Well intervention tools: Pushing back time for aging wells
The Boots & Coots Pulsonix TFA. Material is used with permission from Halliburton.
The Baker Hughes Mastiff. Material is used with permission from Baker Hughes.
Technology advances address water influx, wellbore buildup, seek innovative methods to cut pipe, set cement plugs
By Katherine Scott, editorial coordinator
As fields mature around the world, innovations in well intervention services have become increasingly important as operators work to slow or even reverse declining production rates. Economics is often a driving factor, but cost should never be evaluated in isolation. Products should be looked at by considering both time and cost benefits, Doug Bolingbroke, technical adviser – worldwide drilling for Apache, said. How quickly equipment can be mobilized, as well as going dayrates for a drilling rig versus a well intervention vessel, are key factors to consider.
Operators also must be willing to try new technologies, weighing the potential benefits of innovation against the economics. Providing service companies the chance to field-test a piece of equipment gives operators themselves opportunities to benefit from cutting-edge technology. “When we’re talking with service companies and defining what we want, there’s always a view that we want field-proven equipment, but it’s impossible to have new technology that’s been proven. Someone has to come first,” Mr Bolingbroke said.
Walking the talk, Apache is planning to use a lightweight intervention riser system to permanently abandon wells that allows cement plugs to be set using coiled tubing, whereas a riserless system would be restricted to using wireline. Additionally, the system can be deployed from an intervention vessel, which can be more cost-efficient than using a semisubmersible.
“There is also a significant time saving,” Mr Bolingbroke said, by not having to run an 18 ¾-in. BOP stack, a 21-in. marine riser, or a work string or landing string with a subsea test tree. “This riser system saves all these operations and allows the well work to start much sooner.”
The industry is “right on the cusp of more of this type of equipment,” Mr Bolingbroke said. “As subsea intervention techniques become more reliable and people get more confident with them, there will be more enthusiasm to use them.”
One challenge, however, is that intervention technologies developed for one area may not be suitable for another. For example, the North Sea has many subsea wells that require intervention, whereas the subsea wells needing attention in the Gulf of Mexico are fewer in number but located in deeper waters. “A technique that’s developed in the North Sea is not really applicable or can’t be used in the Gulf of Mexico,” Mr Bolingbroke explained.
Earlier this year, Apache acquired the Beryl Field in the North Sea from ExxonMobil, increasing the company’s needs for intervention innovations that can help to revitalize mature subsea wells. Such needs across the industry are driving service companies to build advanced systems that increase reliability and can mobilize quickly, sometimes through a rigless approach or through one-trip well stimulation.
In any operation, the aim is always to gain better understanding of the well to enable successful interventions on the first try, said Kelly Hebert, manager of the thru tubing tool service line for Boots & Coots. “The more you understand the well, the better it produces and the less well intervention will be required later.”
Weatherford
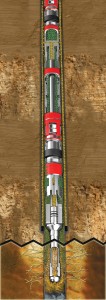
Weatherford has introduced the WidePak retrofit gas lift (RGL) system, which can restore production in gas wells suffering from water influx, or oil wells experiencing production decline. “The tool extends the reach of lift gas deeper into the well, below the production packer, and directly down to the perforations and production zones,” Jake Bramwell, global technical specialist for Weatherford’s Thru Tubing Business Unit, said. “In doing so, it improves the well’s hydraulic efficiency, enabling the lifting of fluids, therefore allowing stranded mobile oil and gas in the reservoirs to produce on their own.”
In spring 2010, the RGL saw its first pilot installation in a well for a major North Sea operator. The gas well had not produced in more than two years due to liquid loading issues. “It allowed the operator to do a fairly economical intervention and get good production results without having to perform a costly workover to remediate the water influx issues,” Mr Bramwell said.
The pilot deployment of the system “was the first time anything like this had been attempted in the North Sea, or globally, that we know of,” Mr Bramwell said. A 5 ½-in. RGL pilot system was installed in the nonproductive well to allow access for lift gas to the lowest perforation, approximately 800 ft below the production packer. After successful application of the RGL, production resumed at a sustained rate of 6 mmscfd. The pilot project took 17 days and over 6,000 manhours to execute, leading to four additional North Sea installations in the same field.
Weatherford notes that the RGL has been V0 certified, an IS0 14310 validation grade for packers and bridge plugs confirming the tool exhibits zero gas leaks in use. “Testing packer equipment to a V0 grade is a very time-intensive process, pushing the tool to its mechanical failure limits and requiring multiple differential pressure reversals, temperature swings and often a third-party witness to certify results,” Mr Bramwell said.
