LWD maps path to new pay on old field
Real-time imaging enabled geosteering on horizontal producer well with tight vertical, lateral tolerances
By Eirik Stueland, Talisman Energy; Matthew Spotkaeff, James Dolan and Christophe Dupuis, Schlumberger
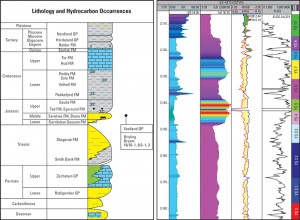
Today’s high oil prices, combined with new well geosteering technology, can make directional drilling a cost-effective option for revitalizing old oilfields previously considered uneconomical. One such case is the Yme field offshore Norway.
Originally developed by Statoil in the 1990s, this field produced 50 million barrels of oil between 1996 and 2001, with a plateau production of 40,000 bbl/day. The field was permanently shut down in May 2001 with an estimated overall recovery factor of 15% to 20%. Reasons for the shutdown included increasing water cut, high operating costs and relatively low oil prices at the time. The Yme field has since become the first abandoned field on the Norwegian Continental Shelf to be redeveloped.
Talisman Energy Norge submitted a plan for redeveloping the Yme field in 2006, and the drilling campaign – aimed at producing an additional 70 million barrels of oil – started in 2008. The plan included three vertical injectors and six high-angle producers with long (1,000-1,500 m) sections within the vertically thin (2-6 m; 10-20 ft) Callovian/Kimmeridgian-age Egersund formation inner estuary reservoir sands (Figure 1). The producers needed to be geosteered to maximize exposure of the targeted reservoir zones.
To delay water entry for as long as possible, the wells were to be drilled in a narrow corridor up-dip between existing watered-out producer wells and the field bounding fault. In addition, wells needed to be placed on the correct side of the bounding fault, as drilling into the unstable shale on the other side would require a sidetrack.
TIGHT TOLERANCES
In 2010, Talisman planned to drill its final horizontal development well: a sidetrack targeting a high-permeability sand not sufficiently drained by other wells. The drilling team not only needed to keep the wellbore within a vertically narrow reservoir but also had to cope with restrictive lateral tolerance for well placement. The sidetrack had to twin much of the original well path, which had intersected the field’s major fault – the reason why this part of the target reservoir remained undrained. The borehole would have anti-collision issues with three offset wells. In addition, the thickness and dip of the formation in the area were uncertain. Thus the pre-drill structural model was not accurate enough for precise well placement.
Finally, subseismic faults had been encountered in previous wells, causing temporary losses of stratigraphic control. The challenge, therefore, was to drill the hole between the fault, mother bore and previous producing wells, identify the target sand, and then geosteer within it for at least 400-m MD – despite all the uncertainties and potential surprises.
NEW LWD TECHNOLOGIES

Detailed pre-job analysis of the drilling, anti-collision and geosteering challenges led to the reliance on two key well placement logging-while-drilling (LWD) technologies with the rotary steerable system (RSS) in the bottomhole assembly (BHA). A Schlumberger well placement team contributed to pre-job planning, real-time operations support and post drilling analysis.
The PeriScope real-time bed boundary mapper tool was used to map the structure around the wellbore to help identify individual sand and intra-shale units while drilling and to help geosteer the horizontal section within the high-permeability pay zone. This deep azimuthal electromagnetic resistivity LWD system makes 360° deep directional measurements that can indicate the distance to, and orientation of, formation boundaries from the borehole, using a combination of tilted coil technology and multiple frequencies and spacings.
During drilling operations, the LWD measurements are transmitted in real time to the surface. The tool is sensitive to contrasts in resistivity within a radius of investigation that varies depending on the particular geological environment.
In the case of the Yme reservoir, distance-to-boundary (DTB) measurements were possible within 4 m (12 ft). The resistivity contrasts can be due to changes in lithology (e.g., sand versus shale) or fluid changes, such as an oil-water contact. The tool’s deep directional measurements provide considerably more information than is possible when using conventional LWD systems in low-measurement-contrast reservoirs. These unique symmetrized directional measurements, with maximum sensitivity to formation or fluid boundaries, enable 3D mapping of resistivity boundaries around the wellbore in real time.
