Reentry campaign gives first-round subsea fields second chance to produce
Redrilling wells to extend field life requires detailed analyses of present and prior operations
By Sean Stright, Nelson Tears, Gregory King, ExxonMobil Development Company; Vikas Srivastava, David W. Smith, ExxonMobil Upstream Research Company
A large number of subsea production wells have been drilled, but to date, there has been limited industry experience of redrilling subsea wells even though redrills have become routine in platform and surface wellhead applications. The focus of this article is to highlight the key aspects of redrilling a subsea production well to extend field life.
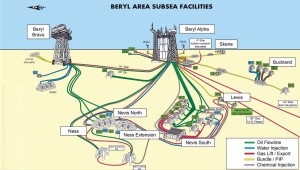
The article will describe how the unique challenges of redrilling three subsea wells were overcome in old and declining fields where the original wells were designed and drilled with limited consideration for redevelopment of the fields through reuse of existing wells. The article will define the problems of and describe the solutions to:
• The mooring and blowout preventer (BOP) handling constraints in the crowded subsea infrastructure of a subsea field development;
• The riser and wellhead analysis for redrilling a well through a subsea tree and the operational practices required to maintain tree and wellbore integrity;
• The analysis of the additional loads put on a subsea well through the extended period of riser and BOP loading; and
• The casing exit and redrill constraints unique to operations from a semisubmersible; casing recovery operations, the management of window milling debris in a subsea BOP system.
There has been limited industry experience of subsea production well redrills, and significant lessons learned will be shared. They will be of wider application as the number of subsea wells increase along with the requirement to maximize recovery and extend field life.
Background
The operator’s affiliate in the UK North Sea, Mobil North Sea, is the operator for the Beryl, Ness, Nevis, Buckland and Skene fields, which constitutes the Beryl field. Other co-venturers in the development include Centrica, Hess, Shell and OMV. The field is approximately 200 miles northeast of Aberdeen.
Production from the Beryl field started from the Beryl Alpha platform in 1976, and the Beryl Bravo platform started production in 1984. Subsea developments include Ness, Nevis North and Nevis South, where wells are tied back to the Beryl Alpha platform and date back as far back as 1996. Three newer subsea fields were developed starting in 2001, including Buckland, Skene and Lewis 1, which is an extension of the Nevis South Development. The water depth is approximately 360 ft (Figure 1).
In 2007, the North Sea Beryl Drilling Campaign was temporarily suspended to reevaluate the drill-well inventory. In 2010, a semisubmersible was contracted for a five-well redevelopment campaign, which consisted of two workover operations and three abandonment and sidetracks. The operations involved reentry of wells having horizontal spool trees and vertical trees. All drilling operations required reuse of the existing wellhead, slot recoveries requiring cut and pull of casing, and whipstock sidetracks.
Mooring and Heavy Lift Considerations
The mooring design for any location is subject to many factors, which change over the life of a field. All mooring design loads are defined by the metocean conditions defined for a given area. In the North Sea, the metocean criteria used as a design basis for mooring designs have evolved, resulting in more conservative environmental criteria at locations such as the Beryl field.
This is not necessarily due to actual worsening weather conditions. Rather, the quality and accuracy of metocean data, hindcasting methods and the numerical models used to develop the design criteria have all improved. Further, the assessments have become site-specific to fields within the North Sea, and the databases continue to grow with new data.
As a result, the metocean data quality and analysis has improved, and the mooring designs will be affected. For the Beryl field, this has resulted in current mooring designs being assessed using more stringent metocean criteria than used for prior campaigns.
An expanding footprint of subsea infrastructure creates a further challenge to maintain sufficient vertical clearance of mooring lines from the subsea infrastructure. For an older field, where new wells may not have been drilled in a long time, routing of subsea flowlines, equipment replacement and general field maintenance may cause the footprint of the subsea infrastructure to grow.
In the absence of an active drilling campaign, the ability of a mobile offshore drilling unit (MODU) to position over the modified infrastructure and maintain adequate clearances to the infrastructure may not have been fully evaluated.
