Closed-loop underbalanced coiled-tubing drilling changes sidetrack drilling landscape
By enabling automated, real-time solids measurements, dual cyclone desander allows continuous solids separation and flow from well
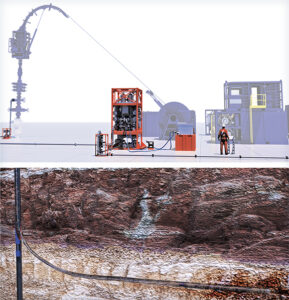
By Olof Nilsson and Aksel Skåland, FourPhase
In today’s energy landscape, operators constantly seek solutions that enhance efficiency, minimize environmental impact and maximize well productivity. One such breakthrough is the use of underbalanced coiled-tubing drilling (UBCTD) in combination with closed-loop solids handling systems for sidetrack drilling operations. As sidetracking becomes an increasingly preferred method to access new reservoir zones, understanding the advantages of a closed-loop system in CTD could be the difference between moderate success and optimal well performance.
CT has been the go-to solution for many of the in-well intervention operations that are normally conducted, both onshore and offshore. It is a versatile tool that can be utilized where a full-scale drilling rig is not required, for operations such as clean-outs, sidetrack drilling, milling, stimulation operations, completion, well logging and diagnostics, perforations, and plug and abandonment (P&A). Common reasons to consider CT include:
- Potential to work with surface pressure: It eliminates the need to “kill” the well, enabling operations under live or underbalanced conditions.
- Minimized formation damage: It avoids the introduction of kill fluids that could impair the formation, thereby maintaining optimal reservoir properties.
- Enhanced HSE: This is achieved through fewer personnel on-site, reduced need for heavy lifting and simplified logistics compared with what is required by a full-sized drilling rig.
- Cost savings: With the reduced labor and equipment needs, CT operations can be more cost-effective than using a traditional drilling rig, particularly for well interventions or smaller drilling projects.
Conventional drilling uses a higher hydrostatic pressure than the reservoir pressure (overbalance). Conversely, if the reservoir pressure is higher than the hydrostatic pressure, it is called underbalance. Underbalanced coiled-tubing milling and drilling operations provide both benefits and challenges compared with conventional drilling.
The utilization of UBCTD presents operators with an opportunity to extract substantial additional value from established reserves and to target multiple reservoir zones in a single trip, enabling the maximization of returns from depleting fields. This is not just a feature but an operational advantage backed by field cases. Research and case studies have shown that UBCTD is efficient in drilling sidetracks. It is associated with reduced formation damage compared with conventional overbalanced methods, making it a validated approach for increased well productivity.
Further, UBCTD allows for the preservation of the natural permeability of the reservoir. This is backed by comparative studies showing increased hydrocarbon recovery rates under underbalanced conditions.
Moreover, CT operations with a dual vessel cyclonic desander enables operation without emissions reaching the atmosphere. This is made possible by creating a closed-loop system using two cyclonic vessels. One cyclonic vessel can continuously produce while any pressure in the other vessel is bled off before solids are emptied. This ensures continuous solids separation and flow from the well and aligns with environmental regulations.
Applying a closed-loop system has proven successful and beneficial for operators to increase the versatility of their CT operations, as treated seawater, chemicals, nitrogen and base oil or similar can be used during operations. Substances are kept within the system, thus reducing personnel and environment exposure to potentially hazardous substances.
The closed-loop system can be used with both traditional and CT setups. A DualFlow desander system is connected to the flow-tee on the CT riser stack. Typically, a surface safety valve (SSV) is installed upstream from the desander to allow for a quick shutdown. By connecting the desander to the cutting skip with level measurements, the system can be fully enclosed at all times. This ensures no hazardous substances are released into the atmosphere. With a conventional operation, the return is produced to a shaker, and there is risk of operators being exposed to H2S, Benzene and NORM (Naturally Occurring Radioactive Materials).
