Robotic system enhances safety by keeping personnel out of red zones on the drill floor during offshore riser operations
Technology incorporates robots with visual detection systems, adaptive control software to automate repetitive bolting operations
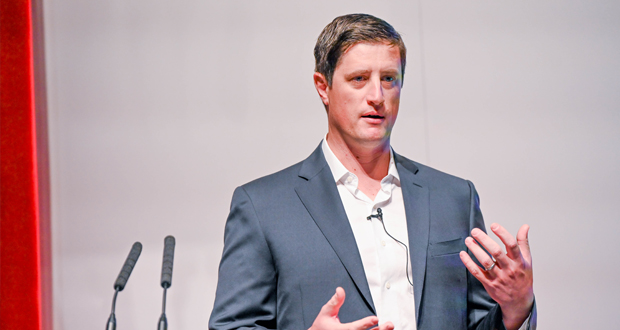
By Jessica Whiteside, Contributor
Installing and removing the bolts that connect the massive sections of a marine drilling riser is a labor-intensive job that requires crews to work with heavy equipment and hydraulics in the restricted-access “red zone,” where risk of injury is high. Transocean is aiming to eliminate that risk to personnel by handing the bolting task to robots instead, keeping workers safely off the drill floor during riser operations.
The offshore driller partnered with Houston-based ARC Specialties and Offshore Robotics to develop the robotic riser system, resulting in two designs for use with flanged connections on NOV and Cameron risers. The Cameron design was deployed on Transocean’s Deepwater Conqueror and Deepwater Poseidon ultra-deepwater drillships in the Gulf of Mexico in 2022. The NOV design was anticipated to be deployed in July, also in the Gulf of Mexico, for the first-ever riser deployment of Transocean’s eighth-generation ultra-deepwater drillship, Deepwater Titan. This would mark the first application of the robotic riser system on a rig with 20,000-psi well control capabilities.
“It’s a very exciting time for Transocean and the industry,” Travis McGuire, Operations Performance Manager – Special Projects for Transocean, said at the 2023 IADC World Drilling Conference in London in June. “It’s been an incredible opportunity and experience.”
Manual riser bolting challenges
In deepwater drilling, connecting the riser joints together may require hundreds of bolts, each of which weighs approximately 55 lb and must be torqued to approximately 18,000 ft-lb – roughly 180 times more torque than a car wheel nut, Mr McGuire said.
Traditional riser running or pulling operations requires six crew members working continuously in the red zone, with additional people supporting the operation, such as drillers, toolpushers, crane operators, floorhands, roughnecks and subsea engineers. Each thousand feet of riser string deployed equates to about eight hours of personnel exposure to the red zone, where the heavy, repetitive work of moving bolts and other equipment and using a 250-lb torque wrench can leave crew members susceptible to hand, finger, foot or back injuries.
That’s a stark contrast to the robotic system, which requires virtually no personnel exposure to the red zone. Humans are only needed if a validation or other check is required, which would take up to a half-hour, Mr McGuire said.
The robotic system also holds advantages in terms of efficiency. It’s capable of making up or breaking out 4-5 joints per hour, compared with an average 3.5-4.5 joints per hour with manual handling. Moreover, those crew members can now use that time to work on other tasks, he noted.
“Those five and six people can now do other activities that are much more valuable than picking up 55-lb bolts, putting them into a hole, holding onto a torque wrench and torquing up. We can do all of that in a much more efficient manner.”
Transocean’s pursuit of a robotic riser system was spurred in part by a fatality on another company’s rig during riser operations in the Gulf of Mexico in 2020. That incident prompted the question, “How do we get people further away from heavy iron and put them in a better place to do their job?” Mr McGuire said.
How the robots work
The patented system developed by Transocean and its partners is set up on the spider deck and incorporates two large robotic arms. The arms are equipped with tools that enable them to pick up and manipulate the riser bolts and place stabbing guides to ensure proper alignment of connections. Cameras capture images of the location and orientation of the bolts and other equipment; a control system then analyzes these images and other sensor information and communicates with the robotic arms to ensure that factors such as position and rotational angle are correct before the robots place and torque the bolts. The robots can also perform other tasks, such as installing or removing a hole cover or filling hydraulic lines.
Robotic arms like these are more commonly used in controlled environments, such as manufacturing plants, not the harsh, dynamic conditions of an offshore drilling rig. The design team incorporated adaptive control software to help the robots perform consistently even when wind or waves affect the motion of the drillship and riser, for example.
The robotic system is integrated with the rig’s restricted zone access management system to ensure people stay away from the robots, which will stop if a person gets too close. There is also a direct link back to onshore operations assurance processes, which continuously monitor how activities are running on the rig.
Next step in offshore automation
The introduction of the robotic riser system has been a positive experience for Transocean and has stimulated idea creation for other potential automation applications, Mr McGuire said.
“You’ve got something like this that completely changes how you’ve ever done anything before – put big yellow robots out on the rig floor. And once you take that step, you start to think, what else is possible? How can we use these things to leverage other ideas?”
What about the common concern that automation is going to displace traditional rig jobs?
“I don’t think we’re near that point right now,” Mr McGuire said. Looking at all of the processes that a drilling operation entails, there are so many small activities that could be automated, but “somebody’s going to be there to be a part of that process.” DC