Rules Engine Exchange: Patterson-UTI applies advanced real-time alerting system to drive operational excellence
Development, rollout process included input from across the company to ensure applicability, buy-in
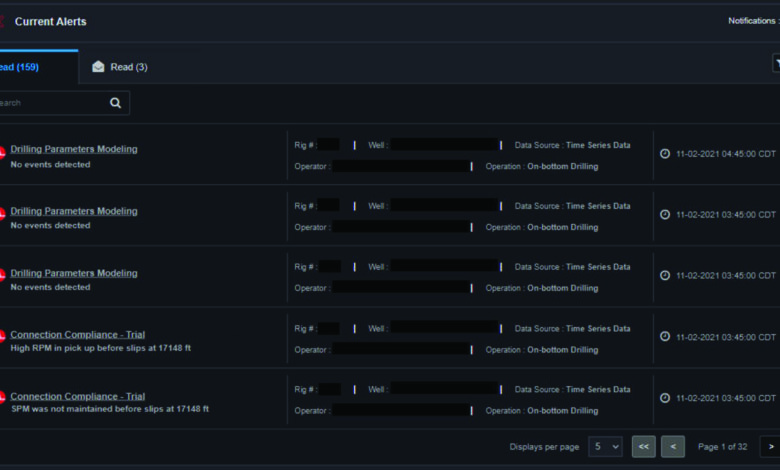
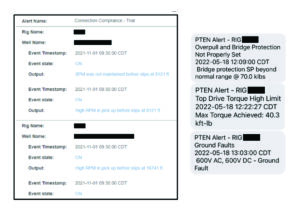
By Trevor Olson, Patterson-UTI Drilling Company
Within the past decade, many industries have found benefits in harnessing and utilizing data for optimizing operations. The drilling industry is currently at the forefront of this trend and is finding an increasing number of applications for data to drive drilling performance. With data coming from drilling contractors, third-party systems and downhole tools, there is an immense amount of information being streamed from location. Initiatives in equipment monitoring, drilling performance and environmental spaces have been the greatest drivers for the utilization of these data sources.
However, one common limitation faced by many data providers is a lack of integration of these data sources. Today, there are very limited solutions available to analyze data from disparate systems. This results in a significant labor cost to monitor for specific trends or operational indicators.
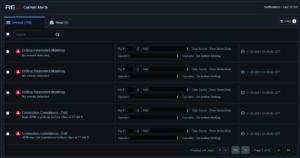
Keeping this in mind, Patterson-UTI wanted to push a development effort to harness the drilling control system (DCS), electronic drilling recorder (EDR) and morning report data into a singular rich dataset for the use of writing custom alerts for driving operational excellence. Rules Engine Exchange (REX) is an interactive feature available in the companywide analytics platform, where users can create and/or subscribe to alerts encompassing several datasets. Alert notifications are deliverable via SMS, email and within the online interface.
Design and development
During the design of REX, the primary goal was to ensure that the value of applicable use cases justified the development effort. Stakeholders were identified and interviewed to align requirements. Department leads from executive management, safety, operations, equipment management, marketing and rig crew personnel were selected to ensure the entire company had a hand in molding this new feature. The initial requirements included:
- Leveraging the company’s current solutions – PTEN+ portal and big data infrastructure;
- Providing a platform where users can subscribe to and/or create alerts on merged EDR, DCS and morning report data;
- Delivering notifications via SMS, email, or within the online interface (Figure 1).
- Having an adjustable delivery method based on alert state change to reduce alert fatigue;
- Having the capability to write alerts using simple arithmetic and expressions for a broad audience with varying technical backgrounds;
- Having an integrated programming language for drilling engineers/analysts to write alerts with high accuracy and share to their team; and
- IP protection on alerts for customers who write alerts within the platform.
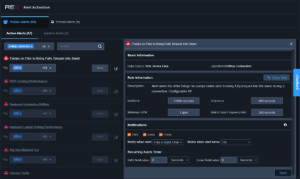
The user interface (UI) was built encompassing three pages: Current Alerts, Alert Activation and Alert Creation.
The Current Alerts page (Figure 2) is where users can view and manage their alerts within the online interface. Users can manage their alerts similar to their email inbox by marking as read, filtering, and searching back to view alert trends.
