Standardizing subsea BOP soak testing: overview of value and recommended best practices
Proposal for API Standard 53 annex aims to unify testing methodology while considering different BOP configurations, potential for digital tools
By Patrick Hillard and Leonard Childers, IPT Global; and Ahmed Omar, Seadrill
The BOP soak test is an important yet often misunderstood part of deployment preparation for subsea BOPs. Although it helps improve both the safety and efficiency of drilling operations, this test remains an area lacking industry standardization, leading to potential uncertainties and inconsistencies in BOP performance. This article explores the history, challenges and potential to standardize an often-overlooked contributor to well control equipment reliability.
The well control equipment evolution
The first BOPs were sketched out by James Abercrombie and Harry Cameron on a sawdust-covered machine shop floor just east of downtown Houston in the early 1920s. Since then, the industry has come a long way. State-of-the-art equipment is used to set wellheads more than 10,000 ft below the water line, deploy, latch and remotely operate multiplex subsea BOPs, and then drill into ultra-deep, high-pressure hydrocarbon reservoirs.
To safely accomplish these engineering breakthroughs, rigorous verification requirements such as pressure testing, function testing, manufacturing specifications, maintenance protocols and kick/leak-off detection methodologies have been developed. These standards have regularly been adopted by state and federal regulators and incorporated into API Standards and/or the Code of Federal Regulations, in the context of subsea BOPs and subsea BOP control systems.
BOP soak test value
The BOP soak test involves detailed evaluation of the multiplex electro/hydraulic circuitry in both the primary and secondary control systems of the BOP. It applies a predetermined pressure to various operators and fluid circuitry for a required duration. During this test, subsea engineers meticulously inspect the BOP for visible leaks, weeps, drips, fogging and other indicators that inform necessary maintenance before deployment. In many instances, digital monitoring and pressure signal analysis are performed concurrently to expedite the soak testing process and mitigate the need for extended troubleshooting iterations.
A robust soak test prior to subsea deployment provides an essential assessment of the health of the BOP. It provides crucial insights into the BOP stack’s fitness for service by identifying potential issues that could affect its performance and availability once deployed. By physically inspecting the BOP and analyzing the stabilized pressure readings over a brief period, trained personnel can identify leaks or potential component degradation within each pressurized fluid circuit. This not only facilitates troubleshooting and smarter maintenance efforts but also offers stakeholders peace of mind by ensuring due diligence has been accomplished to protect personnel, the environment and related assets.
While soak testing remains the foremost method to assess control system health before deployment, it’s imperative to understand the inherent limitations. Soak tests can’t replicate the multifaceted, real-world conditions a BOP would face when placed on a wellhead. These factors, such as stack movement (both tension and compression), fluctuating temperatures and varying hydrostatic pressures, can significantly impact system performance.
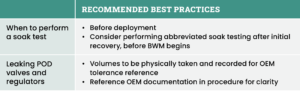
Thus, while current testing methodologies provide valuable insights, it’s important to continually evolve, capturing the nuances of real-world operations in the form of recommended best practices.
Recent industry performance data
Technological advancements have prompted industry experts and regulators to develop stricter requirements for equipment verification. These improvements reflect a deeper understanding of the industry’s increasingly complex equipment, enabling refinement of testing protocols to ensure they are fit for purpose.
Historical data presents some significant findings. As outlined in the BSEE-sanctioned report, “Blowout Preventer (BOP) Maintenance and Inspection Study by the American Bureau of Shipping and ABSG Consulting Inc. (2013),” 61% of subsea BOP system failures were linked to the control system. Notably, the blue and yellow control PODs, along with the surface MUX control system, accounted for over half of these failures. The study’s mean time to failure revealed an average of 48 days of operation between component failures. It’s crucial to note that due to built-in system redundancies, some of these recorded failures signaled the need for upcoming repairs rather than indicating a stack pull.
Fast-forward to the current era, where detailed defect data is available from the Rapid-S53 database. In the 2018 and 2019 annual reports, the cumulative average BOP pulls hovered around the low 30s annually for the represented BOP stacks. It’s clear there is a marked improvement in these figures when juxtaposed with data from preceding years.
Data from 2020 and 2021 present an even more encouraging narrative: The number of stack pulls averaged in the low 20s. Many BOP experts acknowledge the pivotal role of the rigorous soak tests conducted prior to deployment. Although this isn’t a normalized metric, it points toward enhanced reliability performance.
The inference? The industry is leaning into the lessons learned and making strides in equipment reliability performance. Considering this positive trend, coupled with industrywide knowledge sharing, there has been clear progress in the pursuit of zero NPT.
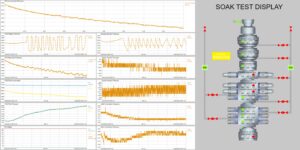
State of industry practices
Current industry practices regarding BOP soak testing exhibit significant variations in frequency, methodology and test duration. Many equipment owners and operators conduct these tests regularly before deployment, while others perform them both before and after deployment. Additionally, there’s no standardized timeframe for these tests, with durations ranging from minutes to days.
