Pre-salt development drives focus on rigs, well integrity, R&D
Critical issues in drilling & completions with Antonio Lage, wells technology manager, Petrobras
By Diane Langley, editorial coordinator

What are some of the key drilling and completions challenges facing the industry today, and how is Petrobras responding to those challenges?
For most of the companies in the E&P segment, the low hanging fruit has gone, meaning that we have to go deeper to find oil and gas in deep and ultra-deep waters. That’s our challenge.
Petrobras has been facing some of these scenarios for a long time. Because we started our deepwater operations by the middle of the ’80s, when two giant fields were discovered, Albacora and Marlim, we are used to dealing with deepwater fields for more than 20 years. In fact, the pre-salt discoveries in the Santos Basin offshore Southeast Brazil are in ultra-deepwater, which makes the development more challenging. However, based on our successful history of managing assets in deep and ultra-deep waters, we do not see it as the toughest feature about it.
The hardest challenges about the pre-salt are associated with reservoir quality predictability and the deep depths of the targets, demanding drilling through thick layers of salt. Obviously, the fact that these discoveries are in ultra-deep waters makes it even more challenging, but the potential of huge recoverable volumes are a drive to develop them quite soon.
The pre-salt areas in the Santos Basin are in water depths between 2,000 meters and 2,500 meters and the true vertical depth subsea of the reservoirs goes from 5,000 meters to 7,000 meters. These recent discoveries represent a huge potential for production, having started a new age for the oil and gas industry for Petrobras and Brazil.
As we are talking about deep targets in ultra-deep waters, to optimize well construction is indeed one of the main challenges. Besides, the thick salt layers pose a special demand regarding the maintenance of integrity assurance for the whole well life cycle.
Further, our operations are not limited to the pre-salt environment. We are keeping operations abroad, such as Chinook and Cascade in the Gulf of Mexico; in many countries of South America and West Africa; and exploration efforts in several parts of the world. But the pre-salt is the pinnacle because of the volumes of oil and associated opportunities and challenges.
In addition to the pre-salt, we are conducting drilling and completion operations in other areas in Brazil, including offshore and onshore activities.
What technologies will prove beneficial in meeting your challenges?
In the pre-salt, drilling and completion are key issues because the wells represent a significant part of the development CAPEX. The main focus is on technologies capable of reducing costs, and we are considering two key alternatives. One, increasing penetration rate while drilling the carbonate reservoir rock, and two, attempting to use different strategies for drilling. As a large number of wells will be drilled in the pre-salt, we are considering the use of one rig to drill the top-hole section, another rig to drill the salt zone, and another one to drill the reservoir, also perhaps being responsible for completing the well.
We are still discussing the various features needed on each of those rig types. So far we have used sixth-generation rigs, which are quite expensive, but we are studying and evaluating other alternatives.
Well integrity is a long-term concern which is associated with the fact that salt moves as time goes by and may encroach upon the casing, increasing load. To address this, we are thinking of enhancing monitoring.
Further, as some reservoirs contain some amount of CO2 dissolved in the oil, the definition of appropriate formulations of cement slurries and proper materials for tubulars are important points of interest. Our efforts in terms of technology development are targeted to address these concerns. We also have logistics challenges in the pre-salt because those targets are located 300 kilometers from the coast.
From a corporate standpoint, how does Petrobras support technology development?
When we began the development of the Campos Basin, we were a smaller company facing challenges. From that perspective, the challenges were tougher in the 1980s than the ones we face now. The structure of the company was smaller, and the technology management process was limited. Besides that, the price of oil was not as valuable as it is nowadays. On top of everything, the Brazilian economy was weaker than it is now.
Despite all of those difficulties, Campos Basin was very successfully developed, generating extraordinary results for Petrobras and for the country as a whole. It was difficult at that time to have the support of suppliers, and Petrobras’ importance in the world scenario was not the same. Now it’s possible because we know that we are demanding a fantastic volume of activities for the suppliers. In the past, we had to develop things inside the company without partnerships. In other words, we are addressing two completely different conditions, defining two different worlds.
As we will drill and complete a considerable number of wells, we know that we have a very attractive market for our suppliers, stimulating them to help us develop the technology we need. In addition to an attractive market, our international suppliers and partners are recognizing the existence of a capable technology park in Brazil. In fact, local content is paramount for the development of the pre-salt areas.
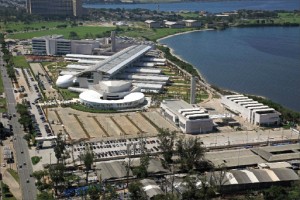
Additionally, the introduction of governmental policies about five years ago created the proper stimulus for forcing Brazilian industries to invest hugely in R&D. Regarding the oil and gas sector, operators have to invest a certain percentage of the production revenue in R&D, half of it in Brazilian R&D institutions. Tied to those mandatory rules, Petrobras has been investing approximately $250 million per year outside the company for four years in a row. This level of investment has been building a first-class infrastructure for Brazilian universities and R&D institutions and generating skilled human resources, which are ready to face the demands of our industry. Summing up all those incentives, most of our suppliers are now building R&D facilities in Brazil.