The ability to design a closed-loop system with a cyclonic desander lies within its automation. The system conducts real-time measurements of the solids separated. By continuously monitoring the weight/volume of separated solids, decisions can be based on operational facts rather than estimates. Additional benefits include:
Interpretation of the solids data alongside the estimated solids calculations provides valuable data to boost the efficiency and quality of CT operations.
Real-time decision making: As the CT operation runs, the solids are tagged, and the cleanout starts. If an expected weight of solids is known, the operation plan can be changed instantly if the volume of solids removed does not match expected results. Steps can then be taken, such as increasing the pumping rate or pulling further out of the hole.
Preventing issues associated with CT getting stuck: CT getting stuck in the well could lead to several scenarios, including loss of operational time, risk of the tool being released in the well where it will need to be fished out or, in the worst case, a shut-in well.
Confidence to operate at optimal speeds: Operators want to run CT as fast as possible. If the data shows that the solids are coming up, operators will have the confidence to proceed at the optimal rate. Using live data in correlation with estimated data can assure and optimize the quality of the CT cleanout. Decisions can be made on the go as the live data is observed. As soon as the data and trends show a clean wellbore, coil can efficiently move to the next step/bite. This can be done with the knowledge that all solids behind the coil tool string are cleaned all the way out of the well.
Ensure a proper cleanout: By analyzing the data in real time, it is possible to verify that the solids are being cleaned out in a scheduled and consistent manner. This means that the closed-loop sand management system topside can handle the solids in an optimum and efficient manner, which translates into economic efficiencies and reduces nonproductive time (NPT). Compact solids plugs can affect separation efficiency. If this happens, all the accumulated sand will be moved out as one compact huge sand plug. This will put pressure on the sand management system, and its efficiency may be reduced. This could lead to sand reaching the process facility.
North Sea case study
To ensure higher production from a field on the Norwegian Continental Shelf, a CT campaign was conducted to clean out stimulated wells over the course of three years. The campaign included eight wells and several stimulated zones. The CT clean-
out was planned to use a mix of nitrogen and base oil to create a lighter fluid column and, therefore, less stress on the reservoir. To avoid any exposure to hazardous substances, including the nitrogen mix, a closed-loop system was necessary. With limited deck space available due to the CT spread onboard, a compact solution for separating the return was sought. In addition, the customer wanted the system to ensure solids-free flow post stimulation.
A FourPhase solids management system was installed together with the CT spread. The system varied slightly from operation to operation but typically included a choke, DualFlow, SSV, Super Duplex pipe, multiphase flowmeter, and a control container to enable remote monitoring.
The setup was prepared to enable the coil operation to flow their return to the shaker. When hydrocarbons were detected, it was rerouted through the closed-loop solids management system. This ensured no hydrocarbons, NORM, H2S or Benzene were produced to the platform deck and kept the offshore operators safe. The base oil used by CT team was sent through the process system topside.
Utilizing real-time solids measurement in combination with the multiphase flow meter provided the operator with imminent flowback data of the four phases (oil, gas, water and sand) flow, confirming the well production rates.
With the solids management capable of handling 5,000 psi, the same system could be utilized for the post-stimulation flow as was used for the CT operation. This eliminated time typically spent on planning and rigging, as well as HSE risks associated with the manual change of equipment. In turn, this enabled the operator to rapidly achieve optimal production during the initial flow back of the well.
Over the course of three years, nine wells were successfully cleaned out with a closed-loop solids management system. There was no exposure of harmful substances to offshore operators or the environment. Total operational hours amounted to 6,365 hr. Of that total, <0.01% or 5 hr was categorized as NPT. With more than 200,000 lb of solids separated, this was considered a success.
The automated solids management system ensured no manual handling was conducted. As one supplier and the same equipment managed solids for both the CT and the post-stimulation flow, planning and operational HAZOPS minimized cost and time spent. DC