For mooring lines that span over subsea infrastructure, it is common to establish a minimum tension requirement to maintain the required vertical clearance. However, with more stringent metocean criteria as the assessment basis, along with a growing subsea infrastructure footprint, specifying a high minimum tension to protect flowlines may not result in appropriate mooring analysis results. A mitigation that can be employed is use of subsea buoyancy of the mooring lines to provide sufficient vertical clearance.
While subsea buoyancy provides a solution to the vertical clearance issue, the addition of mooring hardware in the mooring line creates another potential issue. Loss of subsea buoyancy in conjunction with a mooring line failure creates further failure scenarios that should be considered.
For the Beryl North Sea mooring design, the following general approach was applied:
• The design standard for vertical clearance required by API RP2SK requires a minimum of 10 meters vertical clearance from all subsea infrastructure. The local production affiliate, after extensive review and risk assessment, required 20 meters vertical clearance to protect their infrastructure, so this clearance criteria was used for the campaign. Although API RP2SK provides explicit design criteria, it also states, “to determine clearance criteria, many factors should be considered, such as environment, water depth, and risk of injury, asset and environmental damage, etc. Conservative criteria should be established based on these considerations (API 2005).” Thus, the clearance criteria used by the North Sea team was consistent with this expectation.
• Subsea buoyancy (buoy) was added to mooring lines where a minimum tension in excess of 100 kips was required to ensure adequate vertical clearance from subsea infrastructure. Based on mooring analysis in worst-case metocean conditions, it was determined that it was not feasible to maintain line tension in excess of 100 kips in all environmental conditions.
• Minimum tension specifications for a location were determined assuming that no mooring lines have subsea buoyancy. This is a conservative assumption to ensure the buoyancy is not completely relied upon to protect infrastructure and a loss of subsea buoyancy alone does not result in a mooring line clashing with infrastructure. However, in the event of metocean conditions where the minimum line tensions cannot be maintained on the leeward lines, the infrastructure is still protected by the buoyed mooring line. It was not possible to design for mooring line tensions below the minimum tension specifications concurrent with complete loss of buoyancy.
• Multiple smaller buoys were used instead of one large buoy per mooring line. Loss of a single smaller buoy would not result in complete loss of vertical clearance to the subsea infrastructure.
• Buoys were periodically inspected with vessels and a remotely operated vehicle (ROV) to confirm buoy location and to confirm the mooring hardware was not unacceptably worn or damaged.
Throughout drilling operations, the primary hazard to the integrity of the production flowlines and gas lift lines within the immediate area of the wells being drilled was the potential for dropped objects – either through the moon pool or over side crane work. Strictly applied, previously established operating procedures governed the movement of any MODU lift over water.
The MODU was in continuous contact with the Beryl Alpha platform, allowing all subsea lines to be shut-in immediately prior to any heavy lift. Emergency shutdown (ESD) could be initiated if required via an open communication link between the MODU and the Beryl platform control room during dropped-object exposure periods. There was also a provision for backup communication links and clear instructions to shut down operations should the communication links be lost during deployment/recovery of the heavy lift. The platform control room operator also had clear instructions to initiate a field ESD on instruction from the MODU.
Furthermore, designated heavy lift handling areas were assessed for each location. Vertical clearances of mooring lines to subsea assets were assessed in the mooring analysis for these rig positions, and as often, minimum vertical clearances are observed while at the heavy lift standby location.
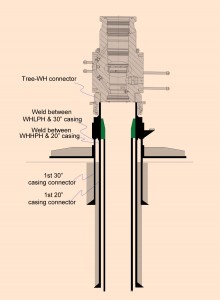
Wellhead Connector and Weld Fatigue Assessment Methodology
Offshore drilling and workover operations impose fatigue in the subsea wellhead and casing system when the system experiences cyclic stresses induced by the motions of the MODU and riser. In shallow water, a shorter riser makes the fatigue load transmission to the wellhead and casing more severe; therefore, shallow-water operations under harsh environments, such as those in North Sea sites, generate more severe fatigue than operations in deeper waters under mild environments.
