Sand control case histories: Shape memory polymers, resins, shunt tubes
By Diane Langley, editorial coordinator

Sand, a familiar adversary for drilling and completion engineers, continues to present a major obstacle to well production. It erodes hardware, blocks tubulars, creates downhole cavities and must be removed and disposed of. The challenge to control sand can cost tens of billions of dollars each year and represents an area of evolving technical expertise.
Sand control is playing a much bigger role in payzone management than in the past. According to Brad Baker, director of sand control systems for Baker Hughes, the realm of sand control has evolved to include systems and devices that are integral to understanding the pay zone, providing correct connections to the reservoir, enhancing the reservoir, maximizing reservoir conductivity and optimizing production.
According to Thomas Murphy, sand management services sales and marketing manager for Schlumberger, there is a growing trend toward open-hole completion techniques due to technology advances. “We are being asked to complete longer intervals with tighter pressure windows, along with the additional challenges we are encountering with shale,“ Mr Murphy said. “Because of this open-hole trend, we are seeing an increased demand for drilling with oil-based mud systems, which creates additional challenges with cleanup, displacement and debris management. This shift makes managing the transition from drilling to completing, and finally production, much more critical.”
“The industry continues to push us to do more in less time with cased-hole environments as well,” Mr Murphy said. Depending on the application, a variety of completion techniques are emerging where it is possible to complete long intervals at one time or to directly isolate and complete different zones separately in a single trip.
Advances to address potential and existing sand control challenges in all types of formations, both consolidated and unconsolidated, have been under development and range from shape memory polymers to increased application characteristics of resins for chemical consolidation. Baker Hughes, Halliburton and Schlumberger share some recent developments and case studies.
Shape memory polymers, nanoparticles
The use of shape memory polymers (SMPs) is undergoing field trials, Mr Baker said. Shape memory materials are smart materials that have the ability to return to their original shape after being introduced into a deformed state by an external stimulus or trigger, such as a temperature change. Sand management was selected as an initial application for SMPs because of its unique materials and properties. Due to the extreme environmental conditions that can be encountered in some wells, an improved SMP with transition temperatures, permeability and filtration properties suitable for downhole use was developed.
A device for use inside casing to control sand from entering perforation tunnels is also becoming available. Mr Baker explained that sand control media-filled telescoping devices connect the reservoir face to the production liner without explosive perforating charges, providing reliable full-bore sand control without gravel packing. Because there are no explosive perforating shaped charges, there is no resulting debris, no damage to the formation face, no sand control screens, no gravel packing and no high-volume/high-rate fluid pumping required, Mr Baker said.
A third technology, nanoparticles, has been in use in sand control applications for about a year. Baker Hughes’ nanoparticle fines migration control additive can be added to the proppant mix at the blender tub on the fly. Inogranic nanocrystals are capable of fixating formation fines, such as colloidal silica, charged and non-charged particles and expandable and non-expandable clays onto proppant particles.
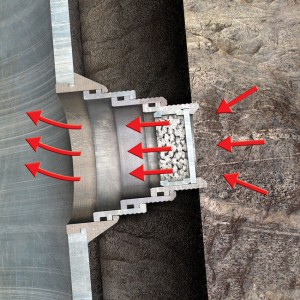
The nanoparticle technology was used on a frac pack completion on a Gulf of Mexico well that had been producing sand for five months. The well, located in Green Canyon 157 in 2,618 ft of water, had a zone of interest with a reservoir pressure of 9,275 psi and temperature of 156° F. The well had been shut down and sidetracked as a result of major sand control and fines migration problems that caused production losses.
In this application of nanoparticle technology, the nanocrystals, having very high surface force interactions, readily attached to the surface of ceramic and silica proppant particles. Approximately 97,000 lbs of 20/40 proppant were delivered through the perforations into the fracture.
