Shell drives down high-potential incidents with global dropped objects prevention campaign
By Gordon Graham, Shell International E&P

Safety is always our top priority. We aim to have zero fatalities and no incidents that harm people or put our neighbours or facilities at risk. When we analyzed the biggest risk areas in our wells operations, we found dropped objects to be the largest category of high-potential incidents (HIPOs) in Shell’s wells operations. We took it as a clear call for action and started a campaign to make a change.
The clear downward trend of HIPOs in the first half of 2010 suggests that it’s working.
HIGH-POTENTIAL INCIDENTS
We define a HIPO as an unplanned HSE incident or near-miss that has the potential severity to cause permanent disability or death. For dropped objects, this is regardless of any barrier that may be in place to prevent personnel from walking into a danger zone.
HIPOs involving dropped objects have accounted for the great majority of potential and actual fatalities in Shell’s well operations over the past few years, including three fatal accidents since June 2008.
Figure 1 shows the different categories of dropped objects against the number of times a HIPO has occurred. This indicates that drilling equipment, lifting equipment and tubulars are key focus areas.

LAUNCHING CAMPAIGN
Determined to eliminate dropped objects, we launched the Prevention of Dropped Objects campaign in mid-2009. It involves everyone who works on drilling, completions and well interventions, including Shell staff and contractors.
The campaign is just one of several ways in which we seek to align with our drilling contractors and international service contractors on safety improvements. Others include the development of Joint Safety Improvement Plans, compliance with our Life-Saving Rules and Temporary Pipework Standard, distilling and sharing key actions arising from HIPOs, and carrying out joint worksite safety audits at a minimum of two locations per contractor per year, with senior management participation.
The rollout of the Prevention of Dropped Objects Manual was the first step in the Prevention of Dropped Objects campaign. It is aimed at management and supervisory staff for Shell and its contractors and is based on four principles, each of which has a series of mandatory requirements for Shell staff and its drilling, completion and well intervention contractors. These principles are:
• Contractors providing equipment and personnel on Shell well sites shall have a dropped object prevention scheme.
• A systematic dropped object inspection programme shall be in place.
• Worksite hazard management for dropped objects shall be in place.
• Audits to check for compliance with the dropped object prevention scheme shall be in place.
We are also determined to stamp out the use of forbidden equipment (Figure 2), which are often the cause of dropped objects, and reinforce and mandate the use of proper equipment, including the use of tethered tools.
Managers, supervisors, operations staff and contractors have adopted the manual and use it across different countries and cultures at more than 100 rig locations and up to 200 well completions and intervention activities every day.
It is also supported by a pocket-sized ABC Guide to Dropped Object Prevention, which is proving popular and useful.
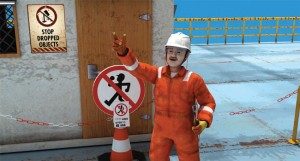
IMPLEMENTING CAMPAIGN
It is clear that issuing the manual was only the first step in a much wider campaign. The manual itself is not enough to change behaviour and working practices. We are determined to make a full-scale change via the Prevention of Dropped Objects campaign, which will involve everyone from management to the worksite employees and contractors who are at risk of injury or worse.
The implementation is challenging, but it is essential that it is rolled out and embedded in all our locations. To succeed in eliminating dropped objects, it is imperative that all Shell wells staff and contractors understand and comply with the mandatory requirements set out in the Prevention of Dropped Objects Manual.
Regional DROPS Focal Points (DFPs) are responsible for ensuring that the requirements for preventing dropped objects are communicated to the local teams, including contractors, and then tracking the status of compliance with mandatory requirements for management review.
The DFPs also appoint and brief local DROPS leads who run the DROPS campaign at their site. A key role for a DROPS lead is to conduct a gap analysis to identify what has to be done to comply with the manual. An action plan for improvement at the respective location is essential to success.
COMMUNICATION, TRAINING MATERIALS
There are six campaign topics supported with communication and training materials that are being rolled out on a quarterly basis until summer 2011. The topics are: tools at height; tubular handling; No-Go Zones and Red Zones; handling lubricators and tool strings; drilling equipment; and winches and tuggers.
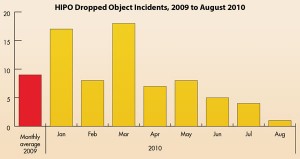
Training for each topic includes cascaded learning sessions to be run at the work site, as well as awareness animations and practical exercises to convey key knowledge and skills. The animations, delivered on DVD, are an innovative way of getting across key learning points (Figure 3). The cartoon characters demonstrate bad and good practice in a humourous way. They are also language-free so can be used worldwide.
Communications includes presentations for managers and supervisors, as well as a regional Drops Focal Points Forum to clarify expectations and share learnings; monthly teleconferences; articles for internal and external publications; a Drops website; and posters for each topic.
We have implemented the training and communication packs for Tools at Height and Tubular Handling. As this article is published, the material for No-Go Zones and Red Zones will have been launched.
We hope that our investment in this training is another way of showing how determined we are to eliminate dropped object incidents throughout the business. We are encouraging all of our own and contractor staff to support and participate in the campaign and demonstrate, by their actions, that compliance with the requirements of the Prevention of Dropped Objects Manual and eliminating dropped objects is important to them.
WHAT’S NEXT?
It’s not enough to roll out materials and training; therefore, we monitor and measure that change is happening. Audits are taking place to check for compliance against the requirements of the Prevention of Dropped Objects Manual through joint site inspection visits, annual contractor facility audits and local area compliance audits. The success of the campaign is demonstrated by the downward trend of HIPO drops incidents throughout 2010.
At the start of the year we had a high of 18 drops HIPOs in a month, and this has reduced to only one incident in August 2010. It is important to stress that we still have a long way to go. Do not think the job is complete; it will require constant vigilance to Stop Dropped Objects.
Gordon Graham is vice president wells HSE, projects and technology, Shell International Exploration & Production.
This article is based on a presentation at the 2010 IADC Drilling HSE Europe Conference & Exhibition, 29-30 September, Amsterdam.
HIPO – We define a HIPO as an unplanned HSE incident or near-miss that has the potential severity to cause permanent disability or death