Driller engagement, feedback essential in human-centered approach to automation design
As long as humans are in the loop, automation and digital solutions must consider human performance to reduce risks of complacency
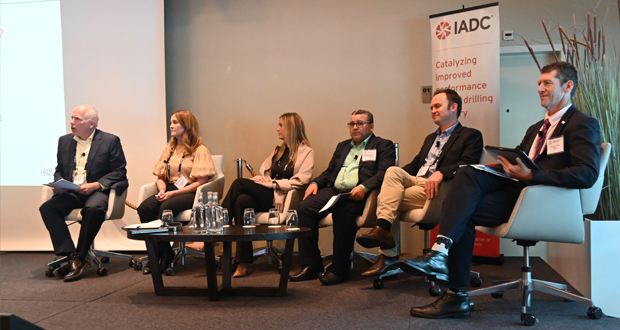
By Jessica Whiteside, Contributor
Automation is transforming the role of the driller. A driller who used to manually adjust drill bit rotation and fluid flow may now be focused on monitoring the progress of automated downhole processes across multiple screens while also keeping an eye on what’s happening on the rig floor. As automation becomes more prevalent, are companies setting their human operators up for success in this new world – or creating the conditions for costly and potentially hazardous process failures?
Advice from a panel at the 2023 IADC Advanced Rig Technology Conference was clear: To tip the scales in favor of success, companies should involve drillers early in the automation development process. In other words, don’t put the end user at the end, said panelist Kristian Solheim Teigen, Principal Engineer, IACS, Digitalization and Cybersecurity, for the Norwegian Petroleum Safety Authority.
Speaking at the conference in Amsterdam on 15 September, Mr Teigen noted that the International Regulators’ Forum is challenging the industry to develop digital solutions that take a human-centered design approach, with the goal of reducing risks from the use of automated systems.
Ironically, while automation is often introduced to reduce human error, its use can trigger new vulnerabilities, such as complacency in the human operator. There’s always a human somewhere in the loop, so automation must be designed for optimal human performance, Mr Teigen said. “You can only train people so much. It needs to work intuitively, as well.”
While the ideal automated system would be user-friendly for drillers across various levels of experience, the current reality of drilling automation is different. Challenges include user interface/user experience designs that fail to reflect drillers’ needs or workflows, ergonomic challenges and way too many screens.
Promoting app portability
A significant challenge for automation is application portability – the ability for an application to be installed, used and supported easily in different host environments. Operators want a variety of options for rig-agnostic automation or analytics. Yet, without portability, the result can be a doghouse overrun with screens where every new third party on a rig means the addition of a new screen.
That’s a problem because engaging with multiple screens simultaneously can pose a safety risk and impair attention and memory over the long term, said Grace Fosdick, Operations Manager, Drilling Optimization Technologies, for Nabors Industries. To boost portability and reduce the proliferation of screens, Nabors has installed a third-party programmable logic controller to allow non-Nabors applications to run on its operating system. The company has also collaborated with other companies to co-develop or port applications to the Nabors operating system. One recent initiative saw Nabors give Corva safe access to its rig controls to enable automatic input of setpoint values.
Mrs Fosdick suggested that, in order for such collaborations to succeed, the parties must find a unified purpose, agree on how to measure success and, depending on the nature of the collaboration, determine contractually how costs will be handled, such as a revenue-sharing model if appropriate.
“We have to let go of the mindset of ‘my equipment, I’m going to build everything that’s on it, I’m going to own all of the applications,’ because realistically that’s not what our customers want.”
Mobilizing field expertise
The rollout of a new automation solution with insufficient field consultation can leave drillers with a new job for which they don’t necessarily feel prepared to do. As companies mature in their automation journeys, they need to consider how well they are really listening to drillers’ perspectives, Mrs Fosdick said.
She recommended deploying effective listening strategies such as probing (asking questions to understand the root causes behind the feedback); paraphrasing (relaying back to the driller what you think you have heard from them); and summarizing (codifying the feedback systematically when you bring it back to the product development team). One of the chief complaints she’s heard from drillers is that nothing happens with their feedback, so it’s important to circle back with them afterwards.