Over the well life, fatigue accumulates in the system from the riser-connected operations. The accumulation can lead to a fatigue crack, which could propagate and lead to loss of integrity of the component. The interactions between the floating vessel, riser, wellhead stack (lower marine riser package), BOP, tree, and low- and high-pressure housings), casings and soils are modeled to evaluate the fatigue at fatigue-critical locations, both above and below the mudline.
Examples of fatigue-critical locations (hot spots) are:
• Connector between the subsea tree and the wellhead;
• Weld at the bottom of the low-pressure housing connecting to the structural casing (typically 36- or 30- in. outer diameter, OD);
• Weld at the bottom of the high-pressure housing connecting to the surface casing (typically 22- or 20-in. OD) or wellhead extension joint;
• Structural casing connectors and connector welds in the first one or two joints of structural casing; and
• Surface casing connectors and connector welds in the first one or two joints of surface casing.
The fatigue assessment methodology applied to analyze the fatigue life of the subsea trees, wellheads and casing connectors and welds is discussed below.
Vessel Motion Analysis
First, a dynamic stationkeeping analysis is conducted to obtain the resulting motions of the vessel’s center of gravity as it is acted upon by the wind, wave and current environment. Vessel motions are dependent on vessel characteristics and whether the vessel is moored or dynamically positioned. In either case, the vessel heading with respect to the wave direction is defined, and its wave motion response amplitude operators (RAOs) are calculated for use in stationkeeping and riser analysis.
For the riser analysis and well system fatigue analysis, the calculated vessel wave motion RAOs are translated to the top of the riser.
Riser Analysis
A global riser analysis includes the vessel motions, actions of waves and currents, tensioning system, slip joints, riser joints, and wellhead stack; structural and inner casing strings below the mudline and soils is then performed. Depending on the mud weight and environmental conditions, minimum riser tension analysis is performed to determine required slip joint tensions and corresponding static and dynamic global loads (moment, axial and shear forces) along the riser system.
In the global riser analysis, tubulars and other components are modeled using beam elements of equivalent weight and stiffness with non-linear spring constraints along the structural casing to model the mechanical behavior of the soils. Static P-Y curves are used to model the soil behavior for the strength analysis, and cyclic P-Y curves are used to model the soil behavior for the fatigue analysis.
Although the global riser analysis may be carried out either in the frequency or time domains, the frequency domain analysis is preferred for ease and efficiency. In the frequency domain approach, it is assumed that the wave frequency response can be represented by a narrow-banded Gaussian process with Rayleigh distributed peaks. The resultant loads are obtained from this global riser analysis and include:
• Mean bending moment, tension and shear loads;
• Root mean square (RMS) shear and RMS bending moment (standard deviation); and
• Zero crossing periods (Tz) of the shear load and bending moment.
Wellhead and Casing System Analysis
A wellhead and casing system analysis is performed to determine the response of the wellhead stack and casing system to the loads imposed by the riser, which were obtained from the global riser analysis. All components in the wellhead and casing system are modeled as concentric pipe-in-pipe (PIP) elements in a finite element package with appropriate geometric and material properties. The soil and casing interaction is modeled with non-linear spring elements using site-specific cyclic P-Y curves for the soil.
The analysis simulates the casing and wellhead installation and cementing sequence to capture the locked-in stress state in the system, followed by the internal and hydraulic pressurization. This is followed by applying the fatigue loads obtained from the global riser analysis at the top of the PIP model for each sea state.
For each sea state, component sectional force and bending moment ranges are obtained at the cross-sections containing the hot spots (reference cross-sections). Following this, nominal or reference stress ranges for the fatigue-critical sections are calculated for each sea state by using the corresponding cross-section geometric properties. The section properties used to calculate the reference stress and stress ranges must be consistent with those used in calculating the stress concentration factor (SCF) for the hot spot.
