Sensor-based system allows real-time detection, monitoring of emissions in frac operations
Users can be alerted to take immediate remedial action, while over time the data can help to identify emissions, equipment trends
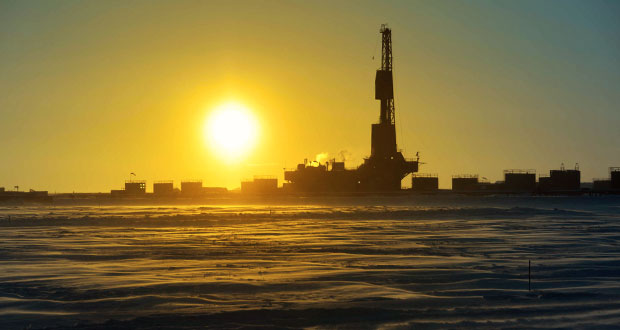
By Stephen Whitfield, Associate Editor
As the oil and gas industry continues to adopt more stringent measures for reducing greenhouse gas (GHG) emissions, especially from significant contributors like heavy fracturing equipment, it is critical companies can get accurate emissions measurements directly in the field to enable comprehensive monitoring and tracking.
Last year, SLB launched a real-time sensor-based emissions detection and monitoring system for hydraulic fracturing operations, which the company says can also be adapted for other applications like drilling. The sensors are placed near heavy fuel-burning equipment like engines and generators to analyze their emissions data, which is then sent to the cloud. Users can view visualizations of the data on dashboards, and they also receive alerts if GHG and other emission levels surpass a predetermined threshold.
“As we look toward a net-zero future, we’ve come to the conclusion that the first step in solving the problem is to capture the greenhouse gas emissions from the wellsite as accurately as possible,” said Rishika Narang, Information Management Engineer at SLB. “We want to enable real-time monitoring, and we want to make sure that we can visualize the data in a way that users don’t get stuck looking at information they have no way to comprehend. We want the asset managers to get notified whenever a key performance objective for emissions levels that we have in mind are breached.”
Ms Narang, who spoke at the 2023 SPE Hydraulic Fracturing Technology Conference in The Woodlands, Texas, on 2 February, said the system utilizes electrochemical sensors that react with gases in the air and identifies CO, CO2, NO2, hydrogen sulfide (H2S), nitric oxide (NO), ozone (O3) and methane (CH4). Continuous readings are sent through an application programming interface (API) to a standard query language server, which processes the data and moves it to a cloud server at one-minute intervals.
Real-time data visualization and analytics dashboards, available at the wellsite and in offices, can then help users to monitor emissions levels. If an emission level crosses a user-set threshold for a given parameter, an alarm pops up on the dashboard to notify the user to examine the source of the emissions and potentially take remedial action. This might include stopping specific pieces of equipment that are generating an abnormal amount of emissions.
This type of monitoring can also be useful for equipment monitoring and maintenance. If users notice an increase in emissions generated from a piece of machinery, they can check it for potential issues like corrosion. Further, SLB’s cloud-based algorithms can spot trends related to issues like fuel adulteration, as well as identify low-performing assets emitting high levels of emissions.
Data aggregation and analytics is another key benefit. The system allows all emissions data from a frac operation to be collected in one place, so companies don’t have to deploy different kinds of meters and capturing devices that might produce disparate data that are difficult to aggregate and analyze.
Ms Narang said this functionality makes it easier for asset managers to keep track of data over time. It will also be beneficial for frac crews who might not have been present at an earlier stage in the frac operation, as they will have the ability to easily view emissions data from any point in time.
“Having this application gives us the freedom to be in touch with the entire data set, so you know exactly where the emissions are coming from and where all potential breaches could be happening,” Ms Narang said.
Taking an even longer-term perspective, the emissions data accumulated over time can help companies understand how they can reduce their overall carbon footprint across multiple operations, as well as provide critical data points for corporate sustainability reports.
Pilot project
Last year, SLB conducted a pilot study of the sensor system on a hydraulic fracturing site for an unnamed operator. Sensors were mounted near exhaust pipes of the frac engines, where the maximum level of emissions could cross the sensors. Sensors were also placed within an enclosed cabin on the frac site in order to measure the cabin’s exhaust efficiency.
For this particular project, the sensors were calibrated to measure two types of particulate matter – fine particulate matter (PM2.5, which is less than 2.5 micro-meters in diameter) and coarse (PM10). They also measured CO2, NO2 and H2S, along with temperature, humidity and air quality index.
Live data of all the gases were successfully captured and transmitted without requiring manual calculation, according to SLB.
The pilot also aimed to test the machine learning algorithms within the cloud-based system. Because the sensor system requires continuous electricity to operate, the algorithms can be useful in the event of electrical failures, by interpolating emissions readings that might have been missed. During the pilot, two sensors measuring CO2 were run in the same location. One was kept running, while the other was intentionally stopped for a fixed duration. The interpolated data points from the stopped sensor matched the CO2 readings from the other sensor, indicating the accuracy of the algorithms.
While most GHG levels recorded during the pilot were below the threshold set by the operator – 1 ppb of H2S, 12 ppb of NO2 and 600 ppm of CO2 – the sensor system did unexpectedly detect a higher-than-expected level of CO2 levels in the closed cabin. This confirmed the need for better ventilation, Ms Narang said. Outside of the cabin, the frac site was not exposed to unwanted higher levels of GHG emissions.
Another more unexpected finds during the project was that there was a drop in NO2 emission levels during the daytime hours. The team traced this to the fact that, in the presence of sunlight, NO2 is converted to NO, and O3 is released as a byproduct; addressing this in the future would likely require for those two gases to be measured, as well. DC
More information can be found in …