiner said.
Software technology relevant to improved recovery includes Halliburton’s new Knoesis service that interprets microseismic knowledge in real time and integrates that information into the fracture design during the fracturing operation. “This involves two disparate technologies talking to each other in real time – applying microseismic or monitoring technology into the pumping schedule while we can actually use it to optimize recovery,” said Ron Hyden, Halliburton’s technology director for production enhancement.
Looking ahead, industry will continue to push for incremental improvements in recovery rates, he believes. “The single-digit recovery rates have not been on the industry radar because we’ve been able to get by with them. But as operators recognize that low recovery rates are not acceptable, they are pushing to improve the economics. We need to look to the science community to determine what about shale rocks makes recovery so marginal, versus classic sandstone or carbonate formations.
“Shale has some unique characteristics that will make it necessary for us to make modifications in our chemistry and production methods,” he continued. “I anticipate that our laboratories will do more work in the development of geomechanics and technologies often referred to as digital rock, where we analyze the formation at a micro level to better understand the mechanics that drive fluid movement.”
Understanding the reservoir
Increasing connectivity with the payzone has been an important driver behind Baker Hughes’ latest generation of its FracPoint multistage fracturing technique for open holes. The latest design allows a single ball to open up to five sleeves per stage to direct fracturing treatment into the formation. Each FracPoint MP sleeve includes eight DirectConnect ports placed 45° around the circumference of the sleeve.
The system can be used as an alternative to the plug-and-perf method in up to 17 stages per well, eliminating the need for cementing the liner in place.
“The system was developed based on information we’ve received from reservoir analyses indicating that by controlling the initiation point of fractures in some wells and reservoirs, we can gain significant improvement in the productivity of the well,” said Ed Wood, product line manager for unconventional completions at Baker Hughes. “We start by understanding the reservoir, drilling the well in the right place, gathering data along the wellbore to identify the sweet spots and then placing the sleeves in the sweet spots so that when we fracture the well, we gain the best opportunity for the most recovery.”
The system allows as many as five sleeves to be opened with one IN-Tallic fracturing ball, which disintegrates over time, he explained. When the ball is dropped, it passes through the sleeves, with the first four sleeves subsiding into a recess to allow the ball to land in the final fixed sleeve. When the sleeves are opened, hydraulic pressure launches the DirectConnect telescoping ports into the formation with up to 15,000 lbs of force.
The impact of the ports into the formation changes the near-wellbore stresses and creates the path of least resistance in the formation, which helps control where the fracture initiates, Mr Wood continued. This allows the operator to directly influence where the fractures are, rather than the fracturing occurring at the naturally weak points in the formation.
These sleeves not only allow multiple initiation points per stage but also the accurate placement of the fracture treatment, ultimately giving better connectivity to the reservoir.
“When compared to cementing with plug-and-perf operations, this method can deliver significant time and cost savings for operators,” Mr Wood said. “Along with directly targeting the optimum places to fracture, we’re getting more sleeves and hundreds of connections to the reservoir with fewer balls, which have the added feature of disintegrating with time.” The system has so far been deployed successfully in North America, including Alaska. “We are evaluating those operations and looking at how this technology can be best used internationally,” he added.
Looking ahead, Mr Wood believes unconventional completions will continue to increase in North America and blossom in other areas globally.
“We believe that by using reservoir models that integrate log-derived, near-wellbore geomechanical and petrophysical properties from calibrated seismic data, operators can optimize well placement and completion design earlier in the reservoir life cycle for more efficient construction and improved recovery,” he said. “Technology combined with field experience will lead us into the new reservoirs.”