SCF analysis
Stress concentrations exist at geometric transitions and misalignments of well system components, welds and casing connectors. The SCFs are calculated using detailed finite element analysis for fatigue-critical locations assuming isotropic linear elastic material properties. The SCF at a given location is defined as the slope of the maximum local stress as a function of reference/nominal stress applied at the reference section. The reference stress ranges are then transformed to the local hot spot stress ranges using the following relation:
Hot Spot Stress (Range) = SCF * Reference Stress (Range)
The hot spot reference stress ranges for each sea state (weather bin), and its annual probability of occurrence are critical inputs to the subsequent fatigue analysis.
Fatigue Damage Assessment
To evaluate fatigue resistance, the material fatigue capacity is defined in terms of S-N curves. Component testing can provide fatigue resistance data, and this approach is
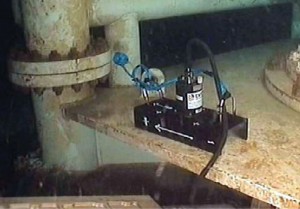
widely used for welded components. For large machined components, testing is typically not pursued for practical and economic reasons. Instead, the strain model can be used based on data generated with small-scale tensile specimens that characterize the monotonic and cyclic properties of the parent material. The S-N curve is defined as:
log N = log A – m* log Δσ
Where:
N = number of cycles to failure
A = S-N curve constant
m = negative inverse slope of S-N curve
Δσ = applied stress range
When a frequency domain approach is used to obtain the dynamic response of the riser at a given reference section, the fatigue damage can be expressed in a close form.
Conservatively, bending moment and shear are assumed to be in phase and the shorter Tz from either the bending moment or shear is used to calculate the number of cycles for estimating the fatigue damage. The fatigue assessment is based on the cumulative damage model (Miner’s rule), which is equally applicable to welded and mechanical connectors, provided their corresponding fatigue resistances are properly characterized. In this model, fatigue damage at a location from various sea states or sequential drilling and workover operations (riser connected days) are additive.
The methodology can be applied to two levels of fatigue assessment: fatigue screening and detailed fatigue analysis.
Fatigue Screening Analysis
The fatigue screening analysis is intended for obtaining quick estimation of the fatigue performance of the wellhead and casing system using simplified and conservative assumptions. The analysis assumes that an assumed environment (e.g., the 95% non-exceedance environment) occurs 100% of the time, and fatigue damage accumulates at one point on the circumference of a component. If the estimated fatigue life meets design requirements, the fatigue assessment is considered complete and detailed fatigue analysis is not required.
Detailed Fatigue Analysis
The detailed analysis is more rigorous with more realistic assumptions than the screening level analysis. The detailed analysis considers seasonal and directional variation in metocean criteria. Site-specific seasonal and directional fatigue weather bins with associated probabilities of occurrence are developed. The fatigue damage is calculated at discrete locations around the circumference of a component for each of the seasonal and directional weather bins.
The cumulative fatigue damage at each circumferential location is then calculated by summing the product of the unweighted damage at that location with the probability of occurrence of each weather bin for which the riser is connected. That is in the detailed fatigue analysis, the reference stress range, zero crossing period, the probability of occurrence of each of the fatigue weather bins, the riser connected days in each season, and the riser disconnect criteria are all used to calculate the cumulative fatigue damage at a number of circumferential location for each of the fatigue critical areas.
Furthermore, the rate at which fatigue damage accumulates at each of the critical locations depending on the season of operations may be calculated.
Crack Propagation Life for Machined Connectors
Welded components usually have inherent flaws left from the fusion process. Therefore, the predicted fatigue life is predominantly related to propagation of these flaws. On the other hand, in machined components, most of the fatigue life is related to initiating a crack since the parent material generally contains only structurally insignificant flaws. For a machined component, such as a tree connector or casing connector, overall fatigue life corresponding to a through thickness crack can be higher than that calculated using the parent material S-N curve, if the S-N curve corresponds to the initiation of a stable crack (Figure 2).
In this case, additional life for crack propagation to an unstable size can be calculated using a fracture mechanics approach.