The aim is to provide confidence in reliability. “If (a tool) can pass this validation test, then the design is good to go. It’s not going to see anything worse in a field application,” he continued. The packer system has been tested through a temperature swing from 40°F to 325°F and a maximum differential pressure of 5,000 psi in a gas environment.
“The RGL system is a way to breathe life into old wells that are seeing that decline in production without having to abandon them or do a major workover to try to squeeze the last life out of the well,” Mr Bramwell said.
This fall, Weatherford will begin a four-well RGL installation program offshore for a major operator in Alaska’s Cook Inlet.
Boots & Coots
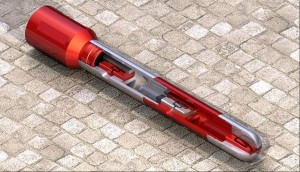
Besides water intake, reduced production rates can also stem from debris build-up. Boots & Coots has developed the Pulsonix Tuned Frequency and Amplitude (TFA) tool, an enhanced fluidic oscillator that removes built-up deposits. When used with coiled tubing or jointed pipe, it enables real-time placement of fluids that treat the area near the wellbore, according to the company.
The tool, now on its third generation, has two ports – active and inactive. Pumped fluid exits the active port while the inactive port additionally takes in fluid, switching back and forth to generate pulses. A change in the third-generation’s oscillator pattern encourages stronger pulses at the formation and less leakage from the opposing port, Robert Howard, global advisor for downhole coiled tubing with Boots & Coots, said.
“What we’re doing downhole is generating pulses to help break up damage, such as perforating debris or built-up scale that is choking back production,” he described. In conventional tools, acid is pumped down the well, which can force the debris deeper into the formation instead of removing it, he explained. With the Pulsonix TFA, “as we make passes up and down the wellbore, this pulsing allows the damage to be flushed out and removed from the wellbore so it’s not pushed back in there to come back and cause problems later.”
In old wells in particular, the tool can help to remove collected particles that have become obstructions. “For the mature field, it’s better to remove this damage and try to bring on the production,” Mr Howard said.
The tool can be used on land and offshore in new and old, vertical and horizontal wells. “There’s no temperature limit; there’s no pressure limit,” Mr Howard said.
In 2010, the tool was tested alongside a rotating-jet nozzle in thick, Oligocene Sespe sandstone in California. Four onshore wells were drilled vertically and completed with uncemented 7-in. pre-slotted casing. Results were based on surface-injection rate and pressure over a period of 400 days; 200 days of data recorded before the stimulation and 200 days of data recorded after the stimulation until the injection rate and pressure returned to pre-stimulation levels. The wells treated with the TFA nozzle showed an improvement in cumulative injection volumes and immediate post-stimulation rates, the company found. The operating company attributed this to the tool’s cyclic-pressure pulses. Additionally, tool reliability was noted due to the lack of moving parts.
The Pulsonix TFA is undergoing commercialization as well as additional field trials in countries such as Nigeria, Mexico, Egypt and Germany, Mr Howard said. “What this tool is about is essentially making it easier for a well to flow by cleaning up damaged areas,” he said. “The better we clean, the more production we get out of the well.”
Welltec
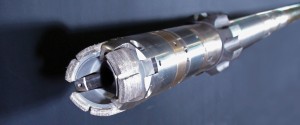
A growing trend in well intervention is the use of increasingly automated tools, and a key enabling technology is robotics. In particular, downhole robotics is becoming an important tool in the operator toolbox, according to Welltec. “They can be quickly deployed, and without needing rigs, they can go in and fix problems in operator wells,” said Brian Schwanitz, vice president for Welltec.
The company introduced downhole robotic intervention tools to the upstream oil and gas industry 16 years ago with the Well Tractor tool, Mr Schwanitz said, noting that mechanical, clean-out and milling tools have more recently enabled a broader range of operations, such as manipulating or removing stuck valves and other restrictions inside pipes.
A natural evolution of advancing robotics was to create a tool that grinds through the walls of the pipe, Mr Schwanitz said. In February, the company introduced the Well Cutter, a pipe-cutting tool that uses grinding pads made of metal matrix composite with embedded diamonds, instead of explosives or chemicals. Deployed on electric-line, either by gravity or conveyed with a tractor in a high-angle hole, the tool is sent to the desired cut point. Surface commands sent through the wireline activate the tool to set two anchors, one at the top and one near the bottom, to hold it in place.
