Landing string buoyancy technology allows deployment of longer, heavier casing while reducing rig time
System uses buoyancy modules to provide uplift force that can offset landing string weight by up to 80%
By Chris von Eberstein, Landing String
The deepwater drilling industry has always required a variety of new and reliable technologies to push operational limits further as operators seek to explore deeper reservoirs around the world. As deeper waters are explored, casing design is also becoming more complex and casing strings becoming longer and heavier.
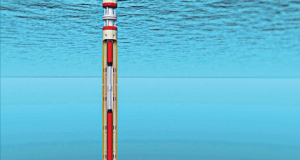
The demand for deeper wells, combined with more complex well designs, are driving operators to either upgrade equipment or to design around current equipment limitations.
While operators recognize the physical limitations of today’s mechanical systems and supporting structures, they are still aggressively pursuing new technologies with the potential to overcome current restrictions.
In today’s market, it is becoming increasingly difficult to feasibly achieve operators’ objectives without incurring substantial costs or compromising operational safety. One technology aims to resolve these restrictions by reducing the overall hookload weight of a landing string, enabling operators to drill deeper wells in deeper waters from existing rigs.
Archimedes Principal
The Archimedes Principle provides the basic concept behind the fully composite Landing String system, which can reduce the overall hookload weight of a drill pipe landing string by clamping buoyancy modules on to the drill pipe tube. Once the casing or landing string is in the riser, the composite-based system creates buoyancy, which reduces the hookload, decreasing the risk of the vessel exceeding its maximum hookload rating.
As a refresher, around 250 BC, Archimedes suggested that any object, totally or partially immersed in a fluid, is buoyed up by a force equal to the weight of the fluid displaced by the object.
Practically, Archimedes’ principle allows the buoyancy of an object partially or fully immersed in a fluid to be calculated. The downward force on the object is simply its weight, and the upward, or buoyant, force on the object is the displaced fluid. Thus, the net force on the object is the difference between the magnitudes of the buoyant force and its weight. If this net force is positive, the object rises; if negative, the object sinks; and if zero, the object is neutrally buoyant – that is, it remains in place without either rising or sinking.
In other words, Archimedes’ principle states that, when an object is partially or completely immersed in a fluid, it experiences an apparent loss in weight that is equal to the weight of the fluid displaced by the immersed object.
In the case of landing string buoyancy, the buoyancy modules are less dense than the wellbore fluid they are displacing – thus providing an effective uplift force and effectively reducing the overall hookload weight of a drill pipe landing string.
Case Study
A new landing string buoyancy technology provides an option for drillers to enhance their current rigs’ hoisting capacities by up to 20%. The system was run in the Gulf of Mexico by a major operator looking to eliminate two liner tiebacks and run larger casing through the entire sub-salt section.
By using the landing string buoyancy technology, the operator was able to shorten its rig time by two months and reduce the weight of the landing string by 206,996 lb. This weight reduction gave the rig the extra hookload to run the larger and longer casing that was desired. In addition, the current rig was able to safely land the string, which practically eliminated the risk of exposure over time while saving millions of dollars in cost.
Equipment at work
The landing string buoyancy technology uses Trelleborg’s syntactic foam modules installed onto the casing landing string to produce upthrust. Custom-designed non-metallic clamps eliminate metal fasteners in the wellbore, with the buoyancy system being assembled onshore, then loaded in purpose-built baskets and shipped to the rig.
Results
Once installed, the landing string buoyancy technology produced the following results:
• Reduced rig time by two months;
• Safely reduced landing string weight; and
• Allowed the rig to operate within its safe hookload limits.
The actual hookload, with the landing string buoyancy system installed, is provided by the landing string solutions rig crew after running of a 16-in. casing. The estimated hookload is from the final landing string solution tally just prior to running the landing string buoyancy system.
Composite Materials
Since the buoyancy sits inside the well casing, there was a requirement for all components of the system to be fabricated from qualified materials that would not damage a well’s subsea wellhead system or casings. To meet this requirement, the system utilizes all non‐metallic components while incorporating the latest syntactic and composite material technologies.

In addition, the system has a minimum 10-year service life, which allows for multiple deployments. Each element is designed to withstand a wide range of temperature and pressure extremes.
The core technology used in landing string buoyancy, syntactic foam, has been used for more than 40 years for various subsea buoyancy applications, from shallow water to full ocean depth. The main enhancement for landing string technology is that it is required to operate in drilling mud, as opposed to seawater.
