ADNOC, Siemens Energy to develop blockchain-based, low-carbon energy certificates
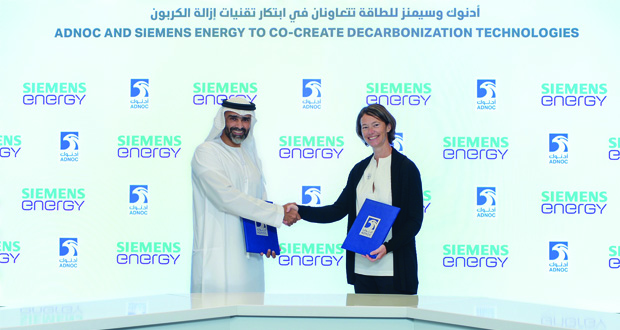
At the 2022 Abu Dhabi International Petroleum Exhibition and Conference (ADIPEC) on 2 November, Abu Dhabi National Oil Company (ADNOC) and Siemens Energy announced plans to pilot blockchain technology to certify the carbon intensity of a range of products.
By using smart sensor data gathered from across ADNOC’s operational chain – from the oil well right to the customer – the pilot will show how much CO2 was used to make products such as Murban crude, ammonia and aviation fuels. This information will be automatically recorded onto a decentralized blockchain ledger.
Such transparency will allow independent regulators to certify the carbon intensity of products. It will also give customers greater confidence and clarity over the carbon footprint of their purchases.
“People typically associate blockchain technology with crypto currencies, but the use of decentralized ledgers has significant implications for the energy industry. This pilot promises to shine a digital spotlight into our manufacturing processes. It will show the world why energy supplied by ADNOC is among the least carbon intensive in the oil and gas industry,” said Abdulmunim Saif Al Kindy, Executive Director, People, Technology and Corporate Support Directorate at ADNOC.
The low-carbon energy certificate initiative forms part of a broader memorandum of understanding between ADNOC and Siemens Energy. Under the agreement, specialists from both companies will co-create technologies to accelerate decarbonization and the transition to clean energy. They will collaborate at ADNOC’s state-of-the art innovation facility in Abu Dhabi. Other areas under joint development include electrification and “Power-to-X” technologies to produce green hydrogen and its derivatives, including synthetic CO2-derived products.
“By leveraging our unique knowledge and expertise of certificates of sustainability, Siemens Energy will work with ADNOC to develop solutions for the benefit of the energy industry. Investing in innovation and the co-creation of technologies are vital tools for reducing emissions and meeting Net Zero targets,” said Fahad Al Yafei, Chief Technology Officer, Siemens Energy Middle East.
The collaboration will begin the end of Q4 2022.