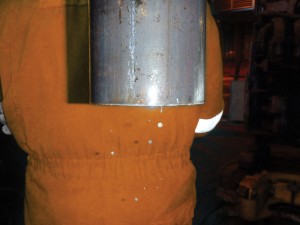
“Once it’s anchored, these grinding pads open out to meet the inner wall of the pipe, and they rotate slowly to initiate the cut and then increase speed to complete the cut. As the pads grind at an angle, they leave a beveled edge so it’s a clean slant, which does not require the normal polishing run to ‘dress’ the cut. The slant cut also allows you to make the cut even though the pipe isn’t in tension,” Mr Schwanitz explained. If production has been suspended due to completion problems, for example, and cutting a stuck tubing is required, this can be a low-risk method to sever the pipe without damaging the outer casing, he said. Further, the Well Cutter produces only a fine powder, which does not interfere with future operations.
The Well Cutter saw its first commercial deployment in February with a pipe-cutting operation for Sakhalin Energy on the Piltun platform offshore Russia. Sakhalin Energy had experienced problems pulling the packer on a previous workover attempt. The pipe was 4 ½ in., 12.6-lbs/ft tubing, and total operating time was approximately six hours. The operation was performed in a deviated 57° well at a well depth of 7,000 ft (2,133.6 meters) and with a downhole temperature of 140°F. The pipe was successfully cut in the first run. By not having to use explosives and chemicals, both safety risks and logistical hurdles for handling these materials were eliminated. “It also saved them from having to go back in and polish off the flaring and all the associated cutting debris that is common with other pipe cuts,” Mr Schwanitz said.
Although a rig will eventually be needed to remove the pipe from the well, the Well Cutter can be mobilized to cut the pipe before the rig arrives, making it a quick solution when explosives or chemicals are not easy to mobilize or a rig is not readily available, Mr Schwanitz said. He adds that Welltec is working to extend the autonomous aspect of downhole robotics by eliminating the power cable. “We are working on a totally wireless set of tools run on batteries that will self-recharge if there is flow from the well. This will be the direction of the future.”
Baker Hughes
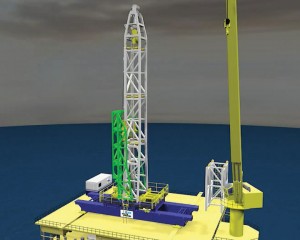
Even with the best technologies, a mature well will eventually pass the point of production. “The aging fleet of platforms around the world are eventually going to be removed, and you need some efficient and economical way to do it,” David Harris, business development manager for Baker Hughes, said.
Baker Hughes recently introduced the Mastiff, a mechanized, self-erecting and self-pinning, rigless intervention system that can be used for workovers, abandonments and drive pipe pre-installation operations. The company was prompted to design the Mastiff after the issuance of NTL5 in the US Gulf of Mexico last year, which requires operators to remove platforms that are no longer producing. Economics is extremely important for these operations because they bring no return on investment, Mr Harris said.
Lighter than a conventional rig, the Mastiff system can perform abandonments on old platforms that can’t take heavy loads due to rust or corrosion, saving operators the expense of a platform upgrade, Paul Adams, manager of plug and abandon operations for tubular services at Baker Hughes, said. It can also be rigged up in less than two days. “During a functional acceptance test, we put the derrick up in an hour and a half from the ground to the crown,” he said.
Further costs are saved because a rig is not required to deploy the system. “Anything you can do offline without a drilling rig saves the customers money in the long run,” Mr Adams said. The API 4F-certified Mastiff has been through a function acceptance test and is expected to mobilize for trials in Q4 this year.
The Mastiff isn’t limited to abandonment work. It can perform various operations such as tubing change-outs through coiled-tubing intervention. “We have the capabilities for a section that will fit a coiled-tubing injector head so that coil can rig up and run right through the Mastiff,” Mr Adams said. “Pretty much any well intervention type work can be accomplished with this unit.”
For continued field development, the Mastiff can initiate a slot recovery program prior to a drilling rig’s arrival. Once the pipe is removed, the well slot can be prepared for a new wellbore, saving rig time and offering the operator the option to further redevelop resources.
The ultimate goal of the system is not only cost savings, however, but safety, Mr Harris said. Because it is self-erecting, he explained, “we don’t have to send people up on riding belts to do the assembly. It’s all automatic once it starts.”
WidePak is a trademark of Weatherford.
Welltec and Well Tractor are registered trademarks of Welltec AS.
RELATED ARTICLE:
Enhanced intelligent well system reduces need for well intervention
Helix Well Ops expands well intervention fleet for Europe, Africa