Amid growing uptake of MPD in deepwater, controlled mud level technology deserves another look
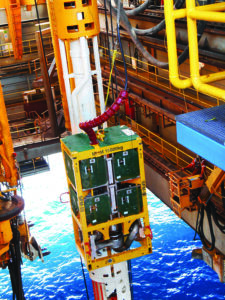
By Anthony Spinler, Enhanced Drilling
The oil and gas industry is constantly evolving, driven by the need for more efficient and sustainable exploration and production methods. EC-Drill and its controlled mud level (CML) systems have grown from an initial concept of two systems used in the North Sea to a technology that has drilled almost 100 offshore wells and, within a few months, has gone from one CML-capable rig in the Gulf of Mexico (GOM) to having its third.
This article delves into the world of CML, exploring its benefits and underlying principles, showing the potential to reshape the future of offshore drilling.
Similar benefits as SBP but achieved differently
Managed pressure drilling (MPD) is one of the most prominent components of the offshore market today. Drilling contractors have stated that approximately 80% of deepwater rig tenders require MPD capability. In almost all cases, the specifications are toward surface back pressure (SBP) technology, which is well established on land and offshore. Drilling engineers and executives may have heard of CML but must familiarize themselves with the breakthroughs driving adoption.
CML, introduced in 2010, is an MPD technique that combines innovative pump technologies and advanced drilling practices to optimize the extraction of oil and gas reserves from the initial liners to completions. Since the wellbore is open, similar to conventional drilling, it enables well-known and established drilling and well control procedures to improve drilling efficiency, increase recoverable reserves and reduce the environmental footprint. Pressure in the wellbore is controlled by changing the equivalent mud weight in real time by adjusting the height of the mud column in the riser; this provides greater flexibility during drilling operations and enables operators to navigate through challenging geological formations with improved accuracy with less pressure-induced risk.
CML offers several advantages similar to SBP, including enhanced wellbore stability, reduced nonproductive time, better control over wellbore pressures and the ability to mitigate kicks and prevent blowouts. But it does so in the opposite way to SBP.
The EC-Drill CML pump systems provide more than MPD, including pre-BOP and pre-riser installation for cuttings transfer and riserless mud recovery. Top-hole sections that cannot use SBP can still utilize CML equipment, providing additional environmental and cost savings at applicable water depths.
Underbalanced vs overbalanced
MPD, predominantly known and used as SBP since 1968, offers a revolutionary approach to drilling through reservoirs. Unlike conventional drilling, SBP uses mud weight less than the formation pressure, causing the well to be hydrostatically underbalanced when not applying back pressure. As such, reservoir fluids can, and are, sometimes allowed to flow into the wellbore as it operates on the pore pressure side of the formation. This technique is particularly beneficial in unconventional reservoirs, tight gas formations and mature fields. SBP starts with an underbalanced mud weight and increases the pressure through a rotating control device (RCD) and choke, thus increasing the pressure from above at the rig floor. In doing so, the pressure returning from the bottom of the hole increases when SBP is applied.
CML utilizes a balanced mud weight for the drilling window and lowers the height of the mud column to reduce the effective bottomhole pressure. Therefore, the hydrostatic pressure profile increases with depth – the opposite of SBP. The wellbore pressure will then match the operating window’s typical trend and allow for longer sections, especially in deepwater environments that would otherwise require frequent casings.
CML is conventional drilling where the balanced mud weight is utilized and only available offshore. In deepwater, the EC-Drill system places an approximately 16.5-ton subsea pump at roughly 1,200 ft (366 m) below the water surface, and the pump’s output maintains the desired riser level to establish the required bottomhole pressure (BHP). Since CML does not insert an RCD into the wellbore, it performs MPD during all drilling operations: drilling, tripping, liner and casing running, measurement, cleaning, completions, or whatever product or tool customers want to put down the hole.
The author estimates that only 30-40% of operational time offshore can utilize SBP; with CML, potentially 100% can be done when the riser is in position. Enhanced Drilling estimates that EC-Drill operations in the GOM have shown utilization during approximately 85% of all drilling operations (drilling, cementing and tripping) and 50% of completions.
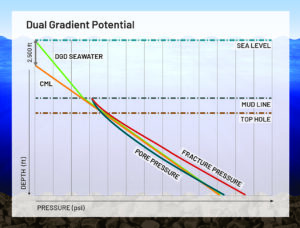
Smoother drilling
One unique aspect of CML is that it is similar to conventional drilling, as the subsea pump does not close the wellbore. With SBP’s use of an RCD, operations require multiple calculations: a lowered mud weight and then applying additional pressure. As SBP operations continue, the well often requires an entirely different mud weight and conducting a mud rollover. The new lower mud weight cycles into the well, so back pressure must increase again to reach the required BHP, or a higher mud weight must be applied to transition out of utilizing SBP.