Working together with our partners, which will be much closer to our R&D facilities in Brazil, is part of our strategy to overcome technological gaps. In addition to attracting R&D partners, we are stimulating the development of manufacturing plants in Brazil for supplying the pre-salt demands, to comply with the country policy.
Besides all these initiatives for creating a collaborative environment, it is worth mentioning Petrobras’ internal efforts. For the last five years, Petrobras has been among the eight biggest investors in R&D in the oil and gas industry, including operators and service companies. In 2008 and 2009, the total R&D investments were in the range of $900 million, which includes $250 million that was invested outside the company in cooperation with Brazilian universities.
Internally, we are maintaining the same successful strategy used for overcoming the technological gaps associated with the exploitation of deepwater fields in the 1980s, which consists of organizing and running R&D programs for concentrating efforts on essential subjects. Prosal, ProCO2, Pravap and Procap are the R&D programs that are closer to exploitation activities. Prosal was created to generate technology solutions for the pre-salt. ProCO2 targets the management of CO2, involving EOR, control of emissions and carbon capture and sequestration. Pravap deals with advanced oil recovery, focusing on the increase of reserves and production. The last item is Procap, which has played a leading role to apply new technologies in deep and ultra-deepwater and continues to do so.
As a final point, Petrobras has also invested in improving our own R&D infrastructure, expanding the area of Cenpes (Petrobras’ research center). The constructed area is being more than doubled from the current 122,000 sq meters to 305,000 sq meters, reinforcing even more our commitment to the future of the oil and energy industry.
What issues exist in the pre- and post-salt plays in particular? How are these being addressed?
In looking to the pre-salt, we are thinking in short-, mid- and long-term achievements. This is a new approach because most of the time we are focusing with much more emphasis on short- to mid-term developments. However, Petrobras is also concentrating huge efforts on making viable technologies that need much longer time for maturation. In other words, we are putting more emphasis than usual on the long-term achievements.
Petrobras is still keen on driving technologies with the focus on short- to mid-term results in these areas that will help in reducing costs and adding value to the well construction process. As an example, we are working with our suppliers to add incremental value to conventional things, such as improving bit performance. On the first well in pre-salt, it used to take 12 months to drill, and now it takes 100 days. It happened based on our learning process and improvements related to the bit and overall drilling technology, but still based on incremental technological gains.
We are also pursuing technology developments related to fluids and drilling parameters. We continue to evolve by using the traditional short- to mid-term approach. However, as we are just increasing the emphasis on technologies that will change the game, we are adding a new perspective to the technological process. In each technological area, we are considering different alternatives for development, but, somewhere in time and budget, the number of alternatives will be reduced for gaining focus on the most attractive in terms of achieving success and adding real value.
Those are some highlights of the strategy. I think it is important to say something else about the topics we are considering for further development. As we perceive value in monitoring and controlling up to a certain level of complexity, smart completions are being considered for many wells. An important issue about introducing new downhole equipment is reliability because, as the rigs are expensive in the pre-salt scenario, we have to avoid interventions. At present, we are developing studies to evaluate downhole equipment – flow valves and sensors for measurement – to determine performance and long-term reliability.
Besides the initiatives for the pre-salt, we also have to think about our older fields because they are a continued source of income, providing financial resources for the investments. In this particular case, technology development tends to be more incremental, but we also have some technology advances for Campos Basin that deserve to be emphasized, such as the development of underbalanced drilling technology from floating rigs, which is planned to happen in 2012.
In general terms, for the post-salt, we would like to reduce cost of interventions by becoming more effective, which is not easy in deepwater. Furthermore, sand control is always an issue there.
Will the Macondo incident have an impact on the way your company conducts its operations, particularly in deepwater? If so, how?
The whole industry observed the difficulties that BP faced to contain the oil production from the Macondo well in an open sea environment. Certainly, every operator realized that it is necessary to focus on containment and response preparedness, which demand internal initiatives for putting the experts together to define blowout scenarios of interest and establish plans of action in advance for each scenario. Besides that, we are developing the discussions in terms of a much more comprehensive approach, including the identification of needs for designing, building and maintaining new equipment for prompt reaction.
In the case of a subsea blowout, besides our internal initiatives, Petrobras is also supporting and actively participating in the International Association of Oil and Gas Producers’ efforts to deliver studies to improve well engineering and procedures, equipment to respond more effectively with capping and containment systems, and techniques to better respond to oil spills.
Preventive actions are always the main goal in which effective training plays an important role. It is a great opportunity to review old training programs and update procedures. Concerning training, I would also like to emphasize the contribution of the IADC WellCap Accreditation Program, which has been helping the industry to practice useful and efficient training by ensuring the quality of well control schools. Besides training, the introduction of new technology for dealing with traditional well control or handling a subsea blowout is welcome, and we are stimulating it.
Will Petrobras continue to invest heavily in the drilling and completions segment? If so, where will the majority of investment be focused, in what technologies and service areas?