After the frac pack was completed, the well was immediately brought back online with no sand control problems reported. The formation pressure, oil production and gas condensate production values returned to their pre-shutdown values.
Another advancement in sand control, the inflow control device, is used as a permanent part of the well completion to control flow from the reservoir to the wellbore along the length of the horizontal section. The device manages inflow by applying a resistance to flow at the reservoir face.
The Baker Hughes inflow control device was used in 2010 to maximize production and ultimate reserve recovery from a reservoir in Russia’s Eastern Siberian Verkhnechonskoye Field. Due to the lack of an active aquifer, a water-injection system was required to maintain the reservoir pressure. Because gas and water tend to cone toward the heel of the well, they can break through anywhere in the well because of permeability variation along the horizontal section.
Three wells, two producers and one injector, were completed in this field using an inflow control device. After drilling the candidate well, the actual permeability profile was built based on final logs, and the completion design was updated. Packer placement depth was selected to isolate high and low permeability. The number of inflow device joints was then determined to mitigate high inflow from the high-permeability zone and to allow flow with little completion resistance for low-permeability zones.
After an initial production period, the operator ran production logging tests in each of the three wells. Engineers then compared the actual with predicted inflow profiles for the same wells without the Baker Hughes inflow system. The inflow profiles indicated good increase in inflow performance. The ability to capture and understand the results and effect of the inflow performance of these wells resulted in the customer being able to develop this marginal field.
Consolidation using resins

According to Bart Waltman, global product manager for sand control fluids for Halliburton, most consolidation treatments are being applied as remedial applications in formation consolidation and repair of gravel pack, frac pack, standalone or expandable screen completions.
However, recent industry economic conditions have begun to make formation consolidation more attractive as the primary pipe and for completing marginal reserves.
Wells completed in weakly consolidated reservoirs that are susceptible to failure under production conditions such as excessive drawdown, depletion and compaction are candidates for formation consolidation to increase their unconfined compressive strength. In addition, formation consolidation can increase the cohesive strength between the grains and prevent sand production in friable formations at water breakthrough.
“To overcome challenges faced with early resin systems, internally catalyzed (IC) systems were developed,” Mr Waltman said. “These lower-viscosity solvent-based systems combine the resin and activator into one component that ensures successful consolidation takes place wherever the formation is treated.”
The latest resin chemical technology entails dispersing the formulation in an aqueous-based carrier (ABC). The low-viscosity ABC resin, which actively seeks out the contact point between the grains to maximize the bonding between the grains, offers advantages over solvent-based systems, he continued. These advantages include the ability to be foamed using nitrogen, that a large over-displacement is not required to reestablish permeability, and that a high flashpoint eliminates the need for special safety and operational procedures.
In 2009, an IC system was used on a well in East Kalimantan, Indonesia, completed in 4.5-in. casing. The reservoir was known for sand production when water was produced. The well was only able to produce sand-free at 1 MMcfd before it was shut in.
In the past, a through-tubing gravel pack would have been the sand control solution. Based on previous success with formation consolidation in a similar reservoir, an IC resin consolidation treatment was considered. This well was particularly challenging due to concerns that the viscous consolidation fluid could not be injected into the low-permeability formation without exceeding the fracture gradient of the formation.
However, after considering all parameters and with the view of performing sand consolidation treatments in offshore wells where reservoirs often have low permeability and high shale content, the operator and the Halliburton team decided to go forward with the treatment.
An optimized IC resin treatment was placed using coiled tubing across the 6.5-ft interval. After the treatment, the well was tested at 2.5 MMcfd with 70 bbl/day of water at 1,000-psi drawdown. Flow rates stabilized at 1.5 MMcfd and 50 bbl/day of water with no sand production.
Another IC resin treatment using the ABC formulation was used by an operator in the Gulf of Mexico. The operator required a rigless sand control solution for a bypassed reservoir in his existing wellbore, and the economics would not support a conventional workover gravel pack. After abandoning the existing completion, electric line perforating was used to access the 8-ft reservoir. Then a foamed ABC resin treatment was bullhead pumped down the existing production tubing. After the treatment, flow rate stabilized at 1.4 MMcfd with no sand production.