CML eliminates these situations by applying a balanced mud weight to the well, starting the BHP closer to the fracture gradient than SBP. Then, the pressure is lowered to manage the BHP. One could say that SBP approaches the MPD solution from the pore pressure side, risking an influx, while CML approaches the MPD solution from the fracture pressure side, risking losses. For operators concerned about the incredibly costly and environmental expense of losses, CML provides the tool to manage losses effectively while lowering the risk of operating from the pore pressure side of the pressure window.
Further, there is an additional ease of use for cementing and completion operations, which require managing increasing pressures as these operations proceed. Excess pressure in cementing results in costly losses and a possible poor cement job, risking catastrophic failure. Excess pressures in completion operations result in a damaged reservoir that could impact everything from initial production to total recovered reserves. With CML, as the pressure rises, lowering the riser level manages the pressure profile and creates what looks like a saw tooth: Pressure goes up during the operation, then the pressure is reduced by CML maintaining the window throughout the cementing or completion.
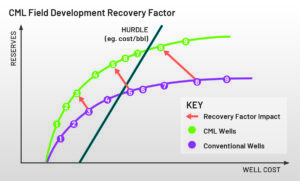
For example, various drilling operations require heavier/denser fluids using water-based drilling fluids or heavy brines like CaBr2 and ZnBr2. An overpressure of these fluids can damage everything from the casing shoe to the reservoir. The ability to lower the overall BHP by reducing the riser fluid level enables standardizing on other proven technologies and fluids.
An issue offshore is that the casing string length sometimes exceeds the water depth, which heavily impacts the value proposition of SBP-based MPD. Even if the SBP drills the well, it cannot manage the pressure while installing these longer liners/casings. This issue does not affect CML, which can apply MPD techniques while installing all casing sizes. In addition, for operators who strive for a robust separation between the primary and secondary barrier, CML provides a clear transition from the barrier envelope to standard well control procedures. Additional steps are not required to roll over the mud or close the BOP while tripping, as it already uses a balanced mud. Operators and drilling contractors can operate with well-established and proven well control procedures while also having MPD.
Improving sustainability
Apart from the operational advantages, CML also contributes to environmental sustainability. By optimizing drilling operations, these techniques minimize the number of wells required to extract equivalent hydrocarbons, reducing the overall surface footprint and ecological impact. Moreover, CML results in less fluid and mud losses, minimizing the environmental impact of creating them. Additionally, the reduced need for re-drilling due to wellbore instability, as well as rig time savings, decrease the carbon footprint.
Dual gradient
Dual-gradient drilling (DGD) represents the pinnacle of managing pressure downhole, which the industry has yet to achieve. As stated by one offshore operator: “It will enable us to drill offshore like we drill land wells.” As analysis and application continue on CML, it reveals that DGD may not be as far away as previously thought. Traditionally, DGD utilizes a lighter mud weight, typically seawater, in the riser on top of the applicable drilling mud below the mud line. With CML, the lighter mud weight is air on top of the controlled mud height. For example, in a typical deepwater well in the GOM, using a 12.5-ppg mud weight, the seawater depth and 12.5-ppg mud weight produce the same annular pressure profile, with CML lowering the mud height 2,500 ft (762 m). No device is needed near the mud line as previously thought to achieve DGD.
To maintain a tight drilling window, standard DGD practices would fall short, whereas a CML system performs constant BHP-enabling MPD while never changing the mud weight.
Shifting financial model
The combined outcome of these benefits can transform development project economics for operators adopting CML technology. Well architecture simplification and drilling operational improvements reduce well cost, and completion results increase recoverable reserves. As shown in Figure 3, that combination of reduced well costs and increased recoverable reserves in wells 1-4 changed well economics and allowed additional wells (5-7) to pass the hurdle rate.
Several offshore operators have stated that they now require their drilling teams to justify not using MPD, signifying that MPD has proven to result in lower overall costs and faster well completions due to less nonproductive time from pressure-related incidents. MPD is a proven offshore technology for SBP and now for CML. While CML holds immense promise, it has similar challenges to SBP. Implementing these advanced techniques requires specialized equipment, well-trained personnel and significant upfront investments.
However, as the oil and gas industry seeks to strike a balance between energy demands and environmental sustainability, the future of CML appears bright. Ongoing R&D efforts will lead to further optimizations and cost reductions, making CML a standard offshore practice. As one operator customer shared, “SBP is the right technology for exploration drilling as we are dealing with high levels of uncertainty. CML is the right technology for development drilling as we should be able to plan the pressures we need to achieve best-in-class drilling, cementing and completions.” DC