Industry must leverage data, automation to create collaborative workflows that eliminate waste
Devon already seeing significant productivity gains by combining underground laboratory of well data with real-time information to make smarter decisions
By Linda Hsieh, Managing Editor

Garrett Jackson is VP of Drilling for Devon Energy.
What do you see as the most critical issues facing our industry today?
A couple of big challenges come to mind, and first and foremost is keeping talent and getting the right skill sets for our employees. As technology changes and as we find better ways to adopt those technologies into our industry, it’s critically important that we train our workforce so they have the proper skills to deploy those technologies. More and more, our employees are technical specialists, not generalists. We don’t just have petroleum or drilling engineers. We have data scientists and black-belt process experts, as well as application development engineers and integrated planning personnel. The staffing transformation is well under way.
The second challenge that comes to mind is getting qualified contractors out into the field. Early in 2017, there was a pretty quick ramp-up in the rig count, and we saw a lot of contractors turning to new-to-industry workers. While increases in activity levels have slowed down since then, we have to make sure that all of our contractors are well-trained and aligned with our priorities. Our operations can only be successful if we’re both fully aligned.
When you mentioned changing technologies that must be matched with changing skill sets, what kind of technologies did you have in mind?
I think everyone sees the move toward digitalization. This industry has always had a large amount of data, but we haven’t always used it as well as we could. Now we’re seeing a race to get to the next step-change, so technologies are advancing quite rapidly. At Devon, we’re already seeing the benefits from the work we’ve been doing over the past several years as far as using real-time data, as well as the collaborative workflows enabled by that data. It has really led to a lot of improvements in cycle times and efficiency gains over the past couple of years.
We’re also seeing rapid advances with process control and automation. They are not necessarily new technologies; a part of it is just our industry learning to utilize technologies from other industries.
Looking to the coming years, what do you see as the biggest challenges in terms of leveraging data and automation?

The big challenge is making sure we’re applying the right technologies that are really going to affect the bottom line and improve safety, and then building on those technologies to change the way we do things. We used to look at saving days on each well. But we’ve improved so much over the past several years that we’re now looking at saving hours and even minutes. We’re at a place where we really have to look at process control and automation for the next improvements.
In the onshore business, we’re also striving to drive higher rates of return in a way that’s sustainable for both the operator and contractor. To do that, we have to eliminate waste. In the coming years, I really think we’ll have to utilize data more aggressively and effectively, in conjunction with advanced rig automation. That’s how we’re going to reach the milestones that we need to get to.
Devon achieved some impressive production rates in 2017 with its wells in the STACK play, most recently the Faith Marie 1-H well that achieved 5,100 oil-equivalent barrels per day. Devon has attributed achievements like this to a new completion design that improves stimulated rock volume through the systematic cycling of pressure and fluid rates. Can you provide more details on this completion design?
It starts with a data-driven approach. Over the years, we’ve invested in an underground laboratory of data. That includes downhole fiber-optic data that we acquire during drilling and completion operations, as well as other downhole information. We learn from these laboratories, where we can use this real-time data to quantify our stimulation results, and then we customize our designs using proprietary software in our real-time center, which we call WellCon.
With all these enabling technologies and data, we’re able to design and customize every individual well that we fracture, even from stage to stage and even while we’re doing the fracture. Further, because we’re doing that in a centralized real-time center, we can quickly apply learnings to all areas of the company. We’re already seeing results, like more stages per day, increased well performance, fewer flowback days and coil-tubing drill-out enhancements, in all of our major basins.
Of course, this wasn’t done overnight; actually it’s been years in the making. I would say it started when we established WellCon in 2014, and then we installed fiber-optics in many of our wells. Those investments allowed us to build the underground laboratory, and now we’ve been able to combine that data with real-time data to drive these results on our current wells.
Is the underground laboratory applicable throughout the lifecycle of the well?
Absolutely. In addition to the completion work already mentioned, in the drilling space, we’re using it for things like bottomhole assembly design and drill bit design. We’re also using it to help us geosteer into target zones. In the production phase, we use the real-time data to optimize production. It’s being used full well lifecycle.
