Noble rigs win two gigs: Australia and Suriname
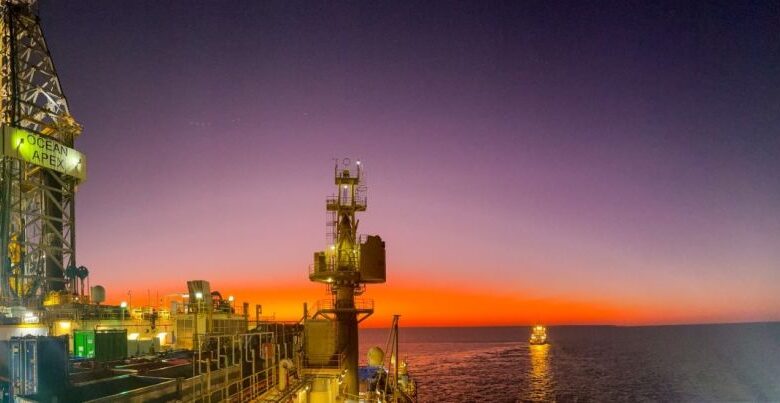
The end of 2024 brought news of two gigs for Noble Corp rigs. First, the semisubmersible Ocean Apex has been contracted for a further period offshore Australia. This contract, which is for a minimum 37 days, will be in direct continuation of the Apex’s prior commitments in Australia, estimated to occur between Q2-Q3 of 2025.
Next up, Noble and Petronas Suriname agreed for the high-specification semisubmersible rig Noble Developer to drill three wells offshore Suriname.
The contract is expected to start around June 2025, with an estimated duration of 200 days. The firm contract value is approximately $84 million including additional services provided, mobilization and demobilization fees. The parties have further agreed to add a one-well option to the contract.