I would like to recall what was said at the beginning of our conversation – the industry has to go deeper in deepwater and ultra-deepwater. Keeping this in mind, it is easy to understand the importance of the role that well construction will play for the oil industry from now on. As a consequence of the operational scenario, exploration and exploitation will demand much more investments for drilling and completing wells than before. Then, the need for services and technology developments will grow together with other demands in the area.
As it consists of a deep reservoir in ultra-deepwater, the pre-salt is part of this context, meaning that Petrobras is just facing it. Well construction is very important, representing an extremely significant amount of investment, meaning that it is considered of utmost importance. As mentioned before, we are very keen on introducing technologies capable of reducing well construction costs, which is our main R&D focus in drilling and completion.
Besides increasing R&D investments in the area, Petrobras recently concluded a comprehensive work to reorganize its well construction management structure. These efforts targeted the conception of an optimized structure for achieving improved operational performance and facing the massive growth of the activities that will happen from now on.
Is the human element still part of the solution to challenges or is industry more poised to rely on automation?
Human resources are still key elements for everything, in particular for the introduction of new technologies. In fact, three things are needed to successfully introduce new technologies: one, physical technology; two, social technology; and three, connection to the business plan. Physical technology is what we are habituated to think of as technology, such as printing presses, microchips, etc. Usually, it takes much more of our attention than the two other aspects. Social technology refers to the way we put people together to do things. In order for technologies to produce positive impact, some group of people has to turn the physical and social technologies from concepts into reality, which is the role played by business.
Having those aspects in mind, we may think of automation as a physical technology. It is part of the process, but it needs the other elements for successful implementation. In other words, regardless of the level of automation adopted, the human factor will keep on playing a decisive role. Certainly, the introduction of more automation into the well construction process will demand redefinition of jobs, creation of new ones and probably introduction of new training paradigms, such as the use of simulators, like in aeronautics and nuclear plants.
Thinking about the future, we will need more trained and skilled people. However, as the demand will be vast, appropriate investment has to be made now. It is worth reminding that some years ago, companies were dealing with the reality of higher oil prices and the impact this brought to the oil and gas sector. While delivering better results for the companies, the business scenario as a whole presented difficulties of higher costs, capacity restrictions, such as rig availability, and a deficit of trained personnel to enable expansion opportunities to be carried out.
Petrobras is recognized for having a long and successful history of developing human resources for the oil and gas industry. However, as it is getting harder and harder to have personnel ready to overcome the future challenges, the winning past is not a guarantee of success for the future. We are concerned about it, and we have been working to respond properly to the different demands. For instance, training people for R&D is quite different from training for operational activities. As a general rule, every engineer takes at least one year to be ready for the job while others take two to three years, depending on the area of work.
What steps have been taken to increase recovery rates over the past year or two? What is the average recovery rate for 2010 and how can that be improved?
Our average recovery rate is about the same as that of the industry – 30%. However, this average does not mean much. As we are averaging parameters from completely different reservoirs in different scenarios, it is difficult to extract noteworthy conclusions. To improve on this rate, one strategy consists of grouping reservoirs with similar characteristics and discovering the best in class for every group. Each best in class is taken as an example for the rest of the group, but other aspects have to be considered. For example, if one reservoir is onshore and the other is offshore in deepwater, differences are expected in terms of recovery rate.
Another Petrobras strategy to get better recovery factor is to apply new technologies, such as 4D seismic, and enhanced oil recovery. We are also improving reservoir characterization, based on high-resolution seismic and high-resolution stratigraphy. In addition, the introduction of the concept of digital fields, subsea processing and boosting are possibilities for increasing recovery. Finally, improving the management of secondary recovery is always a key factor.
Overall, what are the hard truths about drilling and completions facing the industry today?
In the middle of the 1980s, a joint industry project (JIP) was formed to address the issue of a subsea blowout. The effort was named Subsea Blowout Control Capability and involved the most important blowout firefighters and experts from the industry. The studies of the JIP were conducted with the participation of a huge number of operators and service providers, projecting more relevant scenarios of subsea blowouts and designing tools and procedures for a prompt emergency response. The final stage of the JIP’s work was to carry out manufacturing of needed tools and making them available for all participants in emergency situations.
However, as it was a general statement that a subsea blowout would be a very rare event, a decision was made that such an endeavor would not be carried out. By that time, it would be quite difficult to convince companies to manufacture tools and maintain needed personnel ready for an emergency for a very long time. The decision was to stop the program.
Back to 2010, after the Macondo blowout, we know that rare and improbable extreme events do happen and have a great effect. Further, the effects are even higher due to the fact that they are unexpected, looking like a Black Swan Event, which is based on a triplet composed of rarity, extreme impact and retrospective predictability.
The hard truth is that, similar to banks and trading companies, our industry is also vulnerable to a hazardous Black Swan Effect, being exposed to losses beyond that anticipated by our usual prediction paradigm. However, this real tragic case is giving us the opportunity for identifying our vulnerabilities and working for constructing a more robust system, being significantly better prepared to prevent undesirable events to happen or minimize their effects.