Hydraulic tensioning takes variance out of BOP installations
Adapter system replaces hammer wrenches, torque tools to make uniform flange connections, improve safety
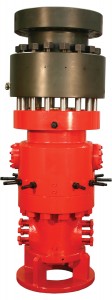
By Joanne Liou, editorial coordinator
In the oil industry, using hammer wrenches or torque tools to bolt the BOP to the wellhead is a tried-and-true method. However, using such conventional methods to make flange connections in the field, especially to BOP installations, can be prone to safety risks – pinch points for fingers and hands, swinging hammers, parts hanging over the head and flying debris. By taking advantage of hydraulics, Weatherford is working to eliminate the tools needed and reduce the number of personnel and the amount of time needed to make the connection with a hydraulic bolt-tensioning system. “We’re saving approximately four hours per installation, but more than that, we’re keeping people safe and reducing incidents,” Todd Travis, global business unit manager for Weatherford’s wellhead systems, said.
The Safety Tensioning Adapter (STA) system is attached to the bottom of a BOP and then stabbed on the casing head. The nuts are then hand tightened, and a hydraulic pump is used to apply pressure on the STA assembly to create a single force on the ring gasket to uniformly stretch the bolts. The only tools required are the hydraulic pump and a small crescent wrench to tighten the pump fitting.
The amount of fluid required for the pump is minimal – 14 oz – about the amount found in a soda can. “From a safety standpoint, if you were to develop a leak or the hose were to break, it would essentially squirt and return to zero pressure,” Mr Travis said.
The conventional method to make connections leaves room for variances. “When you’re torquing nuts, you’re putting tension in the stud. As you turn a nut, you pull on the stud, and the threads rub against each other,” Mr Travis explained. “How well the nuts are lubricated will determine how much torque is required to get the tension that you want through the stud.” However, a person could apply varying amounts of lubricant on each stud and nut, thus affecting the amount of tension in each nut even when the same torque is applied. “There may be as much as 40% difference in tension from stud to stud because of various amounts of lubricant on one stud or nut and less on others,” he added.
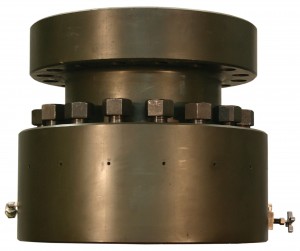
Using pressure, the STA system can stretch the studs to a more precise tension and bolts the flanges together in a uniform pattern. “This system pulls down all bolts at one time, perfectly flat,” Mr Travis explained. With the traditional method, the BOP stack is manually bolted to the wellhead following a star pattern “until, as the API specifies, that nut does not move anymore. When you apply the star pattern to bolt, you pull down one side, then you pull down another side, so you rock on the gasket,” Mr Travis said. Essentially, the rocking can scar the seal and/or seal areas.
With the STA system, one person can complete the BOP connection in about five minutes, while the same task could take up to six hours using hammer wrenches, Mr Travis stated. The system also significantly reduces the amount of time workers spend in the cellar underneath the BOP. Eliminating the use of hammer wrenches further enhances safety by reducing the risk of hand, back and eye injuries, he added.
Before the STA system was commercially launched in January, Weatherford
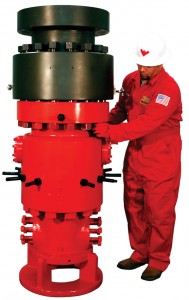
completed three field trials in the US. Each lasted 90 days without incidents, leakages or reliability issues, according to the company. In early 2011, the first trial was completed in the Fayetteville Shale in Arkansas with Southwest Energy. The second field trial was completed with Talisman in the Marcellus, followed by a third in Alaska with ConocoPhillips. The system is suitable for a range of environments and has been tested in temperatures ranging from -50°F to 250°F in all pressure conditions.
Laboratory tests were used to verify the accuracy of the tension. A strain gauge was placed on a stud to determine the exact force of the pull. “We measured the actual strain to verify engineering calculations and determine the stretch on the stud,” Mr Travis explained. Furthermore, a measurement beam was shot through the stud before and after tensioning. The stud, when fully tensioned to API standards, was .009 longer than when it does not have tension on it, he explained.
The removal process can also be completed in three to five minutes. “If our input pressure is 10,000 psi, the way to undo the system is to increase pressure to 10,100 psi, which will stretch the stud a small amount more than before,” Mr Travis said. “The nuts will then be loose.”
Weatherford has delivered about 40 units so far, mostly in North America, and has 40 more units on order from markets such as Mexico, Colombia and Argentina. The system, which can be manufactured and used with any API flange size, has been geared toward land-based applications, but Weatherford plans to apply it on offshore BOPs starting in Q1/Q2 2013. Other applications, such as workovers and fracturing stacks, are expected to follow in Q2 2013.