Repsol discovers one of Campos’ thickest hydrocarbons columns to date
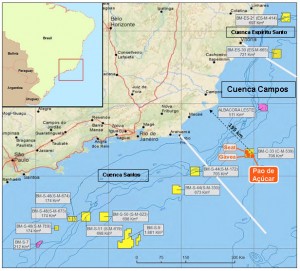
Repsol Sinopec Brasil recently made a new oil discovery in the Campos Basin offshore Brazil. The well, called Pão de Açúcar, found two accumulations of hydrocarbons with a total thickness of 500 meters (1,640 ft), one of the thickest discovered in Brazil to date.
The well is located in block BM-C-33, in a water depth of 2,800 meters (9,186 ft), and first appraisals indicate high-quality oil resources with excellent flow rates. Production tests in a partial section of the pay zone (approximately 200 meters) showed a flow of 5,000 bbl/day of light oil and 28.5 million standard cu ft/day (807,348 cu meters/day) of gas in a choked drill stem test with very limited drawdown.
Repsol is the operator and holds 35% of the discovering consortium and is partnered by Statoil and Petrobras , which hold 35% and 30% respectively. The companies plan additional work in the prospect to confirm the extent of the discovery. The Pão de Açúcar well is the third discovery in BM-C-33 block after Seat and Gávea.