The Alert Activation page (Figure 3) is where users can subscribe to any alert made available to them by Patterson-UTI, anyone in their user group, or their privately created alerts. Users activate an alert by selecting their desired rig(s). By expanding the alert, the user can read the description of an alert and opt in for their preferred notification delivery method.
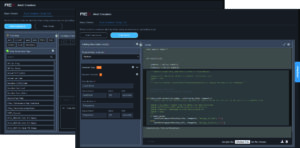
Several novel features help provide the best experience for end users. First, dynamic variables are available if the user would like to change specific parameters of the alert without having to change the underlying code. Second, the user can configure their alert to be notified when the alert turns on and/or off, as well as regardless of the state of the alert and notify continuously. Third, a recurring timer allows the user to set a time frame to receive all alerts for all rigs selected within one notification. Combined, these features allow REX to mitigate alert fatigue for many personnel.
The Alert Creation page (Figure 4) is separated into a simple rule expression tab and a rule script tab. The simple rule expression tab allows users of all technical backgrounds to create alerts using functions, expressions and available tags, with a customizable output message. The rule script tab is where users experienced in programming languages can write fully customizable complex alerts. Embedded in this tab is a fully functional Python platform with code validation over a sample dataset or a user provided one.
Coinciding with the UI development, the backend cloud-based data structure was under construction. EDR, DCS and morning report data were merged into a singular dataset, with the ability to run both in real-time and scheduled alerts.
During the stakeholder interview process, a backlog of alerts to be developed was collected. Alerts were then categorized and prioritized based on the magnitude of impact they would have for internal and external users. An alert creation team was formed with a team of performance engineers and analysts with experience both in data analytics and hands-on operations. The combination of field experience, data analytics experience and knowledge of significant operational indicators resulted in high accuracy and low turnaround time for the creation of the first alerts.
Every alert created and provided to the public is quality control tested to at least 95% accuracy. The availability of in-house subject matter experts to assist in conceptualizing alerts helps to uphold Patterson-UTI’s high standards for operational excellence. By the time REX was publicly available, the alert creation team had 45 alerts built, quality-controlled and beta-tested in real time.
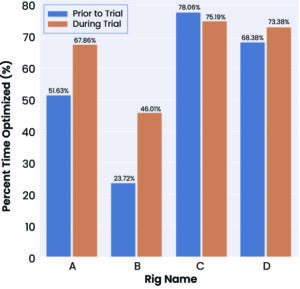
Implementation plan
Upon completion of REX’s backend infrastructure and UI, a rollout plan was formulated. Starting with executive management, presentations were given to ensure all areas of the organization were aligned to gain buy-in. Training sessions were given to operations, HSE, equipment management and marketing to show how to create, activate and monitor their alerts.
Next was to get the alerts flowing to the most applicable users: field personnel. A select number of rigs were initially chosen in one basin to provide the appropriate feedback and to answer any questions or concerns. Following this initial rollout, REX training was introduced in each region to small operational groups. By doing this, the team was able to focus on individual users, answer any questions and ensure that all individuals were comfortable with using REX on their own.
In all presentations, users were signed up for a few alerts made available to them depending on their needs and interests. Alert requests started rolling in once users began to build trust in the system and were able to verify the accuracy the alerts with the rig crews.
Case studies
Once training sessions were complete and positive feedback was given, tangible key indicators were needed to qualify REX’s success and value to the company. Two case studies were arranged around some of the industry’s top focus areas today: procedural compliance and environmental, social & corporate governance (ESG) initiatives.
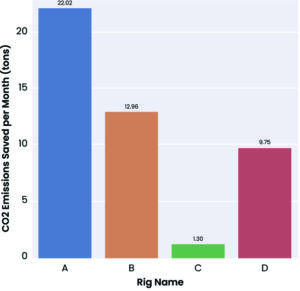
Case Study 1: optimizing generator usage
In the context of ESG, Patterson-UTI has taken proactive measures by applying REX to optimize rig engine utilization and reduce greenhouse gas emissions.
A typical Patterson-UTI rig has three to four generators driven by diesel, bi-fuel or 100% natural gas-powered engines. Running these engines at higher loads allows fuel to be burned more efficiently and reduces the amount of emissions burned per kilowatt hour of power generated.