While being submerged in the synthetic wellbore fluid environment, the buoyancy elements need added protection to contend with harsh chemicals, so a rugged, tough polyurethane coating encapsulates the syntactic foam to protect it from the harsh working environments while also protecting the elements from potential damage during handling or deployment.
Reducing Hookloads
Achieving high buoyancy uplift is critical for operators to justify the utilization of this technology. The amount of lift that can be achieved by this system is substantial and can be designed to offset the landing string weight by up to 80%, in some cases. This can lead to safer, more cost-effective deepwater operations. Depending on the well design, the system may even eliminate a tieback step.
The utilization of the landing string buoyancy system potentially enables operators to land a long casing string in the subsea wellhead versus running a shorter casing string (liner) and subsequent tieback liner due to load limitations of a rig’s hoisting system. When running heavy casing strings and landing strings combined, the resulting static and operating dynamic loads should never equal or exceed a rig’s hoisting system.
Using the landing string buoyancy system allows earlier generation MODUs to be utilized on some complex deepwater wells by providing a significant reduction in the load on its hoisting system.
Further, since the hookload is reduced by using the buoyancy system, the hoisting safety margin of all rigs can be increased. This application greatly expands the capability of a rig contractor’s fleet and could significantly reduce operators’ well cost. Reducing hookloads may decrease the frequency of detailed hoisting system inspections, leading to additional cost reductions.
Critical planning recommendations include:
- Quantify effects of dynamic loading on and off slips regarding equipment limitations, as well as slip crushing limitations;
- Verify clearance between top plate on slips used, and module shells, slips or floatation module diameter will need to be redesigned and/or modified;
- Include a test run to verify rig handling requirements;
- Look to tubular specialists for slip crush analysis and respective slip selection for landing string;
- Work with rig contractors and vendors to identify all critical load-bearing components;
- Document dimensional parameters, material strengths, tensile ratings and inspection results for all system components;
- Evaluate and determine optimum make-up torque and tensile rating for all string component tool joints; and
- Consider unknown variables while drilling and running casing string.
Safety is Paramount
Effectively reducing the weight of the landing string by using this buoyancy technology system provides a cost-effective and safe alternative to upgrading a rig’s hoisting system. This technology has the potential to increase the effective safe working load margin of all MODUs, thus enabling operators and contractors to safely and strategically utilize the inventory of rigs within their fleets. In addition, the technology reduces the potential of slip crushing due to heavy loading.
By taking advantage of weight reductions, landing the casing hanger in the subsea wellhead using the motion compensator may be an option on rigs with reduced load rated motion compensators. The chances of damaging this equipment is reduced during operations where heave is observed by using the motion compensator, thus providing safer working conditions.
Most importantly, effectively reducing extreme loads on a rig’s hoisting system greatly enhances operational safety while running heavy casing and tiebacks on subsea wells.
Future Applications
The reduction in hookload can also be considered to be an increase in effective hook capacity. When considered from this perspective, the potential for older rigs to be upgraded is evident. While not as capable as the newer sixth-generation rigs, fifth-generation rigs are typically much more cost-effective on a dayrate basis.
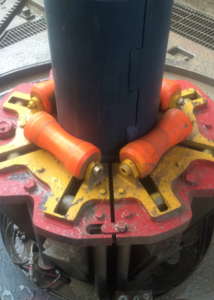
By using landing string buoyancy to increase the hook capacity, it may be possible to compete with sixth-generation rigs on certain well programs but with a significantly lower cost base.
Another factor increasing the demand for rig capacity is the gradual move toward 20k-capable drilling operations. Under such conditions, even sixth-generation rigs are not currently able to accommodate the larger BOP stack and robust casing program(s) required. As opposed to building entirely new vessels with all of the risk this entails in the current market, the use of landing string buoyancy may solve one of the key challenges in upgrading existing rigs for future requirements.
Conclusion
There is a growing demand from operators to drill deeper wells in deeper water with more complex casing designs and longer and heavier strings. This is driving operators to seek out new technologies with the potential to overcome equipment limitations of existing rigs. One proven technology is landing string buoyancy, which enables drilling contractors to deploy longer heavier casing and other downhole tubulars while reducing rig time, maximizing efficiencies and lowering costs.
The overall benefits of this system are extensive, ranging from enhanced operational safety to enabling more flexibility in well design and rig class utilization. Cost savings are more important than ever. However, there are many unknown variables operators must consider before attempting to run casing strings approaching operational limits. Alternative design contingencies are highly recommended, and operators will ultimately have to continue to choose designs based on their respective risk criteria. DC