Supervisory control necessary for future automation in drilling
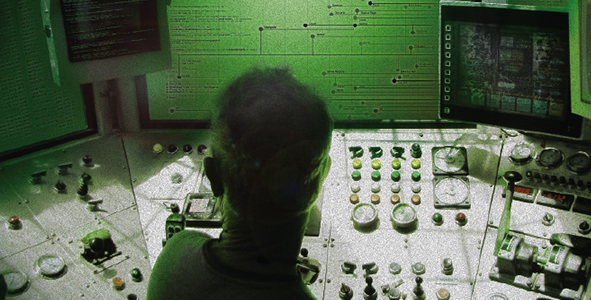
By Alex Endress, Editorial Coordinator

People often think of automation in terms of two extremes – full automation, which requires no human interaction for operation, and manual processes, which completely rely on human labor. However, MIT Professor Tom Sheridan points out that this interpretation is not accurate and that the transition between these two points is actually very gradual. “There are many different levels of automation in between… It is an intimate stage-by-stage kind of thing,” he said, noting the effort and dedication it requires for companies to develop and transition into automation. Dr Sheridan is scheduled to speak about his own experiences in non-oil and gas drilling environments, which can provide insight to the drilling industry to adopt these levels of automation, at a symposium to be jointly held by the IADC Advanced Rig Technology (ART) Committee and the SPE Drilling Systems Automation Technical Section (DSATS) on 29 February in Fort Worth, Texas.
Full automation, in which a rig could drill a hole without any need for human interaction, would be a very long-term goal, Dr Sheridan said. However, supervisory control of automation – in which humans monitor automated machinery and intervene to update instructions when necessary – is nearer on the horizon. “You can think of a supervisory controller of automation in the same way that you think of a supervisor of other humans in a factory,” he said. “The supervisor sets the criteria and the schedule, and (workers) who are doing the actual physical work on the product take orders, saying ‘yes, sir’, ‘no, sir’ or ‘sorry, I ran into this problem.’ Instead of those lower level workers, you’ve got machinery doing the job – robots, if you will.”
Dr Sheridan cited the airline industry as an example of successful supervisory control, as most commercial pilots intermittently instruct the autopilot, which actually flies the airplane for most of the flight, and typically take over manually for take-off and landing. Supervisory control is especially useful for human intervention to deal with multiple unknowns, such as geological factors or pressure deviation, Dr Sheridan said.
Although not as far away from reality as full automation, supervisory control is still high-level automation that must be developed through stages. “You have to go to that slowly,” he explained. In the lowest levels of automation, computers may advise human workers on how to best complete the task they are given using simulation, as information such as pressure levels and ROP, is measured through the computer. “You bring all your sensory information back and put that into a computer and then make extrapolations or projections,” he said. Based on these projections, computers can give recommendations to the human workers. At higher levels of automation the human issues more general commands and criteria and the computer and automation execute the action.
Implementing these different levels of automation will depend on companies’ willingness to invest and try new products, Dr Sheridan said. “You try things and see what works, and there is cost to that.” However, he said it will take not only commitment from operators looking to drill the well more efficiently, but also investments by the service companies themselves to demonstrate what the new developments can do. “Somebody is going to have to make some investments and take some risks, of course, and that goes with any technology.”
Dr Sheridan has been working with the Drilling Systems Automation Roadmap initiative through the Human Systems Integration (HIS) challenge team led by Amanda DiFiore with Circadian. Participants in this team bring current and future drilling input to the displays and control system interface with the human operators to which Dr Sheridan and Dr DiFiore add their HSI experience to guide the understanding of how the human systems interaction should develop for drilling systems automation.
The 2016 SPE DSATS and IADC ART Symposium will be held in advance of the 2016 IADC/SPE Drilling Conference, scheduled for 1-3 March in Fort Worth. Registration for the symposium will open with the Drilling Conference registration in November. For more information, please click here.