Geologists expected the structure to roll over and dip steeply toward the major fault shortly after the sidetrack entered the target reservoir. The EcoScope multifunction LWD service was employed to provide additional structural dip information to help stay on track and update the pre-drill model during geosteering operations. This service integrates formation evaluation, well placement and drilling optimization measurements into one collar. Besides resistivity, neutron porosity, and azimuthal gamma ray and density, the service offers the first commercial LWD measurements of elemental capture spectroscopy and sigma. The tool is also the first to offer commercial LWD nuclear measurement of formation density without chemical radioactive sources.
WATER MAPPING
In any field redevelopment project, water fronts and water fingering are to be expected, and the key to producing efficiently is to understand the fluid distribution. However, in this case, prior knowledge of the fluid distribution was insufficient to predict the dynamics of fluid substitution, so design of the geosteering campaign included measuring, mapping and managing those events as they arose. One of the uses of the bed boundary mapper technology was to define water zones while drilling the producers.
Figure 2 is a real-time geosteering display that shows one of the water zones mapped while drilling one of the producers. Excellent reservoir sand was entered at 3,740-m MD. The apparent structural dip indicated by the DTB inversion was 9°. This was confirmed by dip-picking on the density borehole image. At 3,765 m, a conductive bed is clearly seen from 3 m below the wellbore. This was interpreted as a water-flood zone in the most permeable part of the reservoir.
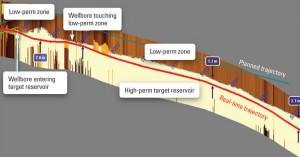
It was decided to drill through it – partly to confirm the hypothesis of water but also because the redevelopment strategy recommended that the wellbores cross as many sand layers as possible rather than drilling within a single layer.
The conventional LWD logs and the DTB inversion around 3,800-m MD confirmed that the observed conductive body was indeed water. After drilling another 40 m, the wellbore exited the water zone and subsequently mapped it 2-m true vertical depth (TVD) above for more than 100-m MD. The well trajectory continued up-structure, and after 3,900-m MD crossed back into the upper part of the sand layer. The tool response clearly indicated that the water zone does not extend to that part of the reservoir.
During the geosteering process, real-time DTB measurements were consistently able to image water-fingering zones within the high-permeability target sands. This capability enabled placement of wells within the thin productive zones and gave the subsurface team a way to visualize the water flooding.
Update model in real time
Schlumberger LWD specialists worked on the rig alongside Talisman wellsite geologists, while well placement engineers provided 24/7 support to the company’s operations geologist and G&G subsurface team onshore Norway. Real-time drilling data, combined with directional drilling experts – both onshore and offshore – successfully avoided collision issues with the other wells.
Prior to landing the wellbore in the target reservoir, the LWD density-neutron measurements enabled geologists to identify an additional 400 m of very good quality reservoir in the upper section of the underlying sand.
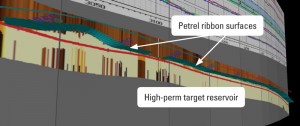
Once inside the target interval, a relative lack of heterogeneity made it tough to determine the structural dip with either of the two LWD tools alone. Combining information from both, however, proved effective and showed that the pre-drill model had been inaccurate. Steepening due to rollover did not occur as much as predicted, and the model was updated accordingly in real time.
Had the actual path followed the planned trajectory, the well could have remained within the overlying low-permeability interval for its entire length (Figure 3). Instead, the geosteered wellbore reached a total distance of 511-m MD within the target sand – exceeding its objective by more than 100 m and achieving a net-to-gross ratio of 92.5%. In addition, the well remained between 0.7 and 2.2 m TVD of the upper boundary, enabling Talisman to maximize production of attic oil.
After drilling, Petrel ribbon surfaces were created, derived from advanced processing of the bed boundary mapper measurements (Figure 4). These surfaces are representations of all formation boundaries detected within the tools’ range. This was a milestone in the use of such real-time LWD imaging data, as in addition to helping geosteering of the wells, better mapping of actual surfaces can refine structural surfaces and fluid distribution in the fieldwide geological model, increasing confidence in drilling decisions for future wells. Successful well placement was the result of the Talisman G&G team’s knowledge and Schlumberger well placement expertise in making geosteering decisions using real-time LWD data.
PeriScope, EcoScope and Petrel are registered trademarks of Schlumberger.