Research expands as sour gas completion challenges increase
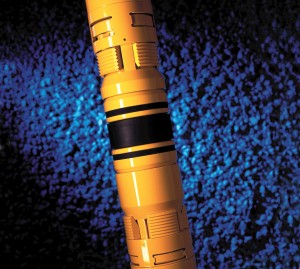
Industry looks to fit-for-purpose equipment, new guidelines for extreme H2S environments
By Katie Mazerov, contributing editor
Like vinegar in a cylinder of honey, hydrogen sulfide (H2S) is the industry’s ultimate party-pooper, a sour intruder that puts the damper on an otherwise healthy well that may hold a wealth of hydrocarbons. Better – and perhaps aptly – known as “sour gas,” this naturally occurring but toxic and highly corrosive chemical has always lurked in the oil patch. However, over the years, producers have been able to either manage it in low concentrations or avoid the problem altogether by moving on to other fields.
As global energy demand increases, however, operators can no longer be choosy about which reservoirs to tap, and completing wells with high concentrations of sour gas is a challenge that many companies can no longer avoid.
Sour gas is a condition complicated by high-pressure, high-temperature (HPHT) environments that often exist in areas where oil companies are pushing the boundaries of production – notably ultra-deepwater, where pressures can exceed 20,000 psi. It is produced with oil and natural gas in varying concentrations.
“Because of its corrosive properties and toxicity to humans, operators must be very careful to use properly rated metals and materials in wells with concentrations of H2S,” said Marco May, senior technical sales manager for Vallourec & Mannesmann, manufacturer of premium Oil Country Tubular Goods (OCTG). Although it is seen in pockets globally, sour gas is prevalent in the Middle East, North Sea, US Gulf of Mexico (GOM) and areas of the former USSR, such as Kazakhstan, he added. Unlike carbon dioxide (CO2), which has a more long-term effect on materials and is more predictive in determining failure, the effects of sour gas occur much faster, sometimes in a matter of 12 hours.
“No one has come up with a process that reduces or eliminates sour gas, and in low concentrations, H2S is manageable,” said Peter Fay, packers product line manager for Baker Hughes. “It depends on how corrosion-resistant the metallurgy of the equipment – tubulars and casing – is that is being put downhole. Considerations also must be given to the selection of elastomers for O-rings and packer elements.”
To that end, the industry looks to NACE International. NACE provides education, training and certification for various industries, promotes research of new technology and advocates on behalf of corrosion experts. NACE MR0175/ISO15156 establishes requirements for materials that can be used in H2S environments in oil and gas production.
Setting the standards
“Our mission is protecting people, assets and the environment from the effects of corrosion,” said Linda Goldberg, director of technical activities for NACE. “This has historically been our most widely used standard.” The standard specifies requirements for metal materials that make up the equipment used in sour gas environments, the chemical composition of those materials, the temperatures to which those materials can be heated and other environmental factors that affect the material.
The standard was first published in 1975 and has undergone several revisions. In 2003, it was adopted by the International Organization of Standardization (ISO). The 1975 standard covered only wellhead components. In 1977, the Texas Railroad Commission requested that the industry provide a standard for all oil and gas production equipment exposed to an H2S environment after an equipment failure caused a fatality.
People can request changes or have materials added to the standard using a ballot process. Ballots approved by NACE are submitted to the ISO for final approval. “Between 2003 and 2009, about 15 ballots were approved and included in the 2009 revision of the standard,” Ms Goldberg said.
There are also two testing standards associated with the primary standard: TM0177-2005, “Laboratory Testing of Metals for Resistance to Sulfide Stress Cracking and Stress Corrosion Cracking in H2S Environments,” and TM0284-2011, “Valuation of Pipeline and Pressure Vessel Steels for Resistance to Hydrogen-Induced Cracking.”
Failures of wellhead equipment and carbon steel tubular goods during the 1950s prompted action by the industry and NACE to define causes and develop possible remedies. The failures involved 13 Cr martensitic stainless steel wellhead components and carbon steel tubing with strengths greater than 100,000-psi yield strength, explained Robert N. Tuttle, a NACE fellow who was on the committee that developed the 1975 standard. “The failures of susceptible steels were identified as being caused by applied tensile stresses while being exposed to H2S. Laboratory and field data demonstrated that susceptible steels were those that were of high strength and could be detected by use hardness measurement.”
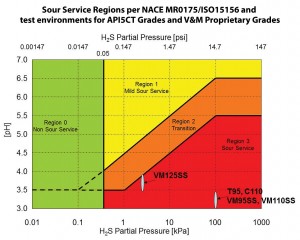
Rockwell C hardness (HRC) measurements were chosen as the method of choice since field hardness testing devices were available. New guidelines limited metal hardness to a maximum hardness of 22 HRC for carbon and low-alloy steels. “Some of the early failures occurred rapidly after exposure to H2S – often within minutes,” Mr Tuttle said. “The failure mode was later defined as sulfide stress cracking. The failures occurred well below normal equipment design stress.”
An urgent effort
NACE participates with organizations like the nonprofit group RPSEA, which is engaged in sour gas research on a number of fronts. “The urgency for dealing with this issue is coming to pass because we are going into HPHT regimes in places like the Lower Tertiary of the GOM,” said James Pappas, vice president of RPSEA’s ultra-deepwater program. “The preference is to have a solution in hand before it’s really necessary and avoid making costly mistakes.”