Cementable Solutions
NSC-Tripoint, which provides downhole completion tools and services for all the major US shale plays, has expanded its STIMPACT portfolio with a ball-dropped cementable frac sleeve (CFS) for multizone operations where cement is either preferred or required due to the type of formation.
The STIMPACT CFS replaces the conventional plug-and-perf method, the stimulation technique still used in 75% of unconventional, horizontal wells, explained Ryan Henderson, operations manager/business development – unconventional completion services for NSC-Tripoint. The system enables one point of entry for each zone; the ball is dropped from the surface, landing on the frac sleeve ball seat. The frac sleeve will then be manipulated by differential pressure, allowing proppant and pad, acid, slick water, N2, CO2 or the applicable stimulation option to enter the formation to begin the stimulation process.
“Customers needing cement for isolation to help pinpoint and project fracture placement can use this technology to increase their efficiency, reduce the amount of water required and reduce the amount of time they need horsepower on location, which is a huge part of the spread costs,” Mr Henderson said. “It also provides greater accuracy in targeting the sweet spots and effectively draining the formation.”
The technology was successfully used in the completion design of a well in the Marcellus play, deployed in the first five stages of a 14-stage hybrid system.
The company’s STIMMAX completion system for cemented and open-hole applications, commercialized in the last year, allows operators to open up to five valves per stage, with five different points of entry, all manipulated with one ball. The method effectively stimulates an entire horizontal wellbore, up to 20 stages, allowing for continuous fracturing and increasing recovery with fewer balls.
“This technology represents a big step forward for the industry by providing the machinery and advanced rubber for seals and O-rings to deliver an effective product that will successfully stimulate the formation, save time and cost, and provide more reliability and also provide limited entry, which is a preferred stimulation method,” Mr Henderson said.
Whereas a 20-stage operation using the conventional plug-and-perf method would likely require seven to 12 days to bring a well on production, both the STIMPACT CFS and STIMMAX systems can reduce that time to one to three days, Mr Henderson noted.
“We’re evolving to provide the technology and solutions our customers want, reducing service costs and helping operators gain a return on their investment in a third of the time.”

Eye on the ball
Weatherford’s ZoneSelect open-hole completion portfolio has been enhanced to include the new i-ball multizone frac sleeve that optimizes production, reduces operational costs and increases efficiency in shale wells. “Most of the efficiency and production improvements we’re looking for today are on the completions side,” said Eric Blanton, global product line director for Weatherford’s Lower Completions division.
The i-ball technology uses a one-size ball, rather than graduated ball sizes, to open an unlimited number of seats, which ultimately disappear. “This opens up new doors for customers needing 40 zones because the internal diameter doesn’t need to be reduced with each sleeve and because it eliminates the need to mill out the balls,” Mr Blanton said.
Initially designed for the Bakken market, the technology has been used successfully in a number of extended-reach wells in the play but can be deployed in both open hole and cemented wells, he noted. Weatherford plans to launch the sleeve in 5 ½-in cased wells and has also tested the system for 4 ½-in casing.

The ZoneSelect MASS frac sliding sleeve provides an alternative to plug-and-perf operations, particularly for cemented wells. The sleeve can be placed between isolation packers in multizone completions, or cement can be used for isolation. “This type of completion comes closest to mimicking a plug-and-perf application because when we drop one ball across the interval, it opens multiple sleeves and allows us to fracture across that interval through all the sleeves at the same time,” Mr Blanton explained.
“It is particularly beneficial when fracturing across multiple perforation clusters to create a transverse fracture.” The system is being used in the Eagle Ford play, where cased-hole completions are still the preferred method, as well as in the Marcellus region and Canada.
For operations requiring coiled tubing (CT) stimulation, the ZoneSelect CT system can open unlimited zones with isolation devices, also eliminating the need for milling. The technology, which monitors pressure along the CT string and facilitates real-time adjustments for each zone, is being used in the northern Bakken region in Canada and will be deployed for applications in the Eagle Ford play, Mr Blanton said.
But along with new technology, significant advances are likely to emerge from the ability of service companies to finally access long-term production logs that are providing important lessons for the industry moving forward. “Up until now, we’ve seen a fairly geometric pattern in these completions – same size stages with uniform distances between perforation clusters,” Mr Fulks said. “But, we’re learning that these operations aren’t nearly as efficient as they need to be because we didn’t take the time to place perforations at the most potentially productive intervals to begin with. Now, we’re starting to look outside the box by studying our logs and cuttings analyses and placing perforation clusters where they have the highest probability of success. We’re beginning to see significant improvement in overall performance simply by putting a little bit of science behind what we do.”
CleanSuite, CleanWave and PermStim are trademarked terms of Halliburton. CleanStim and CleanStream are registered terms of Halliburton. AccessFrac and Knoesis are service marked terms of Halliburton.
KickStart, Mangrove and HiWAY are marks of Schlumberger.
FracPoint, FracPoint MP, DirectConnect and IN-Tallic are trademarked terms of Baker Hughes.
STIMPACT, STIMPACT-CFS and STIMMAX are trademarked terms of NSC-Tripoint.
ZoneSelect and i-ball are registered terms of Weatherford.