Without the help of more advanced systems on the rig, the only way to improve this metric is to optimize the number of engines online. Asking field personnel to monitor generator loads in real time is inefficient, creating the need for an advisory system to help rig crews manage their engines.
REX helps crews by comparing a model for optimal engines online against the actual number of engines online, then providing a notification to all relevant personnel. The model runs on the rig server, reading real-time data looking at the generator loads and targeting an optimal combined generator load of 75%.
For this trial, four rigs for one customer were selected. Overall, the results were favorable (Figures 5 and 6). Rigs A and B improved by 16% and 23%, respectively, in optimized generator usage. All rigs reduced CO2 emissions despite Rig C decreasing in percent time optimized. This was the result of a higher generator load profile on Rig C during the trial, compared with before the trial. Rigs that were more open to the adoption of the new technology showed great success and wanted to get the alerts closer to when the generators online became suboptimal.
Initially, the alert was written to notify when the generators online were higher than optimal for at least an hour. With crews wanting to become more efficient, however, the alert was updated to notify after just 30 minutes. This trial has turned into a major focus area for the customer, who has since then set up all rigs with REX. They are continuously tracking reductions in monthly reports to help reduce their carbon footprint.
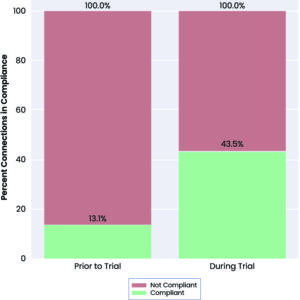
Case Study 2: improving procedural compliance
Operators have begun standardizing their drilling connection practices into procedures for drillers to follow. This helps prolong bit/motor life and mitigate drilling dysfunctions. One customer’s drilling connection procedures were coded into an alert monitoring six phases:
- Minimizing drill-off time after a stand has been completely drilled down;
- Minimizing RPMs after picking up off bottom;
- Ensuring mud pumps are kept running until slips are set;
- Ensuring a low RPM prior to tagging bottom;
- Ensuring a specified percent of WOB is applied manually before engaging the autodriller; and
- Minimizing the time to ramp RPM and WOB to the drilling rates.
One rig was selected for this customer. As in the previous case study, relevant users were subscribed to the alert and notified when connections were not compliant. In addition to simple compliance, the alert also included information on what section was incorrect and how to improve.
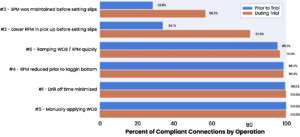
The application of this REX alert resulted in a significant improvement in compliance percentages (Figures 7 and 8). The drillers on this rig were already showing high compliance in phases 4-6 of the drilling connection. Most of the improvement in compliance percentage was in phase 2 and 3 of the connection. Before the trial, 13.1% of all drilling connections satisfied all conditions; this number grew to 43.5% during the trial. Despite not reaching 100% compliance in every area, significant improvements have been made.
Conclusions and future work
The results from both trials showed high potential for the system and created a collaboration between the field and office. Many of the successes in these trials have been a direct result of continued communication, feedback and involvement with the field.
Like all new technology, it takes time to generate buy-in, yet REX has had overwhelming adoption in the field. This success was derived through the top-down rollout plan with continuous training for all groups in all regions. Trust has been gained through high alert accuracy developed over very rich datasets and the expertise of in-house subject matter experts.
Since the completion of the case studies, there have been alert requests from rig managers, superintendents, operational leadership, equipment management leadership and customers. As of mid-June, there were 68 alerts available, 45 in the pipeline and more coming in with user interaction and new technology being deployed.
For future work, REX is in stage 2 of development, where select alerts will be deployed locally on the rig server, as opposed to the current cloud-based structure. This will cut down on cloud computing costs and notification delivery time. Alerts will be capable of running over sub-second data, while also having access to a larger selection of data (i.e., customer downhole shock and vibration data).
REX will be made available on Patterson-UTI’s CORTEX KEY rig platform, and it will be integrated into the rig’s HMI so that alerts are directly delivered to the driller for immediate action. This will allow the system to be utilized to its fullest potential for safe and efficient operations. DC