SIMOPS, dual-activity rig enable best-in-class well offshore Nigeria
Project team successfully challenged existing heavy-lift protocol to leverage rig’s AHC crane for improved efficiencies
By Jessica Whiteside, Contributor
The maxim “time is money” is manifest daily in the offshore oil and gas sector. Especially in deepwater, drilling a well can require tens or hundreds of millions of dollars of investment. In 2017, Shell Nigeria challenged its deepwater team to trim its average well delivery time on a mature field offshore West Africa. In response, the team implemented a simultaneous operations (SIMOPS) strategy that reduced the use of field service vessels (FSVs) and enabled carefully planned and controlled heavy lifting over drill centers.
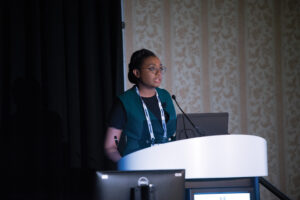
Shell Nigeria engineer Aihanuwa Abuah presented an overview of the project at the 2020 IADC/SPE International Drilling Conference in Galveston, Texas, in March. She explained that, in 2017, the organization set a target to deliver best-in-class wells consistently in 28 days. That equals approximately 25 days per 10,000 ft and was 10 days shorter than the average achieved on the previous campaign, which had used a semisubmersible with a single derrick and single BOP.
To meet the new target, the team decided to deploy a dual-activity rig with two BOPs that would support offline SIMOPS. Not only would this rig generate savings from dual activity during batch drilling, but it would also enable open-water tripping, casing running and surface activities to be moved entirely offline. Use of the rig’s active heave compensated (AHC) crane would also provide the opportunity to run subsea tubing head spools (THS) and Christmas trees offline.
“However, there was a challenge,” Ms Abuah said. “The field’s existing procedures prohibited all heavy-lifting operations (above 15 tonnes) at the drill center due to the risk of drops on subsea infrastructure.” The team decided that, in order to make optimal use of the rig’s capabilities, the existing protocol had to be challenged.
According to the technical paper co-authored by Ms Abuah, previous heavy-lifting operations of the conductor, surface casing and BOP enacted under this policy could only be performed after the rig had moved to a safe handling zone. Similarly, installation or retrieval of a THS historically required the rig to move to a safe zone while an FSV moved over the well center to install or retrieve the THS. Under the team’s proposal, the rig’s AHC crane would handle such THS operations on the spot, eliminating the need for the FSV.
To support its challenge of existing procedures, the team conducted a review of global rig SIMOPS, both within and outside Shell, and found that similar activities had been completed successfully without impact to subsea infrastructure. In addition, they found no history across the field’s 80-plus wells of objects being dropped on the seabed during heavy lifting in a safe zone or drill center.
The team also held an integrated hazard identification workshop to ensure that appropriate preventive controls were in place. A study on the potential impact of dropped objects on subsea facilities led to the incorporation of additional controls into the field’s drilling and completion procedures.
Setting field records
Once approval was secured to perform heavy-lifting operations at the drill centers, the SIMOPS campaign focused on two main areas: top-hole performance and THS installation.
“Most of the results we obtained had to do with eliminating the need to move the rig to the safe handling zone, as well as eliminating dependence on the FSV to perform certain heavy-lifting operations, particularly around the installation of the tubing heads,” Ms Abuah said.
The field uses two standardized well designs: a conventional casing scheme with 20-in. surface casing and a reduced casing scheme with a tapered 20-in. x 13 3/8-in. surface casing. The project included both of these well types and executed SIMOPS on all 10 top holes drilled for the campaign. The new approach included running the surface casing offline while drilling the top hole from the main rotary.
“We saw a significant improvement in the top-hole drilling time,” Ms Abuah said. The fastest top hole took just 2.7 days to drill, while the average across the campaign was 3.9 days, approximately 1.5 days faster than the average from the previous campaign.
The technical paper noted that key enablers of this performance included the installation of centralizers on casing joints onshore prior to mobilization to the rig; racking back of casing in the auxiliary rotary while performing critical path work on the main rotary; preparation and racking back of tools such as the bottomhole assembly, cement head and high-pressure wellhead housing; and preparation of the BOP landing assist tool.
The project’s approach to offline THS installation – using the rig’s own AHC crane rather than FSV support – saved five hours per well. This strategy contributed to the success of the field’s inaugural use of a single-trip completions technology, which saw the rig install both upper and lower completions in a single run and which led to a completion installation time of 3.2 days – a field record.
The success of rig-based THS installation prompted the team to recommend use of the AHC crane for THS retrieval during future well abandonments, a move expected to save four hours per well.
Understanding limitations
Ms Abuah described the SIMOPS as a risk-based option for achieving best-in-class performance for an operation. However, she cautioned that not all wells would benefit from the same SIMOPS approach. While top holes on this field are drilled in batches of two to five wells, situations requiring the drilling of a single top hole would achieve better results with a single-derrick approach.
The team also found that some activities cannot be done offline when the casing length is longer than the water depth because this makes it impossible to run the entire surface casing string length prior to skidding the auxiliary rotary to the well. DC
For more information about this project, please refer to IADC/SPE 199549, “Implementation of Rig Simultaneous Operations Over Drill Centers to Improve Deepwater Drilling Performance,” presented at the 2020 IADC/SPE International Drilling Conference in Galveston, Texas, 3-5 March.