New drill stem rotary shoulder connection incorporates innovative single start shark thread shape
New thread design has curvy shape on loading flanks to generate more torque and enhanced elliptical thread root to reduce stress on connector cross section
By Marta Lafuente, Vallourec Drilling Products; Fabien Carrois, Vallourec Oil and Gas France
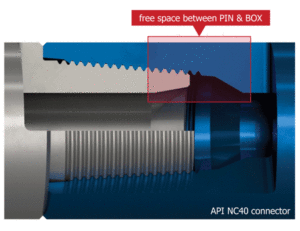
For the past century, the oil and gas industry has been pushing the limits of the existing drilling envelope to reach deeper, more remote hydrocarbon reservoirs. The evolution of drilling programs has driven drill string manufacturers to engineer new drill pipe solutions to safely develop the most challenging horizontal and extended-reach drilling (ERD) well profiles.
In response to new drilling challenges, drill stem elements evolved to provide better mechanical and hydraulic performance. Based on industry requirements, the tensile strength-to-weight ratio of drilling products and their torque ability were steadily improved in order to help operators overcome frictional drag forces and achieve improved hydraulic performance, rates of penetration, control of well trajectories and hole cleaning.

Drilling environments are fast-paced, rough and often unpredictable. Therefore, drilling connections have to be designed differently than other threaded connectors to ensure that they achieve the right level of performance even in the harshest conditions.
Due to the high financial risks associated with drilling operations, oil and gas companies are continuously looking at mitigating drilling risks and reducing total drilling costs. Choosing the right drill string can be critical to achieving the required efficiency, which is generally associated with operational parameters, such as higher rates of penetration (ROP) and lower nonproductive time (NPT).

The performance of a drilling program depends heavily on the design of the connector, which was traditionally measured through its mechanical, hydraulic and operational performance. However, as the industry becomes more competitive, drilling tubulars are also required to be economically efficient.
The drilling connection presented in this article was designed to provide significant operational and economical benefits, covering the two main drivers of the oil and gas industry: performance and cost-efficiency.
Evolution of performance

The first API design became public in the first half of the 20th century. API connectors basically rely on a primary external shoulder and a single start thread with a triangular shape to provide the required mechanical performance (Figure 1).
API connections are still widely used. They are fairly robust and can be run without the use of stabbing guides. Further, they typically have low repair rates and are easy to run.
In the second half of the 20th century, drill pipe premium manufacturers developed a new type of drilling connector based on the API thread design. This was driven by the need for additional torque and hydraulic performance. The new design included a secondary internal shoulder that increased the torque generating surface, allowing for 50% more torsional ability compared with the API design, while tensile and fatigue performance remained intact (Figure 2).
In addition, double-shoulder connections feature a flush internal diameter that prevents turbulent flows, keeps downhole tools from getting stuck and prevents cement from getting trapped in the space between the pin and the box.

In terms of operational performance, API double-shoulder connectors inherited the speed of use and robustness of API connections, although repair rates are slightly higher due to the addition of an exposed functional surface on the internal shoulder.
Although API and API-based double-shoulder connections remain a valid option for most drilling operations seen today, increased wellbore complexity is requiring connections that are able to provide more torque and/or better hydraulic performance.
To fulfill industry requirements, the next generation of high-torque connections, such as VAM Express, had to be designed outside of API design rules.
To achieve increased torsional strength without degrading the tensile strength or the fatigue life of the connector, the thread form and root, taper, lead and pitch diameter of the connector were engineered to provide up to twice the torsional strength of an API connection (Figure 3).
Design features included:
• High torque: up to 100% more torque than API connectors, provided by the engineered thread form and taper and the yield strength of the connector;
• Improved fatigue resistance, due to the elliptical thread root design;
• Quicker make-up and deeper stabbing, provided by the connector taper and proprietary thread design;
• Easier stabbing, due to the optimized taper of the stabbing flank of the thread profile;
• Reduced risk of wedging, due to the reversed angle on thread crests; and
• Optimized hydraulic performance, clearance and fishing ability, due to the slim design of the connector.
Next-generation premium connection
Specification and design process
To address the industry’s evolving drilling challenges, the VAM X-Force was developed with the objective of designing a threaded connection that can excel in mechanical, operational and economic performance:
• Mechanical: by improving the torsional strength of the existing shouldered connections without degrading the tensile strength or the fatigue life of the connection;
• Operational: by increasing the speed of make-up without degrading break-out torque; and
• Economic: by inheriting the “easy to use” characteristic and robustness DNA of the latest generation of premium connections.
During the development process for this connection, a functional analysis was created based on a specified market need; the product lifecycle and field constraints were taken into account. This analytical work served as the base of the design and qualification processes during the rest of the project.
Design philosophy