Do you see this type of data-driven approach to things like bottomhole assembly design and completion design as being the way forward for the industry?
I can’t speak for the industry, but it’s been very successful for us at Devon, and we feel like it’s something that sets us apart.
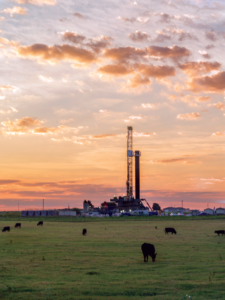
In 2015, we formally established the predictive analytics and artificial intelligence department. We work very closely with that group, as well as our IT resources – along with geology, production and reservoir engineering. We’ve created a very collaborative environment in which we design, construct and produce our wells. That collaborative environment enables us to optimize every facet of the well design and production. It also helps us to spread the learnings across our core basins.
I think that collaborative environment is something that a lot of companies are trying to achieve, but it’s something that takes time. In a siloed environment, you can have resistance to outside opinions. There can also be communication barriers depending on how you’re set up structurally. You have to really work at breaking down the communication barriers and siloed behaviors. As you break them down, you start to have a better stream of ideas.
Like I said, we’ve been working on it for a while, and we’re starting to see the benefits of investing in that collaboration.
Is Devon extending that collaborative environment to the way it works with its contractors?
Absolutely, and I can give you an example. When we talk about rig maintenance, it’s always been a challenge for the contractor to shut down the rig to maintain their equipment. Of course, it’s better in the long term for the rig, but it’s also downtime for the operator. What we’ve done is work proactively with the contractor to schedule the maintenance for a time that makes sense for both of us.
Because of this collaborative way of coordinating rig maintenance, we’ve seen better rig performance and less downtime overall, and the contractor still gets to take care of their equipment. These are really the sustainable types of changes we’re trying to make, where it’s a win-win for both sides, and I believe the benefits will compound in the future.
How can drilling contractors contribute to the work that Devon is doing to improve drilling performance?
The opportunities I see are on the data side. We have to continue to work together to improve the decision process and the utilization of data at the wellsite. We’re already seeing more contractors embrace process control and rig automation, and we definitely see that as the future. We need to continue to align in that direction.
Do you think the equipment and instrumentation that’s on today’s drilling rigs are sufficient for the kinds of process control and automation that you would like to see in the coming years, or will there be more investment required?
I think there is some low-hanging fruit with current rig equipment. The ability to utilize current rig control systems is there; it’s a matter of using the data and working together more collaboratively to move toward more advanced automation. At some point down the line, we may come to a bottleneck, but I don’t see it as a bottleneck right now. I think there is room for improvement with our current equipment.
The industry is seeing some operators move toward more of a vertical integration model in order to address cost challenges. Is this something that Devon is considering, and what are your thoughts on this trend?
We have adopted this model in some areas. Fracture stimulation, for example, is an area where we’ve completely decoupled, and we’ve seen tremendous improvements. We essentially buy our own sand and chemicals, and we separate out the horsepower. By doing that, we’ve really lowered costs and improved performance at the same time.
We’ve seen some opportunity to apply the same concept in areas like directional drilling and drilling muds, but we don’t see it as something that we need to do in every single area or every single service. It requires a lot of planning, so you really have to be proactive for it to really pay off.
North American onshore projects have enjoyed a strong comeback this year as the economics of these projects out-compete other types of projects, such as deepwater. In the coming years, do you see rising costs and the depletion of sweet spots threatening the viability of North American land?
Those have always been the challenges on land. We will always have price increases in an upturn, and companies will always drill their best wells first. So those aren’t new challenges, but we still believe that we have room for improvement. We see the adoption of technologies like data analytics and process automation as enablers for us to make better decisions and improve efficiencies. The use of those technologies is accelerating, not slowing down, so although we know the challenges are there, the investments that we’ve made will help us deliver better and better performance in the years ahead. DC