“Maybe something did happen but that was just not communicated back to them. That’s very demotivating in this feedback loop,” she said. “It’s important that the drillers know what we’re doing with their feedback so that they’re motivated to continue participating in this process.”
For an initiative to redesign the driller’s HMI and workflow to limit engagement with multiple screens, Nabors commissioned a consulting firm to live at the rigsite and shadow the drillers to understand their workflows. The resulting recommendations included improving the hierarchy of information on screens so drillers see priority items first; using colors that reflect the kinds of alarms received; adding visual cues to acknowledge engagement on interactive screens; and consolidating screens.
The importance of putting the end user first was reinforced when developers were establishing naming conventions for automation tools, Mrs Fosdick said. The initial terminology purely described the function of the automation, which did not reflect the slang more commonly used in the field. After a training team of former drillers collected feedback from a diverse group of drillers, some of the HMI terminology was changed to reflect more common language used.
“That’s a very simple fix for us that doesn’t require an extensive development load, but it made a big difference to the field team,” Mrs Fosdick said.
Developing driller-centric designs
Ann Jorid Haugland, Director Software for HMH, outlined six steps her company employs to support user-driven innovation: understand the needs, map the processes, visualize and design, test, pilot and maintain the solution. This last step is critical because, even after an automation solution is introduced, work will be needed to ensure the continued integrity.
“We’ve seen a lot of HMIs that start out with good intentions, and then 10 years later they’re cluttered,” she said. “We need the ownership internally to make sure that we keep the guidelines and the principle intact.”
To gain understanding of user needs, HMH sends designers out to the rigs to get to know the users, processes and pain points, such as information siloed across different screens and systems or stored on paper or whiteboards without being shared. The team then maps the processes that need to be automated or improved.
“We ask, what can we simplify? Are there any redundant steps here? What can be automated?”
The content that appears on a screen should be needs-based, she said. “It shouldn’t be there unless you use it. It is very process-focused. So, based on which process you’re in, you should have the information you need but not more than that.”
Testing is a vital part of the process, including verifying content and flow and launching usability testing in a simulated environment. During the pilot phase, coaches will observe what works and what doesn’t to support continuous improvement. “We can’t create perfect solutions at once. It will take too long, and it will cost too much,” Ms Haugland said. “So, we start simple, and then we build to create more and more value, step by step.”
Considering training early on
How training will be delivered and how competency will be measured should be considered early in a project.
“Potential lack of competency, especially given the high level of turnover in the drilling industry, is something that needs to be identified in the development phases rather than in the deployment stages,” Mrs Fosdick said. Risks can arise from a potential loss of skills among drillers used to being on the joystick but now in roles requiring them to monitor automated systems. Even an experienced driller can fall prey to automation complacency, becoming so habituated to the automation that they lose their situational awareness or otherwise fail to notice a problem that actually requires human intervention.
Automation can be configured to address such risks by incorporating tactics that keep the driller informed about what’s happening even though they don’t manually carry out the process themselves anymore. Transparency is key, Ms Haugland said. The system could indicate how far along they are in a process, for example, or require confirmation that they are ready to continue with the next step.
Individuals who have been using advanced automation systems for a while sometimes report losing their “feel” for what is happening on the rig, Mr Teigen said. To help drillers maintain a mental model of the mechanics of what is happening in the well and driving the automation, “we might need to do more training on the fly, meaning that the (equipment) operator is challenged on the way that his skill is maintained, like they do in the aviation industry,” he said. “There’s hardly any pilot that lands a plane anymore, but they do it a lot of times in simulators.”
In a university setting, students respond well to learning in a simulator environment, said Dr Salaheldin Elkatatny, Professor, Department of Petroleum Engineering, King Fahd University of Petroleum and Minerals (KFUPM). However, an important question is whether simulators used for crisis management training need to be updated to reflect the automated environments individuals may encounter on today’s rigs, he said.
Dr Elkatatny also called for a more multidisciplinary approach for training the new generation. At KFUPM, engineering undergraduates can now pursue a minor concentration in artificial intelligence, machine learning or data analytics. He also recommended that rig automation be incorporated into the curriculum.
“The university can support lifelong training initiatives for the operators,” he said. “We should have a strong collaboration.” DC