Industry set to see surge in water recycling and reuse, with benefits on cost, environmental impact
Increasing adoption of automation also leading to opportunities to optimize water transfers by reducing fuel and personnel requirements
By Linda Hsieh, Editor & Publisher
As oil and gas companies continue to seek ways to reduce costs while working to step up their environmental stewardship, water recycling and reuse for fracturing remains a significant but under-tapped opportunity.
In 2019, oil and gas production resulted in approximately 24 billion barrels of produced and flowback water in the US, but only approximately 5% of that amount was recycled and reused, according to Dean Fanguy, Director of Business Development for TETRA Technologies.
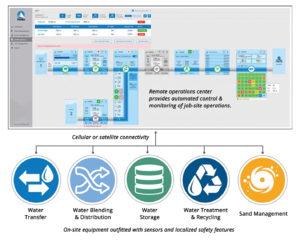
“The No. 1 thing that operators can do to reduce water management costs is to recycle more water,” Mr Fanguy said. Whether produced or flowback, water that is not recycled and reused or reinjected for enhanced oil recovery must be disposed of, which can be challenging and/or costly due to logistics and lack of infrastructure. Some states also place limits on how much water can be injected into a given disposal well at a time, creating another challenge.
The average cost of sourcing fresh water in the US land market is $0.60 per barrel, while average trucking and disposal costs are $1.50 per barrel, according to Mr Fanguy. “It makes sense to use the produced water that is already in the production system, especially if the logistics are favorable.” He believes that recycling produced water can provide cost savings of 30% or more, with an average recycling cost of $0.70 per barrel.
“In addition to the cost benefits, recycling produced water reduces the use of precious fresh water sources, which is a positive contribution to environmental, social and governance initiatives,” Mr Fanguy said.
Innovations in frac chemistries, developed by service companies in recent years, are also making it more cost-effective to recycle water and reuse it in fracking. “It took the industry some time to figure out how clean does the water really need to be to reuse it in hydraulic fracturing?”
Whereas many years ago, the industry tried to treat produced water until it reached the quality of distilled water, today most operators don’t spend the money to do that. New frac chemistries make it much easier for operators to use water with higher levels of salt and chlorides. This means that water is primarily just treated for bacteria and suspended solids – anything that can cause bacteria, scaling or H2S formation in the well.
Because of these changing economics, Mr Fanguy said he believes the industry is poised to see tremendous growth in water recycling and reuse in the coming years. He estimates that from 2019 to 2025, the industry will see an approximately 36% compounded annual growth rate for recycling produced water. At the same time, the incremental amount of produced water in the US will only average around 2% compounded annual growth rate, he added.
Besides recycle and reuse, two other areas providing opportunities for cost reduction are water transfer and the automation of water management.
Since the early 2000s, TETRA has introduced multiple innovations for handling and moving water for hydraulic fracturing. In 2012, the company launched a double-jacketed, UV-resistant lay flat hose with a working pressure of 200 psi and a burst pressure of 600 psi, providing for higher water transfer rates and improved reliability to minimize the risk of spills.
Further, the company has fully automated the pumps that are placed at strategic points along the water transfer route, eliminating the need to have a human being at each pump location. “These pumps are now preprogrammed on the inlet and outlet pressure so they know exactly how to operate based on the water movement requirement,” Mr Fanguy said.
Automation also allows for optimization of pump speeds, which can reduce the amount of fuel used by up to 30%, he added. This reduces the cost and risks related to the coming and going of fuel trucks.
The automation being deployed also encompasses consistent blending of produced and fresh water, and treatment and distribution of blended water to the staging working tanks at the frac site. “If you’re using six pumps to transfer water on one line, you could essentially do it with one or two people, rather than six,” he said.
Automation also reduces the manpower needed during the water distribution, using sensors that measure and track tank levels.
Because of the value that has already been proven, Mr Fanguy said that TETRA will continue to invest in adding automation to all of its equipment, including distribution manifolds, blenders and treatment systems. Going forward, the company will also work to leverage the capabilities of artificial intelligence to further substantiate cost savings and efficiencies.
“The data that we’re getting back from these jobs and the trends that we’re seeing are really giving us better pictures of things like fuel consumption and how we can improve maintenance schedules for our equipment. There is potential for incredible benefits and efficiencies.” DC