The complexity of these tests also varies, from two-step tests to procedures with 15 or more steps. Factors influencing the testing methodology include stack configuration, contractual agreements, deployment duration estimates, maintenance planning, condition-based maintenance program maturity, crew proficiency and digital monitoring capabilities. Despite these differences, “boots-on-the-ground” inspections remain the most common means of leak detection.
There is also significant promise shown in the latest digital trend recognition algorithms. For example, a proactive subsea team, along with a specialized team of remote BOP analysts, have been able to identify system anomalies within minutes of pressure stabilization and pinpoint critical components within each fluid circuit (Figures 2-4). This can significantly reduce troubleshooting and fault-finding efforts during an already stressful, fast-paced pre-deployment period.
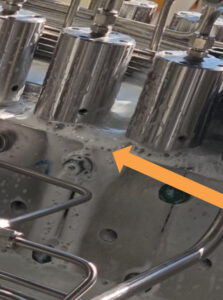
Standardization challenges
Differences in BOP design and operational philosophies among major OEMs also contribute to variations in soak testing practices. Each OEM has testing procedures tailored to their BOP designs, leading to a wide array of testing methodologies.
For instance, OEMs have freedom regarding the rated pressure of the operating chambers in their BOPs. These rated pressures can vary from a few hundred psi up to 5,000 psi or more. The soak tests must accommodate these differences that exist not only between different OEMs but also in different models of operators within each OEM.
An example involves hydraulic wellbore connectors. Some connectors should not be locked with pressure exceeding 1,500 psi due to crushing effects that may be imposed on the wellhead, BOP mandrel or test stump. There are others that physically cannot be latched above a specified psi because a relief valve has been installed on the closing circuit.
Testing should also take into account the OEMs’ allowable return flow for control system valves. This has been discussed in API Standard 53 committee meetings for potential inclusion in the next revision of the standard. Normal return rates have been reduced by design improvements (e.g., highly polished tungsten seal surfaces versus matte finishes on softer materials). Control system OEMs may produce new designs that would lead to tighter systems with less return flow.
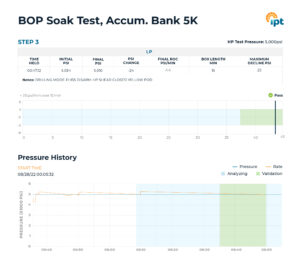
Potential to reshape with technology
Collaboration and digitalization can play a pivotal role in standardizing BOP soak testing practices. By working together within the API committee meeting structure, operators, contractors and service providers can develop a unified testing methodology and recommended best practices that consider the different BOP configurations and unique requirements throughout the industry. Digital tools can streamline this process, making it easier to apply uniform testing protocols across various operations and regions.
In addition, digital applications can be designed to perform trend analyses, remove subjectivity from test results, and help identify testing missteps (e.g., valve alignment and trapped pressure in the wellbore). Digital twin displays can facilitate collaboration and provide insights for the stakeholders as they strive to protect people, the environment and assets.
Standardization framework
Given the history of control system failures, the industry has recognized the need for enhanced testing measures, particularly in soak testing. Drilling contractors have been refining procedures and monitoring techniques. This initiative aligns with the specifications set out in the 5th edition of API Standard 53 from December 2018. This edition introduced the requirement for soak testing subsea stacks prior to deployment. Specifically, Table C7 emphasizes the need to validate the BOP stack hydraulic circuits at the highest pressures anticipated during well control operations. The test’s duration is per the equipment owner’s stipulations, with the key acceptance criterion being a visual confirmation of no leaks.
Standardized BOP soak testing should encompass all aspects of the pre-deployment soak testing process, including test step duration, pressure limitations, configuration (mode) and testing conditions. It should also consider the varying environmental conditions in which BOPs are deployed, as well as the different types of BOPs and their specific requirements.
Path forward
The contributors of this article support the development of standardized recommendations for BOP soak testing for inclusion in the next edition of API Standard 53. This could be an informative annex that will help reduce subjectivity in visual leak verifications, leading to enhanced safety and reliability performance industrywide. Equipment owners would have the benefit of shared best practices as a starting point for their procedures.
Improving the effectiveness of pre-deployment soak testing of BOP systems will reduce risks directly associated with its reduced availability to perform the intended critical functions. In addition, reducing unplanned BOP pulls will eliminate risks associated with retrieval and subsequent redeployment. This further safeguards people and the environment.
A joint effort among stakeholders in crafting this methodology will enable swift and effective BOP assessments and stable health KPIs, and further reduce subsea NPT. The journey to improve the reliability and performance in drilling operations will not cease as we reaffirm our commitment to improving industry standards of performance and safety. DC
Reference: American Bureau of Shipping & ABSG Consulting Inc’s Blowout Preventer (BOP) Maintenance and Inspection Study Final Report for the Bureau of Safety and Environmental Enforcement., June 2013.