Precision leverages automation to take productivity to next level
Enhancing process automation through digital controls provides drilling operations with repeatability, reliability – and tangible results
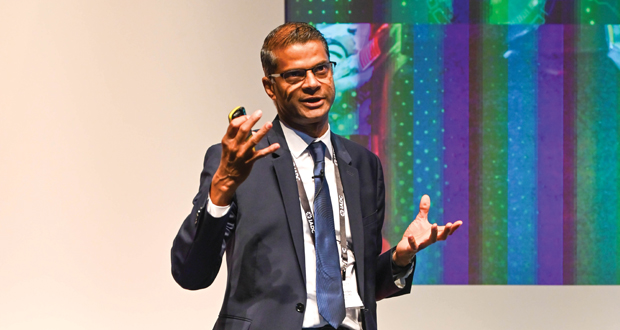
By Stephen Whitfield, Associate Editor
Drillers are always looking for new ways to improve performance, generating value from massive amounts of complex data while managing repetitive tasks in need of frequent attention. The experience level of the driller and the rig crew, as well as individual fatigue levels, are among numerous factors that can cause the quality of a drilling operation to vary from rig to rig, from day to day or even from hour to hour.
Automated systems have become a key component in companies’ efforts to reduce this variability in drilling even as wells become longer and wellbore trajectories become more complicated.
“You’re looking at longer laterals and deeper wells. As a drilling contractor, we have to look at how we can manage this footage productively,” said Ashley Fernandes, VP of Drilling Optimization at Precision Drilling, at the 2023 IADC World Drilling Conference in London on 21 June. “We believe that enhancing process automation through digital control is the next step the in the future. We realize that the variance in how we drill can cause a lot of differences that affect productivity, so the repeatability and reliability provided by process automation can complement our work quite well.”
Precision Drilling launched its Alpha line of automation technologies in 2019. It includes the AlphaAutomation software platform and AlphaApps, a series of applications that control specific functions within the well construction process.
The automation process begins when Precision engineers receive a well plan from the operator and enter it into the software. The well plan outlines parameters such as section lengths and planned total depth. Once the plan is entered, the software determines the equipment configurations for the rig, as well as the applications that it will need to successfully run the automated processes specified by the operator.
For example, the Power Manager app allows the system to automatically manage generators based on operational requirements while keeping loads and fuel substitution at preferred levels. Another app, Z-Torque, automates stick/slip management by controlling top drive functions in real time. Precision also has additional apps for drill-offs, reaming, surge and swab, surveys and downlink, as well as third-party apps from companies like Pason and SLB. Currently, 21 native and third-party apps are configurable with the AlphaAutomation system,
The flexibility of the app configuration allows the operator to utilize automation in the exact fashion Precision wants, Mr Fernandes said. “What we effectively have is a bunch of digital subprocesses – the apps – that commingle with each other. We’re either creating these subprocesses internally or taking them from the OEMs. And when you look at the apps, a customer might come to us and say, ‘I don’t want you to run my directional drilling services, but I want you to run my managed pressure drilling services in an automated fashion.’ If you have the equipment ready, you press a button and you can start things up automatically. If you don’t want to use automation for directional drilling, you don’t need to.”
A more recent addition to the Alpha suite is Alpha Robotics, a set of algorithms designed to enable machine control of seven pieces of equipment – the slips, elevators, top drive, drawworks, mud pumps, generators and iron roughneck – using third-party robotics systems installed on the rig. The system works in a closed loop. It aggregates data collected from sensors installed on the rig, and then machine learning algorithms analyze the aggregated data and re-compute the digital well plan based on that analysis, effectively creating a digital twin of the well.
“While you’re drilling, you often will need to do some tweaking to the well plan,” Mr Fernandes said. “If you’ve got harder rock to cut through, or stringer management when you’re cutting through different layers of rock, you may require a different process or a different subprocess. The system allows you to do that.”
Since its launch in 2019, the Alpha technology suite has been installed on 73 rigs and drilled more than 38 million ft in approximately 3,000 wells.
Reducing driller interaction with screens and joysticks
Mr Fernandes noted that the company has seen a significant reduction in driller interactions between screens and joysticks on the rig – for instance, on a 17,000-ft onshore well drilled in North America, the company registered 10,862 interactions on a non-Alpha enabled Precision Drilling rig. Drilling another well of similar length with an Alpha-enabled rig, the interactions went down to 328. Mr Fernandes said this reduced driller interaction has allowed the company to move its personnel into different areas.
“We won’t take our people out,” he said. “There are a lot of other things that can be done at the rig site. On top of that, we can rotate them around in remote office centers.” Drillers and rig managers can work not only with in-house optimization engineers and the operator’s drilling engineers on digital wells plans, but they can also work with other engineers who are reading dashboards and the results of data analytics. “What we’ve come to realize is that they’re developing very strong skills. I now have four drillers on my team who have learned to code,” he added.
The automation platform has also helped Precision realize greater efficiencies in drilling. In delivering a 27,919-ft well for Shell Canada in 2019, which included a 16,404-ft lateral section, the Alpha system enabled automation of 96% of all drilling connections.
Another example came in early 2021, when an operator working in the Montney Shale in Canada switched from using two Precision land rigs that were not equipped with the Alpha system to using a single Alpha-enabled rig with the same specifications. The operator realized significant gains in drilling productivity and flat time efficiencies when comparing the H2 2020 performance of the two non-Alpha rigs against the 2021 performance of the single Alpha rig.
In particular, it saw:
- a 16.2% decrease in drilling connection time;
- a 16.3% decrease in surface flat time;
- an 8.6% increase in production trip-in rate
- a 14.6% increase in production trip-out rate;
- a 9.1% increase in production casing run rate; and
- an 11.7% decrease in production flat time.
Overall, these results led to a 9.2% reduction in days drilled per well (approximately 1.2 days), saving the operator an average of $56,000 per well throughout the 2021 drilling campaign.
Mr Fernandes said the Alpha platform is an example of embracing a “digital mindset,” where the company bases decisions on the insights gained from its digital systems. Continued leveraging of digital systems will help the industry optimize the competencies of personnel and drive further efficiencies in its operations, he added. To help make the digital mindset more of a reality moving forward, collaboration between drillers and operators will be critical.
“A lot of operators today see automation and technology as an add-on that the driller wants to charge for, but this is a collaborative approach,” Mr Fernandes said. “If you don’t see it as such, you’re not going to make it successful. I think with process automation, there’s a very big difference between who adopts the technology and who doesn’t adopt the technology.” DC