Limitations of Fatigue Analysis
For a reentry campaign, the analysis must consider both anticipated fatigue damage for the proposed work and the fatigue damage accumulated from prior campaigns. There is usually no opportunity to perform physical testing on the materials and welding procedures used for the original installation. Therefore, conservative assumptions may need to be made related to the specifications of the parent material and welds in the absence of the physical testing to verify the S-N curve characteristics.
When high fatigue loading is anticipated, a preloaded wellhead system can minimize the fatigue effects on the wellhead and surface casing by rigidly locking the high-pressure housing to the low-pressure housing. Some conventional wellhead systems are not preloaded, and the required tensile load to lock the high-pressure housing to the low-pressure housing is passively applied by the weight of the surface casing string.
The location of the top of the surface casing cement can also impact the fatigue assessment results. If the top of cement is not well documented, a conservative assumption for the location of the top of cement should be used in the fatigue assessment.
For a reentry campaign, preloading the wellhead or remedial cementing are not feasible options. Thus, the type of system wellhead installed and details of the surface cement job (cement volume and ROV observations during the job) are important considerations in the overall assessment.
In a risk assessment for a reentry or workover operation, failure is usually defined as a loss of containment or structural collapse of the well system. In practice, the fatigue analysis does not provide a quantifiable relationship between the calculated fatigue safety factor and the probability of loss of containment or structural failure of the component.
The S-N curves used to evaluate fatigue resistance are associated with different definitions of failure (crack initiation for parent material and through thickness crack for welds) that are not directly related to loss of containment or structural failure. Additionally, the S-N curves used are typically the “mean minus two standard deviation” curve, based on regression analysis of test data.
In BS 7608, “Fatigue design and assessment of steel structures,” it is suggested that a normal distribution may be assumed in calculating the probability of failure associated with a particular value of fatigue safety factor. However, BS 7608 does not provide a basis for the use of the recommended normal distribution assumption.
The engineering analysis also needs to be balanced with proven industry experience. The planned riser connected days for all wells in the North Sea Beryl campaign were within the North Sea experience envelope for the respective wellhead systems. This was also considered when evaluating the risk potential of each reentry.
Subsea Slot Recovery
Slot recovery operations from floating rigs presents several unique challenges over land or fixed platform operations. Performing precise casing-cutting operations from a heaving rig can cause damage to either the wellhead or the bottomhole assemblies being used. The subsea wellhead must be reused, and extensive effort is required to ensure protection of the wellhead and all seal areas.
Subsea well reentries involve recovery of items that are very close to the full bore of the BOP, including subsea test tree assemblies, casing hangers and seal assemblies. Some assemblies may have been designed for the original installation, and recovery or reuse of these components many years after initial installation may not have been considered in the engineering design. Furthermore, casing recovery will inherently cause metal debris to be introduced into the wellbore, which may introduce risk of damage to BOP or wellhead seal areas. These considerations are discussed in further detail below.
Wellhead Preservation/Seal Recovery
In the North Sea, the combined effect of high seas and shallow water depth (360 ft) makes vertical motion control of the drill string especially challenging. A typical passive heave compensator (common in older-generation rigs) will provide sufficient heave compensation while drilling (i.e., while “down weight” is being applied to the drill string). However, a drill string that is suspended above a wellhead will not be compensated. This can be problematic when pulling and setting seal assemblies or performing any work at the wellhead or BOP. Attempting to work in excessive sea states could result in permanent damage of the wellbore. Defining maximum sea states and rig heave is a critical consideration for each operation.
Seal assemblies vary in design but generally are designed to serve three functions: provide a primary pressure barrier in the casing hanger annulus and lock to the casing hanger and the wellhead. Locking mechanisms vary in type, and the issues outlined in this article are not associated with every wellhead system.
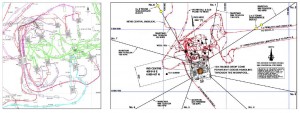
Some older-style wellhead systems have locking mechanisms for which recovery of the seal assembly years after installation was not envisaged. A locking ring expands in a profile beyond the nominal inner diameter (ID) of the wellhead to provide a path for the required reactive force between the hanger and seal assembly. The lock ring (when engaged) is larger than the fullbore ID of both the wellhead and BOP. To pass through the BOP upon recovery, the lock ring must retract to its original shape.