Cased-Hole techniques
In the deepwater Gulf of Mexico, Schlumberger worked with an operator who required a solution to eliminate sand production and achieve low skin value in complex wells. The field was being produced from eight different wells. Six of those wells employed a single selective frac pack, with one using a stacked, commingled frac pack.
In an attempt to reduce the high costs associated with stacking frac packs in these deepwater completions, it was decided that the number of completions should be minimized by completing long, perforated intervals.

The targeted wells featured multiple zones, resulting in complex directional wells with 50° to 60° maximum hole angles. The wells were completed using dry trees from a tension-leg platform and are produced primarily from massive, fine-grained, Pleistocene reservoirs. The reservoir can be characterized as unconsolidated and silty, adding to the complexity of the wells in the field.
To maximize well productivity with minimum solids production, the wells required completions with cased-hole frac packs. Sand control methodology was required to prevent the sand production at the expected drawdowns that were planned over the life of the well.
The completion design took into account the long intervals of the producing reservoirs, as well as the large variations in sand grain size and permeability. To reduce the high costs associated with stacked frac packs in multiple zones, the operator chose to complete the long intervals in single stages.
To ensure optimal proppant placement in the screen and casing annulus over the entire interval, the Alternate Path shunt tube technology was used to provide alternate, or redundant, gravel-pack slurry pathways. These pathways bypassed bridges and filled any voids in the gravel pack.
Because of the long completion intervals and the reservoir thickness, the potential for voids in the annulus pack was considered high. Small grain size added an additional challenge, making it difficult to balance obtaining high permeability in the annulus pack versus preventing sand production. Due to the challenges that were presented, a number of steps were taken to ensure the reduction of the potential for completion failure and sand production.
The Alternate Path shunt tube technology was selected to achieve the ultimate goal of propagating a fracture across most, or all, of the reservoir height with high pump rates, while ensuring complete gravel pack of the entire screen and casing annulus. As part of the screen design, shunt tubes were attached to the outside diameter (OD), which assisted with gravel packing the screen/casing-annulus sections of long intervals.
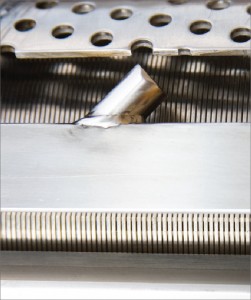
The typical casing/screen geometry was an 8 1/16-in. OD liner with 6 ½-in. drift through the production interval, and with a 3 ½-in. OD base pipe premium screen inside. Two of the wells, A8 and A9, had larger production liners with 9 ½-in. and 8 ½-in. drifts. A 4 ½-in. OD base-pipe premium screen was employed for these wells, using a 7 3/10-in. OD across the shunt tubes.
Through the use of the shunt tube technology, it was learned that thick, silt/very fine sand in highly permeable formations of over 500 ft could be successfully stimulated in a single stage. The job also proved that sand control integrity could be maintained by pumping high-rate frac packs and employing effective shunt tube technology.
The Alternate Path shunt tubes effectively eliminated sand production in all wells. With this technology, the operator was able to successfully stimulate the formation, achieving a low to negative skin value while ensuring a successful gravel pack over the entire interval. This exceeded the pre-project estimate of a skin value of five. Frac-packing multiple zones in a single stage and covering an interval of over 500 ft of the completed wells saved the operator an estimated five days of rig time per well. The process allowed the operator to produce additional reserves that may have been bypassed using conventional stacked completions.
OptiPac is a mark of Schlumberger.
Alternate Path is a mark of ExxonMobil; technology licensed exclusively to Schlumberger.
What chemical recippe was use for the gas well treatment. Did you use a diesel preflush or what did you do