The new design was conceived as an optimization of VAM Express. By keeping the existing design base, that product’s ease of use was continued, while torsional strength was improved without degrading other performances.
The final design of VAM X-Force includes a single start “shark” thread, which provides robustness and make-up speeds equivalent to that of a double start thread design. However, the innovative thread shape is the main feature of the new design. It is characterized by:
• A curvy shape on the loading flanks that’s able to generate more torque than other triangular threads due to the increased available surface; and
• An enhanced elliptical thread root that reduces stress on the critical cross section of the connector, thus improving its fatigue life.
In addition to mechanical and operational performance, economic considerations weighted the final design selection. Such considerations led to a thread taper, as well as a thread height that reduced the re-cut length as much as possible.

Design
The final design is composed of:
• A primary external torque shoulder serving to provide initial seal and pre-load during make-up;
• A secondary internal torque shoulder serving to provide torque, internal flushness and monolithism of the connector; and
• A “shark” thread design that provides increased torsional strength and better fatigue life.
Qualification process

The first step of qualification process was to evaluate the design through finite element analysis (FEA). As shown in Figure 5 and 6, the FEA results revealed that the stress repartition in the VAM X-Force is more homogeneous than in the latest double-shoulder premium rotary connector of the former generation. This improved stress repartition allows for make-up torques up to 22% higher than for the former generation of connector to reach the same level of stress in the cross critical section.
Further, physical testing demonstrated that:
1. The connection is able to withstand at least 100 makes and breaks without galling or compromising the seal ability of the connector, even when made up with the highest available torque;
2. The connection is able to withstand at least equivalent axial bending and pressure loads as VAM Express. Figure 8 presents the new drill stem rotary shoulder connector performance envelope under internal pressure, combined with axial loads and bending;
3. The connection has a fatigue performance significantly better than previous generations of rotary connectors. Figure 9 presents the VAM X-Force fatigue test results compared with ISO 10407 and VAM Express fatigue performances.
Conclusion
This article provided a review of the evolutions of requirements on threaded connection and presents the design and qualification of the VAM X-Force solution designed to improve the operational and economic performance of drilling operations. Benefits include:
• An innovative thread form that reduces the stress on the critical cross section and enhances fatigue resistance;
• An engineered single start thread design, which allows for faster trip times;
• A make-up to break-out torque ratio between 0.7 and 1.1, which reduces the risk of the string backing out while drilling;
• An optimized taper and thread design that allows for a deeper stabbing and eliminates the need for stabbing guides; and
• The ability to design tool joints with a reduced OD and an enlarged ID, which reduces the pressure and hydraulic horsepower requirements for circulating drilling fluids, viscous pills and cement. DC
VAM is a registered trademark of Vallourec. VAM Express and VAM X-Force are trademarks of Vallourec.
This article is based on SPE/IADC 184745, “Innovative Drill Stem Rotary Shoulder Connection Designed for Cost Efficient Operations in the Most Challenging Drilling Environments,” 2017 SPE/IADC Drilling Conference, 14-16 March, The Hague, The Netherlands.