For wells in the Beryl North Sea campaign, recovery of seal assemblies involves pulling seal assemblies 15 years after initial installation and after exposure to high temperatures and production loads. The ring does not retain any of its original properties and likely cannot be pulled back through the same bore ID that it could on the original installation.
Leaving the lock ring in the wellhead introduces a risk of damage to internal seal areas when recovering casing hangers and will prevent access to set bore protectors and seal assemblies. Conventional fishing tools are not designed to recover lock rings while inside the wellhead.
If the lock ring cannot be recovered by conventional means, an extensive evaluation and risk assessment of the well barriers needs to be made before unlatching the BOP connector and recovering the lock ring with an ROV. Recovery of a lock ring with an ROV may not be avoidable and should be considered as a high-probability scenario before starting any subsea reentry campaign.
Risk mitigation is well-specific, and no generic rules can be followed to state when it is safe to remove the BOP. Additional barriers may be required before this can safely be done.
Casing Recovery
Recovery of casing by cutting and pulling is a proven method of performing a slot recovery. When cutting casing from a MODU, the rig motion must not be transmitted to the casing-cutter assembly. Excessive cutter motion will cause damage to the cutter and prevent a sufficient quality cut to be made to recover the casing.
Utilizing a marine swivel (landed off at the wellhead) is a simple and commonly used method to prevent rig motion from being transmitted down the drill string. The marine swivel is normally landed off on a casing hanger. When problems are encountered retrieving casing, the casing string may be cut in smaller sections to maximize the tension applied at the cut point. When this is done, the casing hanger that was normally used to support the marine swivel may have been removed from the wellbore.
In the absence of a marine swivel, it will be necessary to use a cut-and-pull spear, where a grapple is engaged inside the casing stub, and tension is applied to the top of the casing stub, preventing transmission of rig motion of the casing cutter. When this situation was encountered in the North Sea campaign, a conventional mud motor was placed between the grapple and the casing cutter to cut the casing.
For subsea slot recovery work, it is highly likely that multiple cut-and-pull runs will be required. Jarring is generally limited as extensive jarring could cause damage to the subsea wellhead. The preference is to cut into smaller sections and recover the casing with minimal force.
Furthermore, heavier and stronger drill strings that provide high overpull capacity are generally not shearable with conventional blind shear rams. When recovering casing in smaller sections, the minimum casing cut length will be determined by the length between the grapple and the casing cutter.
Whipstock Sidetracks
Whipstock sidetracks have routinely been used to establish a sidetrack from a wellbore for subsequent drilling operations. The primary difference between a whipstock deployment for a subsea well compared with a surface or fixed platform is the motion of the drill string.
Prior to running the whipstock, a drift assembly simulating the length, stiffness and configuration of the whipstock assembly is run to verify the whipstock is capable of being run to the planned depth. A significant difference between the whipstock and drift assembly is the shear bolt attaching the whipstock to the milling assembly. Rig motion, especially when the drill string is in slips, can cause cyclic loading on the shear bolt. This effect will not be fully evaluated by the drift assembly. Consideration must be made for acceptable environmental conditions for running the whipstock; otherwise, the whipstock may be lost in the wellbore.
If a hydraulic anchor is being used, the surge/swab pressure introduced by rig motion may also interfere with the setting procedure.
Single-trip whipstock assemblies, which allow both running the whipstock and milling a window with a single assembly, may be the quickest method of establishing a sidetrack. However, relative to a multiple-trip system, these assemblies are generally longer and stiffer because of the additional casing mills in the assembly.