First to consider is the magnitude of the problem, he said. “The empirical equations used to estimate damage from HPHT in a sour environment are inadequate in many cases. We’re having to extrapolate the damage assessment from information we have from laboratory testing.”
RPSEA is launching a project to examine sour environments at various combinations of 350°F and 400°F and pressures ranging from 20,000 psi to 30,000 psi to try and verify the data and, more importantly, to establish new equations.“These new equations can be plugged into models to better forecast what is happening in sour environments and ultimately determine what the best metals are and see if any new alloys need to be created. We know corrosion inhibitors work because we’ve tested them at lower temperatures and pressures. We may need to create new inhibitors at these higher temperatures and pressures, but we won’t know that until we do the analysis.”
RPSEA is also studying the fatigue limits of deepwater risers in H2S environments. Lab tests put riser materials under different stresses to determine breaking points and understand what happens from a chemical side. “The next step is to verify the lab results by conducting a field test in which we introduce H2S to actual risers hanging off a platform but not hooked to a well,” he said.
Elastomer guidelines
For completion equipment, Baker Hughes has developed general guidelines for elastomers, Mr Fay explained. “It depends on the concentration of sour gas and the temperature of the well, because the higher the temperature, the more susceptible both the metals and elastomer materials are to the effects of H2S. For example, nitrile rubber can be used safely in wells with a low concentration of sour gas, but once the temperature goes above 175° F, standard nitrile is no longer acceptable.”
For typical applications, Baker Hughes recommends hydrogenated nitrile elastomers for service up to 50-psi partial pressure up to 250°F, but if the temperature is above that mark, the H2S concentration can only be 10-psi partial pressure. “When we start using more premium elastomers, the standard guidelines switch from partial pressure measurements to percentages of fluid,” Mr Fay added.
Specifications also pertain to an occurrence known as hydrogen embrittlement, where high levels of sour gas cause equipment to crack or break, even in cases where corrosion is not a problem. “For low-end completions, many of our customers will use a carbon steel alloy, but that has limits on the hardness of the material,” he continued. “In those cases, the sour gas concentration is relatively low and corrosion is not a concern, but hydrogen embrittlement can still occur. In situations with a higher concentration of H2S, operators will choose a 13-chrome (corrosion-resistant) base material. For highly corrosive applications, Inconel is the product of choice.”
The industry has known solutions within a certain boundary of temperatures, and new research is looking at solutions for either higher concentrations of sour gas or higher temperatures. “Once we get outside the box defined by NACE, we’re facing a huge research and development project to develop materials that will meet the standards we strive for,” Mr Fay noted.
“For example, with GOM Lower Tertiary deepwater platforms, we’re typically talking about higher temperatures and pressures, so if sour gas is present in those environments, we are pushing the boundaries of where we haven’t been before. NACE only covers metallurgies up to 450°F, so if we have a sour gas completion that exceeds 450°, we have to do our own metallurgical evaluation of the properties and materials under those conditions because there are no published standards.”
Research is advanced by the major service companies, which have an interest in ensuring the materials can perform. “We are constantly developing HPHT technology to try and push the boundaries,” he said. “We offer many types and models of HPHT equipment – packers, safety valves, liner hangers – and they could all see service in H2S applications.”
Strength versus ductility
Sour gas is also problematic in high-pressure wells, where there are currently not a lot of accepted industry equipment grades especially when the concentration of H2S is high. “If we have higher pressures, such as 20,000 psi and above, even small amounts of sour gas are a problem,” Mr May said. While stronger steel and casing are required to handle depths and high pressure, a more malleable or ductile steel is necessary to withstand the sour gas conditions. “Depending on how deep you drill, the tubulars require a certain tensile strength, collapse behavior and burst pressures that require higher-strength steel.
“But, those products are not acceptable by NACE for use in sour gas environments because they are susceptible to hydrogen embrittlement,” he continued. “Lower-strength steel prevents that issue but isn’t strong enough to meet the pressure.” For example, Vallourec’s VM-125 SS (sour service) is a high-strength steel that has been used for HPHT environments in the GOM with slightly sour conditions, but it is not rated for the most severe level of H2S as defined by NACE. Addressing that conundrum will require a two-step process, Mr May believes. “We need to develop stronger steels that aren’t susceptible to this type of hydrogen embrittlement, and we need to design heavier-wall casing that still meets all the properties through the wall thickness.”
Through its VAM product line, Vallourec provides OCTG for three levels of resistance to sour service environments as defined in NACE MR-0175/ISO15156: Mild Sour (Region 1); Intermediate Sour (Region 2) and Severe Sour (Region 3).
For extreme environments, the solution is to develop fit-for-purpose equipment. “For completions that encounter CO2, in addition to H2S, the choice will be a high-quality alloy for the tubing, such as high-grade nickel, rather than carbon steel,” Mr May said. “We are seeing increasing demand for fit-for-purpose equipment as more and more operators are conducting well testing to better understand the conditions and determine if they need full-scale sour gas equipment.”
Inconel is a registered term of Special Metals Corporation.
VAM is a registered term of Vallourec & Mannesmann.