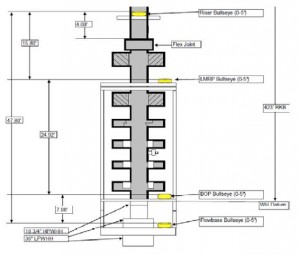
Consideration should be made for localized doglegs at the wellhead area when determining which system should be used. Factors include wellhead inclination, taper of casing cross overs below the wellhead and changes in geometry through the BOP and wellhead. Furthermore, the differential angle between the flex joint and wellhead should be minimized and closely monitored while running the whipstock through the BOP and wellhead. Prior to running the whipstock, the rig may need to be repositioned to achieve the lowest flex joint differential angle.
Milling of a window that will enable passage of all drilling assemblies requires precise control of weight on bit (WOB). Generally, low and consistent WOB is required to mill casing windows. In conditions where high rig heave is being encountered, a passive heave compensator may not be capable of providing the required WOB control.
As with running whipstocks, environmental limitations should be considered for milling operations. Excessive WOB can result in an excessive dogleg, making the window unusable.
Metal swarf created by casing milling is likely to accumulate at the BOP area due to the larger ID of the BOP and riser, and in the cavities in the BOP area capable of capturing debris. A riser boost line can enhance hole cleaning, but the boost line is commonly above the BOP and would not sufficiently boost the flow rate across the BOP. A combination of fullbore jetting assemblies with magnets and junk baskets below the jet sub can remove the excess metal debris.
If the jet sub is larger than the internal diameter of the wellhead profile below, a drill pipe hang-off tool designed for the wellhead profile can be run below the jet sub to prevent risk of damage to the jet sub and wellhead.
Lessons Learned
The Beryl North Sea campaign was successfully completed in 2011. All of the concepts outlined here were factored into the well designs and operations for all three wells drilled in this campaign. The geological objective of each reentry was achieved. Key lessons learned and observations throughout the campaign included:
• All mooring patterns were designed for the stringent vertical clearance requirements jointly set by the drilling team and the production affiliate and were subject to extensive risk assessment. Use of subsea buoyancy was effective to ensure adequate vertical clearance to protect infrastructure at all times. Extensive simultaneous operations procedures were also strictly followed for all heavy lift operations;
• A detailed wellhead fatigue analysis was completed for the locations. Primary attention was for wells with horizontal trees, as the detailed analysis showed that the connector between the tree and wellhead had the shortest predicted fatigue life. The horizontal spool trees have an inherent elevated exposure to fatigue.
Both the abandonment and subsequent completion operations must be performed with the tree connected.
The only opportunity to reduce the fatigue damage was to remove the tree for sidetrack drilling operations. The scope of work in this campaign involved predominately abandonment and completion activity so the potential to reduce the fatigue damage to the subsea tree was minimal;
• The translation of rig motion to the riser, BOP and wellhead was monitored through use of an ROV-deployed digital inclinometer. The inclinometer is capable of monitoring any minute movement with a high degree of accuracy (+/- 0.05°). Conventional bull’s-eye readings can be subjective and cannot be used accurately to quantify dynamic changes in inclination (Figure 3);
• A whipstock was lost in hole while running an extended-length ramp whipstock on a single-trip assembly. The combination of a 1.5° wellhead inclination, a steeply tapered 10 3/4 in. x 9 5/8-in. cross-over directly below the casing hanger and a moderate rig heave contributed to the unplanned shear of the whipstock shear bolt. The whipstock was being run very slowly, and at no time could excessive down weight be observed on any rig weight indicator.
The whipstock was fished from the well on the first attempt using a custom-designed box tap that was shipped with the whipstock on load-out. For the subsequent run and for all subsequent work with whipstocks, a two-trip assembly was used. This reduced the length and effective stiffness of the assembly. No further problems were encountered deploying whipstocks;
• Outer lock rings on all casing seal assemblies were not recoverable by conventional methods. Prior to pulling the seal assemblies, a drift assembly was run to confirm fullbore drift through the riser and BOP. An annular preventer was then closed, and the BOP was drifted again after 15 min to verify the preventer was fully open. The seal assembly was then retrieved with the same annular closed to assess trapped pressure in the annulus.
After confirming the well was static, the annular preventer was opened and left to relax for one hour prior to pulling the seal assembly through it.
Despite all risk-mitigation measures, the outer lock rings could not be recovered, as they did not return to their original shape – the OD of expanded lock ring was larger than the minimum ID of the BOP. This outcome was anticipated based on an engineering review of the wellhead system, and the appropriate risk assessments were performed during the well-planning phase for this outcome. These procedures were followed to verify the well barriers, unlatch the BOP and recover the lock rings with an ROV;
• Use of drill pipe-conveyed cameras were effectively used to evaluate the condition of the wellheads. Although the lack of drill string compensation resulted in poor video quality, sufficient still photos could be taken to effectively evaluate the condition of the wellhead and assess the condition of seal assembly lock rings when lost in hole; and
• After all casing-cutting and whipstock milling operations, the 18 3/4-in. BOP bore was jetted using a 16-in. OD jet sub with a pocketed string magnet that captured debris within pockets on the tool itself. A “junk basket” was used at the bottom of the assembly to catch any debris that fell below the magnets. Between each well, the BOPs were thoroughly stripped down and inspected due to the potential for damage caused by the metal debris.
No swarf was observed at the BOP upon recovery to surface, and there was no wear or damage to the BOP, confirming the jetting was effective.
Despite extensive up-front planning, a subsea well reentry will always have higher potential for nonproductive time and equipment issues than a new well. However, the reentry can always be performed just as safely. Problems encountered may not be the result of current operations but could be inherited from prior operations (drilling or production).
The keys to success for a reentry program are to develop a realistic well plan that does not rely on a “success-based” outcome for each well operation and that provides relevant well data at each operational step to help make informed decisions on forward plans.
The well plan also needs to give clear operating limits for when to continue and when to cease operations. Reentries involve reuse, refurbishment and preservation of a certain component of the original wellbore. If that component is compromised, either from previous or current well operations, the most economic decision may be to cease the operation.
Effective preservation of the original wellbore components can safely extend the service life of the entire operating asset.
This article is based on IADC/SPE 151202, “Regeneration of First-Generation Subsea Fields: The Challenges of New Wells in Old Infrastructure,” presented at the 2012 IADC/SPE Drilling Conference and Exhibition, San Diego, Calif., 6–8 March 2012.
Acknowledgements
The authors thank ExxonMobil Development Company and ExxonMobil Upstream Research Company for allowing the publication of this paper together with co-venturers Shell Exploration & Production, Centrica Energy Upstream, Hess Limited, and OMV Exploration & Production.
Exxon Mobil Corporation has numerous subsidiaries, many with names that include ExxonMobil, Exxon, Esso and Mobil. For convenience and simplicity in this paper, the parent company and its subsidiaries may be referenced separately or collectively as “ExxonMobil.” Abbreviated references describing global or regional operational organizations and global or regional business lines are also sometimes used for convenience and simplicity. Nothing in this paper is intended to override the corporate separateness of these separate legal entities.
References
API Recommended Practice 2SK, “Design and Analysis of Stationkeeping Systems for Floating Structures,” Third Edition, October 2005, Addendum May 2008.
British Standard 7608. 1993. Code for Practice for Fatigue Design and Assessment of Steel Structures.
Buitrago, J., Krishnan, V. R., and Sommerfield, P. M., “Fatigue Assessment of Subsea Tree Connectors and Wellheads,” OMAE 2011 – 49853, Proceedings of the ASME 2011 30th International Conference on Ocean, Offshore and Arctic Engineering, June 2011.
King, Gregory W. September 1990. Drilling Engineering for Subsea Development Wells. Journal of Petroleum Technology, Volume 42, Number 9.
King, Gregory W. 1995. The Instrumentation of the Conductor of a Subsea Well in the North Sea to Measure the Installed Conditions and Behaviour Under Load. Presented at the SPE Drilling and Completions Conference in December.
UK Health and Safety Executive (HSE). 1997. Overview of the Work Carried Out During the North European Storm Study; the Hindcasting of North Sea Metocean Parameters. Presented the Offshore Technology Report – OTO 97 051, July.